Introducción al sinterizado por plasma de chispa (SPS)
El sinterizado por plasma de chispa (SPS) representa un enfoque innovador en las modernas tecnologías de procesamiento de materiales, revolucionando la forma en que se sinterizan los materiales. Este innovador método destaca por emplear pulsos de corriente continua para lograr un calentamiento y una sinterización rápidos, diferenciándose significativamente de las técnicas tradicionales. El proceso único de SPS implica la generación de un plasma de chispas mediante corrientes pulsadas, lo que facilita la creación de materiales con propiedades superiores. A medida que profundicemos en esta completa guía, exploraremos los entresijos del SPS, sus innumerables aplicaciones en diversos sectores y las sustanciales ventajas que ofrece frente a los métodos de sinterización convencionales. Acompáñenos mientras descubrimos el potencial transformador del SPS para dar forma al futuro de la ciencia de los materiales.
Cómo funciona el horno de sinterización por plasma de chispa
El Sinterizado por Plasma de Chispa (SPS), también conocido como Sinterizado por Corriente Eléctrica Pulsada (PECS), Sinterizado Activado por Plasma (PAS), o Tecnología de Sinterizado Asistido por Campo (FAST), es una sofisticada técnica de sinterizado que aprovecha las altas corrientes de CC pulsadas para calentar un polvo compacto dentro de una configuración de matriz/punzón. Este método permite aplicar fuerzas de compresión de hasta 250 kN, con salidas de transformador capaces de alcanzar 10 V y corrientes de hasta 10 kA. Los patrones de corriente continua pulsada pueden ajustarse con segmentos ON y OFF que van de 0 a 255 ms, lo que permite un control preciso del proceso de sinterización.
El proceso SPS se caracteriza por sus rápidas velocidades de calentamiento y enfriamiento, que pueden superar los 1.000 °C/min y los 400 °C/min respectivamente, en función del tamaño y el diseño de la herramienta. Este rápido ciclo térmico minimiza los procesos de engrosamiento a bajas temperaturas y preserva las nanoestructuras intrínsecas incluso después de la densificación completa. La temperatura dentro del horno SPS se controla mediante un pirómetro central que enfoca el fondo de un orificio en el punzón superior, lo que garantiza una medición precisa de la temperatura independientemente de las propiedades o el tamaño de la muestra. Se puede conseguir una monitorización adicional de la temperatura utilizando un pirómetro externo y termopares flexibles colocados en varios lugares.
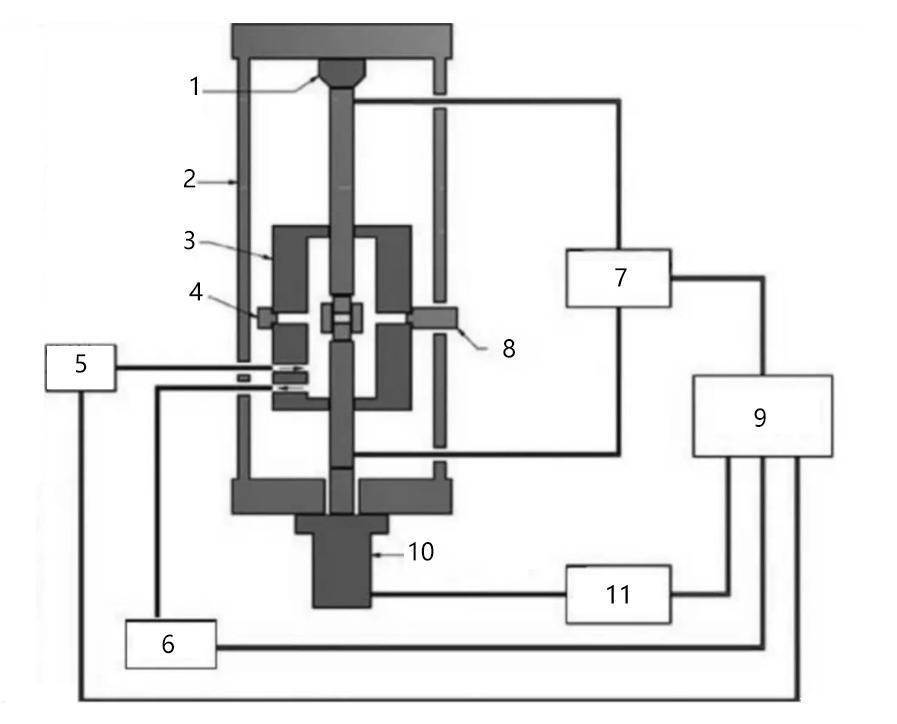
1. Unidad de carga 2. Bastidor de carga 3. Cámara de vacío 4. Ventana de observación 5. Canal de gas inerte 6. Bomba de vacío 7. Interruptor de impulsos 8. Medidor de temperatura 9. Sistema de control 10. Cilindro hidráulico 11. Sistema hidráulico
