El recocido, si bien es beneficioso para mejorar las propiedades de los materiales como la ductilidad y la reducción de las tensiones internas, tiene ciertas desventajas. Un inconveniente importante es su impacto en las propiedades mecánicas, particularmente en materiales como el acero para tuberías X80. Por ejemplo, el recocido con bajo contenido de hidrógeno a 200 °C durante 12 horas altera la curva tensión-deformación, lo que conduce a un aumento del límite elástico pero a una reducción del alargamiento. Esto ocurre debido a que los átomos de carbono se difunden en los sitios intersticiales de dislocaciones, formando una atmósfera de Cottrell que fija las dislocaciones, reduciendo así la densidad de las dislocaciones móviles. Dichos cambios pueden comprometer el rendimiento del material en aplicaciones específicas, lo que resalta la necesidad de una consideración cuidadosa de los parámetros de recocido.
Puntos clave explicados:
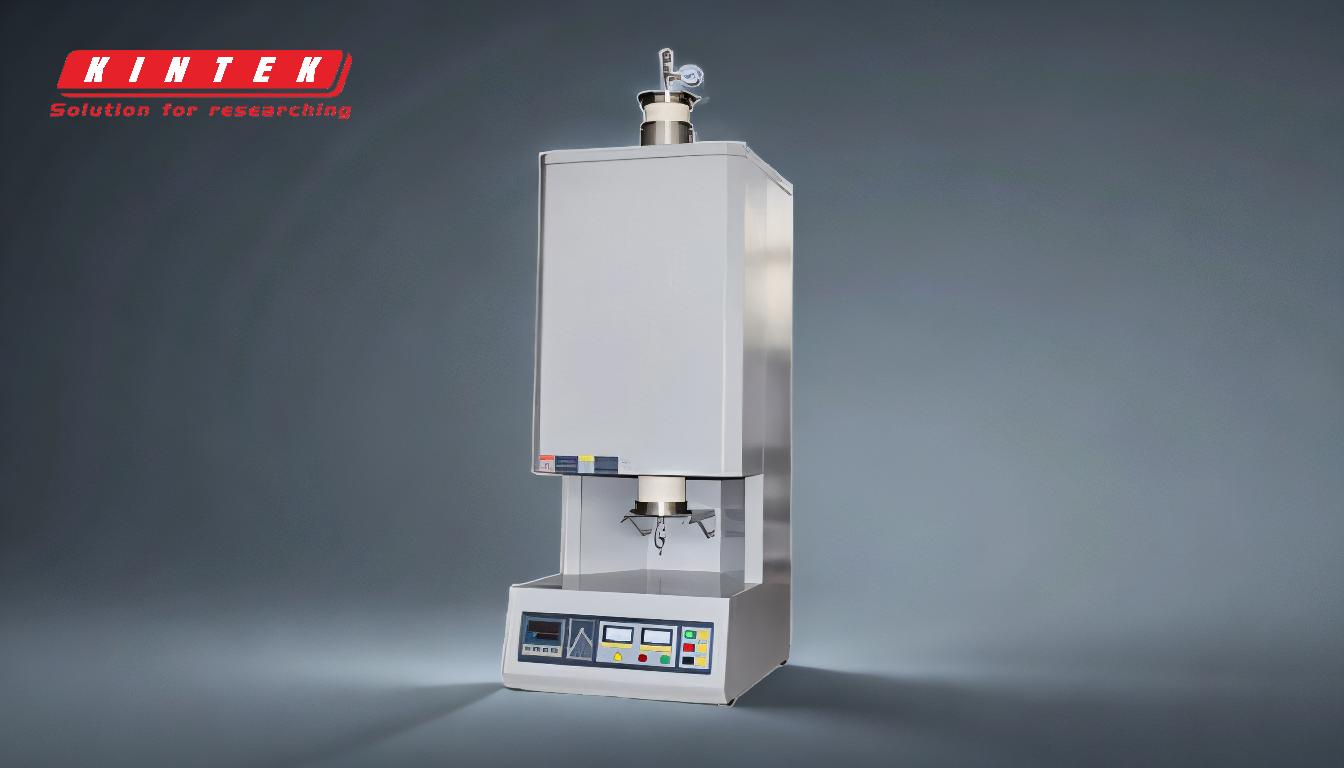
-
Alteración de propiedades mecánicas:
- Aumento del límite elástico: El recocido puede conducir a un aumento en el límite elástico, como se observa en el acero para tuberías X80, donde aumenta aproximadamente un 10%. Esto puede parecer beneficioso, pero también puede hacer que el material sea más quebradizo.
- Reducción del alargamiento: El alargamiento del material disminuye aproximadamente un 20%, lo que indica una pérdida de ductilidad. Esta reducción puede ser perjudicial en aplicaciones que requieren flexibilidad del material.
-
Formación de la atmósfera Cottrell:
- Difusión de átomos de carbono: Durante el recocido, los átomos de carbono se difunden hacia los sitios intersticiales de las dislocaciones. Este proceso forma lo que se conoce como atmósfera de Cottrell.
- Fijación de dislocaciones: La atmósfera de Cottrell fija las dislocaciones en su lugar, lo que reduce la densidad de las dislocaciones móviles. Este efecto de fijación es responsable de los cambios observados en las propiedades mecánicas.
-
Impacto en el rendimiento del material:
- Ductilidad reducida: La disminución del alargamiento significa una reducción en la capacidad del material para deformarse plásticamente antes de fracturarse, lo que puede ser una desventaja crítica en muchas aplicaciones de ingeniería.
- Potencial fragilidad: Si bien en algunos contextos puede ser deseable un mayor límite elástico, a menudo esto tiene el costo de una mayor fragilidad, lo que hace que el material sea más propenso a agrietarse bajo tensión.
-
Consideraciones para la aplicación:
- Requisitos específicos de la aplicación: Las desventajas del recocido deben sopesarse con los requisitos específicos de la aplicación. Por ejemplo, en aplicaciones donde la ductilidad es crucial, la reducción del alargamiento podría ser inaceptable.
- Optimización de los parámetros de recocido: Para mitigar estas desventajas, es esencial optimizar los parámetros de recocido como la temperatura y la duración. Esta optimización puede ayudar a lograr un equilibrio entre propiedades mecánicas mejoradas y efectos adversos mínimos.
En resumen, si bien el recocido puede mejorar ciertas propiedades del material, también presenta desventajas importantes, particularmente en lo que respecta al rendimiento mecánico. Comprender estos inconvenientes es crucial para tomar decisiones informadas en el procesamiento y aplicación de materiales.
Tabla resumen:
Desventaja | Descripción |
---|---|
Mayor límite elástico | El límite elástico aumenta aproximadamente un 10%, pero puede provocar fragilidad. |
Alargamiento reducido | El alargamiento disminuye ~20%, lo que reduce la ductilidad y la flexibilidad. |
Atmósfera Cottrell | Los átomos de carbono fijan las dislocaciones, reduciendo las dislocaciones móviles y alterando las propiedades. |
Potencial fragilidad | Un mayor límite elástico puede hacer que los materiales sean propensos a agrietarse bajo tensión. |
Limitaciones de la aplicación | La ductilidad reducida puede ser inadecuada para aplicaciones que requieren flexibilidad del material. |
¿Necesita ayuda para optimizar los procesos de recocido de sus materiales? Póngase en contacto con nuestros expertos hoy ¡Para soluciones personalizadas!