Los hornos de inducción, si bien son muy eficientes para fundir metales, presentan varias desventajas notables. Estos incluyen la incapacidad de refinar materiales, lo que requiere que los materiales de carga estén libres de óxidos y de composición conocida, lo que puede conducir a la pérdida de algunos elementos de aleación debido a la oxidación. Además, la inversión inicial para los hornos de inducción es significativa y abarca equipos especializados y suministros de energía. El funcionamiento de estos hornos también exige personal capacitado y con conocimientos de los principios del calentamiento por inducción y los procedimientos de seguridad. Además, el calentamiento por inducción es más eficaz para el calentamiento de superficies, lo que limita potencialmente su aplicación en determinados procesos de tratamiento térmico.
Puntos clave explicados:
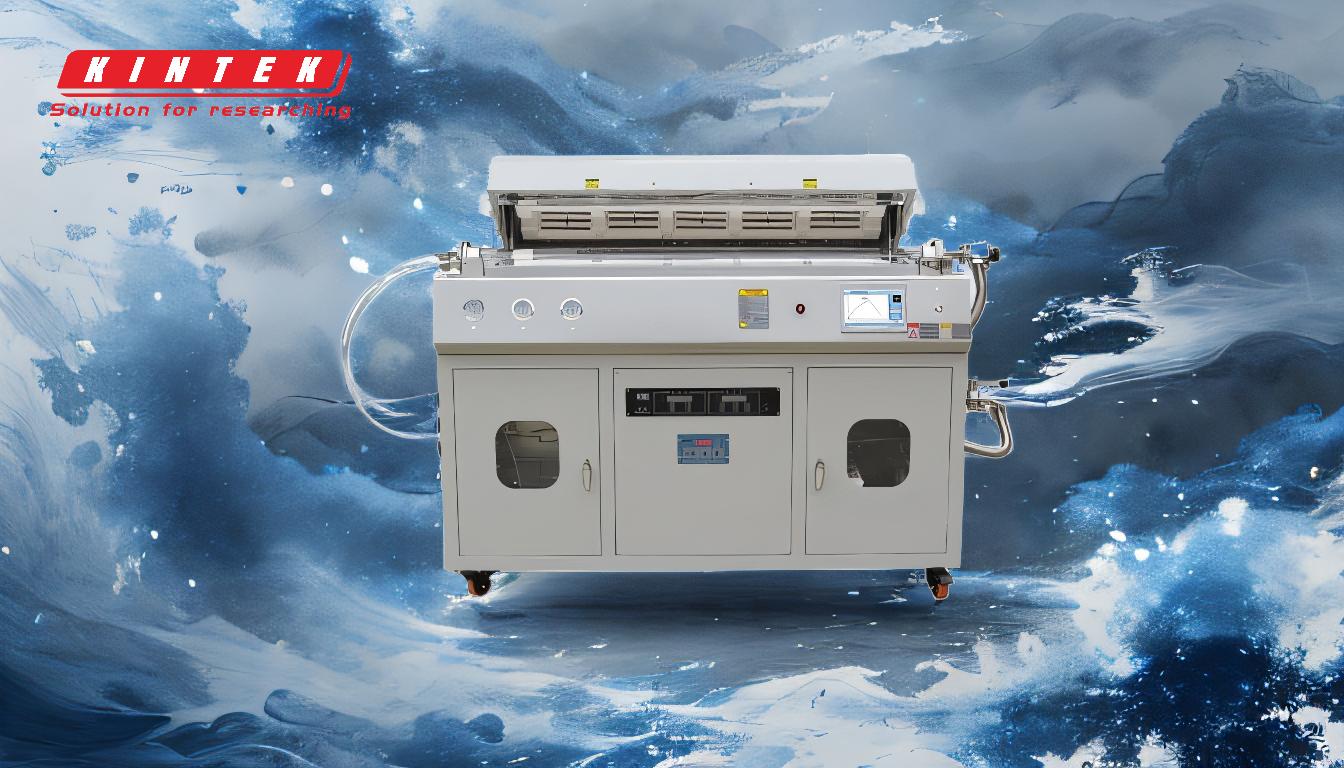
-
Falta de capacidad de refinación
- Los hornos de inducción no pueden refinar materiales, lo que significa que los materiales de carga ya deben estar libres de óxidos y tener una composición conocida. Esta limitación puede resultar problemática cuando se trata de materiales impuros o contaminados, ya que el horno no puede eliminar las impurezas durante el proceso de fusión.
