El austenitizado es un proceso de tratamiento térmico que ofrece varias ventajas, como la mejora de la ductilidad, la tenacidad y la reducción de la distorsión en comparación con el temple y revenido tradicionales.Sin embargo, también tiene desventajas notables, como limitaciones en la idoneidad del material, costes más elevados y complejidad del proceso.El proceso no es aplicable universalmente a todos los aceros, sobre todo a los que tienen un alto contenido de carbono, y requiere un control preciso de la temperatura y el tiempo, lo que puede aumentar los costes operativos.Además, la necesidad de equipos especializados y los tiempos de procesamiento más largos pueden hacer que el austempering sea menos eficiente para la producción de grandes volúmenes.Estos factores deben tenerse muy en cuenta a la hora de decidir si utilizar el austempering para una aplicación específica.
Explicación de los puntos clave:
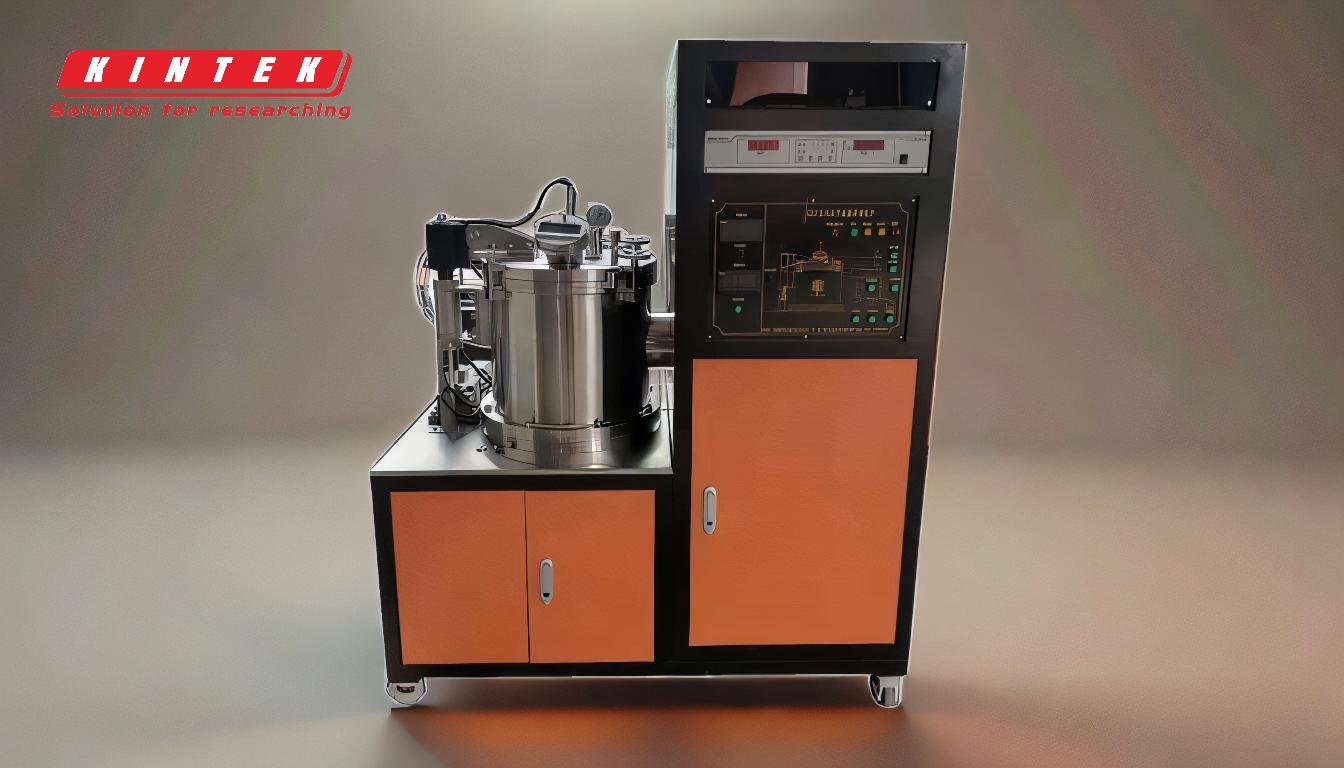
-
Limitaciones materiales:
- No apto para todos los aceros:El austenitizado es más eficaz para los aceros de carbono medio y algunos aceros aleados.Los aceros con alto contenido en carbono, como los aceros para herramientas, son menos adecuados porque pueden no alcanzar la microestructura deseada (bainita) debido a su alta templabilidad y al riesgo de formación de martensita.
