Desarrollo histórico de la tecnología de revestimiento al vacío
Los primeros retos y la tecnología CVD
La tecnología de revestimiento al vacío dio sus primeros pasos significativos en la década de 1960 con la llegada del depósito químico en fase vapor (CVD). Esta técnica pionera, aunque revolucionaria en su momento, no estuvo exenta de desafíos. Uno de los obstáculos más importantes era el requisito de altas temperaturas, que limitaba los tipos de sustratos que podían recubrirse eficazmente. Las elevadas exigencias térmicas de los procesos CVD implicaban que sólo los materiales con gran estabilidad térmica podían soportar las condiciones de deposición, lo que reducía considerablemente el campo de aplicaciones potenciales.
Además, la tecnología CVD inicial se veía limitada por la escasa variedad de recubrimientos que podía producir. La complejidad y especificidad de las reacciones químicas implicadas en el CVD implicaban que sólo se podían depositar de forma fiable unos pocos materiales, lo que restringía aún más su utilidad. Estas limitaciones supusieron importantes retos para el desarrollo y la adopción generalizada de la tecnología de revestimiento al vacío, lo que hizo necesaria la búsqueda de métodos alternativos que pudieran superar estas barreras.
En las décadas siguientes, estos primeros retos allanarían el camino para el desarrollo de tecnologías de revestimiento más versátiles y eficaces, como el depósito físico en fase vapor (PVD), que surgió en la década de 1970 y ofrecía una solución más adaptable y respetuosa con el medio ambiente.
Aparición de la tecnología PVD
En la década de 1970, el panorama de la tecnología de revestimiento al vacío experimentó una importante transformación con la aparición de la tecnología de deposición física de vapor (PVD). Este nuevo método no sólo abordó algunas de las preocupaciones medioambientales asociadas a su predecesor, el depósito químico en fase vapor (CVD), sino que también introdujo una miríada de propiedades superficiales versátiles que antes eran inalcanzables. El paso del CVD al PVD se caracterizó por una reducción de las temperaturas operativas y una ampliación de la gama de revestimientos que podían aplicarse, lo que amplió sus aplicaciones en diversas industrias.
Las ventajas medioambientales del PVD fueron especialmente notables. A diferencia del CVD, que a menudo requiere altas temperaturas y productos químicos potencialmente peligrosos, el PVD funciona en condiciones más controladas, lo que permite reducir el consumo de energía y las emisiones. Este respeto por el medio ambiente, unido a su capacidad para producir revestimientos de mayor dureza, resistencia al desgaste y protección contra la corrosión, atrajo rápidamente la atención tanto de investigadores como de industriales.
El rápido desarrollo de la tecnología PVD durante este periodo puede atribuirse a su adaptabilidad y a las importantes mejoras que aportó a la calidad y durabilidad de los revestimientos. Industrias tan diversas como la automovilística o la aeroespacial empezaron a adoptar el PVD por su capacidad para mejorar el rendimiento de herramientas y componentes, lo que se tradujo en una mayor eficacia y una vida útil más larga de los productos. Esta adopción generalizada impulsó los avances en las técnicas de PVD, haciendo avanzar la tecnología y consolidando su lugar en el ámbito de los procesos industriales modernos.
Estado actual y retos
Desarrollo desequilibrado
A pesar de la adopción generalizada de la tecnología de revestimiento al vacío con fines decorativos, la aplicación de estos revestimientos en la fabricación de moldes industriales sigue estando plagada de desafíos. El principal obstáculo radica en los estrictos requisitos de adherencia exigidos por los moldes industriales, que requieren una unión más robusta y duradera entre el revestimiento y el sustrato. Las tecnologías de recubrimiento actuales no satisfacen fácilmente esta mayor demanda, ya que a menudo dan prioridad al atractivo estético frente a la durabilidad funcional.
Además, la falta de tecnologías de procesos integrales adaptadas específicamente al recubrimiento de moldes industriales agrava aún más estos retos. A diferencia de los recubrimientos decorativos, que pueden permitirse ser menos rigurosos en sus métodos de aplicación, los recubrimientos de moldes industriales requieren procesos precisos y controlados para garantizar un rendimiento y una longevidad óptimos. Esta disparidad en el desarrollo tecnológico ha dado lugar a un crecimiento desequilibrado en el sector de los revestimientos al vacío, en el que los avances en revestimientos decorativos no se han reflejado adecuadamente en las aplicaciones industriales.
Para hacer frente a estos problemas, existe una necesidad acuciante de desarrollar tecnologías y metodologías especializadas que puedan satisfacer las demandas exclusivas del revestimiento industrial de moldes. Esto incluye no sólo la mejora de las propiedades de adhesión de los recubrimientos, sino también el perfeccionamiento de toda la cadena de procesos, desde el tratamiento previo hasta el control de calidad posterior a la aplicación. Centrándose en estas áreas, la industria puede salvar la distancia entre los recubrimientos decorativos y los industriales, fomentando una trayectoria de desarrollo más equilibrada y completa.
