La forja es un proceso de fabricación fundamental en la industria del automóvil, que se utiliza para producir componentes resistentes, duraderos y de alto rendimiento.Consiste en dar forma al metal utilizando fuerzas de compresión localizadas, normalmente con martillos, prensas o matrices.La industria del automóvil utiliza varios procesos de forja para crear piezas como cigüeñales, bielas, engranajes y componentes de suspensión.Cada método de forja ofrece ventajas únicas en términos de precisión, propiedades de los materiales y eficacia de la producción.Comprender los distintos tipos de procesos de forja ayuda a los fabricantes a seleccionar el método más adecuado para aplicaciones específicas de automoción.
Explicación de los puntos clave:
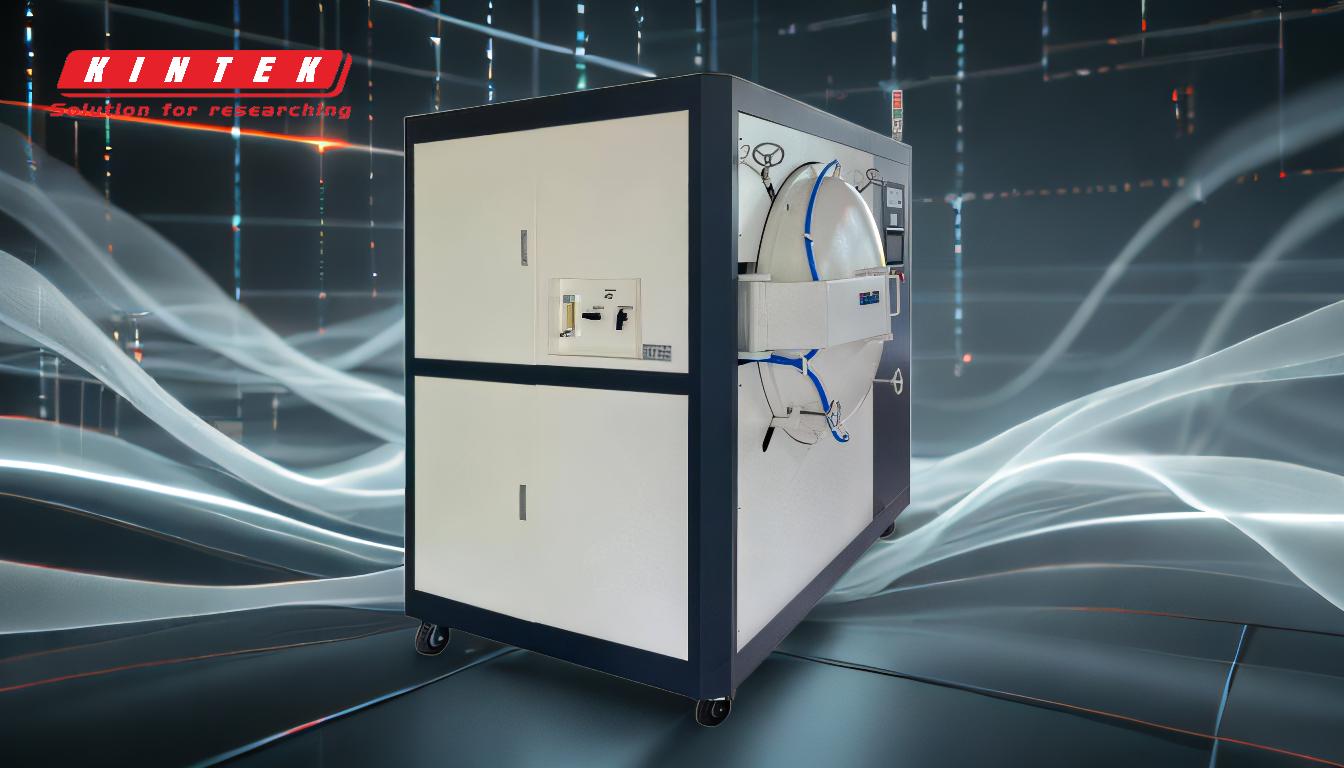
-
Forja con matriz abierta
- Descripción:La forja con matriz abierta, también conocida como forja libre, consiste en deformar el metal entre matrices planas o de forma simple.La pieza no está totalmente cerrada, lo que permite una gran flexibilidad de forma y tamaño.
