Los sistemas de lecho fluidizado, en particular los reactores de lecho fluidizado (FBR) y los pirolizadores, se utilizan ampliamente en industrias como el procesamiento químico, el refinado de petróleo y la conversión de biomasa.Estos sistemas ofrecen importantes ventajas, como una distribución uniforme de la temperatura, una transferencia de calor eficaz y un alto rendimiento de los productos deseados, como los bioaceites.Sin embargo, también plantean problemas, como la necesidad de partículas de pequeño tamaño, los elevados costes de funcionamiento y la necesidad de grandes cantidades de gases inertes.Comprender estos pros y contras es esencial para evaluar su idoneidad para aplicaciones específicas.
Explicación de los puntos clave:
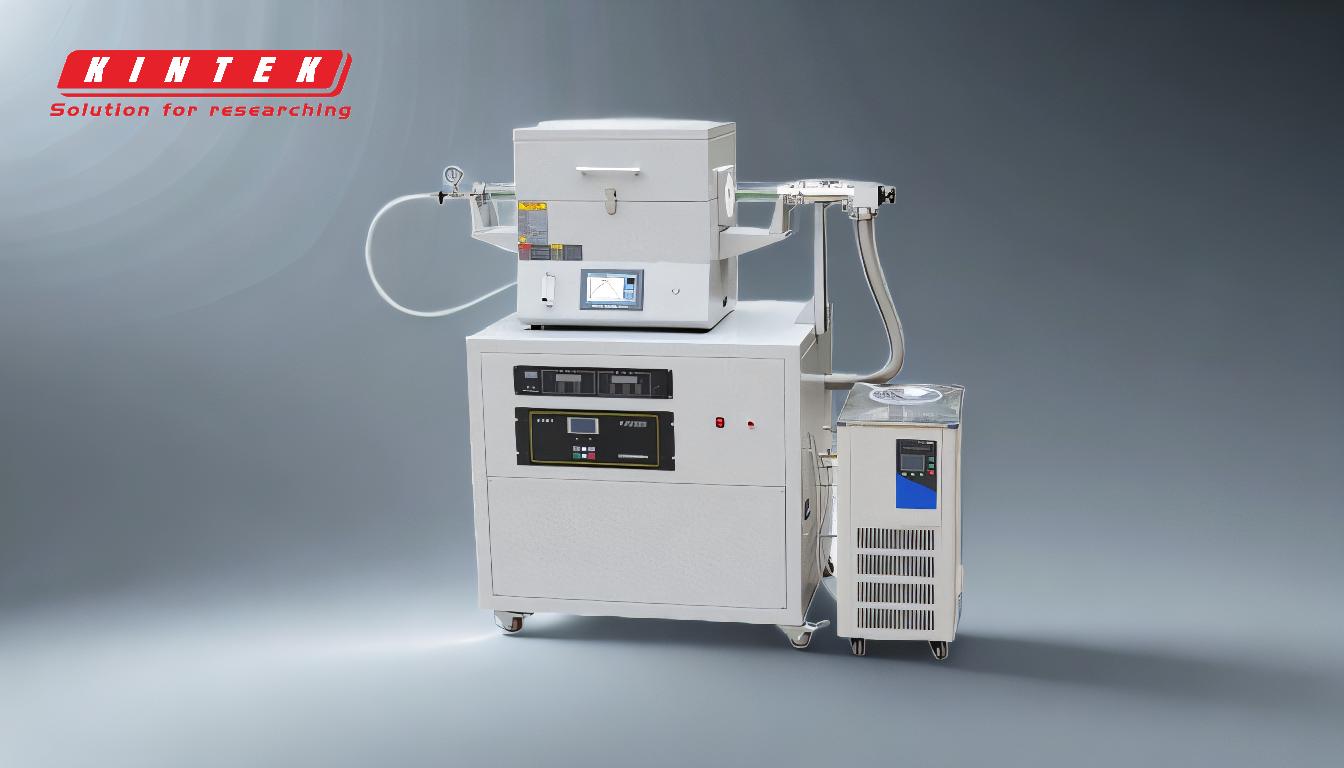
-
Ventajas de los sistemas de lecho fluidizado
-
Distribución uniforme de la temperatura:
Los sistemas de lecho fluidizado garantizan gradientes de temperatura uniformes, lo que evita puntos calientes o fríos.Esto es especialmente beneficioso para las reacciones exotérmicas, ya que minimiza el riesgo de fuga térmica y garantiza una calidad constante del producto. -
Transferencia de calor eficaz:
El comportamiento fluido de las partículas sólidas del lecho favorece la transferencia de calor entre las partículas y el gas circundante.El resultado es un calentamiento más rápido y eficaz, crucial para procesos como la pirólisis. -
Alto rendimiento de los productos deseados:
Los pirólizadores de lecho fluidizado, por ejemplo, pueden alcanzar altos rendimientos de bioaceite de hasta el 75%.Esto los hace muy eficaces para convertir la biomasa en subproductos valiosos como bioaceites y gases. -
Mezcla uniforme de partículas:
El proceso de fluidización garantiza la mezcla completa de las partículas, eliminando los gradientes de concentración radiales y axiales.Esto mejora la eficacia de la reacción y la consistencia del producto. -
Complejidad media en la construcción y el funcionamiento:
Aunque los sistemas de lecho fluidizado son más complejos que algunas alternativas, en general son más fáciles de construir y operar en comparación con otros reactores avanzados. -
Facilidad de ampliación:
Los sistemas de lecho fluidizado son relativamente fáciles de ampliar para aplicaciones industriales, lo que los hace adecuados para la producción a gran escala. -
Funcionamiento continuo:
A diferencia de los procesos por lotes, los reactores de lecho fluidizado pueden funcionar de forma continua, eliminando la necesidad de frecuentes arranques y paradas.Esto mejora la eficiencia de la producción y reduce el tiempo de inactividad.