Los componentes clave de un horno SPS incluyen el dispositivo de presión axial, el electrodo de punzonado refrigerado por agua y la cámara de vacío. El dispositivo de presión axial aplica la fuerza de compresión necesaria, mientras que los electrodos de punzonado refrigerados por agua ayudan a gestionar el calor generado durante el proceso. La cámara de vacío, junto con un sistema de control de la atmósfera que puede alternar entre entornos de vacío y argón, garantiza unas condiciones de sinterización óptimas. La fuente de alimentación de impulsos de CC, junto con un sistema de agua de refrigeración, medición de desplazamiento, medición de temperatura y unidades de control de seguridad, completan la configuración del SPS, facilitando un control exhaustivo del proceso y la programación del ciclo de sinterización a través de una interfaz de pantalla táctil fácil de usar.
El horno SPS se utiliza ampliamente para sinterizar una amplia gama de materiales, como cerámicas, cermets y metales. Sus principales ventajas técnicas residen en sus elevadas velocidades de calentamiento y enfriamiento, que reducen significativamente los tiempos de procesamiento. La alta corriente pulsada no sólo mejora la densificación en materiales conductores de la electricidad, sino que también activa múltiples mecanismos de sinterización, como la eliminación del óxido superficial, la electromigración y la electroplasticidad. Esta combinación de presión mecánica, campo eléctrico y campo térmico mejora significativamente la unión y densificación entre partículas, haciendo del SPS un método preferido para la preparación de materiales de alto rendimiento.
En resumen, el proceso de sinterización por plasma de chispa es un método altamente eficaz y controlado para la densificación de materiales, que ofrece tiempos de procesamiento rápidos y la capacidad de mantener microestructuras finas. Sus aplicaciones abarcan diversos campos, desde la cerámica avanzada hasta los compuestos metálicos, lo que pone de relieve su versatilidad e importancia en la ciencia y la ingeniería de materiales modernas.
Ventajas del uso del SPS en el procesamiento de materiales
El sinterizado por plasma de chispa (SPS) ha revolucionado el campo del procesamiento de materiales al ofrecer ventajas significativas sobre las técnicas tradicionales de sinterizado. El SPS es una técnica de sinterización asistida por campo que utiliza tanto la temperatura como la presión para lograr una rápida densificación de los materiales. Este método es especialmente eficaz para sinterizar una amplia gama de materiales, como cerámicas, metales y materiales compuestos, con notable eficacia y precisión.
Velocidades de sinterización rápidas
Una de las ventajas más notables del SPS es su capacidad para lograr tasas de sinterización rápidas. Los métodos de sinterización tradicionales, como el prensado en caliente y la sinterización sin presión, pueden tardar varias horas en lograr la densificación deseada. En cambio, el SPS puede densificar materiales en cuestión de minutos. Esta rápida sinterización es posible gracias a las altas velocidades de calentamiento, que pueden superar los 500 °C por minuto. Por ejemplo, alcanzar una temperatura de 1.200 °C puede lograrse en tan sólo 4 minutos con SPS, en comparación con las 2 a 4 horas de los métodos convencionales. Esta velocidad no sólo aumenta la productividad, sino que también reduce el consumo de energía y los costes operativos.
