Introducción a los hornos de sinterización por plasma de chispa (SPS)
Los hornos de sinterización por plasma de chispa (SPS) representan una tecnología de vanguardia en el campo de la ciencia de materiales, ofreciendo un enfoque único para la sinterización mediante el uso de corriente de impulsos de CC on-off para la generación de plasma. Esta completa guía profundiza en los entresijos de la tecnología SPS, explorando sus componentes, como el dispositivo de presión axial, el electrodo de punzón refrigerado por agua y la cámara de vacío. Al comprender las características clave y las versátiles aplicaciones de SPS, podemos apreciar cómo esta tecnología revoluciona la sinterización rápida, eficiente y de alta calidad de diversos materiales, desde metales y cerámicas hasta nanomateriales y materiales compuestos.
Características principales de los hornos de sinterización por plasma de chispa
Los hornos de sinterización por plasma de chispa (SPS) han revolucionado el campo de la ciencia de materiales con sus capacidades únicas y tiempos de procesamiento rápidos. Estos hornos utilizan una corriente continua pulsada de alta intensidad para calentar y sinterizar los polvos compactos, ofreciendo varias ventajas claras sobre los métodos de sinterización tradicionales. A continuación, profundizamos en las principales características de los hornos SPS, como el sinterizado rápido, el sinterizado de purificación y activación, el sinterizado de grano fino, el sinterizado a temperatura de amplio rango, el sinterizado de control de densidad y el sinterizado de gradiente de temperatura.
Sinterización rápida
Una de las ventajas más significativas de los hornos SPS es su capacidad para lograr una sinterización rápida. La velocidad de calentamiento puede superar los 500 °C/min, lo que es significativamente más rápido que los métodos tradicionales como el prensado en caliente, el prensado isostático en caliente (HIP) y el sinterizado sin presión. Esta rápida velocidad de calentamiento permite tiempos de sinterización mucho más cortos, reduciendo a menudo el proceso de horas a meros minutos. Las rápidas velocidades de calentamiento y enfriamiento también minimizan los procesos de engrosamiento y ayudan a mantener las nanoestructuras intrínsecas del material tras la densificación completa.
Sinterización de purificación y activación
Los hornos SPS ofrecen un proceso de sinterización de purificación y activación único. La alta corriente continua pulsada induce un efecto de purificación de la superficie de las partículas, que elimina los gases adsorbidos y las películas de óxido. Este proceso de purificación, combinado con el efecto de activación de la superficie de las partículas, permite sinterizar materiales que tradicionalmente son difíciles de sinterizar. Esta característica es especialmente beneficiosa para materiales con requisitos de pureza elevados o sensibles a los contaminantes superficiales.
Sinterización de grano fino
El rápido aumento de la temperatura en los hornos SPS inhibe el crecimiento del grano, lo que permite regular la microestructura y preparar cuerpos sinterizados de grano fino. Esta característica hace del SPS un método excelente para preparar materiales nanocristalinos. Controlando los parámetros de sinterización, los investigadores pueden conseguir el tamaño de grano y la microestructura deseados, lo que resulta crucial para optimizar las propiedades mecánicas, eléctricas y térmicas del material.
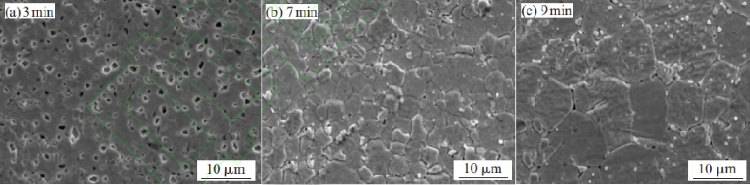
Sinterización a una amplia gama de temperaturas
Los hornos SPS pueden funcionar en una amplia gama de temperaturas, desde bajas temperaturas hasta 2300°C. Esta amplia gama de temperaturas hace que los hornos SPS sean ideales para la sinterización de aleaciones de molibdeno ultrafinas. Este amplio rango de temperaturas hace que los hornos SPS sean versátiles para sinterizar una gran variedad de materiales, incluyendo cerámicas, metales y materiales compuestos. La capacidad de alcanzar altas temperaturas de forma rápida y eficaz es especialmente útil para materiales que requieren un procesamiento a alta temperatura para lograr una densificación completa y unas propiedades óptimas.