Disparidades técnicas
En el ámbito de la tecnología de revestimiento al vacío, especialmente en el contexto del PVD (depósito físico en fase vapor), las capacidades técnicas nacionales se encuentran a menudo por detrás de las normas internacionales. Esta disparidad no es sólo una cuestión de sofisticación de los equipos, sino que abarca una gama más amplia de factores, como la optimización de los procesos, los avances en la ciencia de los materiales y las metodologías de control de calidad.
Para colmar esta brecha, es urgente que la industria nacional no sólo introduzca equipos avanzados, sino que también absorba e integre tecnologías de vanguardia. Esto implica un planteamiento polifacético, que incluye
- Modernización de los equipos: Invertir en cámaras de vacío, fuentes de alimentación y sistemas de entrada de gas de última generación capaces de gestionar con precisión complejos procesos de PVD.
- Absorción tecnológica: Investigación y desarrollo en colaboración con socios internacionales para comprender y aplicar las mejores prácticas en tecnología PVD.
- Optimización del proceso: Perfeccionamiento de los procesos existentes para garantizar la uniformidad de la calidad del revestimiento, abordando cuestiones como la adherencia y la consistencia de la capa.
Aspecto | Situación nacional | Normas internacionales |
---|---|---|
Equipos | Básicos o anticuados | Avanzados y de alta precisión |
Control del proceso | Manual o semiautomatizado | Totalmente automatizado con soporte de IA |
Ciencia de materiales | Investigación limitada | Amplia investigación e innovación |
Control de calidad | Métodos ad hoc | FQC sistemático y riguroso |
El camino hacia la paridad no sólo implica la adquisición de tecnología, sino también el desarrollo de un ecosistema sólido que apoye la innovación y la mejora continuas. Este enfoque holístico es esencial para elevar las capacidades nacionales y garantizar que puedan competir a escala mundial.
Conceptos básicos y características del revestimiento PVD
Métodos y técnicas
El depósito físico en fase vapor (PVD) engloba varios métodos avanzados, cada uno con características y aplicaciones únicas. Dos técnicas destacadas dentro del PVD son el metalizado multiarco y el sputtering magnetrónico.
El metalizado multiarco consiste en la evaporación del material objetivo mediante un arco eléctrico que ioniza el material y lo impulsa hacia el sustrato. Este método es conocido por sus altas velocidades de deposición y su capacidad para recubrir geometrías complejas. Sin embargo, puede adolecer de problemas como la contaminación por partículas y la falta de uniformidad del grosor del revestimiento.
Por otro lado, el pulverizado con magnetrón emplea un campo magnético para aumentar la ionización de los átomos objetivo, que se aceleran hacia el sustrato. Esta técnica permite controlar mejor las propiedades del revestimiento, como la densidad y la uniformidad, por lo que es ideal para aplicaciones que requieren revestimientos precisos. A pesar de estas ventajas, el sputtering por magnetrón puede ser más lento y consumir más energía que el metalizado multiarco.
Método | Ventajas | Desventajas |
---|---|---|
Metalizado multiarco | Altas velocidades de deposición, adecuado para geometrías complejas | Contaminación por partículas, espesor de recubrimiento no uniforme |
Pulverización catódica por magnetrón | Excelente control de las propiedades del revestimiento, alta densidad y uniformidad | Proceso más lento, mayor consumo de energía |
Comprender estos métodos y sus respectivos pros y contras es crucial para seleccionar la técnica de PVD más adecuada para aplicaciones industriales específicas.
Combinación de tecnologías
La integración de las tecnologías multiarco y magnetrón representa un avance significativo en el campo del revestimiento al vacío. Esta combinación no es una mera suma de sus partes, sino un enfoque sinérgico que maximiza las ventajas de ambas tecnologías, garantizando la producción de revestimientos estables y de alta calidad.
El metalizado multiarco, conocido por sus altas velocidades de deposición y su capacidad para producir revestimientos densos, complementa al sputtering por magnetrón, que destaca en la producción de revestimientos uniformes y conformados con un calentamiento mínimo del sustrato. Combinando estos métodos, los fabricantes pueden lograr un equilibrio entre la velocidad de deposición y la uniformidad del revestimiento, algo fundamental para las aplicaciones que requieren eficiencia y precisión.
Además, la hibridación de estas tecnologías permite optimizar las propiedades del revestimiento. Por ejemplo, la incorporación de iones multiarco en el proceso de pulverización catódica por magnetrón puede mejorar la adherencia y dureza de los revestimientos, abordando retos comunes en el revestimiento de moldes industriales donde una mayor adherencia y durabilidad son primordiales.
