El proceso de fabricación por sinterización es una técnica utilizada para crear materiales sólidos a partir de sustancias en polvo mediante la aplicación de calor y presión, sin fundir el material hasta el punto de licuarlo.Este proceso se utiliza ampliamente en industrias como la metalurgia, la cerámica y la fabricación de vidrio.Consta de varios pasos clave: preparación de la mezcla de polvo, compactación para darle la forma deseada, sinterización a altas temperaturas para unir las partículas y tratamientos posteriores a la sinterización, como el mecanizado o el montaje.El proceso garantiza la creación de materiales con baja porosidad, alta integridad estructural y propiedades mecánicas específicas.La sinterización es esencial para producir componentes con formas complejas, alta precisión y características de material a medida.
Explicación de los puntos clave:
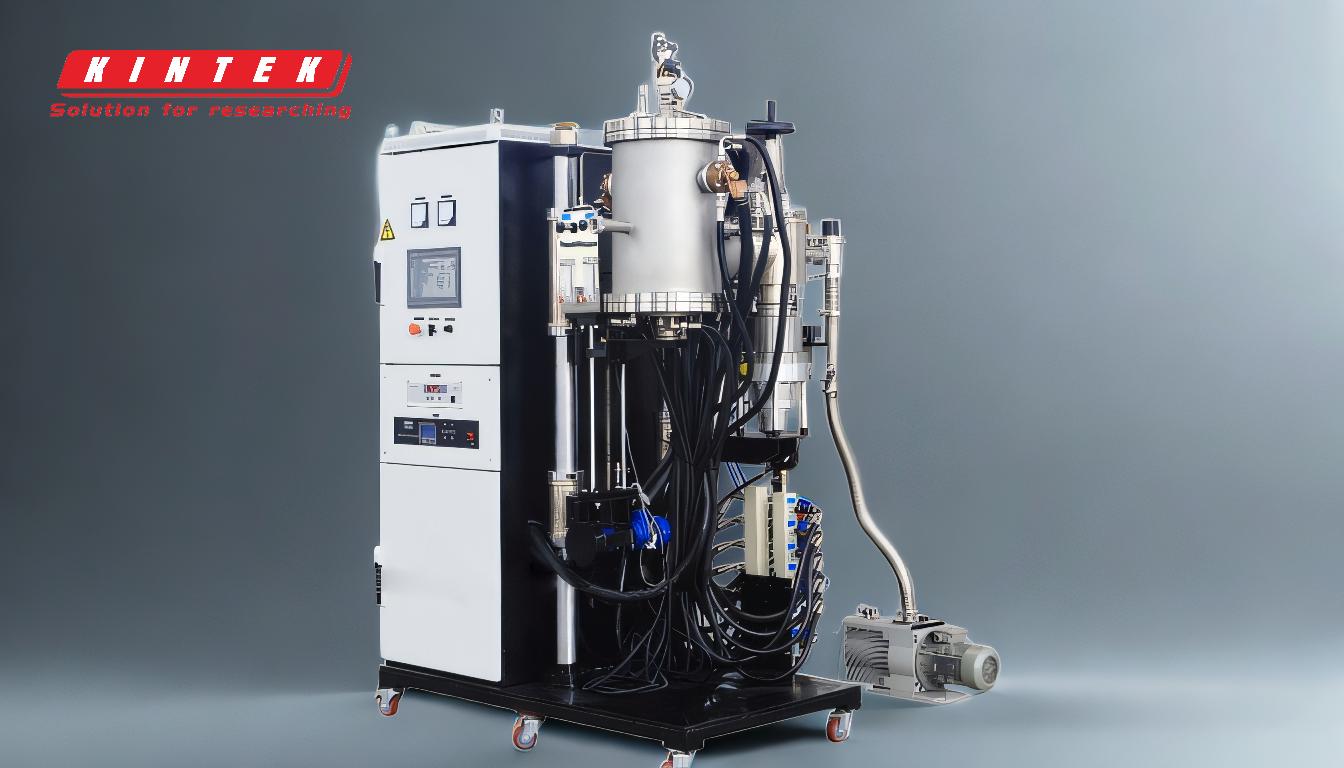
-
Preparación de la mezcla en polvo:
- El proceso comienza con la preparación de una mezcla en polvo, que puede incluir materias primas, agentes de acoplamiento y aditivos como polvo de cobre o carburos cementados.
- El polvo se mezcla cuidadosamente para garantizar la uniformidad de la composición, que es fundamental para conseguir propiedades de material uniformes en el producto final.
- En algunos casos, se añaden aglutinantes o lubricantes para mejorar la fluidez y la compactación del polvo.
-
Compactación (prensado):
- A continuación, el polvo mezclado se compacta en una forma específica utilizando herramientas de prensado a alta presión o moldes.Este paso forma un "cuerpo verde", que es una estructura coherente pero frágil.
- La compactación puede realizarse a temperatura ambiente o con moldes calentados, según el material y las propiedades deseadas.
