El depósito físico en fase vapor (PVD) es una técnica muy utilizada para depositar películas finas de material sobre un sustrato.El proceso suele realizarse en un entorno de vacío por varias razones fundamentales.El vacío reduce la densidad de átomos en la cámara, lo que aumenta la trayectoria libre media de los átomos y les permite recorrer distancias más largas sin colisionar.Este entorno también minimiza la contaminación gaseosa, garantizando películas puras de alta calidad.Además, el vacío facilita altos índices de evaporación térmica y evita reacciones químicas no deseadas entre el material y los gases atmosféricos, que podrían comprometer las propiedades de la película.El entorno de vacío controlado es esencial para aplicaciones como la fabricación de microchips, donde incluso una contaminación mínima puede provocar defectos importantes.
Explicación de los puntos clave:
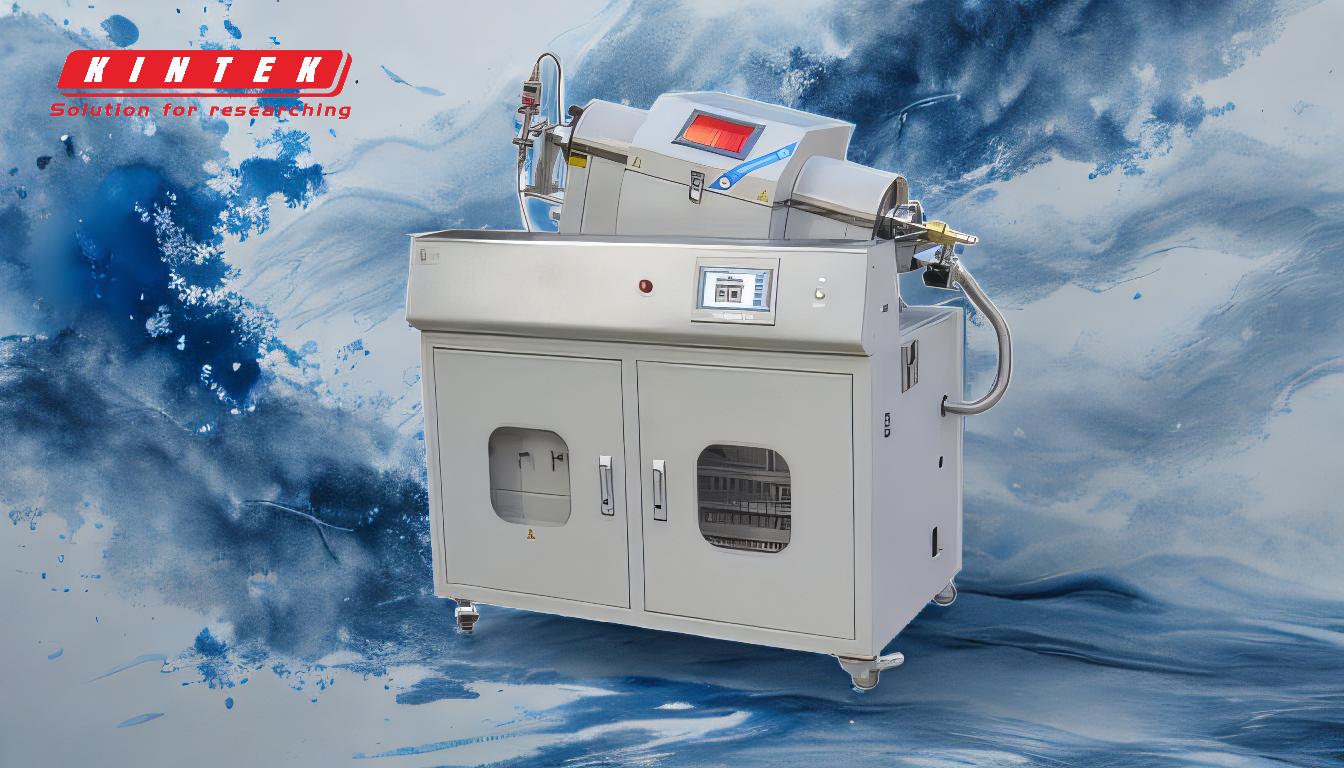
-
Aumento del camino libre medio de los átomos:
- En el vacío, la densidad de átomos se reduce significativamente, lo que aumenta la trayectoria libre media, es decir, la distancia media que puede recorrer un átomo antes de colisionar con otro átomo o molécula.Esto es crucial en PVD porque permite que el material vaporizado viaje sin obstáculos desde la fuente hasta el sustrato, garantizando una deposición uniforme y películas finas de alta calidad.