- Restringidos a aplicaciones específicas:El proceso no es de aplicación universal y suele limitarse a piezas que requieren gran dureza y resistencia al desgaste, como engranajes, muelles y equipos agrícolas.
-
Costes más elevados:
- Equipos especializados:El tratamiento térmico requiere un control preciso de la temperatura y baños de enfriamiento especializados (por ejemplo, baños de sal o de metal fundido), cuya instalación y mantenimiento pueden resultar costosos.
- Tiempos de procesamiento más largos:El proceso implica mantener el material a una temperatura intermedia durante un período prolongado para formar bainita, lo que aumenta el consumo de energía y los costes de mano de obra en comparación con el temple y revenido tradicionales.
-
Complejidad del proceso:
- Control preciso de temperatura y tiempo:La obtención de la microestructura bainítica deseada requiere un control estricto de la temperatura del medio de temple y de la duración del mantenimiento isotérmico.Cualquier desviación puede dar lugar a microestructuras no deseadas, como martensita o perlita.
- Compatibilidad con espesores limitados:Las secciones más gruesas pueden no enfriarse uniformemente, lo que da lugar a una microestructura y unas propiedades incoherentes.Esto limita el austemperizado a piezas con secciones transversales relativamente uniformes.
-
Menor eficacia en la producción de grandes volúmenes:
- Tiempos de ciclo más lentos:Los prolongados tiempos de mantenimiento necesarios para la formación de bainita hacen que el austemplado sea menos adecuado para la producción de grandes volúmenes en la que es esencial un procesamiento rápido.
- Limitaciones del procesamiento por lotes:El proceso suele realizarse por lotes, lo que puede limitar el rendimiento en comparación con los métodos de tratamiento térmico continuo.
-
Posibilidad de resultados incoherentes:
- Sensibilidad a la tasa de enfriamiento:La velocidad de enfriamiento debe controlarse cuidadosamente para evitar la formación de martensita, que puede comprometer las propiedades mecánicas deseadas.
- Dependencia del medio de enfriamiento:La eficacia del templado austenítico depende de la capacidad del medio de temple para mantener una temperatura constante, lo que puede resultar difícil en operaciones a gran escala.
-
Preocupaciones medioambientales y de seguridad:
- Uso de baños de sal:Los baños de sal, comúnmente utilizados en el austempering, pueden plantear riesgos medioambientales y de seguridad debido a la posibilidad de derrames de sal, humos y la necesidad de una eliminación adecuada.
- Manipulación de metales fundidos:Si se utilizan baños de metal fundido, se requieren precauciones de seguridad adicionales para proteger a los trabajadores de quemaduras y de la exposición a materiales peligrosos.
En conclusión, aunque el austempering ofrece importantes ventajas en cuanto a propiedades mecánicas y reducción de la distorsión, hay que sopesar cuidadosamente sus desventajas, como las limitaciones de material, los costes más elevados, la complejidad del proceso y la menor eficacia para la producción de grandes volúmenes.Estos factores lo hacen menos adecuado para determinadas aplicaciones y requieren una cuidadosa consideración de los requisitos específicos de la pieza que se va a tratar.
Cuadro sinóptico:
Desventaja | Detalles |
---|---|
Limitaciones materiales | No apto para aceros de alto contenido en carbono; limitado a aplicaciones específicas. |
Costes más elevados | Requiere equipos especializados y tiempos de procesamiento más largos. |
Complejidad del proceso | Necesidad de un control preciso de la temperatura y el tiempo; compatibilidad limitada con espesores. |
Eficiencia reducida | Tiempos de ciclo más lentos; el procesamiento por lotes limita el rendimiento. |
Resultados inconsistentes | Sensibilidad a la velocidad de enfriamiento; dependencia del medio de enfriamiento. |
Riesgos medioambientales y de seguridad | El uso de baños salinos y metales fundidos plantea riesgos. |
¿Está considerando el austemperizado para su aplicación? Póngase en contacto con nuestros expertos para hablar de sus necesidades.