El proceso de recocido, aunque muy utilizado en metalurgia y ciencia de materiales para mejorar las propiedades de metales y aleaciones, tiene varias limitaciones. Entre ellas se encuentran las restricciones relacionadas con el control de la temperatura, los requisitos de tiempo, los retos específicos de los materiales, el consumo de energía y el potencial de oxidación de la superficie. Además, es posible que el proceso no siempre consiga las propiedades deseadas del material debido a complejidades microestructurales o a una selección inadecuada de los parámetros. Comprender estas limitaciones es crucial para optimizar el proceso de recocido y garantizar los resultados deseados para aplicaciones específicas.
Explicación de los puntos clave:
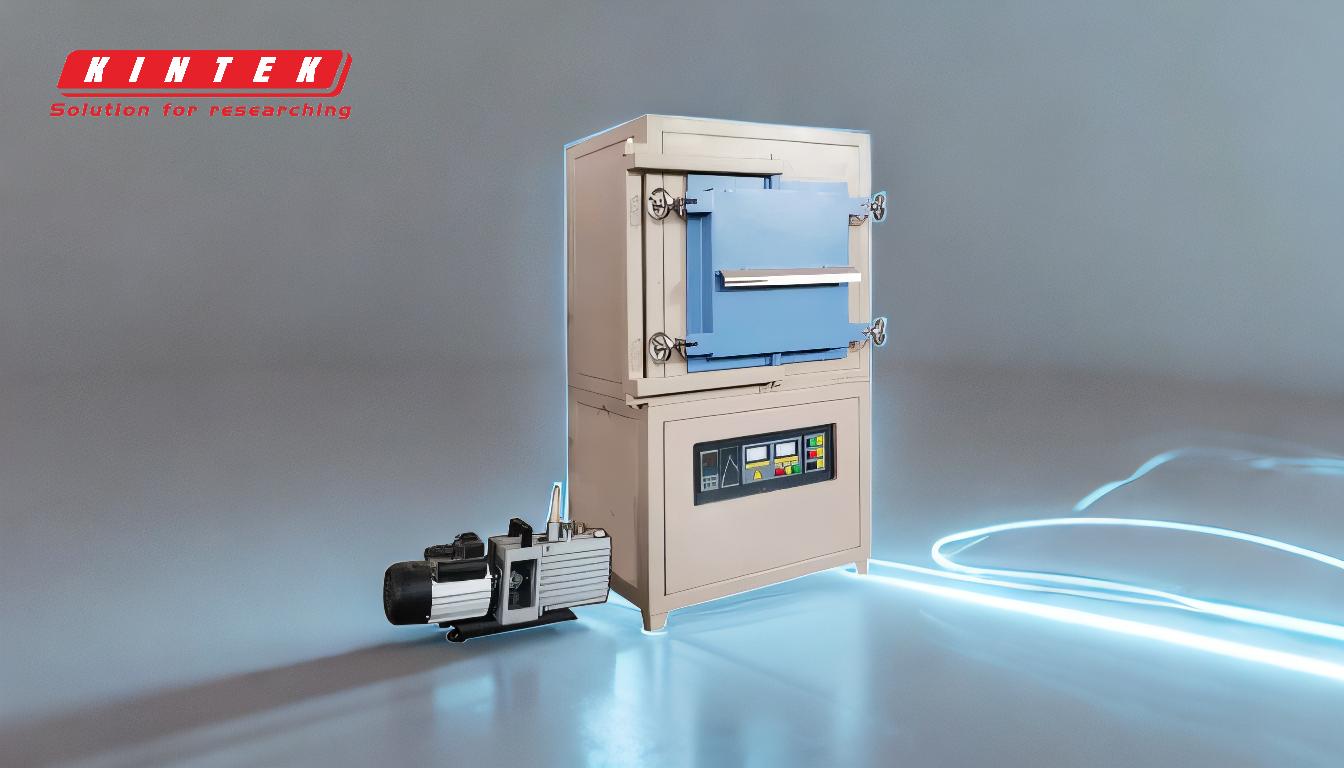
-
Desafíos del control de la temperatura:
- Requisitos de precisión: El recocido requiere un control preciso de la temperatura para conseguir las propiedades deseadas del material. Ligeras desviaciones pueden provocar una recristalización incompleta o problemas de crecimiento de grano.
- Limitaciones del equipo: No todos los hornos pueden mantener temperaturas uniformes en piezas grandes o complejas, lo que da lugar a resultados desiguales.
- Sensibilidad del material: Algunos materiales, como los aceros con alto contenido en carbono o determinadas aleaciones, tienen rangos de temperatura estrechos para un recocido eficaz, lo que hace que el proceso sea más difícil.
