La deposición física de vapor (PVD) es un proceso fundamental en la fabricación moderna, sobre todo para crear películas finas y revestimientos sobre sustratos. Llevar a cabo el PVD en un entorno de vacío es esencial por varias razones, como la reducción de la contaminación, el aumento de la trayectoria libre media de las partículas y el control preciso del proceso de deposición. El vacío minimiza la presencia de átomos y moléculas indeseables, garantizando un entorno limpio y controlado, necesario para obtener revestimientos de alta calidad. Además, permite una transferencia y adherencia eficientes del material, que son cruciales para aplicaciones en microelectrónica, óptica y otras tecnologías avanzadas.
Explicación de los puntos clave:
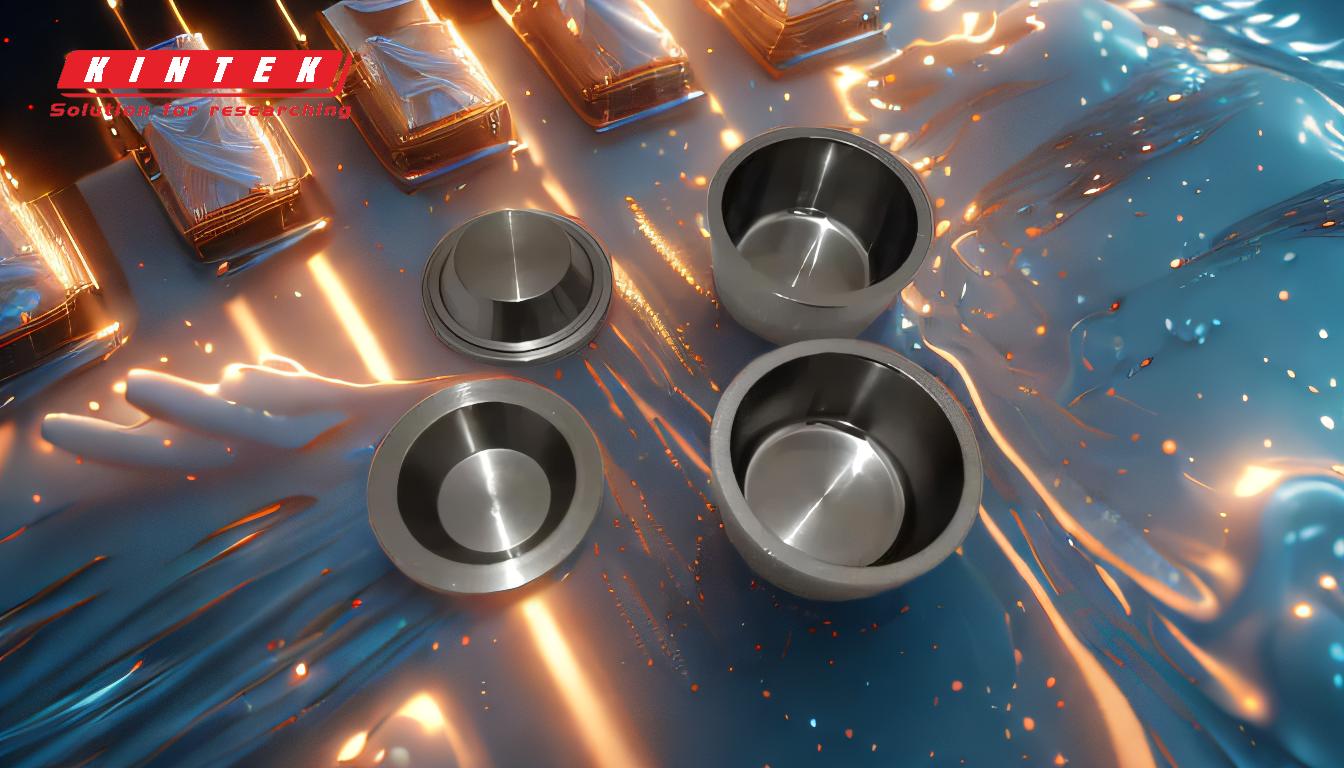
-
Reducción de la densidad de partículas y aumento de la trayectoria libre media:
- En un entorno de vacío, la densidad de las moléculas de gas se reduce considerablemente. Esta reducción aumenta el recorrido libre medio de las partículas, que es la distancia media que recorre una partícula antes de colisionar con otra. Un camino libre medio más largo garantiza que el material vaporizado pueda viajar directamente al sustrato sin dispersarse ni ralentizarse por colisiones con moléculas de gas. Esta trayectoria directa es crucial para conseguir revestimientos uniformes y de alta calidad.