Esta integración también abre nuevas vías para la selección de materiales y el control de procesos. Al aprovechar los puntos fuertes de ambas tecnologías, es posible depositar una gama más amplia de materiales con propiedades a medida, desde revestimientos duros resistentes al desgaste hasta estructuras multicapa más complejas. El resultado es una solución de revestimiento más versátil y robusta que satisface las diversas demandas de varias aplicaciones industriales.
En resumen, la combinación de las tecnologías multiarco y magnetrón no sólo mejora la calidad y la estabilidad de los revestimientos, sino que también amplía el alcance de las propiedades de los materiales y la eficiencia de los procesos que se pueden conseguir. Este avance es fundamental para ampliar los límites de lo que puede lograr la tecnología de revestimiento al vacío, convirtiéndola en una piedra angular en la evolución de los revestimientos industriales.
Equipos y procesos de recubrimiento modernos
Componentes y sistemas
Los modernos equipos de revestimiento son un sofisticado conjunto de componentes esenciales, cada uno de los cuales desempeña un papel crucial en el proceso de deposición al vacío. En el corazón de este sistema se encuentra lacámara de vacíoun entorno sellado que aísla el sustrato de las condiciones atmosféricas, garantizando una superficie prístina para el revestimiento. La cámara de vacío suele construirse con materiales como el acero inoxidable, conocido por su durabilidad y resistencia a la corrosión.
Para alcanzar los niveles de vacío necesarios,piezas de obtención de vacío de vacío. Entre ellas se encuentran las bombas de vacío, como las bombas rotativas de paletas y las bombas turbomoleculares, que trabajan en tándem para reducir la presión de la cámara a los niveles ultrabajos necesarios para los procesos de PVD. La eficacia de estas bombas es fundamental, ya que influye directamente en la calidad y uniformidad del revestimiento.
Las fuentes de alimentación son otro componente crítico, ya que proporcionan la energía eléctrica necesaria para vaporizar el material de revestimiento. Los sistemas modernos suelen utilizarfuentes de alimentación de frecuencia intermedia otecnología de impulsosque ofrecen un control preciso del proceso de deposición, lo que se traduce en revestimientos de mayor calidad. Estas fuentes de alimentación avanzadas ayudan a mitigar problemas como la formación de arcos y la deposición no uniforme, problemas habituales en las configuraciones tradicionales de PVD.
Por último, lossistemas de entrada de gas de proceso forman parte integral de la operación. Estos sistemas introducen gases reactivos en la cámara de vacío, lo que permite la formación de revestimientos complejos con propiedades a medida. El control preciso de los caudales y la composición de los gases permite crear revestimientos con características mecánicas, químicas y ópticas específicas, lo que aumenta la versatilidad y aplicabilidad de la tecnología.
En resumen, el equipo de recubrimiento moderno es una compleja interacción de cámaras de vacío, piezas de obtención de vacío, fuentes de alimentación y sistemas de entrada de gas de proceso, cada uno de los cuales contribuye a la precisión y calidad del proceso de PVD.
Técnicas avanzadas
En el ámbito de la tecnología de revestimiento al vacío, han surgido varias técnicas avanzadas que mejoran significativamente la calidad y aplicabilidad de los revestimientos. Una de estas técnicas es la utilización decampos magnéticos de no equilibrio. Estos campos permiten un control más preciso del proceso de deposición, posibilitando la creación de revestimientos con una uniformidad y adherencia superiores. Esto es especialmente beneficioso en aplicaciones industriales en las que la durabilidad y el rendimiento del revestimiento son fundamentales.
Otro avance fundamental es la introducción defuentes de alimentación de frecuencia intermedia. A diferencia de las fuentes de alimentación tradicionales, estos sistemas de frecuencia intermedia ofrecen mayor estabilidad y eficacia. Facilitan la deposición de revestimientos más gruesos y robustos sin comprometer la integridad del material subyacente. Esta innovación es especialmente útil en industrias que requieren revestimientos de alto rendimiento para moldes y herramientas.
Además,tecnología de pulsos ha revolucionado el proceso de revestimiento. Al suministrar energía en ráfagas cortas y controladas, la tecnología de pulsos minimiza la tensión térmica sobre el sustrato, evitando deformaciones y degradaciones. Este método es especialmente ventajoso para materiales delicados o que requieren tratamientos superficiales complejos. El suministro preciso de energía también garantiza que el revestimiento se adhiera con mayor eficacia, lo que se traduce en resultados más duraderos y fiables.
Estas técnicas avanzadas contribuyen colectivamente a la evolución de la tecnología de revestimiento al vacío, haciéndola más versátil y eficaz en diversas aplicaciones industriales. La integración de campos magnéticos de no equilibrio, fuentes de alimentación de frecuencia intermedia y tecnología de pulsos no sólo mejora la calidad de los revestimientos, sino que también amplía su aplicabilidad, satisfaciendo las demandas cada vez más estrictas de las industrias modernas.
