La sinterización en pulvimetalurgia es un proceso térmico crítico que transforma los polvos metálicos compactados en componentes sólidos de alta resistencia calentándolos justo por debajo de su punto de fusión.Este proceso consta de varias fases, como la selección de la aleación, el prensado, la sinterización y el acabado.La fase de sinterización, realizada en hornos de sinterización , es donde las partículas metálicas se unen por difusión, formando estructuras cristalinas.Se emplean distintos tipos de procesos de sinterización en función del material y las propiedades deseadas, siendo la sinterización en estado sólido la más común.La elección del horno, como los hornos continuos o de cinta, depende de los requisitos de temperatura y del rendimiento de la producción.
Explicación de los puntos clave:
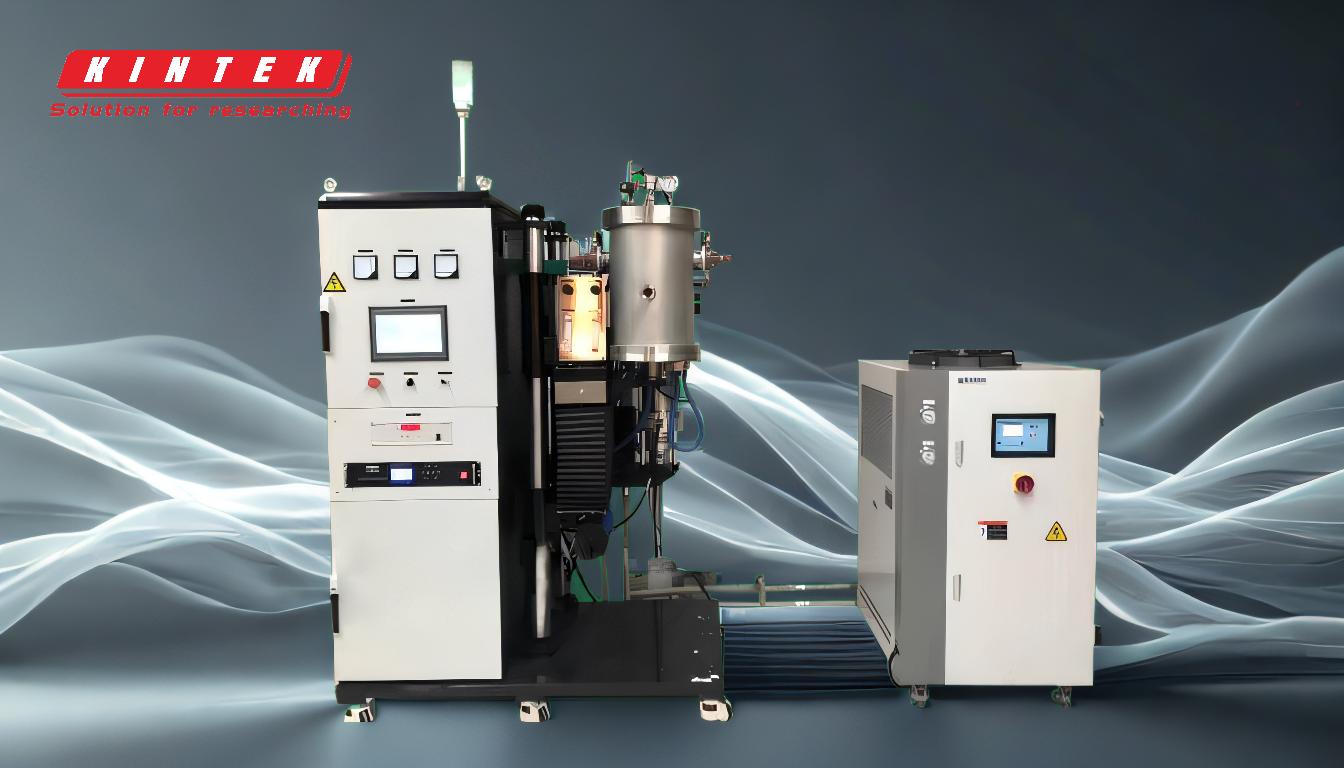
-
Sinterización en estado sólido:
- Es el proceso de sinterización más común en pulvimetalurgia.Consiste en calentar polvos metálicos compactados por debajo de su punto de fusión, lo que permite que las partículas se difundan y se adhieran sin licuarse.El resultado es un material denso y muy resistente con mejores propiedades mecánicas.