- Algunos elementos de aleación pueden perderse debido a la oxidación, lo que hace necesario volver a agregarlos a la masa fundida. Esto añade complejidad y coste al proceso, especialmente en aplicaciones que requieren composiciones de aleación precisas.
-
Alta inversión inicial
- El costo de establecer una horno de inducción igbt es sustancial. Esto incluye no sólo el horno en sí, sino también los equipos especializados y los suministros de energía necesarios para su funcionamiento. El gasto de capital inicial puede ser una barrera para operaciones más pequeñas o aquellas con presupuestos limitados.
- La necesidad de componentes de alta calidad y tecnología avanzada, como los sistemas IGBT (transistor bipolar de puerta aislada), aumenta aún más los costos. Estos componentes son esenciales para un funcionamiento eficiente y confiable, pero tienen un costo elevado.
-
Requisito de personal calificado
- Operar un horno de inducción requiere un alto nivel de experiencia. El personal debe conocer bien los principios del calentamiento por inducción, los procedimientos de seguridad y los matices operativos específicos del equipo.
- La complejidad de la tecnología significa que capacitar y retener a operadores calificados puede ser un desafío y costoso. Esto es particularmente cierto en regiones donde esa experiencia es escasa.
-
Limitaciones en las aplicaciones de tratamiento térmico
- El calentamiento por inducción es más eficaz para el calentamiento de superficies, lo que puede limitar su aplicación en procesos que requieren un calentamiento uniforme en todo el material. Por ejemplo, es posible que determinados procesos de tratamiento térmico no consigan los resultados deseados si el calor no penetra lo suficientemente profundo.
- Esta limitación puede restringir el uso de hornos de inducción en industrias donde el calentamiento profundo y uniforme es esencial, como en el tratamiento térmico de componentes grandes o gruesos.
-
Consumo y eficiencia energética
- Si bien los hornos de inducción son generalmente eficientes energéticamente, los altos requisitos de energía para fundir metales pueden generar un consumo de energía significativo. Esto puede ser una preocupación en regiones con altos costos de electricidad o donde los recursos energéticos son limitados.
- La eficiencia del horno también puede verse influenciada por la calidad del suministro de energía y el estado del equipo. Cualquier ineficiencia puede generar mayores costos operativos con el tiempo.
-
Desafíos operativos y de mantenimiento
- Los hornos de inducción requieren un mantenimiento regular para garantizar un rendimiento óptimo. Esto incluye revisar y reemplazar componentes como bobinas, crisoles y fuentes de alimentación, que pueden desgastarse con el tiempo.
- El entorno operativo también puede plantear desafíos, como la necesidad de sistemas de refrigeración para gestionar el calor generado durante el funcionamiento. Estos sistemas aumentan la complejidad y el costo de mantener el horno.
En resumen, si bien los hornos de inducción ofrecen muchas ventajas, como un calentamiento rápido y un control preciso de la temperatura, también presentan importantes inconvenientes. Estos incluyen la falta de capacidad de refinación, la alta inversión inicial, la necesidad de personal calificado, las limitaciones en las aplicaciones de tratamiento térmico, las preocupaciones sobre el consumo de energía y los desafíos de mantenimiento. Comprender estas desventajas es crucial para tomar decisiones informadas al considerar el uso de hornos de inducción en diversas aplicaciones industriales.
Tabla resumen:
Desventaja | Detalles |
---|---|
Falta de capacidad de refinación | No se pueden refinar materiales; Requiere materiales de carga previamente purificados. |
Alta inversión inicial | Costos de instalación significativos para equipos y suministros de energía. |
Requisito de personal calificado | Necesita operadores capacitados en protocolos de seguridad y calentamiento por inducción. |
Limitaciones en el tratamiento térmico | Efectivo para calentamiento superficial, pero no para calentamiento profundo o uniforme. |
Consumo de energía | Los altos requisitos de energía pueden generar mayores costos operativos. |
Desafíos de mantenimiento | Se necesita mantenimiento regular para serpentines, crisoles y sistemas de enfriamiento. |
¿Quiere saber más sobre los hornos de inducción y sus alternativas? Póngase en contacto con nuestros expertos hoy !