Sinterización de grano fino
El SPS facilita la sinterización de grano fino, que es crucial para mejorar las propiedades mecánicas y físicas de los materiales sinterizados. Las rápidas velocidades de calentamiento inhiben el crecimiento del grano, lo que permite crear materiales con microestructuras controladas. Esto es especialmente beneficioso para la producción de materiales nanocristalinos, en los que el mantenimiento de tamaños de grano pequeños es esencial para conseguir propiedades superiores. El sinterizado de grano fino también mejora la homogeneidad de los productos sinterizados, lo que se traduce en un rendimiento más uniforme y fiable.
Capacidad para controlar los gradientes de densidad y temperatura
El SPS proporciona un excelente control de los gradientes de densidad y temperatura en los materiales sinterizados. Este nivel de control se consigue mediante la aplicación simultánea de temperatura y presión, lo que permite realizar ajustes precisos en el proceso de sinterización. El control de la densidad es especialmente importante para crear materiales con niveles de porosidad específicos o lograr una densificación completa. Además, el SPS puede crear gradientes de temperatura dentro del molde, lo que permite la sinterización simultánea de materiales con diferentes puntos de fusión. Esta capacidad es inestimable para la producción de materiales con gradientes funcionales (FGM), en los que la composición y las propiedades varían espacialmente.
Eficiencia y compacidad de los hornos SPS
Los hornos SPS están diseñados para ser altamente eficientes y compactos, lo que los hace ideales tanto para la investigación como para aplicaciones industriales. El diseño compacto de los hornos SPS reduce el espacio necesario y permite integrarlos fácilmente en las líneas de producción existentes. Además, la eficiencia de los hornos SPS se ve reforzada por su capacidad para alcanzar velocidades de calentamiento y enfriamiento rápidas, lo que contribuye aún más al ahorro de energía y a la reducción de los costes operativos. El mecanismo de calentamiento interno, que implica el calentamiento Joule del molde de grafito y de la briqueta de polvo, garantiza una distribución uniforme del calor y minimiza la pérdida de calor, optimizando así el proceso de sinterización.
Sinterización por purificación y activación
SPS también ofrece ventajas únicas en términos de sinterización de purificación y activación. El proceso puede eliminar los gases adsorbidos y las películas de óxido de las superficies de las partículas, lo que da lugar a interfaces más limpias y una mejor unión. Este efecto de purificación, combinado con la activación de las superficies de las partículas, permite sinterizar materiales que de otro modo serían difíciles de procesar. Esta capacidad amplía la gama de materiales que pueden sinterizarse eficazmente mediante SPS, incluidos los materiales cerámicos y compuestos avanzados.
En conclusión, el sinterizado por plasma de chispa (SPS) ofrece multitud de ventajas que lo convierten en una opción superior para el procesamiento de materiales. Sus rápidas velocidades de sinterización, su capacidad de sinterización de grano fino, el control de la densidad y del gradiente de temperatura, su eficiencia y su compacidad lo convierten en una herramienta inestimable tanto para la investigación como para las aplicaciones industriales. Aprovechando estas ventajas, el SPS sigue ampliando los límites de la ciencia y la ingeniería de materiales, permitiendo el desarrollo de materiales innovadores y de alto rendimiento.
Aplicaciones del SPS en diversas industrias
La tecnología Spark Plasma Sintering (SPS) ha revolucionado los procesos de fabricación en múltiples industrias, permitiendo la creación de materiales avanzados con propiedades únicas. El SPS es especialmente conocido por su capacidad para producir materiales de alta densidad y grano fino de forma rápida y a temperaturas relativamente bajas, lo que lo convierte en el método preferido para la síntesis de nanomateriales, cerámicas, materiales compuestos e implantes médicos.
Nanomateriales
Una de las aplicaciones más significativas de la SPS es la preparación de nanomateriales. Los nanomateriales presentan propiedades mecánicas y físicas excepcionales debido a su pequeño tamaño de grano, que aumenta su resistencia y plasticidad. Los SPS facilitan la síntesis de estos materiales al inhibir el crecimiento del grano durante el proceso de sinterización. El rápido calentamiento y los cortos tiempos de sinterización inherentes a la SPS ayudan a mantener el tamaño de grano a escala nanométrica, que es crucial para el rendimiento de los nanomateriales. Esta técnica es especialmente eficaz para sinterizar polvos obtenidos mediante métodos como la aleación mecánica, que a menudo resultan difíciles de consolidar con los métodos tradicionales.
