El sinterizado láser de metales (MLS) es un sofisticado proceso de fabricación aditiva que utiliza un láser de alta potencia para fusionar capa a capa partículas de polvo metálico y crear un objeto sólido tridimensional.Este proceso se utiliza ampliamente en sectores como el aeroespacial, la automoción y los dispositivos médicos debido a su capacidad para producir geometrías complejas con gran precisión y eficiencia material.El proceso implica varios pasos clave, como la preparación del polvo, el sinterizado láser y el postprocesado, cada uno de los cuales desempeña un papel fundamental en la obtención de las propiedades deseadas del producto final.
Explicación de los puntos clave:
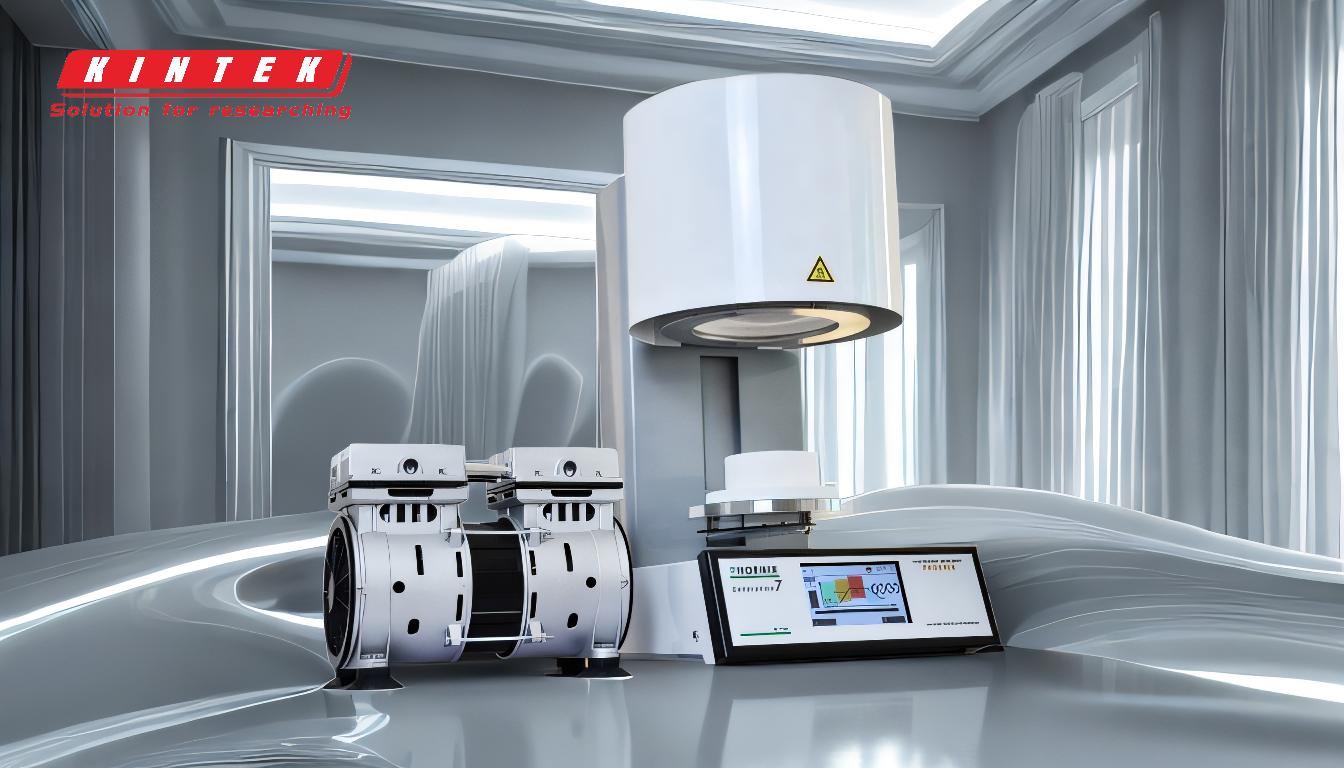
-
Preparación del polvo:
- Selección de materiales:El proceso comienza con la selección de los polvos metálicos adecuados.Los materiales más comunes son el titanio, el aluminio, el acero inoxidable y las aleaciones de níquel.La elección del material depende de las propiedades deseadas del producto final, como la fuerza, la durabilidad y la resistencia térmica.