Aplicación y control de calidad en PVD para moldes
Procesos de pretratamiento y recubrimiento
Los métodos de pretratamiento son pasos cruciales en la preparación de superficies para el recubrimiento por deposición física de vapor (PVD). Estos métodos incluyen la limpieza con vapor a alta temperatura, que elimina eficazmente los contaminantes y garantiza un sustrato limpio. El chorro de arena es otra técnica vital, ya que proporciona una superficie rugosa que mejora la adherencia del revestimiento. El propio proceso de revestimiento PVD depende en gran medida de un control preciso de la temperatura y un calentamiento uniforme para lograr resultados óptimos.
El calentamiento uniforme es esencial porque garantiza que el sustrato se caliente uniformemente, lo que a su vez permite una deposición uniforme del material de revestimiento. El control de la temperatura es igualmente importante, ya que las desviaciones pueden provocar incoherencias en el grosor y la calidad del revestimiento. A menudo se emplean técnicas avanzadas, como fuentes de alimentación de frecuencia intermedia y tecnología de impulsos, para mantener unas condiciones de calentamiento estables y constantes, mejorando así la calidad general del revestimiento PVD.
Estos procesos de pretratamiento y revestimiento son esenciales para el éxito de las aplicaciones de PVD en moldes industriales. No sólo mejoran la durabilidad y el rendimiento de los moldes, sino que también prolongan su vida útil, lo que los hace indispensables en entornos de fabricación de alta precisión.
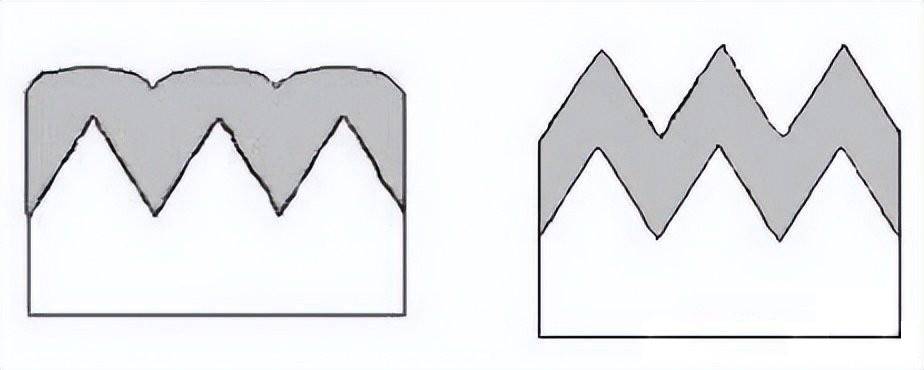
Medidas de control de calidad
El Control de Calidad Funcional (FQC) es un aspecto crítico para garantizar la fiabilidad y el rendimiento de los moldes recubiertos. Este proceso abarca varias inspecciones meticulosas para garantizar que los revestimientos cumplen las normas exigidas.
Uno de los métodos principales del FQC es lainspección de aspecto. Se trata de un examen visual minucioso para detectar cualquier imperfección de la superficie, como arañazos, picaduras o decoloración. Estos defectos pueden afectar significativamente a la funcionalidad y la vida útil del molde, por lo que este paso es indispensable.
Otro método clave es lainspección en profundidad de capas. Esta técnica mide el grosor de las capas de revestimiento para garantizar que se ajustan a los parámetros especificados. Se emplean diversos instrumentos, como perfilómetros y microscopios electrónicos de barrido, para determinar con precisión la profundidad y uniformidad del revestimiento.
Elinspección de adherencia también es crucial. Este proceso evalúa la fuerza de adherencia entre el revestimiento y el sustrato del molde. Entre los métodos habituales se incluyen pruebas de rayado, pruebas de tracción y pruebas de corte transversal. Estas pruebas ayudan a identificar posibles problemas de delaminación o desprendimiento, garantizando la durabilidad y eficacia del revestimiento.
Mediante la integración de estos métodos de FQC, los fabricantes pueden garantizar que sus moldes recubiertos no sólo cumplen las normas del sector, sino que las superan, proporcionando herramientas fiables y de alto rendimiento para diversas aplicaciones industriales.
CONTÁCTANOS PARA UNA CONSULTA GRATUITA
Los productos y servicios de KINTEK LAB SOLUTION han sido reconocidos por clientes de todo el mundo. Nuestro personal estará encantado de ayudarle con cualquier consulta que pueda tener. ¡Contáctenos para una consulta gratuita y hable con un especialista del producto para encontrar la solución más adecuada para sus necesidades de aplicación!