Un horno de inducción es un sistema de calentamiento especializado que se utiliza principalmente para fundir metales y crear aleaciones precisas.Su funcionamiento se basa en los principios de la inducción electromagnética y el efecto Joule, según los cuales una corriente alterna que circula por una bobina genera un campo magnético.Este campo induce corrientes parásitas en la carga metálica conductora, produciendo calor por resistencia.El horno alcanza altas temperaturas sin contacto directo entre el elemento calefactor y el metal, lo que garantiza una fusión eficaz y limpia.El proceso consiste en convertir la energía eléctrica en energía térmica, por lo que es ideal para aplicaciones que requieren un control preciso de la temperatura y un calentamiento rápido.
Explicación de los puntos clave:
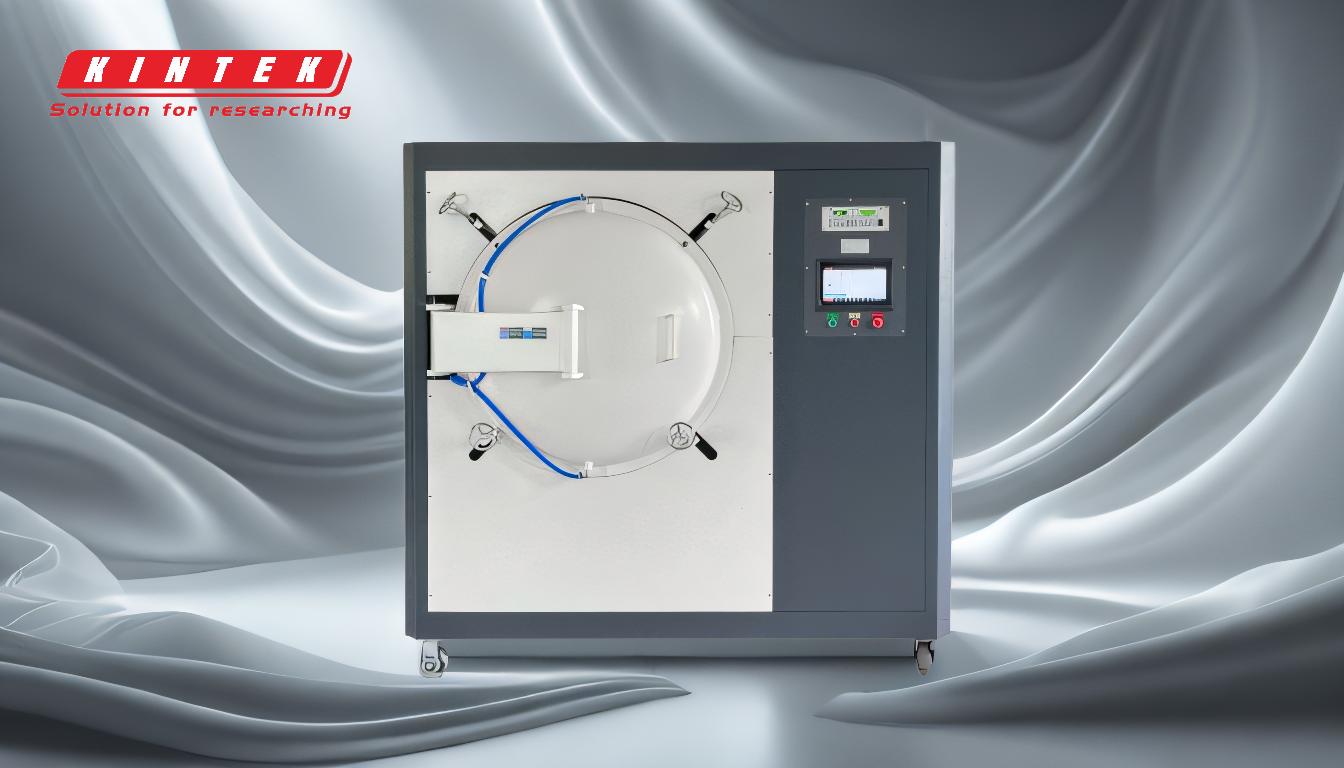
-
Principio del calentamiento por inducción:
- El calentamiento por inducción es un método sin contacto que se basa en la inducción electromagnética y el efecto Joule.
- Una corriente alterna en una bobina crea un campo magnético que induce corrientes de Foucault en el metal conductor.
- La resistencia del metal a estas corrientes parásitas genera calor, fundiendo el metal.
-
Componentes de un horno de inducción:
- Bobina de inducción:Bobina de cobre hueca que rodea la carga metálica y transporta corriente alterna para generar el campo magnético.
- Fuente de alimentación:Convierte la frecuencia de alimentación estándar (50 Hz) en frecuencia media (300 Hz a 1.000 Hz) para un calentamiento eficaz.
- Sistema de condensadores e inductores:Trabaja con la bobina para crear líneas magnéticas de alta densidad, mejorando el proceso de inducción.
-
Mecanismo de trabajo:
- La fuente de alimentación convierte la corriente alterna trifásica en corriente continua y, a continuación, en corriente alterna regulable de frecuencia media.
- Esta corriente circula por el condensador y la bobina de inducción, generando un campo magnético.
- El campo magnético induce corrientes de Foucault en el metal, produciendo calor y fundiéndolo.
-
Ventajas de los hornos de inducción:
- Eficiencia:El calor se genera directamente dentro del metal, minimizando la pérdida de energía.
- Precisión:Permite un control exacto de la temperatura y la composición de la aleación.
- Limpieza:La ausencia de contacto directo entre el elemento calefactor y el metal reduce la contaminación.
- Velocidad:Capacidad de calentamiento y fusión rápidos.
-
Aplicaciones:
- Ideal para fundir metales como acero, hierro, aluminio y cobre.
- Se utiliza en fundiciones para la producción de fundición y aleaciones.
- Adecuado para aplicaciones que requieren una gran pureza y un control preciso de la temperatura.
-
Refrigeración y seguridad:
- Las bobinas primarias están refrigeradas por agua para evitar el sobrecalentamiento.
- Las superficies del horno pueden calentarse, pero el calor se genera principalmente dentro de la carga metálica.
Aprovechando estos principios y componentes, los hornos de inducción ofrecen una solución fiable y eficaz para la fusión industrial de metales y la producción de aleaciones.
Cuadro sinóptico:
Aspecto clave | Detalles |
---|---|
Principio | La inducción electromagnética y el efecto Joule generan calor en los metales conductores. |
Componentes | Bobina de inducción, fuente de alimentación, condensador y sistema inductor. |
Mecanismo de funcionamiento | Convierte la CA en CC y, a continuación, en CA de frecuencia media para inducir corrientes parásitas. |
Ventajas | Alta eficacia, control preciso de la temperatura, limpieza y calentamiento rápido. |
Aplicaciones | Fundición de acero, hierro, aluminio y cobre; fundición y producción de aleaciones. |
Refrigeración y seguridad | Las bobinas refrigeradas por agua evitan el sobrecalentamiento; el calor se encuentra principalmente dentro del metal. |
Descubra cómo un horno de inducción puede revolucionar su proceso de fusión de metales. contacte con nosotros para recibir asesoramiento experto.