-
Minimización de la contaminación:
- Un entorno de vacío reduce la presencia de átomos y moléculas indeseables, como oxígeno, nitrógeno y vapor de agua, que pueden contaminar la película depositada. Los contaminantes pueden degradar la calidad del revestimiento y provocar defectos, reducir la adherencia y comprometer el rendimiento. Al mantener un alto vacío, el proceso garantiza un entorno más limpio y controlado, lo que es especialmente importante para aplicaciones como la fabricación de microchips, donde incluso los contaminantes más diminutos pueden causar problemas importantes.
-
Composición controlada de gases y vapores:
- El vacío permite controlar con precisión la composición de los gases y vapores dentro de la cámara de procesamiento. Este control es esencial para adaptar las propiedades de la película depositada, como su grosor, uniformidad y composición química. Ajustando la presión y la composición de los gases, los fabricantes pueden conseguir las propiedades específicas del material requeridas para distintas aplicaciones, como revestimientos ópticos, capas resistentes al desgaste o películas conductoras.
-
Alto índice de evaporación térmica:
- En el vacío, la velocidad de evaporación térmica de los materiales es significativamente mayor que en condiciones atmosféricas. Esto se debe a que la presión reducida disminuye el punto de ebullición de los materiales, lo que les permite vaporizarse a temperaturas más bajas. Una tasa de evaporación elevada garantiza una transferencia y deposición eficaces de los materiales, lo que es fundamental para conseguir el grosor y la calidad deseados de la película en un tiempo razonable.
-
Mayor adherencia del material:
- La ausencia de aire u otros fluidos en un entorno de vacío permite que el material vaporizado llegue al sustrato con más energía. Esta mayor energía mejora la adherencia del material al sustrato, lo que se traduce en un revestimiento más resistente y duradero. La mejora de la adherencia es especialmente importante en aplicaciones en las que el revestimiento está sometido a tensiones mecánicas, ciclos térmicos o entornos corrosivos.
-
Proceso de deposición repetible y controlado:
- Un entorno de vacío proporciona un proceso estable y repetible, esencial para las aplicaciones industriales. Al mantener unas condiciones constantes de presión y temperatura, los fabricantes pueden conseguir revestimientos uniformes con propiedades predecibles. Esta repetibilidad es crucial para la producción en serie, donde la consistencia y el control de calidad son primordiales.
-
Entorno de plasma a baja presión:
- El vacío facilita la creación de un entorno de plasma a baja presión, que suele utilizarse en procesos de PVD como el sputtering. El plasma aumenta la ionización del material vaporizado, mejorando la energía y la direccionalidad de las partículas a medida que se depositan sobre el sustrato. El resultado es una mayor densidad, adherencia y calidad general de la película.
-
Requisitos específicos de la aplicación:
- Ciertas aplicaciones, como la producción de microchips, CD y DVD, requieren entornos extremadamente limpios y controlados. Un alto vacío garantiza la eliminación incluso de las partículas más pequeñas, evitando defectos que podrían comprometer la funcionalidad del producto final. Este nivel de limpieza es inalcanzable en condiciones atmosféricas.
En resumen, realizar el PVD en un entorno de vacío es esencial para conseguir revestimientos de alta calidad, uniformes y libres de contaminación. El vacío proporciona las condiciones necesarias para una transferencia eficaz del material, una deposición controlada y una adherencia mejorada, lo que lo hace indispensable para una amplia gama de aplicaciones industriales y tecnológicas.
Cuadro recapitulativo:
Beneficio clave | Descripción |
---|---|
Contaminación reducida | Minimiza los átomos/moléculas no deseados, garantizando revestimientos más limpios y de mayor calidad. |
Aumento de la trayectoria libre media | Aumenta la distancia de desplazamiento de las partículas para una deposición uniforme y precisa. |
Composición controlada del gas | Permite adaptar las propiedades de la película, como el grosor, la uniformidad y la composición química. |
Alto índice de evaporación térmica | Permite una transferencia eficaz del material y una deposición más rápida. |
Adhesión mejorada | Mejora la resistencia y durabilidad del revestimiento en aplicaciones exigentes. |
Proceso repetible | Garantiza resultados uniformes y predecibles para la producción en serie. |
Entorno de plasma a baja presión | Aumenta la densidad y la calidad de la película mediante una ionización mejorada. |
Limpieza específica para cada aplicación | Cumple los estrictos requisitos de industrias como la microelectrónica y la óptica. |
¿Necesita una solución de PVD al vacío para sus necesidades de fabricación? Póngase en contacto con nosotros para saber más