Cerámicas y cermets
El SPS también se utiliza ampliamente en la producción de cerámicas y cermets de alta densidad y grano fino. El mecanismo de calentamiento único del SPS, en el que cada partícula de polvo y los poros entre ellas actúan como fuentes de calor, permite una rápida densificación y una reducción significativa de los tiempos y temperaturas de sinterización. Este método es muy ventajoso para la producción industrial, ya que ahorra energía y mejora la eficacia de la producción. La capacidad de producir cerámicas con alta densidad y estructura de grano fino aumenta su resistencia mecánica y durabilidad, lo que las hace adecuadas para diversas aplicaciones de ingeniería.
Materiales funcionales gradientes
Los materiales funcionales gradientes, que tienen una distribución gradiente en ciertas direcciones, son otra área en la que el SPS ha hecho contribuciones significativas. Los métodos de sinterización tradicionales tienen dificultades con las diferentes temperaturas de sinterización necesarias para cada capa en los materiales de gradiente. El SPS, sin embargo, puede gestionar eficazmente este gradiente, permitiendo la producción a escala industrial de estos complejos materiales. El proceso de sinterización controlada del SPS garantiza que cada capa alcance las propiedades deseadas sin comprometer la integridad de la estructura global.
Implantes médicos
En el campo médico, el SPS se utiliza para fabricar implantes con propiedades mecánicas y biocompatibilidad adaptadas. La capacidad de controlar con precisión las condiciones de sinterización permite crear implantes con propiedades mecánicas específicas que se adaptan al hueso humano, mejorando su funcionalidad y longevidad. Además, los SPS pueden utilizarse para producir estructuras porosas que faciliten el crecimiento óseo, mejorando la integración de los implantes con el tejido circundante.
Materiales compuestos y nanoestructurados
Los SPS son fundamentales para la fabricación de materiales compuestos y nanoestructurados con propiedades mejoradas, como características magnéticas, piezoeléctricas, termoeléctricas y ópticas. El rápido proceso de sinterización del SPS ayuda a mantener la nanoestructura de los materiales, que es crucial para su rendimiento. Por ejemplo, el SPS se utiliza en la sinterización de nanotubos de carbono para desarrollar electrodos de emisión de electrones de campo, lo que demuestra su versatilidad en el tratamiento de distintos tipos de materiales.
En conclusión, el sinterizado por plasma de chispa se ha convertido en una técnica versátil y potente con aplicaciones en diversos sectores. Su capacidad para producir materiales avanzados de alta calidad con propiedades únicas la convierte en una herramienta indispensable en la fabricación moderna. A medida que la investigación y el desarrollo en este campo sigan avanzando, se espera que las aplicaciones potenciales del SPS se amplíen aún más, impulsando la innovación en la ciencia y la ingeniería de materiales.
Casos prácticos: Aplicaciones de SPS con éxito
La tecnología Spark Plasma Sintering (SPS) ha revolucionado el campo de la ciencia de materiales, permitiendo la rápida sinterización y densificación de una amplia gama de materiales con propiedades mejoradas. En esta sección se presentan varios estudios de casos que ponen de relieve las aplicaciones con éxito del SPS tanto en entornos de investigación como industriales, demostrando su versatilidad y eficacia.
Materiales de almacenamiento de energía
Una de las aplicaciones más significativas de la SPS es el desarrollo de materiales avanzados para el almacenamiento de energía. Por ejemplo, la SPS se ha utilizado para producir baterías de iones de litio de alta capacidad con un rendimiento mejorado. Controlando con precisión los parámetros de sinterización, los investigadores han podido crear materiales para baterías con mayores densidades energéticas y ciclos de vida mejorados. Según algunos estudios, las baterías de iones de litio procesadas con SPS han demostrado un aumento del 20% en la capacidad de almacenamiento de energía en comparación con los métodos convencionales, lo que las hace ideales para su uso en vehículos eléctricos y aparatos electrónicos portátiles.