Sinterización con control de densidad
Otra característica notable de los hornos SPS es su capacidad para controlar la densidad del cuerpo sinterizado. Desde cuerpos porosos hasta cuerpos sinterizados totalmente densos, los hornos SPS ofrecen un control flexible de la densidad. Esto se consigue ajustando los parámetros de sinterización, como la fuerza aplicada, el recorrido del pistón y la corriente. El control preciso de la densidad es esencial para adaptar las propiedades del material a aplicaciones específicas, como la industria aeroespacial, de automoción y médica.
Sinterización con gradiente de temperatura
Los hornos SPS pueden crear un gradiente de temperatura dentro del molde, lo que permite la sinterización simultánea de materiales con diferentes puntos de fusión. Esta característica es especialmente útil para preparar materiales de gradiente funcional (FGM), en los que diferentes capas o regiones del material requieren diferentes condiciones de procesamiento. La capacidad de crear un gradiente de temperatura (cientos de °C/mm) dentro del molde permite la producción de materiales complejos de varias capas con propiedades y funcionalidades a medida.
En conclusión, los hornos SPS ofrecen una serie de características avanzadas que los convierten en una potente herramienta en el campo de la ciencia de los materiales. Su capacidad para lograr la sinterización rápida, la sinterización de purificación y activación, la sinterización de grano fino, la sinterización a temperatura de amplio rango, la sinterización de control de densidad y la sinterización de gradiente de temperatura los hace versátiles y eficientes para una amplia gama de aplicaciones. A medida que avanzan la investigación y el desarrollo en este campo, los hornos SPS están preparados para desempeñar un papel cada vez más importante en la producción de materiales de alto rendimiento.
Versatilidad en el procesamiento de materiales con SPS
El sinterizado por plasma de chispa (SPS) es una técnica muy eficaz y versátil que se utiliza en la sinterización de una amplia gama de materiales, como metales, cerámicas, nanomateriales y materiales compuestos. Este método aprovecha los impulsos de corriente continua para generar chispas de plasma entre las partículas, lo que facilita el calentamiento rápido y los procesos de densificación. El SPS es conocido por su capacidad para lograr una preparación de materiales de alta calidad con ventajas significativas sobre los métodos tradicionales de sinterización.
Amplia aplicabilidad del SPS
Nanomateriales
La tecnología SPS es especialmente eficaz en la preparación de nanomateriales. Los métodos de sinterización tradicionales suelen tener dificultades para mantener el tamaño de grano a escala nanométrica y lograr una densidad completa. SPS, con su calentamiento rápido y tiempos de síntesis cortos, suprime eficazmente el engrosamiento del grano. Este rápido proceso también permite retener defectos y subestructuras en el polvo, lo que puede ser beneficioso para la síntesis de materiales metaestables y nanomateriales.
Materiales funcionales de gradiente
Los materiales funcionales de gradiente (FGM) son compuestos con una distribución de gradiente en una dirección determinada, que a menudo requieren diferentes temperaturas de sinterización para cada capa. Los métodos tradicionales, como el depósito químico en fase vapor (CVD) y el depósito físico en fase vapor (PVD), resultan costosos y complicados para la producción industrial. El SPS supera estos retos al permitir la sinterización de materiales con gradientes de resistencia térmica, resistencia al desgaste, dureza, conductividad y porosidad, con la capacidad de manejar múltiples capas.
Materiales electromagnéticos
SPS también se utiliza en la producción de diversos materiales electromagnéticos, incluidos elementos de conversión termoeléctrica y materiales utilizados en el campo de la electrónica, como materiales superconductores, materiales magnéticos, materiales dieléctricos, etc. Estos materiales son cruciales para aplicaciones que van desde el almacenamiento de energía hasta la ingeniería biomédica.
Compuestos intermetálicos
Los compuestos intermetálicos, conocidos por su fragilidad y altos puntos de fusión, requieren procesos especializados para su preparación. SPS ofrece un método eficaz para preparar estos compuestos utilizando el autocalentamiento y la activación superficial entre partículas, lo que permite una sinterización rápida y a baja temperatura.
Cerámicas y cermets de alta densidad y grano fino
El proceso SPS acorta significativamente los tiempos de sinterización y reduce las temperaturas aprovechando el calor generado dentro de cada partícula de polvo y los espacios entre ellas. Esto hace que el SPS sea un método excelente para preparar cerámicas y cermets de grano fino y alta densidad, que son esenciales para diversas aplicaciones industriales.
