El proceso pulvimetalúrgico es un método de fabricación utilizado para producir piezas y componentes metálicos a partir de materiales en polvo.Consta de cuatro pasos fundamentales: preparación del polvo, mezcla y combinación, compactación y sinterización.Cada paso desempeña un papel fundamental en la conformación del producto final, garantizando que cumpla las especificaciones deseadas en cuanto a resistencia, densidad y precisión dimensional.Este proceso se utiliza mucho en industrias como la automovilística, la aeroespacial y la electrónica por su capacidad de producir formas complejas con un desperdicio mínimo de material.A continuación, analizaremos cada paso en detalle para comprender su importancia y cómo contribuye al proceso global.
Explicación de los puntos clave:
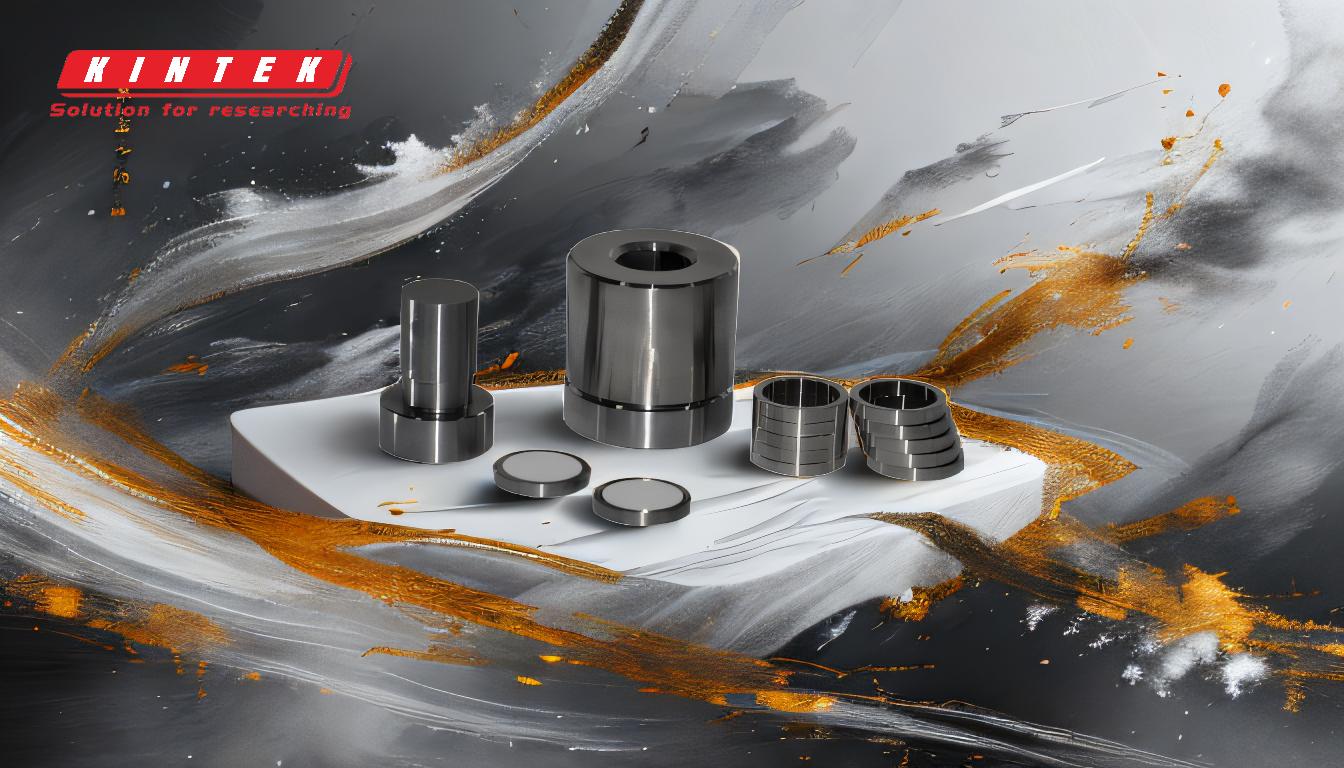
-
Preparación del polvo
- La preparación del polvo es la primera etapa del proceso pulvimetalúrgico.Implica la producción de polvos metálicos, lo que puede lograrse mediante diversos métodos, como la atomización, la reducción química o los procesos mecánicos.
