El proceso de pulverización catódica es un método muy utilizado para depositar películas finas sobre sustratos, comúnmente empleado en industrias como la fabricación de semiconductores, la óptica de precisión y el acabado de superficies.Consiste en crear un plasma mediante la ionización de un gas inerte, normalmente argón, dentro de una cámara de vacío.Los iones cargados positivamente del plasma se aceleran hacia un material objetivo cargado negativamente, provocando la expulsión de átomos o moléculas de la superficie del objetivo.A continuación, estas partículas expulsadas viajan a través de la cámara y se depositan sobre un sustrato, formando una película fina, uniforme y adherente.El proceso requiere un control preciso de las condiciones de vacío, la presión del gas y la transferencia de energía para garantizar revestimientos de alta calidad.
Explicación de los puntos clave:
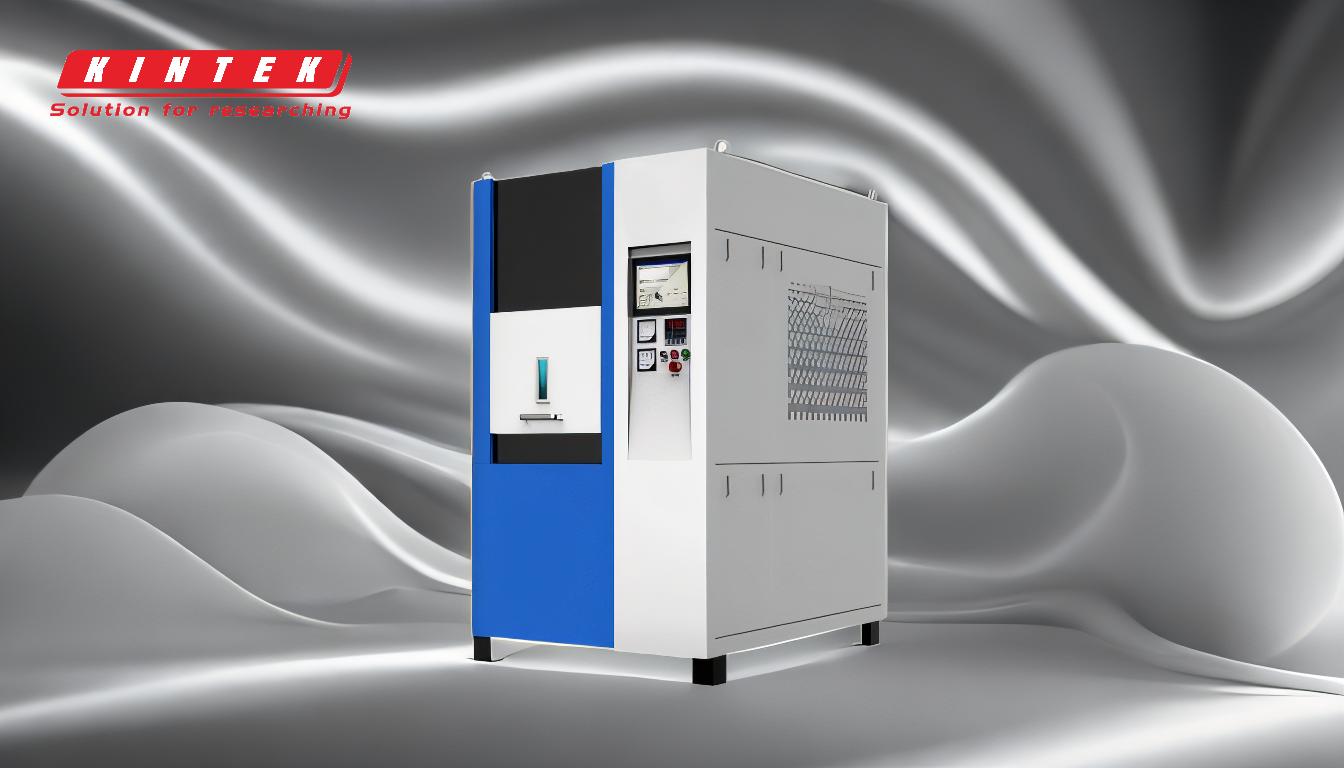
-
Ionización con gas inerte:
- El proceso de sputtering comienza con la introducción de un gas inerte, como el argón, en una cámara de vacío.El gas se ioniza mediante un alto voltaje o excitación electromagnética, creando un plasma compuesto de iones cargados positivamente (por ejemplo, Ar+).