- Mezcla de polvos:Los polvos metálicos suelen mezclarse con elementos de aleación y aditivos para mejorar propiedades específicas.Esta mezcla garantiza una mezcla homogénea que dará como resultado un producto final uniforme.
-
Proceso de sinterización por láser:
- Deposición de capas:Se extiende uniformemente una fina capa de polvo metálico sobre la plataforma de impresión.El grosor de esta capa suele oscilar entre 20 y 100 micras, en función de la resolución deseada y de la aplicación específica.
- Fusión por láser:Un rayo láser de alta potencia se dirige al lecho de polvo, fundiendo selectivamente las partículas de polvo según el modelo digital en 3D de la pieza.La energía del láser se controla con precisión para garantizar que las partículas de metal se fundan sin causar una distorsión térmica excesiva.
- Unión de capas:A medida que se sinteriza cada capa, se adhiere a las capas anteriores sinterizadas situadas debajo.Este enfoque por capas permite crear geometrías y estructuras internas complejas que serían difíciles o imposibles de conseguir con los métodos de fabricación tradicionales.
-
Atmósfera controlada:
- Gas inerte Medio ambiente:El proceso de sinterización suele tener lugar en una atmósfera controlada, a menudo llena de gases inertes como el argón o el nitrógeno.Este entorno evita la oxidación y contaminación del metal, garantizando la integridad y calidad del producto final.
- Control de la temperatura:El horno de sinterización mantiene una temperatura precisa, normalmente justo por debajo del punto de fusión del metal, para facilitar la difusión atómica y la unión entre las partículas sin provocar su fusión total.
-
Tratamiento posterior:
- Eliminación del exceso de polvo:Una vez finalizado el proceso de sinterización, se retira el polvo sobrante que no ha sido fundido por el láser.A menudo, este polvo puede reciclarse y reutilizarse en construcciones posteriores.
- Tratamiento térmico:Dependiendo del material y de las propiedades deseadas, la pieza sinterizada puede someterse a procesos adicionales de tratamiento térmico, como el recocido o el alivio de tensiones, para mejorar sus propiedades mecánicas.
- Acabado de la superficie:El paso final suele implicar procesos de acabado superficial como el mecanizado, el pulido o el revestimiento para conseguir la calidad superficial y la precisión dimensional deseadas.
-
Ventajas y aplicaciones:
- Geometrías complejas:El MLS permite crear piezas con estructuras internas complejas y detalles intrincados que no son factibles con los métodos de fabricación tradicionales.
- Eficacia del material:El proceso es muy eficiente en cuanto al material, ya que sólo utiliza la cantidad de polvo necesaria para construir la pieza, minimizando los residuos.
- Personalización y creación de prototipos:El MLS es especialmente valioso para la creación rápida de prototipos y la fabricación a medida, ya que permite una rápida iteración y personalización de los diseños.
- Aplicaciones industriales:La tecnología se utiliza ampliamente en sectores que requieren componentes de alto rendimiento, como el aeroespacial para estructuras ligeras, el automovilístico para piezas a medida y el médico para implantes específicos para cada paciente.
En resumen, el sinterizado láser de metales es un proceso de fabricación versátil y preciso que aprovecha la potencia de los láseres para fusionar polvos metálicos en piezas complejas de alto rendimiento.El proceso implica una preparación cuidadosa de los materiales, un control preciso del entorno de sinterización y un postprocesado minucioso para conseguir las propiedades y el acabado deseados.Esta tecnología sigue revolucionando la fabricación al permitir la producción de piezas que antes eran imposibles de crear con los métodos tradicionales.
Cuadro sinóptico:
Pasos clave | Detalles |
---|---|
Preparación del polvo | - Selección del material (por ejemplo, titanio, aluminio, acero inoxidable). |
- Mezcla de polvos para obtener propiedades uniformes. | |
Sinterización láser | - Deposición de capas (20-100 micras). |
- Fusión por láser para una fusión precisa.
- Unión por capas para geometrías complejas.| | Atmósfera controlada
- | - Entorno de gas inerte (argón o nitrógeno). Control preciso de la temperatura.| |
- Tratamiento posterior
- | Eliminación del exceso de polvo. Tratamiento térmico (recocido, distensión). Acabado superficial (mecanizado, pulido).|
- |
- Ventajas | Geometrías complejas. Eficacia de los materiales.
Creación rápida de prototipos y personalización.| | Aplicaciones