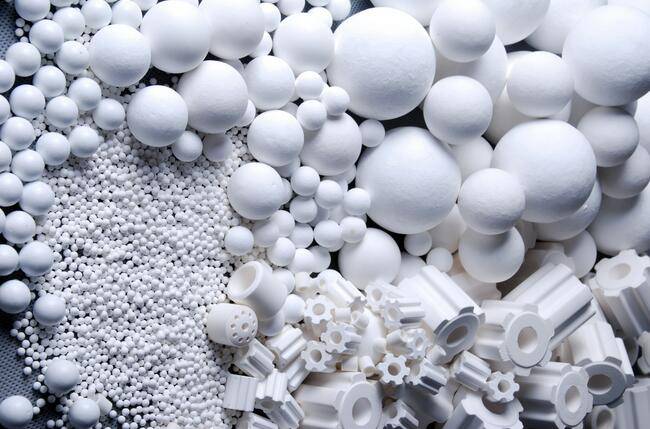
Ventajas del SPS
- Ciclos más cortos: El SPS reduce significativamente los ciclos de sinterización de horas o días a sólo minutos, mejorando la productividad y la capacidad de desarrollo rápido de materiales.
- Temperaturas de sinterización más bajas: Permite sinterizar a temperaturas más bajas en comparación con los procesos convencionales, lo que resulta especialmente beneficioso para los materiales sensibles al calor.
- Control de procesos de alta precisión: SPS proporciona un control preciso de los parámetros de sinterización, como la temperatura y la presión, lo que garantiza resultados óptimos y permite la creación de químicas únicas que no son factibles con los métodos convencionales.
- Versatilidad: Puede densificar una amplia gama de materiales, desde metales de bajo punto de fusión hasta cerámicas de temperatura ultra alta, e incluso unir materiales disímiles que requieren distribuciones de temperatura no uniformes.
Aplicaciones de SPS
La tecnología SPS encuentra aplicaciones en diversos campos, entre ellos:
- Almacenamiento de energía: Baterías de iones de litio de alta capacidad y otros materiales avanzados de almacenamiento de energía.
- Ingeniería biomédica: Cerámica porosa para administración de fármacos y andamiajes para ingeniería de tejidos.
- Cerámica avanzada: Superconductores de alta temperatura y cerámicas piezoeléctricas de alto rendimiento.
- Intermetálicos: Aleaciones avanzadas con propiedades mecánicas, térmicas y eléctricas mejoradas.
- Materiales compuestos: Cerámicas y metales reforzados con propiedades mecánicas mejoradas.
En conclusión, el Spark Plasma Sintering destaca como un método muy versátil y eficiente para la sinterización de diversos materiales, ofreciendo ventajas significativas en términos de control de procesos, eficiencia energética y la capacidad de producir materiales de alta calidad para una amplia gama de aplicaciones.
Facilidad operativa y características de seguridad de los hornos SPS
Los hornos de sinterización por plasma de chispa (SPS) son famosos por su avanzada facilidad de funcionamiento y sus sólidas características de seguridad, que los convierten en la opción preferida en diversas aplicaciones industriales. Estos hornos están diseñados con un enfoque en interfaces fáciles de usar y mecanismos de seguridad integrales para garantizar operaciones eficientes y seguras.
Diseño y sistemas de control fáciles de usar
Los hornos SPS están equipados con sistemas de control de última generación que facilitan su uso. Una característica notable es la integración de interfaces de pantalla táctil y controladores lógicos programables (PLC) para el control central. Esta configuración permite a los operarios supervisar y ajustar fácilmente los parámetros del horno, reduciendo la complejidad del funcionamiento y minimizando el potencial de error humano. El sistema PLC de Allen-Bradley, por ejemplo, es conocido por su facilidad de programación y modificación, lo que simplifica aún más la gestión de las operaciones del horno.
El armario de control de estos hornos está diseñado para alojar todos los controles eléctricos en un armario NEMA 12 estándar, lo que garantiza el cumplimiento de normas de seguridad como la NFPA 70. Este control centralizado no sólo mejora la seguridad, sino que también facilita el mantenimiento y la resolución de problemas. La inclusión de un enclavamiento integrado del interruptor eléctrico principal añade una capa adicional de seguridad al evitar operaciones no autorizadas o accidentales.
Mecanismos de seguridad avanzados
La seguridad es una preocupación primordial en el funcionamiento de los hornos SPS, y estos sistemas están equipados con múltiples capas de protección. Entre las principales características de seguridad se incluyen las alarmas de sobretemperatura y sobrepresión, que alertan a los operarios de posibles peligros en tiempo real. Además, los sistemas mecánicos de protección automática de la presión protegen contra los problemas relacionados con la presión, garantizando la integridad del horno y de los materiales que se procesan.