- La elección del gas depende del material objetivo.Para elementos ligeros, se prefiere el neón, mientras que para objetivos más pesados se utilizan elementos más pesados, como el criptón o el xenón, para garantizar una transferencia eficaz del momento.
-
Entorno de vacío:
- El proceso se realiza en condiciones de vacío para eliminar los contaminantes y garantizar un entorno de deposición limpio.La presión de la cámara suele reducirse a aproximadamente 1 Pa (0,0000145 psi) antes de introducir el gas de pulverización catódica.
- Inicialmente, se mantienen presiones más bajas para eliminar la humedad y las impurezas, seguidas de presiones más altas (de 10^-1 a 10^-3 mbar) para el proceso de sputtering propiamente dicho.
-
Transferencia de energía y expulsión de átomos del blanco:
- Los iones cargados positivamente del plasma se aceleran hacia el material objetivo cargado negativamente (cátodo) debido a un alto voltaje aplicado (3-5 kV).
- Al colisionar, los iones transfieren su energía cinética a los átomos del blanco, provocando su expulsión de la superficie.Estas partículas expulsadas son átomos neutros, grupos o moléculas.
-
Deposición de películas finas:
- Los átomos objetivo expulsados se desplazan en línea recta a través de la cámara de vacío y se depositan sobre el sustrato, formando una fina película.
- La película resultante se caracteriza por una excelente uniformidad, densidad y adherencia, lo que la hace adecuada para diversas aplicaciones.
-
Confinamiento del campo magnético:
- A menudo se utiliza un campo magnético para confinar el plasma alrededor del blanco, lo que aumenta la eficacia del bombardeo iónico y garantiza un proceso de deposición más controlado.
- Este campo magnético se crea colocando un electroimán cerca del blanco, lo que también ayuda a mantener un plasma estable.
-
Control de la temperatura:
- La cámara puede calentarse a temperaturas comprendidas entre 150°C y 750°C, en función del material depositado.Este paso de calentamiento mejora la calidad y la adherencia de la película fina.
-
Aplicaciones del sputtering:
- El sputtering se utiliza ampliamente en industrias como el procesamiento de semiconductores, la óptica de precisión y el acabado de superficies debido a su capacidad para producir películas finas de alta calidad con un control preciso del espesor y la composición.
Siguiendo estos pasos, el proceso de sputtering consigue un método altamente controlado y eficaz para depositar películas finas, lo que lo hace indispensable en la fabricación moderna y en la ciencia de materiales.
Cuadro sinóptico:
Aspecto clave | Detalles |
---|---|
Ionización de gases inertes | Argón u otros gases inertes ionizados para crear plasma para sputtering. |
Entorno de vacío | Presión de la cámara reducida a ~1 Pa para una deposición limpia y sin contaminantes. |
Transferencia de energía | Iones acelerados a 3-5 kV para expulsar átomos objetivo para la formación de películas finas. |
Confinamiento del campo magnético | Mejora el control del plasma y la eficacia del bombardeo iónico. |
Control de la temperatura | Cámara calentada entre 150°C y 750°C para mejorar la calidad y la adherencia de la película. |
Aplicaciones | Utilizado en semiconductores, óptica de precisión e industrias de acabado de superficies. |
Descubra cómo el sputtering puede mejorar su proceso de fabricación. contacte con nuestros expertos hoy mismo ¡!