- La calidad del polvo es crucial, ya que afecta directamente a las propiedades del producto final.Los polvos deben tener un tamaño de partícula, una forma y una composición uniformes para garantizar la uniformidad durante los pasos posteriores.
- Los metales más utilizados en pulvimetalurgia son el hierro, el cobre, el aluminio y el titanio, así como aleaciones como el acero inoxidable y el bronce.
-
Mezcla y combinación
- Tras la preparación del polvo, el siguiente paso es la mezcla.Esto implica combinar diferentes polvos metálicos o añadir lubricantes y aglutinantes para mejorar la fluidez y compresibilidad de la mezcla de polvo.
- Los lubricantes se añaden para reducir la fricción durante la compactación, mientras que los aglutinantes ayudan a mantener unidas las partículas de polvo tras la compactación.
- El objetivo de este paso es lograr una mezcla homogénea, garantizando que el producto final tenga propiedades uniformes y un rendimiento constante.
-
Compactación
- La compactación es el proceso de aplicar una presión intensa a la mezcla de polvo para formar un "compacto verde", que es una pieza con forma pero sin sinterizar.Este paso se realiza normalmente utilizando una prensa hidráulica o mecánica y una matriz.
- La presión aplicada durante la compactación oscila entre 100 y 1.000 MPa, según el material y la densidad deseada del producto final.
- El compacto verde conserva la forma de la matriz, pero es relativamente frágil y requiere una manipulación cuidadosa.
-
Sinterización
- La sinterización es la etapa final y más crítica del proceso pulvimetalúrgico.Consiste en calentar el compacto verde en una atmósfera controlada (por ejemplo, vacío, hidrógeno o gas inerte) a una temperatura inferior al punto de fusión del metal.
- La temperatura de sinterización suele oscilar entre el 70% y el 90% del punto de fusión del metal.Por ejemplo, el hierro se sinteriza a unos 1.100°C a 1.300°C.
- Durante la sinterización, las partículas de polvo se unen por difusión, lo que da lugar a un producto final más denso y resistente.Este paso también ayuda a eliminar cualquier resto de lubricante o aglutinante.
Siguiendo estos cuatro pasos, el proceso pulvimetalúrgico puede producir piezas metálicas de alta calidad con dimensiones precisas, excelentes propiedades mecánicas y un desperdicio mínimo de material.Este método es especialmente ventajoso para fabricar formas y componentes complejos que serían difíciles o costosos de producir con métodos tradicionales.
Cuadro sinóptico:
Paso | Descripción | Detalles clave |
---|---|---|
Preparación del polvo | Producción de polvos metálicos mediante métodos como la atomización, la reducción química o los procesos mecánicos. |
- Tamaño, forma y composición uniformes de las partículas.
- Metales: hierro, cobre, aluminio, titanio, acero inoxidable, bronce. |
Mezcla y combinación | Combinación de polvos con lubricantes y aglutinantes para mejorar la fluidez y la compresibilidad. |
- La mezcla homogénea garantiza propiedades uniformes.
- Los lubricantes reducen la fricción; los aglutinantes mantienen unidas las partículas. |
Compactación | Aplicación de presión (100-1.000 MPa) para formar un "compacto verde" mediante una prensa hidráulica o mecánica. |
- El compacto verde tiene forma pero es frágil.
- Conserva la forma del troquel, requiere una manipulación cuidadosa. |
Sinterización | Calentamiento del compacto verde en una atmósfera controlada por debajo del punto de fusión del metal. |
- Temperatura: 70-90% del punto de fusión.
- Une las partículas, aumenta la densidad y elimina los aglutinantes. |
¿Está listo para optimizar la producción de sus piezas metálicas? Póngase en contacto con nosotros para obtener más información sobre soluciones pulvimetalúrgicas.