Los hornos también disponen de funciones de enclavamiento que impiden el funcionamiento en condiciones inseguras. Por ejemplo, los enclavamientos se utilizan para desactivar el horno en caso de falta de electricidad o agua, presión insuficiente o sobretemperatura. Estos enclavamientos son cruciales para evitar accidentes y proteger tanto el equipo como a los operarios.
Las capacidades de control remoto son otra característica de seguridad importante, ya que permiten el diagnóstico remoto de averías y la actualización de programas. Esto no sólo mejora la eficacia del mantenimiento, sino que también reduce el riesgo de exposición a condiciones peligrosas para los técnicos.
Integración de termopares
El control preciso de la temperatura es esencial en los procesos de sinterización, y los hornos SPS utilizan termopares de alta calidad, como los de tipo "S" y tipo "K", para la supervisión y el control precisos de la temperatura. Estos termopares se integran con paneles de toma adecuados para la supervisión y el control del trabajo, lo que garantiza que el proceso de sinterización se mantenga dentro de unos rangos de temperatura seguros y óptimos.
Conclusión
En resumen, la facilidad operativa y las características de seguridad de los hornos SPS están diseñadas para proporcionar una experiencia de sinterización fluida y segura. Con sistemas de control fáciles de usar, mecanismos de seguridad avanzados y un control preciso de la temperatura, estos hornos son ideales para una amplia gama de aplicaciones en el procesamiento de metales, cerámica, nanomateriales, etc. La integración de tecnología moderna y sólidos protocolos de seguridad garantiza que los operarios puedan trabajar de forma eficiente al tiempo que se minimizan los riesgos.
Sistemas avanzados de control y supervisión en SPS
Los sistemas avanzados de control y supervisión forman parte integral del proceso de sinterización por plasma de chispa (SPS), permitiendo una regulación precisa de la temperatura, la presión y la corriente, junto con una adquisición de datos exhaustiva para realizar un seguimiento y analizar los parámetros de sinterización. Estos sistemas son cruciales para garantizar la calidad y reproducibilidad de los materiales sinterizados.
Control automatizado del programa
El proceso SPS comienza con la carga de una cantidad conocida de muestra de polvo seco y molido en una matriz cilíndrica revestida con una lámina de grafito, que facilita la extracción del compacto sinterizado. A continuación, la matriz se coloca dentro de la cámara SPS y se establece el perfil específico de tiempo-temperatura necesario para el experimento. La atmósfera dentro de la cámara se mantiene según sea necesario, ya sea vacío, argón u otros ambientes controlados. La potencia se ajusta al máximo en el modo Auto, y se aplica la carga requerida a la matriz. La posición del eje z se pone a cero y se activa el temporizador antes de pulsar SINTER para iniciar el proceso de sinterización.
Para la medición de la temperatura, SPS utiliza dos tipos de instrumentos: termopares para temperaturas de sinterización inferiores a 1000°C y pirómetros para temperaturas superiores a 1000°C. Se hace pasar un pulso de corriente continua elevada entre los electrodos de grafito y se aplica simultáneamente una presión axial desde el principio del ciclo de sinterización. La muestra se calienta por calentamiento Joule y chispas entre las partículas, lo que provoca una transferencia de calor y masa más rápida de forma instantánea. Tras la sinterización, se desconecta la alimentación y se deja enfriar la muestra.
Sistemas de control informatizados
El sistema de control de los SPS suele estar informatizado y cuenta con un sistema de control automático PLC de pantalla plana táctil que permite cambiar manualmente a los modos automáticos. El software del sistema de control se desarrolla internamente y ofrece una interfaz fácil de usar con supervisión en tiempo real de las condiciones del horno. El sistema es estable y fiable, con una respuesta rápida y una gran capacidad antiinterferencias. El software muestra una pantalla de simulación en color, que integra la visualización de la temperatura y el control de la válvula de vacío para un funcionamiento intuitivo.
El dispositivo puede adoptar diversas curvas para el análisis, como curvas de temperatura, potencia, vacío, temperatura del agua, presión del aire y tiempo de sinterización. Estas curvas permiten analizar fácilmente el proceso de sinterización a partir de datos históricos. El sistema puede generar automáticamente archivos Excel a través de la interfaz USB para su posterior análisis.
