El procesamiento SPS (Spark Plasma Sintering) es una técnica avanzada de fabricación de materiales que combina los principios del prensado en caliente y la corriente eléctrica pulsada para lograr una sinterización rápida y eficaz de los materiales. Este proceso se caracteriza por su capacidad para producir materiales con microestructuras y propiedades únicas mediante un control preciso de la temperatura, la presión y la velocidad de calentamiento. El SPS funciona en vacío o en una atmósfera controlada para evitar la oxidación y garantizar la pureza del material. El proceso consta de cuatro etapas principales: eliminación del gas y creación del vacío, aplicación de presión, calentamiento resistivo y enfriamiento. El efecto de chispa de plasma, generado por corrientes pulsadas, inhibe el crecimiento de partículas y permite crear materiales con composiciones y propiedades a medida. El SPS se utiliza ampliamente en la investigación y en aplicaciones industriales, en particular para sintetizar materiales avanzados como las cerámicas de temperatura ultra alta.
Explicación de los puntos clave:
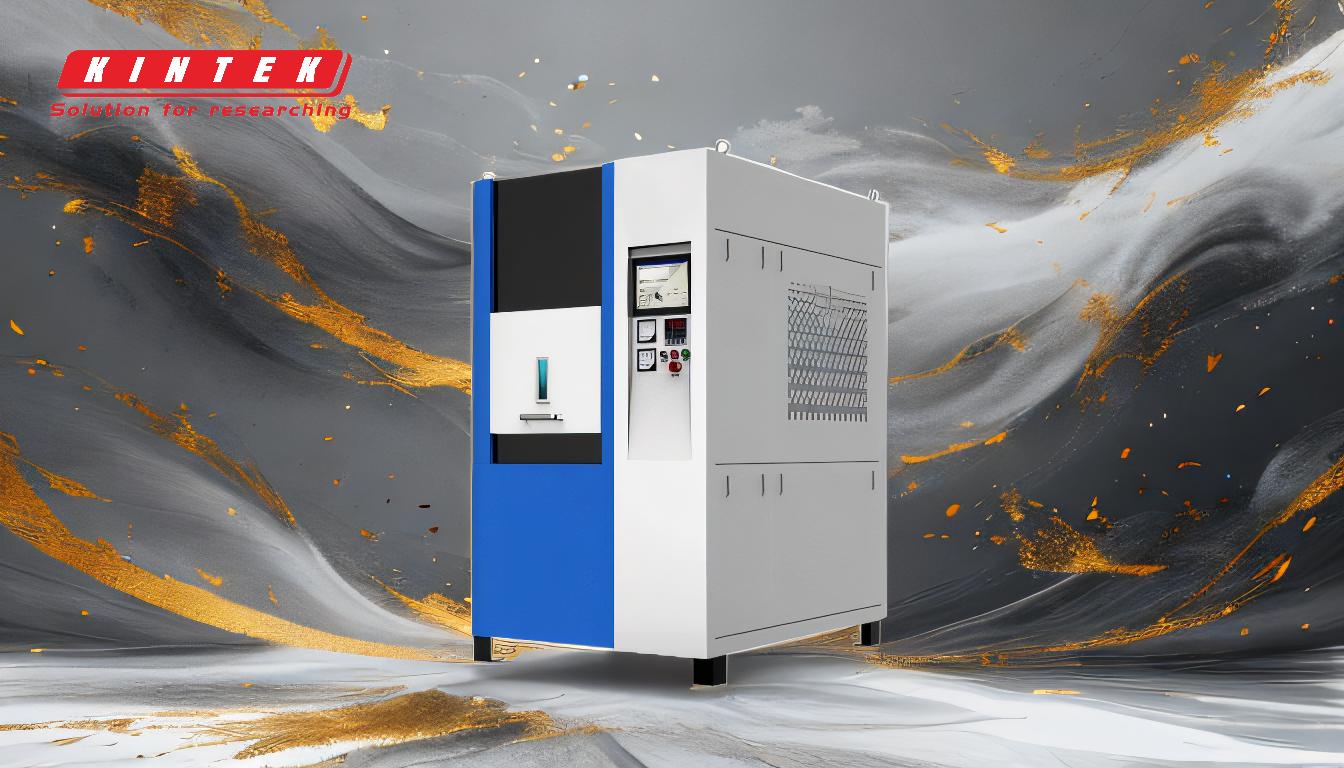
-
Definición y finalidad del procesamiento SPS:
- SPS, o Spark Plasma Sintering, es una técnica de fabricación de materiales que combina el prensado en caliente con corrientes eléctricas pulsadas para sinterizar materiales de forma eficiente.
- Está diseñada para producir materiales con microestructuras y propiedades únicas, como cerámicas de alta densidad, nanomateriales y materiales compuestos, que son difíciles de conseguir con los métodos convencionales.
-
Mecanismo central: Efecto de plasma de chispa:
- El proceso se basa en el "efecto plasma de chispa", en el que las corrientes eléctricas pulsadas generan altas temperaturas localizadas en las superficies de las partículas.