- Aplicaciones:Se utiliza para componentes de gran tamaño y formas sencillas, como ejes, anillos y cilindros en la industria del automóvil.
-
Ventajas:
- Adecuado para piezas grandes.
- Permite la personalización y la flexibilidad.
- Mejora la resistencia del material y la estructura del grano.
- Limitaciones:Menos precisa que la forja con matriz cerrada, requiere mecanizado adicional para las dimensiones finales.
-
Forja con matriz cerrada (forja con matriz de impresión)
- Descripción:En la forja con matriz cerrada, el metal se comprime entre dos o más matrices que contienen un perfil precortado de la pieza deseada.El material fluye por las cavidades de las matrices para dar la forma final.
- Aplicaciones:Comúnmente utilizado para producir piezas complejas de automoción como engranajes, cigüeñales y bielas.
-
Ventajas:
- Alta precisión y exactitud dimensional.
- Mínimo desperdicio de material.
- Excelentes propiedades mecánicas gracias al flujo controlado del grano.
- Limitaciones:Costes de utillaje más elevados y limitación a piezas pequeñas y medianas.
-
Forja con rodillos
- Descripción:La forja con rodillos consiste en hacer pasar el metal entre dos rodillos giratorios con ranuras perfiladas.Los rodillos comprimen y moldean el metal a su paso.
- Aplicaciones:Se utiliza para fabricar componentes largos y cónicos como ejes, palancas y ballestas en vehículos.
-
Ventajas:
- Eficaz para piezas largas con secciones transversales uniformes.
- Reduce el desperdicio de material y mejora el acabado superficial.
- Limitaciones:Limitado a piezas con geometrías sencillas y requiere equipos especializados.
-
Forja por deformación
- Descripción:La forja por recalcado aumenta el diámetro de una pieza metálica comprimiendo su longitud.Este proceso suele realizarse con prensas horizontales o verticales.
- Aplicaciones:Ideal para crear cabezas de tornillos, válvulas y otros componentes con extremos agrandados.
-
Ventajas:
- Aumenta la resistencia y la densidad del material.
- Adecuado para grandes volúmenes de producción.
- Limitaciones:Limitado a piezas con ampliaciones localizadas y requiere un control preciso del flujo de material.
-
Forja isotérmica
- Descripción:La forja isotérmica se realiza a una temperatura constante, normalmente utilizando matrices calentadas para mantener la temperatura de la pieza durante todo el proceso.
- Aplicaciones:Se utiliza para componentes de alto rendimiento como álabes de turbina y piezas aeroespaciales, pero también se aplica en automoción para aplicaciones especializadas.
-
Ventajas:
- Produce piezas con propiedades mecánicas superiores.
- Reduce las tensiones residuales y mejora la precisión dimensional.
- Limitaciones:Elevados costes de equipamiento y energía, por lo que es menos habitual para piezas estándar de automoción.
-
Forja de precisión
- Descripción:La forja de precisión es un proceso que produce piezas con requisitos mínimos de mecanizado.Utiliza matrices de alta precisión para conseguir tolerancias muy ajustadas.
- Aplicaciones:Adecuado para componentes críticos de automoción como engranajes, piezas de transmisión y componentes de dirección.
-
Ventajas:
- Reduce el desperdicio de material y el tiempo de mecanizado.
- Mejora la solidez y la resistencia a la fatiga de las piezas.
- Limitaciones:Costes iniciales de utillaje elevados y requiere equipos avanzados.
-
Forja en frío
- Descripción:La forja en frío se realiza a temperatura ambiente o próxima a ella, utilizando matrices de alta presión para dar forma al metal.
- Aplicaciones:Comúnmente utilizado para la producción de elementos de fijación, pernos y pequeños componentes de automoción.
