Introducción al depósito en fase vapor de silicio-carbono (VPD-SiC)
Ventajas del VPD-SiC
El VPD-SiC presenta mejoras sustanciales con respecto a los materiales convencionales en varias áreas críticas, lo que lo convierte en una opción superior para aplicaciones de baterías avanzadas. En primer lugar, laeficiencia de primer giro del VPD-SiC es notablemente superior, lo que se traduce en ciclos iniciales de carga-descarga más eficaces y en una menor pérdida de energía. Esta mejora es fundamental para el rápido despliegue de baterías de alto rendimiento en diversas industrias.
Además, el VPD-SiC aumenta significativamente ladensidad energética. Al integrar partículas de silicio dentro de una matriz porosa de carbono, el material puede almacenar más energía por unidad de volumen o masa, ofreciendo tiempos de funcionamiento más largos y frecuencias de carga reducidas. Esto resulta especialmente ventajoso para la electrónica portátil, los vehículos eléctricos y los sistemas de almacenamiento de energías renovables.
Elrendimiento cíclico del VPD-SiC también es superior, con una mayor estabilidad en ciclos repetidos de carga y descarga. Esta durabilidad es crucial para la longevidad y fiabilidad de los sistemas de baterías, ya que garantiza un rendimiento constante durante periodos prolongados sin degradación.
Además, el VPD-SiC mitiga eficazmente laexpansión celular de los ánodos tradicionales de silicio. Esta reducción de la expansión del volumen durante los procesos de carga y descarga ayuda a mantener la integridad estructural de la batería, aumentando así su vida útil y su seguridad.
En términos dereducción de costesVPD-SiC ofrece un potencial de industrialización prometedor. El proceso de síntesis simplificado, combinado con el uso eficiente de las materias primas, puede dar lugar a métodos de producción más rentables. Este beneficio económico es esencial para aumentar la producción y hacer más accesibles las baterías de alto rendimiento.
En general, las amplias ventajas del VPD-SiC en cuanto a eficiencia de primer giro, densidad energética, rendimiento en ciclos, expansión de celdas y reducción de costes lo convierten en un material transformador para la próxima generación de tecnologías de baterías.
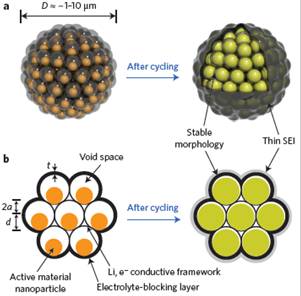
Principales etapas de la tecnología VPD-SiC
El proceso de deposición en fase de vapor (VPD) para crear materiales de ánodo de silicio-carbono (SiC) es un procedimiento de varias etapas que integra varios pasos críticos para lograr soluciones de almacenamiento de energía de alto rendimiento. La tecnología puede dividirse en tres fases principales: la preparación de un esqueleto de carbono poroso, la deposición de partículas de silicio y la aplicación de un recubrimiento de carbono.
-
Preparación del esqueleto de carbono poroso:
- La base del proceso VPD-SiC, el esqueleto de carbono poroso, se elabora meticulosamente para proporcionar un marco robusto que mejore el rendimiento general del material. Este paso es esencial para crear una estructura con una elevada superficie específica y una excelente conductividad eléctrica, que son vitales para mejorar la capacidad del ánodo y la estabilidad del ciclo.
-
Deposición de partículas de silicio:
- Una vez establecido el esqueleto de carbono poroso, el siguiente paso consiste en depositar partículas de silicio dentro de los poros. Esto se consigue normalmente mediante el uso de gas silano, que desempeña un papel fundamental en la formación de silicio dentro de la matriz de carbono. El proceso de deposición es muy sensible a parámetros como la temperatura y el caudal de gas, que deben controlarse con precisión para garantizar una distribución uniforme de las partículas y unas propiedades óptimas del material.
-
Recubrimiento de capas de carbono:
- El último paso de la tecnología VPD-SiC es el recubrimiento del compuesto de silicio-carbono con una capa de carbono. Esta capa cumple múltiples funciones: protege las partículas de silicio de la degradación, mejora la conductividad eléctrica del material y proporciona estabilidad mecánica adicional. El recubrimiento de carbono suele aplicarse mediante deposición química de vapor (CVD) u otras técnicas similares, lo que garantiza una capa uniforme y continua que encapsula eficazmente las partículas de silicio.