- El sinterizado en estado sólido es ideal para metales con puntos de fusión elevados, como el tungsteno o el molibdeno, en los que es crucial mantener la integridad estructural sin fundirse.
-
Sinterización en fase líquida:
- En este proceso, se añade a la mezcla de polvo metálico una pequeña cantidad de un material con un punto de fusión más bajo.Durante el calentamiento, este aditivo se funde, creando una fase líquida que facilita la unión y densificación de las partículas.
- La sinterización en fase líquida es especialmente útil para materiales como los carburos cementados, en los que la fase líquida mejora la unión y reduce la porosidad.
-
Sinterización asistida por presión:
- Este método combina calor con presión externa para acelerar el proceso de sinterización.La presión aplicada ayuda a conseguir densidades más altas y enlaces más fuertes entre las partículas.
- Técnicas como el prensado en caliente y el sinterizado por plasma de chispa (SPS) entran en esta categoría.Se utilizan para materiales avanzados como la cerámica y los compuestos, en los que son fundamentales una alta densidad y una porosidad mínima.
-
Sinterización reactiva:
- La sinterización reactiva implica reacciones químicas entre los componentes del polvo durante el proceso de calentamiento.Estas reacciones pueden conducir a la formación de nuevas fases o compuestos, mejorando las propiedades del material.
- Este método se utiliza a menudo para producir compuestos intermetálicos o cerámicas avanzadas, en las que la reacción química forma parte integrante de las características del producto final.
-
Sinterización por microondas:
- El sinterizado por microondas utiliza la energía de microondas para calentar los polvos metálicos de manera uniforme y rápida.Este método reduce el tiempo de sinterización y el consumo de energía, al tiempo que mejora las propiedades del material.
- Es especialmente eficaz para materiales difíciles de sinterizar con métodos convencionales, como ciertas cerámicas y nanomateriales.
-
Tipos de hornos de sinterización:
- Hornos continuos:Se utilizan ampliamente en entornos de producción por su alto rendimiento y su control constante de la temperatura.Son adecuados para la fabricación a gran escala de componentes como piezas de automoción.
- Hornos de cinta:Ideales para procesos a baja temperatura, los hornos de cinta no suelen utilizarse para la sinterización a alta temperatura, pero son eficaces para procesos como la soldadura fuerte o el recocido.
- Hornos discontinuos:Se utilizan para la producción a pequeña escala o para aplicaciones especializadas en las que se requiere un control preciso de la temperatura y flexibilidad.
-
Etapas del proceso de sinterización:
- Selección de aleaciones:La elección de los polvos metálicos y los aditivos determina las propiedades del producto final.
- Prensado:Los polvos se compactan en la forma deseada mediante prensas hidráulicas, moldes o matrices.
- Sinterización:La pieza compactada se calienta en un horno para unir las partículas y conseguir la integridad estructural.
- Acabado:Los tratamientos posteriores a la sinterización, como el calibrado o el acabado superficial, se aplican para cumplir las especificaciones finales.
Al comprender estos procesos de sinterización y el papel de los hornos de sinterización Los fabricantes pueden seleccionar el método y el equipo adecuados para conseguir las propiedades deseadas del material y la eficacia de la producción.
Tabla resumen:
Proceso de sinterización | Descripción | Aplicaciones |
---|---|---|
Sinterización en estado sólido | Calentamiento por debajo del punto de fusión; las partículas se adhieren sin licuarse. | Ideal para metales con un punto de fusión elevado, como el wolframio y el molibdeno. |
Sinterización en fase líquida | Añade un material con un punto de fusión más bajo para crear una fase líquida para la unión. | Se utiliza en carburos cementados para reducir la porosidad. |
Sinterización asistida por presión | Combina calor con presión externa para obtener mayor densidad y uniones más fuertes. | Materiales avanzados como cerámicas y compuestos. |
Sinterización reactiva | Las reacciones químicas durante el calentamiento forman nuevas fases o compuestos. | Compuestos intermetálicos y cerámicas avanzadas. |
Sinterización por microondas | Utiliza energía de microondas para un calentamiento rápido y uniforme y para mejorar las propiedades de los materiales. | Materiales difíciles de sinterizar, como cerámicas y nanomateriales. |
¿Necesita ayuda para seleccionar el proceso de sinterización adecuado para su aplicación? Póngase en contacto con nuestros expertos hoy mismo ¡!