Ingeniería biomédica
En el campo de la ingeniería biomédica, los SPS han sido fundamentales en la creación de cerámicas porosas para la administración de fármacos y andamios para la ingeniería de tejidos. Estos materiales requieren un control preciso de su microestructura para garantizar su compatibilidad con los sistemas biológicos. La SPS permite fabricar estructuras muy porosas con poros de tamaño controlado, que son cruciales para la administración eficaz de fármacos y el crecimiento de los tejidos. Por ejemplo, los andamiajes de hidroxiapatita procesados con SPS se han utilizado en la ingeniería de tejidos óseos, demostrando una biocompatibilidad y una resistencia mecánica superiores a las de los métodos tradicionales.
Cerámica avanzada
Los SPS también se han utilizado ampliamente en la producción de cerámicas avanzadas, como superconductores de alta temperatura y cerámicas piezoeléctricas de alto rendimiento. Estos materiales son fundamentales para aplicaciones que van desde la transmisión de energía a sensores y actuadores. El SPS permite densificar estas cerámicas a temperaturas más bajas y en menos tiempo, conservando sus propiedades únicas. Por ejemplo, la SPS se ha utilizado para producir superconductores de óxido de itrio, bario y cobre (YBCO) con densidades cercanas a las teóricas, mejorando significativamente sus temperaturas de transición superconductora.
Intermetálicos y compuestos
La versatilidad de la SPS se demuestra también en el procesamiento de intermetálicos y materiales compuestos. La SPS se ha utilizado para crear aleaciones avanzadas con propiedades mecánicas, térmicas y eléctricas mejoradas. Por ejemplo, la SPS se ha empleado para sintetizar aleaciones intermetálicas de aluminuro de titanio (TiAl), que presentan una resistencia superior a altas temperaturas y a la oxidación. Además, la SPS ha permitido la producción de cerámicas y metales reforzados con propiedades mecánicas mejoradas, como los compuestos de matriz de titanio con partículas cerámicas incrustadas, que dan como resultado materiales de alta resistencia y resistencia al desgaste.
Aplicaciones industriales
En entornos industriales, el SPS se ha adoptado para la producción de diversos materiales, como materiales magnéticos, materiales duros y materiales funcionales gradientes. Por ejemplo, empresas japonesas como Ohta Seiki han implantado con éxito el SPS para la producción en masa de materiales superduros 100% WC, suministrando a más de 40 fabricantes en Japón y en el extranjero. Estos materiales se utilizan en una amplia gama de aplicaciones, desde herramientas de corte hasta componentes electrónicos, lo que demuestra la escalabilidad industrial del SPS.
Conclusión
Los casos prácticos aquí presentados ilustran la amplia aplicabilidad de los SPS en diversos campos, desde el almacenamiento de energía hasta la ingeniería biomédica y los materiales avanzados. La capacidad del SPS para sinterizar y densificar rápidamente materiales a bajas temperaturas, junto con su preciso control del proceso, lo convierten en una herramienta inestimable para los científicos e ingenieros de materiales. A medida que avancen la investigación y el desarrollo, se espera que las aplicaciones potenciales del SPS se amplíen aún más, consolidando su posición como tecnología líder en el procesamiento de materiales.
Retos y consideraciones en SPS
La implantación de la tecnología Spark Plasma Sintering (SPS) presenta varios retos y consideraciones que las organizaciones deben abordar para aprovechar plenamente sus ventajas. Entre ellos se incluyen los elevados costes de los equipos, las complejidades operativas y la necesidad de formación especializada. Comprender estos retos y desarrollar estrategias para superarlos es crucial para el éxito de la integración y utilización de la tecnología SPS.
Coste de los equipos
Uno de los principales obstáculos a la adopción de la tecnología SPS es la elevada inversión inicial que requieren los equipos. Los sistemas SPS son sofisticados e incluyen características avanzadas como un control preciso de la temperatura y la presión, sistemas de vacío y fuentes de alimentación especializadas. Estos componentes no sólo aumentan el coste inicial, sino que también requieren un mantenimiento y calibración periódicos para garantizar un rendimiento óptimo.