Cada uno de estos pasos es interdependiente, y su integración satisfactoria es crucial para la producción de materiales de ánodo de silicio-carbono de alta calidad que satisfagan las estrictas exigencias de las aplicaciones modernas de almacenamiento de energía.
Síntesis de materiales de carbono poroso
Importancia del carbono poroso
Los materiales de carbono poroso desempeñan un papel fundamental en la optimización de los ánodos de silicio-carbono, ya que mejoran significativamente su rendimiento general. Esta mejora se atribuye principalmente a varias propiedades clave inherentes al carbono poroso.
En primer lugar, la elevada superficie específica del carbono poroso proporciona una amplia plataforma para la deposición de partículas de silicio. Esta gran superficie garantiza que las partículas de silicio se distribuyan uniformemente, lo que es crucial para mantener la integridad estructural y el rendimiento del ánodo.
En segundo lugar, la excelente conductividad eléctrica del carbono poroso facilita una transferencia eficiente de electrones dentro del material del ánodo. Esta propiedad es vital para mantener una alta eficiencia energética y reducir la resistencia interna, que son esenciales para el rendimiento y la durabilidad a largo plazo del ánodo.
Por último, la buena estabilidad mecánica del carbono poroso contribuye a la resistencia estructural del ánodo. Esta estabilidad es especialmente importante durante los repetidos ciclos de carga y descarga, ya que ayuda a mitigar los cambios de volumen que sufren las partículas de silicio, evitando así su degradación y prolongando la vida útil del ánodo.
En resumen, la combinación de una elevada superficie específica, una excelente conductividad eléctrica y una buena estabilidad mecánica hace que los materiales de carbono poroso sean indispensables para el avance de los ánodos de silicio-carbono en la tecnología de las baterías.
Consideraciones sobre la síntesis
A la hora de sintetizar materiales de carbono poroso para ánodos de silicio-carbono, hay que tener en cuenta meticulosamente varios factores críticos para garantizar un rendimiento y una escalabilidad óptimos. El diseño de la estructura de los poros es primordial, ya que influye directamente en la capacidad del material para adaptarse a los cambios de volumen durante los ciclos de litiación y deslitiación. Una estructura de poros bien diseñada puede mejorar significativamente la estabilidad del ánodo durante los ciclos y la retención de la capacidad.
La selección del precursor es otro aspecto fundamental. La elección del material precursor afecta no sólo a las propiedades finales del carbono poroso, sino también a la facilidad de síntesis y al coste del material. Normalmente se prefieren los precursores con alto rendimiento de carbono y bajo contenido en cenizas, ya que facilitan la formación de una matriz de carbono uniforme y conductora. Además, el precursor debe ser compatible con técnicas de producción escalables para garantizar la viabilidad de la fabricación a gran escala.
La escalabilidad para la producción a gran escala es una consideración innegociable. El proceso de síntesis debe ser adaptable a reactores de escala industrial, garantizando una calidad y un rendimiento constantes. Esto implica optimizar las condiciones de reacción, como la temperatura, la presión y las concentraciones de reactivos, para lograr una deposición uniforme de partículas de silicio dentro del carbono poroso. Además, el proceso debe minimizar el consumo de energía y la generación de residuos, en consonancia con las prácticas de fabricación sostenibles.
En resumen, la síntesis de materiales de carbono poroso para ánodos de silicio-carbono requiere un enfoque holístico, que equilibre el diseño de la estructura de poros, la selección de precursores y la escalabilidad para satisfacer las demandas tanto de rendimiento como de aplicación industrial.
Silano y proceso de deposición
Papel del gas silano
El gas silano (SiH₄) desempeña un papel fundamental en la deposición de partículas de silicio dentro de la estructura porosa de carbono, un paso crítico en la fabricación de materiales de ánodo de silicio-carbono. La eficacia de este proceso depende de la gestión cuidadosa de las propiedades del silano y del intrincado equilibrio de los parámetros de deposición.