El método de control de temperatura utiliza un termopar para temperaturas de hasta 1700 °C, mientras que los infrarrojos toman el relevo para temperaturas superiores a 1700 °C. El sistema admite varias interfaces de comunicación, como RS232, RS422, CAN, LAN y USB, lo que facilita la conexión en red con otros equipos. La interfaz de control del software se visualiza, mostrando dinámicamente el flujo de trabajo para mayor comodidad e intuitividad. Además, el software se puede actualizar gratuitamente de por vida.
Controladores y adquisición de datos
Al igual que otras cámaras de pruebas, SPS ofrece varias opciones de controladores, que van desde sistemas completamente manuales a sistemas totalmente automatizados. Los controladores automatizados permiten a los usuarios establecer los parámetros del proceso y, a medida que se desarrolla el procedimiento, el sistema realiza ajustes en la presión, la temperatura y otros factores programados. Estos sistemas de control son configurables con software personalizable y diversos métodos de recogida de datos. La elección del controlador viene determinada por la criticidad de la aplicación y el tamaño de la cámara de vacío. Las cámaras más pequeñas pueden necesitar sólo un simple medidor para controlar el bombeo y la presión, mientras que las cámaras más grandes pueden exigir un sistema más agresivo y sofisticado.
Componentes de la máquina de sinterización
La máquina SPS está asistida por varios componentes, como una prensa uniaxial, electrodos de punzonado, cámara de vacío, atmósfera controlada, generador de impulsos de CC y unidades de medición de posición, temperatura y presión. El control de la temperatura de sinterización se consigue ajustando parámetros como el tiempo de mantenimiento, la velocidad de rampa, la duración del pulso y la corriente y el voltaje del pulso. La descarga de impulsos de CC genera plasma de chispa, presión de impacto de chispa, calentamiento Joule y un efecto de difusión del campo eléctrico. En el SPS, la sinterización es asistida por el voltaje de pulso CC on-off, que es diferente del prensado en caliente convencional. La aplicación de presión ayuda al flujo plástico del material, y el flujo de corriente de impulsos de CC a través de las partículas se ilustra en diagramas detallados.
En conclusión, los sistemas avanzados de control y supervisión en SPS son esenciales para lograr resultados de sinterización precisos y reproducibles. Estos sistemas permiten realizar ajustes en tiempo real y adquirir datos exhaustivos, garantizando la calidad y consistencia de los materiales sinterizados. Con la integración del control informatizado, el software personalizable y los métodos avanzados de recopilación de datos, la tecnología SPS sigue ampliando los límites de la ciencia y la ingeniería de materiales.
Aplicaciones del sinterizado por plasma de chispa en la ciencia de materiales
El Spark Plasma Sintering (SPS) es una técnica de sinterización versátil y avanzada que ha revolucionado el campo de la ciencia de materiales. Mediante la combinación de presión uniaxial, corriente continua pulsada y calentamiento rápido, el SPS permite la síntesis de una amplia gama de materiales con propiedades y estructuras únicas. Esta sección profundiza en las polifacéticas aplicaciones del SPS, como la sinterización, la unión, el conformado, la modificación de superficies y la síntesis de materiales como electrolitos sólidos y materiales térmicos eléctricos.
Sinterización de materiales avanzados
El SPS es especialmente conocido por su capacidad para sinterizar materiales de alto punto de fusión y nanomateriales de forma eficiente. Las rápidas velocidades de calentamiento (hasta 1.000 °C/min) y los breves tiempos de procesamiento inherentes al SPS ayudan a mantener la nanoestructura de los polvos, evitando el crecimiento de los granos y preservando las propiedades inherentes de las partículas de tamaño nanométrico. Esto convierte a la SPS en un método ideal para producir cerámicas y cermets de alta densidad y grano fino. Por ejemplo, el nitruro de titanio, un material conocido por sus escasas propiedades de sinterización y su fragilidad, puede densificarse a altos niveles mediante SPS, alcanzando densidades cercanas a los valores teóricos a presiones de 1-5 GPa.
Unión y conformado
Además de la sinterización, la SPS también se utiliza para unir materiales distintos y conformar formas complejas. La corriente continua aplicada durante el proceso no sólo calienta el material, sino que también mejora la unión por difusión entre las partículas, facilitando la unión de materiales que tradicionalmente son difíciles de unir, como la cerámica con los metales. Esta capacidad es especialmente útil en las industrias aeroespacial y del automóvil, donde la demanda de materiales compuestos ligeros y de alta resistencia es elevada.