Complejidades operativas
Las operaciones de SPS implican múltiples etapas, como la creación de vacío, la aplicación de presión, el calentamiento por resistencia y el enfriamiento controlado. Cada etapa requiere una supervisión y un ajuste minuciosos para evitar defectos y garantizar las propiedades deseadas del material. La complejidad de estas operaciones requiere un alto nivel de conocimientos técnicos y una atención meticulosa a los detalles, lo que puede suponer un reto para las organizaciones sin experiencia previa en técnicas avanzadas de sinterización.
Formación especializada
Dada la naturaleza técnica de los SPS, el personal implicado en el funcionamiento y mantenimiento de los equipos debe recibir una formación especializada. Esta formación debe abarcar no sólo el funcionamiento básico del sistema SPS, sino también temas avanzados como la optimización del proceso, la resolución de problemas y los protocolos de seguridad. El coste y el tiempo necesarios para esta formación pueden ser considerables y retrasar la implantación de la tecnología sanitaria y fitosanitaria.
Estrategias para superar los retos
Para superar estos retos, las organizaciones pueden adoptar varias estrategias:
-
Inversión en equipos de alta calidad: Aunque el coste inicial es elevado, invertir en equipos fiables y de alta calidad puede reducir los costes operativos y de mantenimiento a largo plazo. Elegir equipos de fabricantes reputados con sólidas redes de asistencia y servicio también puede ayudar a mitigar los problemas que surjan durante el funcionamiento.
-
Colaboración y asociaciones: Asociarse con instituciones de investigación u otras empresas con experiencia en MSF puede aportar información y apoyo valiosos. Los proyectos de colaboración pueden ayudar a compartir los costes y los conocimientos necesarios para una implantación satisfactoria.
-
Formación y desarrollo continuos: Invertir en la formación continua del personal puede garantizar que se mantengan al día de las últimas técnicas y las mejores prácticas en materia de MSF. Esto puede conseguirse mediante talleres, cursos en línea y sesiones de formación práctica.
-
Optimización de procesos: El desarrollo de procesos sólidos, bien documentados y estandarizados puede ayudar a reducir la variabilidad y mejorar la coherencia de los resultados. Esto implica una cuidadosa experimentación y validación para identificar las condiciones óptimas para cada material y aplicación.
-
Centrarse en la investigación y el desarrollo: Involucrarse en la investigación y el desarrollo continuos puede ayudar a las organizaciones a mantenerse a la vanguardia de la tecnología sanitaria y fitosanitaria. Esto puede implicar la exploración de nuevos materiales, la optimización de los procesos existentes y el desarrollo de aplicaciones innovadoras para los componentes producidos mediante SPS.
Conclusión
Aunque la implantación de la tecnología sanitaria y fitosanitaria presenta varios retos, éstos pueden gestionarse eficazmente con las estrategias e inversiones adecuadas. Si se abordan los elevados costes, las complejidades operativas y los requisitos de formación, las organizaciones pueden liberar todo el potencial de la tecnología SPS y lograr avances significativos en la ciencia de los materiales y la fabricación.
Tendencias futuras en el sinterizado por plasma de chispa
La tecnología Spark Plasma Sintering (SPS), conocida por su rápida capacidad de sinterización a temperaturas relativamente bajas, sigue evolucionando, ofreciendo avances significativos en eficiencia, escalabilidad y diversidad de aplicaciones. A medida que crece la demanda de nuevos materiales y procesos de fabricación eficientes, el SPS se sitúa a la vanguardia de la innovación tecnológica en la ciencia de los materiales.
Mejoras en la eficiencia
Una de las principales áreas de interés de la tecnología SPS es la mejora de su eficiencia. Los métodos tradicionales de sinterización pueden llevar mucho tiempo y consumir mucha energía, mientras que el SPS reduce significativamente tanto el tiempo de procesamiento como el consumo de energía. Los desarrollos futuros pretenden optimizar aún más estos aspectos perfeccionando las técnicas de corriente pulsada y mejorando los sistemas de control de los dispositivos SPS. Por ejemplo, los avances en los sistemas de alimentación y control podrían permitir un control más preciso de la temperatura y la presión, lo que daría lugar a procesos de sinterización más eficientes.
