El consumo eléctrico de un horno de inducción, sobre todo para fundir acero, es un factor crítico para la eficiencia operativa y la gestión de costes.Por término medio, un horno de inducción de acero consume aproximadamente 625 kWh por tonelada de acero fundido.Esta cifra puede variar en función de factores como el diseño del horno, las condiciones de funcionamiento y el tipo de tecnología de inducción utilizada, como un horno de inducción IGBT .Comprender estas variables ayuda a optimizar el uso de la energía y a reducir los costes operativos.
Explicación de los puntos clave:
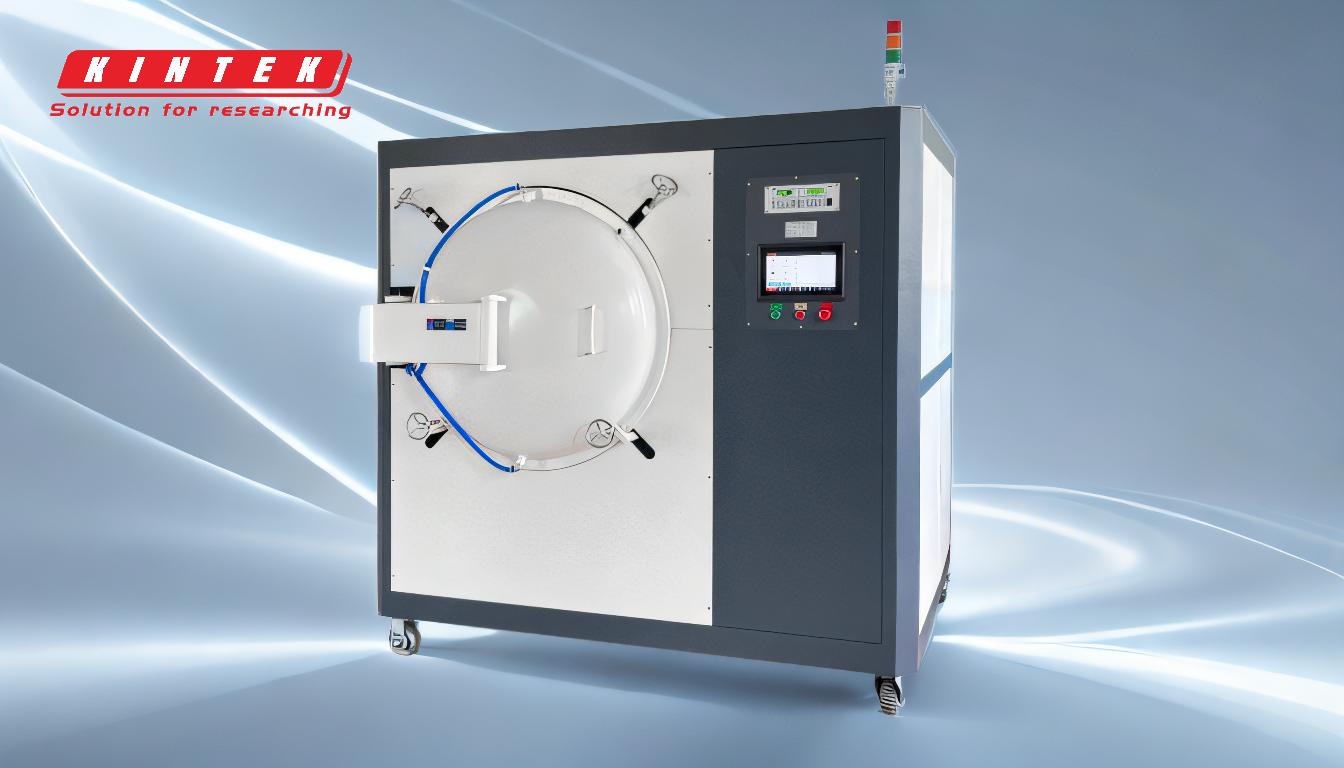
-
Consumo estándar:
- El consumo eléctrico estándar de un horno de inducción de acero es de 625 kWh/tonelada .Se trata de una referencia de eficiencia energética en las operaciones de fundición de acero.
- Esta cifra se basa en hornos bien diseñados y que funcionan correctamente, garantizando un desperdicio mínimo de energía.
-
Factores que influyen en el consumo eléctrico:
- Diseño de hornos:La eficiencia del diseño del horno, incluida la configuración de la batería y el aislamiento, desempeña un papel importante en el consumo de energía.
- Condiciones de funcionamiento:Factores como la velocidad de fusión, la calidad del material de carga y el control de la temperatura influyen en el consumo de energía.Por ejemplo, una mayor velocidad de fusión puede aumentar el consumo de energía.
- Tecnología de inducción:Tecnologías avanzadas como hornos de inducción IGBT ofrecen una mayor eficiencia y un control preciso de la potencia, reduciendo el consumo total de energía en comparación con los antiguos sistemas basados en SCR.
-
Importancia de la eficiencia energética:
- La reducción del consumo eléctrico disminuye directamente los costes operativos y mejora la sostenibilidad del proceso de fusión.
- Los hornos energéticamente eficientes también contribuyen a reducir las emisiones de gases de efecto invernadero, en consonancia con la normativa medioambiental.
-
Estrategias de optimización:
- Mantenimiento regular:Asegurarse de que el horno está bien mantenido minimiza las pérdidas de energía debidas al desgaste.
- Preparación adecuada de la carga:El uso de materiales de carga limpios y del tamaño adecuado reduce el tiempo de fusión y el consumo de energía.
- Sistemas de control avanzados:Implantación de modernos sistemas de control en hornos de inducción IGBT permite una gestión precisa de la energía, mejorando aún más la eficiencia.
-
Comparación con otros tipos de hornos:
- Por lo general, los hornos de inducción consumen menos energía que los hornos de arco tradicionales, sobre todo cuando se trata de operaciones a pequeña escala.
- El uso de hornos de inducción IGBT mejoran aún más esta ventaja gracias a su mayor eficiencia y capacidad de calentamiento más rápido.
Centrándose en estos puntos clave, los operadores pueden comprender y gestionar mejor el consumo eléctrico de los hornos de inducción, garantizando un funcionamiento rentable y sostenible.
Tabla resumen:
Aspecto clave | Detalles |
---|---|
Consumo estándar | 625 kWh/tonelada de acero fundido (referencia de eficiencia energética) |
Factores que afectan al consumo |
- Diseño del horno (serpentín, aislamiento)
- Condiciones de funcionamiento (velocidad de fusión, calidad de la carga) - Tecnología de inducción (por ejemplo, IGBT) |
Estrategias de optimización |
- Mantenimiento regular
- Preparación adecuada de la carga - Sistemas de control avanzados |
Comparación con los hornos de arco | Menor consumo de energía, especialmente con los hornos de inducción IGBT |
Descubra cómo optimizar la eficiencia energética de su horno de inducción. contacte hoy mismo con nuestros expertos ¡!