Uno de los principales retos que plantea el uso del silano es su sensibilidad a las condiciones ambientales. Por ejemplo, la introducción de oxígeno en la cámara de deposición puede provocar la formación de SiOH, lo que perjudica la calidad de la película de silicio. Por el contrario, en ausencia de oxígeno, se pueden conseguir películas de silicio amorfo, que son puras y adecuadas para la deposición. Esto pone de manifiesto la necesidad de controlar con precisión el entorno de deposición para evitar reacciones químicas no deseadas.
Además, el coste y la disponibilidad del silano son factores importantes que influyen en la viabilidad de la producción a gran escala. El material debe manipularse con cuidado debido a su naturaleza reactiva, lo que requiere equipos especializados y protocolos de seguridad para mitigar los riesgos. Además, el proceso de deposición requiere un delicado equilibrio de silano y otros gases, como oxígeno y xenón, para lograr el compuesto de silicio-carbono deseado.
Para optimizar el proceso de deposición, es esencial mantener tasas medias de introducción de silano. Un exceso de silano puede provocar la formación de SIH, mientras que un exceso de oxígeno puede dar lugar a SiOH, y ambos degradan la calidad del producto final. Conseguir el equilibrio adecuado es crucial para obtener películas de silicio que sean amorfas y duras a la vez, lo que mejora las características de rendimiento del ánodo.
En resumen, el papel del gas silano en el proceso de deposición es polifacético y requiere un conocimiento profundo de sus propiedades químicas y una gestión cuidadosa de los parámetros de deposición para garantizar la producción de materiales de ánodo de silicio-carbono de alta calidad.
Parámetros del proceso de deposición
Los parámetros del proceso de deposición desempeñan un papel fundamental en la determinación de la calidad y el rendimiento de los materiales de ánodo de silicio-carbono (Si-C). Los parámetros clave incluyen la temperatura de deposición, las condiciones de reacción y las estrictas medidas de seguridad, cada uno de los cuales influye significativamente en las características del producto final.
Influencia de la temperatura
La temperatura de deposición es un factor crítico que afecta directamente a la uniformidad y densidad de las partículas de silicio dentro de la matriz de carbono poroso. Las temperaturas más altas pueden mejorar la difusión del gas silano en los poros de carbono, lo que conduce a una deposición más uniforme. Sin embargo, las temperaturas excesivamente altas también pueden provocar la degradación térmica de la estructura de carbono, reduciendo su estabilidad mecánica y su superficie específica. Por lo tanto, la optimización de la temperatura de deposición es esencial para equilibrar estos efectos contrapuestos.
Condiciones de reacción
Las condiciones de reacción, como el caudal de gas y la presión, son igualmente importantes. Estas condiciones determinan el tiempo de permanencia de los reactivos en la cámara de deposición y la velocidad de formación de partículas de silicio. Por ejemplo, un mayor caudal de gas puede acortar el tiempo de permanencia, reduciendo potencialmente la uniformidad del depósito de silicio. Por el contrario, un caudal menor puede mejorar el proceso de deposición, pero también puede aumentar el riesgo de obstrucción u otros problemas operativos. Por tanto, es necesario un control preciso de estas condiciones para conseguir unas propiedades óptimas del material de silicio-carbono.
Medidas de seguridad
Dada la peligrosidad del gas silano, es indispensable adoptar estrictas medidas de seguridad durante el proceso de deposición. Estas medidas incluyen el uso de sistemas avanzados de detección de gases, protocolos de parada de emergencia y sólidos sistemas de ventilación para mitigar el riesgo de fugas o explosiones. Garantizar un entorno de trabajo seguro no sólo protege al personal, sino que también garantiza la fiabilidad y consistencia del proceso de deposición, algo crucial para la producción a escala industrial.
En resumen, los parámetros del proceso de deposición -temperatura, condiciones de reacción y medidas de seguridad- están estrechamente relacionados con el rendimiento y la calidad de los materiales de ánodos de silicio-carbono. Optimizar estos parámetros es esencial para mejorar las propiedades electroquímicas del material y garantizar su viabilidad para aplicaciones a gran escala.