-
Limitaciones temporales:
- Largos plazos de tramitación: El recocido suele requerir ciclos prolongados de calentamiento y enfriamiento, lo que puede llevar mucho tiempo y resultar ineficaz para la producción de grandes volúmenes.
- Sensibilidad a la tasa de enfriamiento: En algunos materiales son necesarias velocidades de enfriamiento lentas para evitar tensiones internas, pero esto puede alargar aún más los tiempos de procesamiento.
-
Limitaciones específicas de los materiales:
- Microestructuras no uniformes: Los materiales con composiciones heterogéneas o historiales de procesado previos pueden no responder uniformemente al recocido.
- Problemas de crecimiento de los cereales: El recocido excesivo puede provocar un crecimiento excesivo del grano, reduciendo la resistencia y la tenacidad del material.
- Aplicabilidad limitada: Algunos materiales, como los compuestos no metálicos o la cerámica, no se benefician significativamente del recocido.
-
Consumo de energía:
- Grandes necesidades energéticas: Mantener altas temperaturas durante periodos prolongados consume mucha energía, lo que hace que el proceso sea costoso y menos respetuoso con el medio ambiente.
- Ineficiencia en el tratamiento por lotes: El recocido por lotes, aunque habitual, es menos eficiente desde el punto de vista energético que los procesos de recocido continuos.
-
Oxidación superficial y descarburación:
- Riesgos de oxidación: La exposición a altas temperaturas en presencia de oxígeno puede provocar la oxidación de la superficie, degradando la calidad del material.
- Descarburización: En los aceros, el calentamiento prolongado puede provocar la pérdida de carbono de la superficie, reduciendo la dureza y la resistencia al desgaste.
-
Complejidad del proceso y requisitos de cualificación:
- Optimización de parámetros: La selección de la temperatura de recocido, el tiempo y la velocidad de enfriamiento correctos requiere experiencia y experimentación.
- Tratamientos posteriores al recocido: Pueden ser necesarios procesos adicionales, como el temple o el revenido, para conseguir las propiedades deseadas, lo que añade complejidad.
-
Limitaciones económicas y prácticas:
- Coste del equipo: Los hornos de recocido y los sistemas de control de temperatura de alta calidad pueden ser caros de adquirir y mantener.
- Espacio necesario: Las operaciones de recocido a gran escala requieren un espacio considerable, que puede no ser viable para instalaciones más pequeñas.
-
Resultados incoherentes:
- Variabilidad en la respuesta del material: Incluso con parámetros controlados, las variaciones en la composición del material o el procesamiento previo pueden dar lugar a resultados incoherentes.
- Error humano: El control manual de los procesos de recocido aumenta el riesgo de errores, como el ajuste incorrecto de la temperatura o de los tiempos.
-
Mejora limitada de determinados inmuebles:
- Compromisos entre dureza y resistencia: El recocido suele reducir la dureza y la resistencia para mejorar la ductilidad, lo que puede no ser deseable para todas las aplicaciones.
- Impacto limitado en los defectos: Aunque el recocido puede reducir las tensiones internas, es posible que no elimine todos los defectos, como huecos o inclusiones.
-
Medio ambiente y seguridad:
- Calor y emisiones: Los procesos a alta temperatura generan calor y emisiones, por lo que requieren una ventilación adecuada y medidas de seguridad.
- Seguridad de los trabajadores: La manipulación de materiales calientes y el manejo de equipos de alta temperatura entrañan riesgos para la seguridad.
Al comprender estas limitaciones, los fabricantes e ingenieros pueden diseñar mejor los procesos de recocido, seleccionar los materiales adecuados y aplicar tratamientos complementarios para lograr resultados óptimos.
Cuadro recapitulativo:
Categoría de limitación | Principales retos |
---|---|
Control de la temperatura | Requisitos de precisión, limitaciones del equipo, sensibilidad del material |
Limitaciones temporales | Largos tiempos de procesamiento, sensibilidad a la velocidad de enfriamiento |
Cuestiones específicas de los materiales | Microestructuras no uniformes, crecimiento del grano, aplicabilidad limitada |
Consumo de energía | Elevados requisitos energéticos, ineficacia en el procesamiento por lotes |
Oxidación superficial | Riesgos de oxidación, descarburación en aceros |
Complejidad del proceso | Optimización de parámetros, tratamientos posteriores al recocido |
Limitaciones económicas | Coste de los equipos, espacio necesario |
Resultados incoherentes | Variabilidad en la respuesta del material, error humano |
Mejora limitada de la propiedad | Compromisos entre dureza y resistencia, eliminación limitada de defectos |
Preocupaciones medioambientales | Calor y emisiones, riesgos para la seguridad de los trabajadores |
¿Necesita ayuda para optimizar su proceso de recocido? Contacte hoy mismo con nuestros expertos soluciones a medida