-
Minimización de la contaminación gaseosa:
- Un entorno de vacío reduce drásticamente la presencia de átomos y moléculas indeseables, como el oxígeno, la humedad y otros gases reactivos.Estos contaminantes pueden reaccionar con el material vaporizado, alterando sus propiedades o creando defectos en la película depositada.Al mantener un alto vacío, el PVD garantiza un entorno limpio y controlado, lo que es especialmente importante para aplicaciones como la fabricación de microchips, donde incluso las trazas de contaminantes pueden causar problemas importantes.
-
Alta tasa de evaporación térmica:
- El entorno de vacío facilita una elevada tasa de evaporación térmica al reducir la presión dentro de la cámara.Esto permite que el material se vaporice a temperaturas más bajas, lo que resulta beneficioso para depositar materiales con puntos de fusión elevados.La ausencia de aire u otros gases también garantiza que el material vaporizado llegue al sustrato con una pérdida de energía mínima, lo que se traduce en un proceso de deposición más eficiente y eficaz.
-
Prevención de reacciones químicas no deseadas:
- En el vacío, se eliminan los elementos reactivos presentes en el aire, como el oxígeno, el dióxido de carbono y el hidrógeno.Esto evita reacciones químicas no deseadas entre el material vaporizado y estos elementos, que de otro modo podrían alterar las propiedades superficiales de la película depositada.Por ejemplo, las reacciones con el oxígeno podrían dar lugar a la formación de óxidos, que podrían ser indeseables en determinadas aplicaciones.
-
Proceso de deposición controlado y repetible:
- El vacío proporciona un entorno controlado que es esencial para lograr resultados consistentes y repetibles en PVD.Al mantener un nivel de vacío específico, los parámetros del proceso pueden controlarse con precisión, garantizando que se reproduzcan las mismas condiciones en cada ciclo de deposición.Esto es fundamental para aplicaciones industriales en las que la uniformidad y la fiabilidad son primordiales.
-
Adhesión y calidad de película mejoradas:
- La ausencia de aire u otros fluidos en el vacío garantiza que el material vaporizado llegue al sustrato con más energía, lo que produce una mejor adherencia y una película más uniforme.Esto es especialmente importante en aplicaciones que requieren revestimientos resistentes y duraderos, como la producción de CD, DVD y otros soportes ópticos.
-
Flexibilidad en los tipos de revestimiento:
- Aunque el PVD se utiliza normalmente para depositar metales y aleaciones sin reacciones químicas, el entorno de vacío también permite la introducción de gases reactivos si se desea.Por ejemplo, puede introducirse oxígeno para crear revestimientos de óxido, lo que proporciona flexibilidad en los tipos de revestimientos que pueden producirse mediante PVD.
En resumen, realizar el PVD en vacío es esencial para conseguir películas finas de alta calidad, libres de contaminación y con un control preciso del proceso de deposición.El entorno de vacío no sólo mejora la eficiencia y la eficacia del proceso, sino que también garantiza que el producto final cumpla los estrictos requisitos de diversas aplicaciones industriales.Para más información sobre procesos relacionados, puede explorar deposición química en fase vapor por plasma y microondas .
Cuadro recapitulativo:
Razón clave | Explicación |
---|---|
Mayor recorrido libre medio | Permite que los átomos se desplacen sin obstáculos, garantizando una deposición uniforme y películas de alta calidad. |
Minimización de la contaminación gaseosa | Reduce los gases reactivos como el oxígeno y la humedad, evitando defectos en la película. |
Alto índice de evaporación térmica | Permite la vaporización a temperaturas más bajas, mejorando la eficiencia y la eficacia. |
Prevención de reacciones químicas | Elimina las reacciones no deseadas con los gases atmosféricos, preservando las propiedades de la película. |
Proceso controlado y repetible | Garantiza resultados uniformes manteniendo niveles de vacío específicos. |
Adhesión y calidad de película mejoradas | Mejora la transferencia de energía, lo que conduce a una mejor adhesión y recubrimientos uniformes. |
Flexibilidad en los tipos de revestimiento | Permite la introducción de gases reactivos para diversas opciones de recubrimiento. |
Obtenga más información sobre cómo el PVD en vacío puede mejorar sus procesos. contacte con nuestros expertos hoy mismo ¡!