Mejoras de la escalabilidad
La escalabilidad es otro aspecto crítico de la tecnología SPS. En la actualidad, la tecnología SPS se utiliza principalmente en laboratorios y en la producción a pequeña escala. Sin embargo, para satisfacer la demanda industrial, los futuros sistemas SPS tendrán que manejar volúmenes mayores y formas más complejas. Los investigadores están explorando nuevos materiales y diseños de moldes que puedan soportar mayores presiones y temperaturas, garantizando la integridad y reutilización de los moldes. Además, la integración de la robótica y la automatización avanzadas en los equipos de SPS podría facilitar la producción de piezas más grandes y complejas, convirtiendo el SPS en una opción viable para la fabricación de grandes volúmenes.
Expansión a nuevos tipos de materiales e industrias
La tecnología SPS se ha utilizado tradicionalmente para sinterizar metales y cerámica. Sin embargo, sus capacidades únicas ofrecen potencial para expandirse a nuevos tipos de materiales e industrias. Es probable que la investigación futura se centre en la aplicación de la tecnología SPS a una gama más amplia de materiales, como polímeros, materiales compuestos y nanomateriales. Esta expansión podría abrir nuevas aplicaciones en sectores como la electrónica, la industria aeroespacial y la ingeniería biomédica, donde el control preciso de las propiedades de los materiales es crucial.
Beneficios medioambientales y económicos
Los beneficios medioambientales y económicos del SPS también impulsan su desarrollo futuro. El proceso de producción de SPS, eficiente desde el punto de vista energético y con un bajo nivel de residuos, está en consonancia con los objetivos mundiales de sostenibilidad. Dado que las industrias buscan cada vez más soluciones de fabricación respetuosas con el medio ambiente, el SPS podría convertirse en el método preferido para producir materiales de alto rendimiento. Además, la reducción de los tiempos de procesamiento y los menores costes energéticos asociados al SPS pueden suponer un importante ahorro económico, lo que lo convierte en una opción atractiva para los fabricantes.
Integración y colaboración tecnológicas
Por último, es probable que el futuro de la tecnología SPS implique una mayor integración con otras tecnologías de fabricación avanzada y esfuerzos de colaboración entre distintos campos. Por ejemplo, la combinación de SPS con técnicas de fabricación aditiva podría conducir a la creación de procesos de fabricación híbridos que aprovechen los puntos fuertes de ambas tecnologías. Además, la investigación interdisciplinar en la que participen la ciencia de los materiales, la ingeniería eléctrica y la ingeniería mecánica podría dar lugar a grandes avances en la comprensión y optimización del proceso SPS.
En conclusión, el futuro del sinterizado por plasma de chispa es prometedor, con posibles avances que lo convertirán en una tecnología más eficiente, escalable y versátil. A medida que continúen la investigación y el desarrollo, el SPS podría revolucionar la forma en que producimos materiales avanzados, contribuyendo a las innovaciones en diversas industrias y promoviendo prácticas de fabricación sostenibles.
Conclusión: El papel de los SPS en la ciencia de los materiales
En conclusión, elsinterización por plasma de chispa (SPS) destaca como una tecnología transformadora en el campo de la ciencia de los materiales. Su capacidad para sinterizar rápidamente materiales a niveles de grano fino, junto con su eficacia y versatilidad, sitúan al SPS como piedra angular en el procesamiento moderno de materiales. De cara al futuro, el SPS está preparado para impulsar innovaciones significativas, ampliando sus aplicaciones a diversos sectores y allanando el camino para el desarrollo de materiales avanzados de alto rendimiento. La continua evolución y adopción de la tecnología SPS marcará sin duda el futuro de la ciencia de los materiales, ofreciendo nuevas posibilidades y soluciones a los complejos retos que plantean los materiales.
CONTÁCTANOS PARA UNA CONSULTA GRATUITA
Los productos y servicios de KINTEK LAB SOLUTION han sido reconocidos por clientes de todo el mundo. Nuestro personal estará encantado de ayudarle con cualquier consulta que pueda tener. ¡Contáctenos para una consulta gratuita y hable con un especialista del producto para encontrar la solución más adecuada para sus necesidades de aplicación!