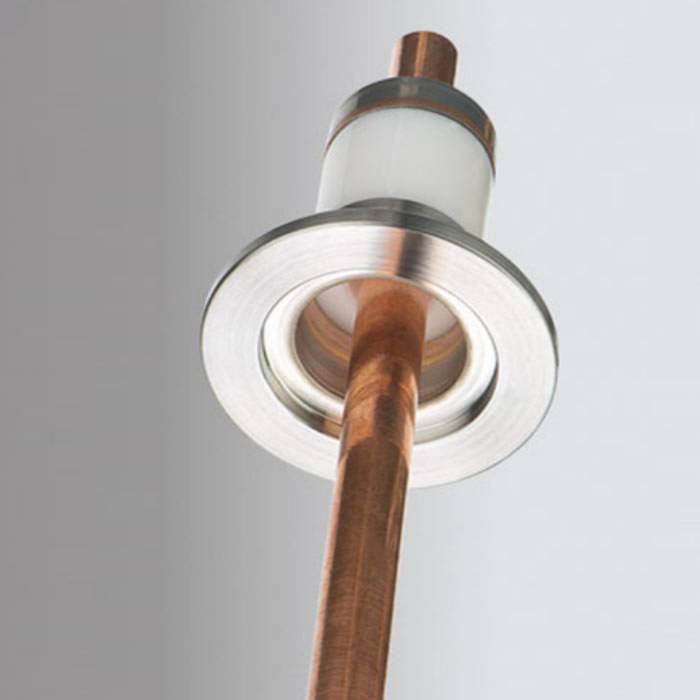
Modificación de superficies
Los SPS también pueden utilizarse para la modificación de superficies, mejorando las propiedades superficiales de los materiales sin afectar a sus características generales. Controlando la densidad de corriente y la presión, se pueden adaptar capas superficiales específicas para conseguir las propiedades deseadas, como una mayor dureza, resistencia al desgaste o resistencia a la corrosión. Esta aplicación es especialmente beneficiosa para materiales de utillaje y componentes expuestos a entornos agresivos.
Síntesis de materiales funcionales
Una de las aplicaciones más significativas de los SPS es la síntesis de materiales funcionales, incluidos los electrolitos sólidos y los materiales térmicos eléctricos. Los electrolitos sólidos, cruciales para aplicaciones en baterías de estado sólido y pilas de combustible, requieren un alto grado de densificación y pureza. Los SPS facilitan la síntesis de estos materiales con una segregación mínima de los límites de grano y una excelente conductividad iónica. Del mismo modo, los materiales térmicos eléctricos, utilizados en diversas aplicaciones de calefacción, pueden sintetizarse con conductividad térmica y resistividad eléctrica controladas mediante parámetros de procesamiento SPS precisos.
Importancia industrial y perspectivas de futuro
La importancia industrial de los SPS radica en su capacidad para producir materiales de alto rendimiento con un consumo energético reducido y tiempos de procesamiento más cortos. La tecnología es especialmente adecuada para la producción de nanomateriales, aleaciones amorfas y materiales funcionales gradientes, que son difíciles de sintetizar con los métodos tradicionales. A medida que la investigación siga descubriendo nuevas aplicaciones y optimizando los parámetros de procesamiento, la tecnología SPS está llamada a desempeñar un papel crucial en el futuro de la ciencia de materiales, impulsando avances en diversas industrias de alta tecnología.
En conclusión, el Spark Plasma Sintering destaca como una tecnología transformadora en la ciencia de los materiales, que ofrece un amplio espectro de aplicaciones, desde la sinterización y la unión hasta la modificación de superficies y la síntesis de materiales funcionales avanzados. Su capacidad para procesar materiales con gran eficacia y precisión la convierte en una herramienta indispensable tanto para investigadores como para profesionales de la industria.
Retos y consideraciones en el uso de la tecnología SPS
La tecnología Spark Plasma Sintering (SPS) ha revolucionado el campo de la ciencia de materiales al permitir la síntesis de materiales avanzados con propiedades únicas. Sin embargo, la aplicación de la tecnología SPS conlleva una serie de retos y consideraciones que deben tenerse en cuenta para lograr unos resultados óptimos de sinterización. Esta sección profundiza en los aspectos críticos de la selección y el mantenimiento de moldes, así como en las consideraciones más generales para un funcionamiento eficaz del SPS.
