El depósito físico en fase vapor (PVD) es una técnica de revestimiento versátil que se utiliza para depositar películas finas de diversos materiales sobre sustratos.El proceso consiste en vaporizar un material sólido en el vacío y luego condensarlo sobre un sustrato para formar una película fina.El PVD puede depositar una amplia gama de materiales, como metales, aleaciones, cerámicas e incluso algunos materiales orgánicos.La elección del material depende de las propiedades deseadas del revestimiento, como la dureza, la resistencia a la corrosión, la conductividad eléctrica o las propiedades ópticas.Entre los materiales más utilizados en PVD se encuentran el titanio, el circonio, el aluminio, el acero inoxidable, el cobre, el oro y diversos nitruros, carburos y óxidos.Además, los sustratos deben ser compatibles con el vacío y a menudo es necesario un tratamiento previo para garantizar una adhesión y una calidad de película adecuadas.
Explicación de los puntos clave:
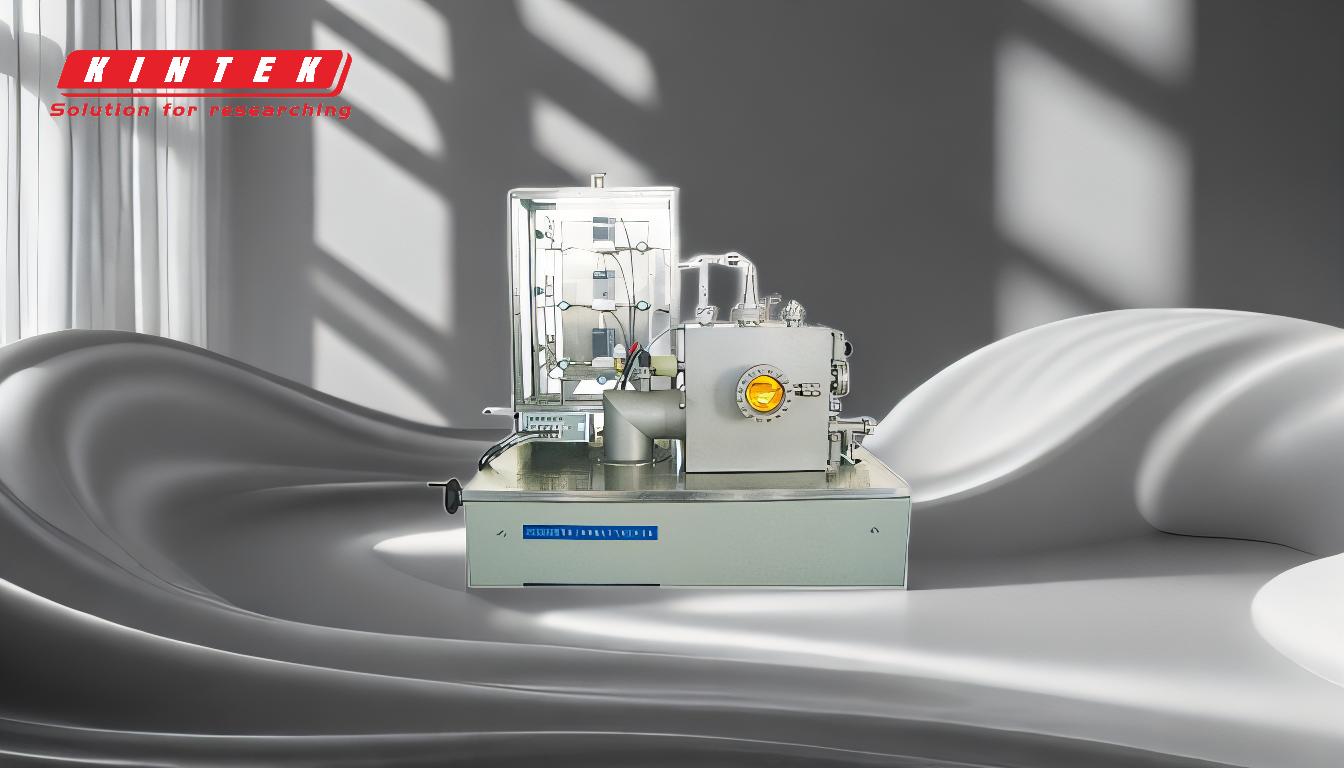
-
Tipos de materiales utilizados en PVD:
- Metales:El PVD se utiliza habitualmente para depositar metales como titanio, circonio, aluminio, acero inoxidable, cobre, oro, cromo, níquel, estaño, platino, paladio y tántalo.Estos metales se eligen por sus propiedades específicas, como la resistencia a la corrosión, la conductividad eléctrica o el atractivo estético.
- Aleaciones:El PVD también puede depositar aleaciones, que son combinaciones de metales diseñadas para conseguir propiedades específicas.Algunos ejemplos son las aleaciones de níquel-cromo y cobre-níquel.