- La presión aplicada durante la compactación garantiza que las partículas de polvo estén en estrecho contacto, lo que es esencial para una sinterización eficaz posterior.
-
Sinterización (calentamiento y unión):
- El cuerpo verde se coloca en un horno de sinterización y se calienta a una temperatura justo por debajo del punto de fusión del material primario.Esta temperatura se controla cuidadosamente para evitar la fusión y permitir la unión de las partículas.
- Durante la sinterización, se eliminan los componentes volátiles, como aglutinantes o lubricantes, y las partículas comienzan a unirse por difusión, creando una estructura de baja porosidad.
- Parámetros clave como la temperatura, el volumen de aire, el vacío y el grosor de la capa se controlan meticulosamente para garantizar una sinterización óptima.
-
Fusión y densificación de partículas:
- Al aumentar la temperatura, las partículas se densifican y se fusionan, reduciendo la porosidad y aumentando la resistencia y densidad del material.
- En algunos casos, se utiliza la sinterización en fase líquida (LPS), en la que se forma una fase líquida que fluye hacia los poros restantes, aumentando aún más la densificación.
- Esta etapa puede implicar la formación de microestructuras martensíticas o cristalinas, que contribuyen a las propiedades mecánicas del material.
-
Enfriamiento y solidificación:
- Tras la sinterización, el material se enfría gradualmente para permitir la solidificación en una masa unificada.
- La velocidad de enfriamiento puede influir en la microestructura final y en las propiedades del material, por lo que es un paso crítico en el proceso.
-
Tratamientos posteriores a la sinterización:
- Mecanizado:Las piezas sinterizadas pueden requerir mecanizado con herramientas de diamante o métodos ultrasónicos para conseguir dimensiones y acabados superficiales precisos.
- Montaje:En algunos casos, las piezas cerámicas o metálicas sinterizadas se metalizan y sueldan para unirlas a otros componentes.
- Pueden aplicarse tratamientos adicionales, como el tratamiento térmico o el revestimiento de la superficie, para mejorar propiedades específicas como la dureza o la resistencia a la corrosión.
-
Aplicaciones y variaciones:
- La sinterización se utiliza en varias industrias, incluida la producción de acero (donde el mineral de hierro y el coque se sinterizan para su uso en altos hornos), cerámica y materiales avanzados como los carburos cementados.
- El proceso puede adaptarse a distintos materiales y aplicaciones, como componentes impresos en 3D o piezas de formas complejas que requieren gran precisión.
-
Ventajas de la sinterización:
- Formas complejas:El sinterizado permite la producción de componentes con geometrías intrincadas que son difíciles de conseguir con los métodos de fabricación tradicionales.
- Eficacia del material:El proceso minimiza el desperdicio de material, ya que el polvo sobrante a menudo puede reutilizarse.
- Propiedades a medida:Ajustando la composición, la compactación y los parámetros de sinterización, los fabricantes pueden adaptar las propiedades del material a aplicaciones específicas.
-
Retos y consideraciones:
- Control de parámetros:La obtención de resultados uniformes requiere un control preciso de la temperatura, la presión y otros parámetros de sinterización.
- Gestión de la porosidad:Aunque la sinterización reduce la porosidad, algunas aplicaciones pueden requerir pasos adicionales para eliminar los poros residuales.
- Limitaciones del material:No todos los materiales son adecuados para la sinterización, y algunos pueden requerir equipos o técnicas especializados.
En resumen, el proceso de fabricación por sinterización es un método versátil y eficaz para producir materiales y componentes de alto rendimiento.Controlando cuidadosamente cada paso -desde la preparación del polvo hasta los tratamientos posteriores a la sinterización- los fabricantes pueden crear productos con propiedades a medida y geometrías complejas, lo que convierte al sinterizado en una piedra angular de la fabricación industrial moderna.
Tabla resumen:
Paso | Descripción |
---|---|
Preparación del polvo | Mezcla de materias primas, aditivos y aglutinantes para garantizar la uniformidad y la fluidez. |
Compactación (prensado) | Moldeado a alta presión del polvo en un frágil "cuerpo verde". |
Sinterización (calentamiento) | Calentamiento por debajo del punto de fusión para unir las partículas, reducir la porosidad y aumentar la resistencia. |
Enfriamiento y solidificación | Enfriamiento gradual para solidificar el material e influir en la microestructura. |
Tratamientos posteriores al sinterizado | Mecanizado, ensamblaje o tratamientos adicionales para conseguir precisión y mejorar las propiedades. |
Aplicaciones | Se utiliza en la producción de acero, cerámica y materiales avanzados como los carburos cementados. |
Ventajas | Produce formas complejas, minimiza los residuos y permite adaptar las propiedades de los materiales. |
Desafíos | Requiere un control preciso de los parámetros y puede tener limitaciones de material. |
Descubra cómo el sinterizado puede transformar su proceso de fabricación. contacte hoy con nuestros expertos ¡!