Selección y mantenimiento de moldes
La elección del material del molde es un factor fundamental en la tecnología SPS. Tradicionalmente, el grafito ha sido el material preferido por su resistencia a altas temperaturas, su excelente conductividad eléctrica y térmica y su estabilidad química. Sin embargo, los moldes de grafito tienen limitaciones como su baja resistencia mecánica, su corta vida útil y la posible contaminación de los materiales sinterizados. Estos problemas obligan a buscar materiales alternativos para los moldes.
Los últimos avances han conducido al desarrollo de materiales de moldeo alternativos, como el carburo cementado, la cerámica conductora y el grafito de fibra de carbono. Cada uno de estos materiales ofrece ventajas únicas, pero también presenta retos. Por ejemplo, los moldes de carburo cementado son más resistentes, pero pueden deformarse a altas temperaturas. La cerámica conductiva ofrece un equilibrio de propiedades, pero suele ser cara. Los moldes de grafito de fibra de carbono combinan las ventajas del grafito con mejores propiedades mecánicas, pero requieren una manipulación cuidadosa para evitar daños.
Mantener la integridad del molde es crucial para obtener resultados de sinterización uniformes. La inspección periódica y la sustitución de los moldes desgastados son esenciales para evitar incoherencias en el proceso de sinterización. Además, una limpieza y acondicionamiento adecuados de los moldes entre usos puede prolongar su vida útil y mantener la calidad de los materiales sinterizados.
Obtención de resultados óptimos de sinterización
Para lograr unos resultados óptimos de sinterización, deben tenerse en cuenta varias consideraciones. Entre ellas se incluyen la selección de los parámetros de sinterización adecuados, el control del entorno de sinterización y la comprensión del mecanismo de sinterización.
Parámetros de sinterización
Los parámetros de sinterización, como la temperatura, la presión y el tiempo de permanencia, desempeñan un papel fundamental en la determinación de las propiedades finales del material sinterizado. Las rápidas velocidades de calentamiento y enfriamiento que se consiguen con los SPS pueden dar lugar a microestructuras no equilibradas, lo que puede ser ventajoso para obtener propiedades únicas de los materiales. Sin embargo, estas velocidades deben controlarse cuidadosamente para evitar un crecimiento excesivo del grano u otros defectos.
Entorno de sinterización
El entorno de sinterización, que incluye la atmósfera y los gradientes de temperatura, puede influir significativamente en el proceso de sinterización. El control de la atmósfera puede evitar la oxidación y otras reacciones químicas que pueden degradar el material. Los gradientes de temperatura dentro del molde pueden provocar una densificación no uniforme, lo que requiere un diseño cuidadoso y la optimización de la configuración de sinterización.
Comprensión del mecanismo de sinterización
El mecanismo de sinterización en SPS implica la generación de un plasma de chispas entre las partículas, lo que facilita un calentamiento y una densificación rápidos. Sin embargo, los mecanismos exactos que rigen este proceso aún no se comprenden del todo y son objeto de investigaciones en curso. Las simulaciones de elementos finitos se han revelado como una valiosa herramienta para estudiar el proceso de sinterización, ya que proporcionan información sobre las distribuciones de temperatura y campo eléctrico dentro del material.
Orientaciones futuras
La mejora continua de la tecnología SPS requiere investigación y desarrollo constantes. Entre las áreas clave que se explorarán en el futuro se encuentran el desarrollo de nuevos materiales para moldes con propiedades mejoradas, la optimización de los parámetros de sinterización mediante técnicas de simulación avanzadas y un conocimiento más profundo del mecanismo de sinterización.
En conclusión, aunque la tecnología SPS ofrece ventajas significativas para la síntesis de materiales avanzados, también presenta varios retos y consideraciones que deben abordarse para lograr resultados óptimos. Seleccionando y manteniendo cuidadosamente los moldes, controlando los parámetros de sinterización y avanzando en el conocimiento del mecanismo de sinterización, podemos seguir ampliando los límites de lo que es posible con la tecnología SPS.
Futuras tendencias e innovaciones en tecnología SPS
La tecnología Spark Plasma Sintering (SPS), conocida por su capacidad de sinterización rápida, ha sido un punto de interés en el campo de la ciencia de materiales debido a su capacidad para producir materiales de alta calidad con propiedades únicas. A medida que la investigación sigue evolucionando, surgen varias tendencias e innovaciones que prometen mejorar la eficacia, ampliar las aplicaciones y mejorar la seguridad de la tecnología SPS.