- Cerámica:Los materiales cerámicos, incluidos los nitruros (p. ej., nitruro de titanio), carburos (p. ej., carburo de silicio) y óxidos (p. ej., dióxido de silicio), se depositan a menudo mediante PVD.Estos materiales se valoran por su dureza, resistencia al desgaste y estabilidad térmica.
- Semiconductores y aislantes:El PVD puede depositar materiales semiconductores como el dióxido de silicio (SiO2) y el óxido de indio y estaño (ITO), que se utilizan en aplicaciones electrónicas y ópticas.Los aislantes, como el vidrio, también pueden recubrirse mediante PVD.
- Materiales orgánicos:Aunque menos comunes, algunos materiales orgánicos pueden depositarse mediante PVD, aunque suele ser más difícil debido a su menor estabilidad térmica.
-
Materiales adecuados para PVD:
- Requisitos de vaporización:Los materiales utilizados en PVD deben poder vaporizarse o bombardearse para formar vapor.Esto suele implicar calentar el material a altas temperaturas o utilizar técnicas como el sputtering.
- Compatibilidad con el vacío:El material debe ser estable en condiciones de vacío.Algunos materiales pueden descomponerse o reaccionar bajo vacío, lo que los hace inadecuados para PVD.
- Adherencia y calidad de la película:La calidad de la película depositada, incluida su adhesión al sustrato, es fundamental.Una mala adherencia o calidad de la película puede provocar delaminación u otros defectos.
-
Consideraciones sobre el sustrato:
- Compatibilidad con el vacío:Los sustratos deben ser compatibles con el vacío o estar tratados para serlo.Entre los sustratos más comunes se encuentran los aceros para herramientas, el vidrio, el latón, el zinc y el plástico ABS.
- Tratamiento previo:Los sustratos suelen recibir un tratamiento previo para mejorar la adherencia y la calidad de la película.Esto puede incluir limpieza, recubrimientos orgánicos o galvanoplastia con materiales como níquel y cromo.
-
Aplicaciones de los materiales recubiertos con PVD:
- Aeroespacial y electrónica:El oro se utiliza a menudo en la electrónica aeroespacial por su excelente conductividad y resistencia a la corrosión.
- Herramientas y herramientas de corte:El nitruro de titanio y otros revestimientos duros se utilizan para prolongar la vida útil de herramientas de corte y moldes.
- Recubrimientos ópticos y decorativos:El PVD se utiliza para aplicar revestimientos decorativos y funcionales en artículos como relojes, joyas y piezas de automoción.
- Fabricación de semiconductores:El PVD se utiliza para depositar películas finas de materiales como el dióxido de silicio y el óxido de indio y estaño en la producción de semiconductores y pantallas.
-
Limitaciones y retos:
- Limitaciones materiales:No todos los materiales son adecuados para el PVD.Algunos materiales pueden no vaporizarse eficazmente o degradarse bajo las altas temperaturas o condiciones de vacío requeridas.
- Espesor de la película:El PVD suele depositar películas finas, con espesores que oscilan entre unos pocos nanómetros y varios cientos de nanómetros.Para conseguir recubrimientos más gruesos pueden ser necesarios varios ciclos de deposición.
- Coste y complejidad:Los equipos y procesos de PVD pueden ser caros y complejos, sobre todo para aplicaciones a gran escala o de alta precisión.
En resumen, el PVD es una técnica de revestimiento muy versátil capaz de depositar una amplia gama de materiales, como metales, aleaciones, cerámicas y algunos materiales orgánicos.La elección del material depende de las propiedades deseadas del revestimiento y de la aplicación específica.Los sustratos deben ser compatibles con el vacío y a menudo requieren un tratamiento previo para garantizar una adhesión y una calidad de película adecuadas.Aunque el PVD ofrece numerosas ventajas, también tiene limitaciones, como la idoneidad del material, el grosor de la película y el coste.
Tabla resumen:
Categoría | Materiales | Propiedades clave |
---|---|---|
Metales | Titanio, circonio, aluminio, acero inoxidable, cobre, oro, cromo, etc. | Resistencia a la corrosión, conductividad eléctrica, atractivo estético |
Aleaciones | Níquel-cromo, Cobre-níquel | Propiedades a medida para aplicaciones específicas |
Cerámica | Nitruro de titanio, carburo de silicio, dióxido de silicio | Dureza, resistencia al desgaste, estabilidad térmica |
Semiconductores | Dióxido de silicio (SiO2), óxido de indio y estaño (ITO) | Utilizados en aplicaciones electrónicas y ópticas |
Materiales orgánicos | Uso limitado debido a problemas de estabilidad térmica | Aplicaciones especializadas que requieren revestimientos orgánicos |
¿Está listo para explorar los recubrimientos PVD para su proyecto? Póngase en contacto con nuestros expertos ¡para empezar!