-
Ventajas:
- Mejora la resistencia del material y el acabado superficial.
- Rentable para grandes volúmenes de producción.
- Limitaciones:Limitado a piezas más pequeñas y requiere equipos de alta presión.
-
Forja en caliente
- Descripción:La forja en caliente consiste en calentar el metal por encima de su temperatura de recristalización para hacerlo más maleable.A continuación, se da forma al metal calentado mediante matrices o prensas.
- Aplicaciones:Ampliamente utilizado para la producción de grandes piezas de automoción como cigüeñales, bielas y componentes de suspensión.
-
Ventajas:
- Permite formas complejas y piezas de gran tamaño.
- Mejora la ductilidad del material y reduce la resistencia a la deformación.
- Limitaciones:Mayor consumo de energía y posibilidad de oxidación o incrustación.
Cada proceso de forja ofrece ventajas distintas y se elige en función de los requisitos específicos del componente de automoción que se va a fabricar.Factores como la complejidad de la pieza, las propiedades del material, el volumen de producción y las consideraciones de coste desempeñan un papel crucial en la selección del método de forja adecuado.Aprovechando estos procesos, la industria del automóvil puede producir componentes de alta calidad, duraderos y fiables que satisfagan las exigencias de los vehículos modernos.
Tabla resumen:
Proceso de forja | Descripción | Aplicaciones | Ventajas | Limitaciones |
---|---|---|---|---|
Forja con matriz abierta | Deforma el metal entre matrices planas o de forma simple. | Componentes grandes de forma simple como ejes, anillos y cilindros. | Adecuado para piezas grandes, personalizable, mejora la resistencia del material. | Menos preciso, requiere mecanizado adicional. |
Forja en matriz cerrada | Comprime el metal entre matrices con perfiles precortados. | Piezas complejas como engranajes, cigüeñales y bielas. | Alta precisión, mínimo desperdicio, excelentes propiedades mecánicas. | Costes de utillaje más elevados, limitado a piezas pequeñas y medianas. |
Forja por rodillos | Da forma al metal entre rodillos giratorios con ranuras. | Componentes largos y cónicos como ejes, palancas y ballestas. | Eficaz para piezas largas, reduce los residuos y mejora el acabado superficial. | Limitado a geometrías sencillas, requiere equipos especializados. |
Forja por deformación | Aumenta el diámetro comprimiendo la longitud. | Atornilla cabezas, válvulas y componentes con extremos agrandados. | Aumenta la resistencia y la densidad, adecuado para la producción de grandes volúmenes. | Limitado a ampliaciones localizadas, requiere un control preciso. |
Forja isotérmica | Se realiza a temperatura constante con matrices calentadas. | Componentes de alto rendimiento como álabes de turbina y piezas aeroespaciales. | Propiedades mecánicas superiores, reduce las tensiones residuales. | Costes de equipo y energía elevados, menos habituales para piezas estándar de automoción. |
Forja de precisión | Proceso de forma casi neta con un mecanizado mínimo. | Componentes críticos como engranajes, piezas de transmisión y componentes de dirección. | Reduce los residuos y el tiempo de mecanizado, mejora la resistencia y la resistencia a la fatiga. | Costes de utillaje elevados, requiere equipos avanzados. |
Forja en frío | Da forma al metal a temperatura ambiente o cercana a ella utilizando matrices de alta presión. | Elementos de fijación, pernos y pequeños componentes de automoción. | Mejora la resistencia y el acabado superficial, rentable para grandes volúmenes. | Limitado a piezas pequeñas, requiere equipos de alta presión. |
Forja en caliente | Calienta el metal por encima de la temperatura de recristalización para darle forma. | Piezas grandes como cigüeñales, bielas y componentes de suspensión. | Permite formas complejas, mejora la ductilidad, reduce la resistencia a la deformación. | Mayor consumo de energía, posibilidad de oxidación o incrustación. |
¿Necesita ayuda para elegir el proceso de forja adecuado para sus componentes de automoción? Póngase en contacto hoy mismo con nuestros expertos para obtener soluciones a medida.