Industrialización y producción en masa
Una de las tendencias más significativas de la tecnología SPS es su transición hacia la industrialización. Comparado con los métodos tradicionales de sinterización, el SPS ofrece ventajas sustanciales en términos de ahorro de energía y tiempo, mayor eficiencia de producción y control superior sobre el rendimiento del producto. Países como Japón ya han conseguido aplicaciones industriales del SPS, principalmente en la producción de materiales magnéticos, aleaciones duras y materiales funcionales gradientes. Por ejemplo, la empresa japonesa Ohta Seiki ha logrado producir en masa materiales superduros 100% WC mediante SPS y suministra a más de 40 fabricantes de todo el mundo. Por el contrario, la tecnología SPS en otras regiones, como China, permanece en gran medida en fase de investigación de laboratorio, centrándose en la preparación e investigación de procesos de nuevos materiales.
Diversificación de las formas sinterizadas
En la actualidad, la tecnología SPS se limita a producir muestras cilíndricas sencillas debido a las limitaciones del mecanismo de sinterización y de los moldes de grafito. Sin embargo, existe una tendencia creciente a desarrollar la tecnología SPS para crear formas y estructuras más complejas. Este avance ampliaría significativamente la aplicabilidad de la tecnología SPS en diversos sectores de la ingeniería, permitiendo la producción de componentes intrincados que actualmente son inalcanzables.
Síntesis y conexión de materiales
La tecnología SPS no sólo se utiliza para la sinterización de materiales a granel, sino también para la síntesis de polvos, especialmente aquellos que son difíciles de obtener por métodos convencionales. Por ejemplo, la tecnología SPS se ha utilizado para sintetizar polvo de material ZrC a temperatura ultra alta, consiguiendo una gran pureza y un tamaño de grano fino de aproximadamente 100 nm. Además, se está explorando la SPS para la conexión (soldadura) de materiales, incluidas las uniones cerámica-cerámica y cerámica-metal. La capacidad de conectar materiales sin una capa intermedia, mediante la autodifusión potenciada por el campo eléctrico SPS, abre nuevas posibilidades para crear estructuras compuestas robustas y duraderas.
Optimización del rendimiento de los moldes de sinterización
El grafito, aunque se utiliza habitualmente en los SPS por su resistencia a altas temperaturas y su excelente conductividad eléctrica y térmica, tiene limitaciones como su baja resistencia y la posible contaminación de los materiales sinterizados. Existe una tendencia hacia el desarrollo de nuevos materiales para moldes que ofrezcan mayor resistencia, reutilización y menor contaminación. Se están investigando materiales como moldes de carburo cementado, moldes cerámicos conductores y moldes de grafito con fibra de carbono, aunque persisten retos como la deformación a altas temperaturas y los elevados costes.
Avances en simulación y modelización
Comprender el complejo proceso de sinterización en SPS es crucial para optimizar sus parámetros y predecir los resultados. La simulación por elementos finitos se ha revelado como una valiosa herramienta en este sentido, ya que permite a los investigadores analizar las distribuciones de temperatura y campo eléctrico durante la sinterización. Para simular el proceso de sinterización se utilizan programas como ABAQUS, MATLAB y MSC.MARC, que proporcionan información sobre el impacto de diversos parámetros y ayudan a orientar teóricamente la producción.
Funciones de seguridad mejoradas
A medida que la tecnología SPS sigue evolucionando, se presta cada vez más atención a la mejora de sus características de seguridad. Esto incluye el desarrollo de protocolos de funcionamiento más seguros, la mejora de la fiabilidad de los equipos SPS y la garantía de que la tecnología pueda utilizarse en una gama más amplia de entornos sin comprometer la seguridad.
En conclusión, el futuro de latecnología SPSes prometedor gracias a la investigación y el desarrollo en curso para mejorar la eficacia, ampliar las aplicaciones de los materiales y mejorar la seguridad. Estos avances están llamados a revolucionar el campo de la ciencia de materiales, permitiendo la producción de materiales y componentes de alto rendimiento que antes eran inalcanzables. A medida que la tecnología SPS siga madurando, desempeñará sin duda un papel fundamental en la configuración del futuro de la fabricación y la innovación de materiales.
CONTÁCTANOS PARA UNA CONSULTA GRATUITA
Los productos y servicios de KINTEK LAB SOLUTION han sido reconocidos por clientes de todo el mundo. Nuestro personal estará encantado de ayudarle con cualquier consulta que pueda tener. ¡Contáctenos para una consulta gratuita y hable con un especialista del producto para encontrar la solución más adecuada para sus necesidades de aplicación!