Equipos de deposición
Tipos de equipos de deposición
Los hornos rotatorios y los lechos fluidizados son los principales tipos de equipos utilizados en el proceso de deposición de materiales de ánodo de silicio-carbono. Cada tipo de equipo ofrece ventajas y retos distintos, que son consideraciones cruciales para conseguir unas propiedades y una escalabilidad óptimas del material.
Hornos rotatorios
- Simplicidad operativa: El funcionamiento de los hornos rotatorios es relativamente sencillo, lo que los convierte en la opción preferida para los experimentos iniciales y la producción a pequeña escala.
- Rentabilidad: Suelen ser más rentables tanto en términos de inversión de capital como de costes operativos, lo que puede resultar beneficioso para proyectos a escala piloto.
- Flexibilidad: Los hornos rotatorios ofrecen flexibilidad en el manejo de diversos materiales precursores y pueden adaptarse a diferentes condiciones de deposición.
Lechos fluidizados
- Uniformidad y eficiencia: Los lechos fluidizados son famosos por su superior uniformidad en la distribución de partículas y sus mayores índices de utilización del gas silano. Esto se traduce en unas propiedades del material más uniformes y un mejor rendimiento general.
- Medidas de seguridad mejoradas: El uso de lechos fluidizados requiere protocolos de seguridad estrictos debido a la alta reactividad del gas silano. Los sistemas de seguridad avanzados y la supervisión continua son esenciales para mitigar los riesgos asociados a las fugas de gas y otros peligros.
- Complejidad y fiabilidad: A pesar de sus ventajas, los lechos fluidizados son más complejos y requieren una gran fiabilidad para garantizar un funcionamiento continuo y estable. Esta complejidad puede plantear problemas a la hora de ampliar la producción a escala industrial.
En resumen, mientras que los hornos rotatorios proporcionan una solución más sencilla y rentable, los lechos fluidizados ofrecen una mayor uniformidad y eficiencia, aunque con una mayor complejidad y requisitos de seguridad. La elección del equipo depende de las necesidades específicas y de la escala del proceso de producción.
Retos de la industrialización
La producción a gran escala de materiales de ánodo de silicio-carbono mediante lechos fluidizados presenta varios retos importantes. Estos retos giran principalmente en torno a garantizar un funcionamiento continuo, mantener la uniformidad en el proceso de deposición y lograr un alto aprovechamiento del gas silano.
Uno de los principales obstáculos es la necesidad deoptimización del equipo y del proceso. Los lechos fluidizados, aunque ofrecen una uniformidad y una utilización del silano superiores, requieren un control meticuloso de diversos parámetros como la temperatura, los caudales de gas y la distribución del tamaño de las partículas. Cualquier desviación de estas condiciones óptimas puede dar lugar a propiedades inconsistentes del material, que son perjudiciales para el rendimiento global del ánodo.
Además, lafiabilidad y seguridad del sistema de lecho fluidizado son críticas. El uso de gas silano, que es altamente reactivo y potencialmente explosivo, requiere medidas de seguridad sólidas y una supervisión continua. Esto añade una capa de complejidad al proceso de industrialización, exigiendo sistemas avanzados de automatización y control para garantizar un funcionamiento seguro y eficiente.
Además, laescalabilidad del proceso de lecho fluidizado es un problema importante. Pasar de los experimentos a escala de laboratorio a la producción industrial a gran escala exige estudiar detenidamente cómo mantener el mismo nivel de control y uniformidad en volúmenes mayores. Esto suele implicar importantes inversiones de capital en mejoras de los equipos y del proceso.
En resumen, aunque los lechos fluidizados ofrecen ventajas prometedoras para la producción de ánodos de silicio-carbono, su industrialización exige superar importantes retos técnicos y operativos. Entre ellos figuran la optimización de los equipos y los procesos, la garantía de fiabilidad y seguridad y la resolución de problemas de escalabilidad para lograr una producción continua a gran escala.
CONTÁCTANOS PARA UNA CONSULTA GRATUITA
Los productos y servicios de KINTEK LAB SOLUTION han sido reconocidos por clientes de todo el mundo. Nuestro personal estará encantado de ayudarle con cualquier consulta que pueda tener. ¡Contáctenos para una consulta gratuita y hable con un especialista del producto para encontrar la solución más adecuada para sus necesidades de aplicación!