-
Distribución uniforme de la temperatura:
-
Desventajas de los sistemas de lecho fluidizado
-
Necesidad de partículas de pequeño tamaño:
Los sistemas de lecho fluidizado requieren que los materiales de alimentación sean finamente molidos en pequeñas partículas para lograr una fluidización adecuada.Este paso de preprocesamiento puede aumentar la complejidad y los costes operativos. -
Costes operativos elevados:
La necesidad de grandes cantidades de gases inertes (por ejemplo, nitrógeno) para mantener el estado fluidizado y evitar reacciones no deseadas puede aumentar considerablemente los gastos de explotación. -
Gran cantidad de gases inertes:
La dependencia de los gases inertes no sólo aumenta los costes, sino que también introduce retos logísticos, como el almacenamiento y la manipulación. -
Erosión y desgaste:
El movimiento constante de las partículas en el lecho puede provocar la erosión y el desgaste de los componentes del reactor, lo que requiere un mantenimiento y una sustitución frecuentes. -
Complejidad en el manejo de partículas finas:
Las partículas finas pueden ser difíciles de manipular y pueden provocar problemas como atascos o pérdidas de material durante el procesado. -
Aplicabilidad limitada a determinadas materias primas:
Aunque los sistemas de lecho fluidizado son eficaces para sustratos particulados como la biomasa leñosa, pueden no ser adecuados para todos los tipos de materias primas, en particular las que tienen formas irregulares o un alto contenido de humedad.
-
Necesidad de partículas de pequeño tamaño:
-
Aplicaciones e idoneidad
-
Conversión de biomasa:
Los sistemas de lecho fluidizado son muy eficaces para convertir la biomasa en bioaceites, gases y otros subproductos valiosos.Su capacidad para tratar sustratos particulados los hace ideales para la biomasa leñosa y materiales similares. -
Industrias química y petrolera:
Estos sistemas se utilizan ampliamente en las industrias química y petrolera para procesos como el craqueo catalítico y la gasificación, en los que son fundamentales una temperatura uniforme y una transferencia de calor eficaz. -
Reacciones exotérmicas:
Los gradientes de temperatura uniformes de los reactores de lecho fluidizado los hacen especialmente adecuados para reacciones exotérmicas, en las que es esencial controlar la liberación de calor.
-
Conversión de biomasa:
-
Consideraciones para los compradores
-
Análisis coste-beneficio:
Los compradores deben sopesar los elevados costes iniciales y de explotación frente a las ventajas de un alto rendimiento del producto y un funcionamiento eficaz. -
Compatibilidad de las materias primas:
Es importante asegurarse de que la materia prima es compatible con el sistema de lecho fluidizado, especialmente en lo que se refiere al tamaño de las partículas y al contenido de humedad. -
Requisitos de mantenimiento:
El potencial de erosión y desgaste debe tenerse en cuenta en los planes y presupuestos de mantenimiento. -
Escalabilidad:
Para la producción a gran escala, la facilidad de ampliación de los sistemas de lecho fluidizado es una ventaja significativa.
-
Análisis coste-beneficio:
En conclusión, los sistemas de lecho fluidizado ofrecen numerosas ventajas, como la distribución uniforme de la temperatura, la transferencia eficaz de calor y el alto rendimiento de los productos.Sin embargo, hay que tener muy en cuenta sus desventajas, como los elevados costes de funcionamiento y la necesidad de partículas de pequeño tamaño.Evaluando estos factores, los compradores pueden determinar si los sistemas de lecho fluidizado son la opción adecuada para sus aplicaciones específicas.
Cuadro sinóptico:
Aspecto | Ventajas | Desventajas |
---|---|---|
Control de la temperatura | Distribución uniforme de la temperatura, evita puntos calientes/fríos | Requiere partículas de pequeño tamaño para una fluidización adecuada |
Transferencia de calor | Transferencia de calor eficiente, calentamiento más rápido para procesos como la pirólisis | Costes de funcionamiento elevados debido a los requisitos de gas inerte |
Rendimiento del producto | Alto rendimiento de los productos deseados (por ejemplo, bioaceites de hasta el 75%) | Se necesitan grandes cantidades de gases inertes, lo que aumenta los retos logísticos |
Mezcla de partículas | Mezcla completa, elimina los gradientes de concentración | Erosión y desgaste de los componentes del reactor debido al constante movimiento de partículas |
Escalabilidad | Fácil de ampliar para aplicaciones industriales | Manipulación compleja de partículas finas, posibilidad de obstrucción o pérdida de material |
Funcionamiento | Funcionamiento continuo, reduce el tiempo de inactividad y mejora la eficiencia | Aplicabilidad limitada para materias primas con formas irregulares o alto contenido de humedad |
¿Está listo para optimizar sus procesos industriales con sistemas de lecho fluidizado? Póngase en contacto con nuestros expertos para obtener soluciones a medida.