- Este efecto provoca la evaporación, la fusión y la formación de cuellos entre las partículas, lo que conduce a una rápida densificación y sinterización.
- El efecto del plasma de chispa también inhibe el crecimiento de las partículas, permitiendo la creación de materiales de grano fino con propiedades mecánicas y térmicas mejoradas.
-
Etapas clave del proceso SPS:
-
Etapa 1: Eliminación del gas y creación del vacío:
- La cámara se evacua para eliminar los gases y crear un vacío, evitando la oxidación y garantizando la pureza del material.
-
Etapa 2: Aplicación de presión:
- Se aplica presión uniaxial al polvo compacto para facilitar la reorganización y densificación de las partículas.
-
Etapa 3: Calentamiento resistivo:
- Corrientes eléctricas pulsadas fluyen a través de la matriz de grafito y la muestra, generando calor mediante calentamiento resistivo.
-
Etapa 4: Enfriamiento:
- Tras la sinterización, la muestra se enfría en condiciones controladas para preservar la microestructura y las propiedades deseadas.
-
Etapa 1: Eliminación del gas y creación del vacío:
-
Ventajas del procesamiento SPS:
-
Altas velocidades de calentamiento y tiempos de procesado cortos:
- El SPS alcanza velocidades de calentamiento de hasta cientos de grados por minuto, lo que reduce significativamente los tiempos de procesamiento en comparación con los métodos de sinterización convencionales.
-
Bajas temperaturas de sinterización:
- El proceso funciona a temperaturas más bajas que el sinterizado tradicional, lo que minimiza el crecimiento del grano y preserva las microestructuras finas.
-
Control preciso:
- La temperatura, la presión y la velocidad de calentamiento pueden controlarse con precisión, lo que permite fabricar materiales con propiedades a medida.
-
Versatilidad:
- La tecnología SPS es adecuada para una amplia gama de materiales, como cerámicas, metales, materiales compuestos y nanomateriales.
-
Altas velocidades de calentamiento y tiempos de procesado cortos:
-
Aplicaciones de la tecnología SPS:
-
Síntesis de materiales avanzados:
- La tecnología SPS se utiliza para producir cerámicas de temperatura ultra alta (por ejemplo, ZrC), nanomateriales y materiales con gradientes funcionales.
-
Investigación y desarrollo:
- La técnica se utiliza ampliamente en la investigación de la ciencia de los materiales para explorar nuevas composiciones y propiedades.
-
Fabricación industrial:
- El SPS se emplea en industrias que requieren materiales de alto rendimiento, como la aeroespacial, la automovilística y la electrónica.
-
Síntesis de materiales avanzados:
-
Control de equipos y procesos:
-
Matrices de grafito:
- El grafito se utiliza habitualmente para las matrices de prensado debido a su alta conductividad térmica y eléctrica.
-
Interfaz de pantalla táctil:
- El proceso se controla y programa mediante una pantalla táctil, lo que permite un ajuste preciso de los parámetros y una supervisión en tiempo real.
-
Vacío o atmósfera controlada:
- El proceso se lleva a cabo en un entorno de vacío o gas inerte para evitar la contaminación y garantizar la pureza del material.
-
Matrices de grafito:
-
Comparación con los métodos convencionales:
- El SPS ofrece ventajas significativas sobre los métodos de sinterización convencionales, como tiempos de procesamiento más rápidos, menor consumo de energía y la capacidad de producir materiales con propiedades únicas.
- Los métodos convencionales suelen requerir temperaturas más altas y tiempos de procesamiento más largos, lo que provoca el crecimiento de granos y reduce el rendimiento del material.
En resumen, el procesamiento SPS es una tecnología de vanguardia que permite la fabricación rápida y precisa de materiales avanzados. Su combinación única de corrientes eléctricas pulsadas, presión controlada y altas velocidades de calentamiento la convierten en una potente herramienta para los científicos e ingenieros de materiales. Ya sea para aplicaciones industriales o de investigación, el SPS ofrece un control y una versatilidad sin precedentes, lo que lo convierte en una tecnología clave para el desarrollo de materiales de última generación.
Tabla resumen:
Aspecto | Detalles |
---|---|
Definición | Combina el prensado en caliente y las corrientes eléctricas pulsadas para una sinterización eficaz. |
Mecanismo central | El efecto de plasma de chispa permite una rápida densificación y materiales de grano fino. |
Etapas clave | Extracción de gas, aplicación de presión, calentamiento resistivo y enfriamiento controlado. |
Ventajas | Altas velocidades de calentamiento, bajas temperaturas de sinterización, control preciso, versatilidad. |
Aplicaciones | Síntesis de cerámicas, nanomateriales y materiales industriales de alto rendimiento. |
Equipamiento | Matrices de grafito, interfaz de pantalla táctil, vacío/atmósfera controlada. |
Comparación | Mayor rapidez, menor consumo de energía y mejores propiedades de los materiales que con los métodos convencionales. |
Libere el potencial de los materiales avanzados con la tecnología SPS. póngase en contacto con nuestros expertos para obtener más información.