El prensado isostático en caliente (HIP) de piezas fundidas es un proceso de fabricación que aplica alta temperatura y presión hidrostática uniforme a materiales, generalmente metales o cerámicas, para eliminar la porosidad interna, mejorar la densidad y mejorar las propiedades mecánicas. Este proceso es particularmente beneficioso para aplicaciones críticas donde la integridad y el rendimiento del material son primordiales. HIP se utiliza ampliamente en industrias como la aeroespacial, automotriz y de dispositivos médicos para producir componentes de alta calidad con resistencia, durabilidad y confiabilidad superiores.
Puntos clave explicados:
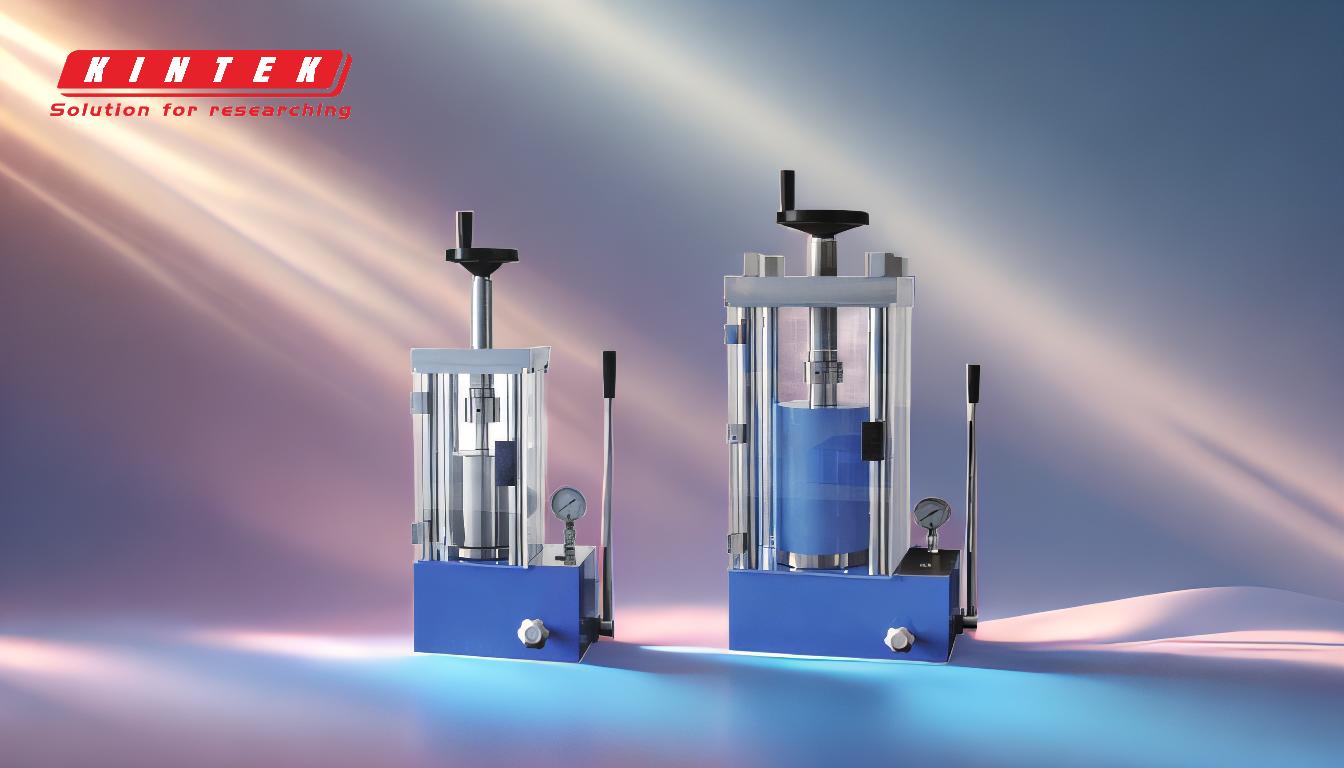
-
¿Qué es el prensado isostático en caliente (HIP)?
- HIP es un proceso que combina alta temperatura (normalmente 900–2000 °C) y presión hidrostática uniforme (100–200 MPa) para densificar materiales y eliminar defectos internos como porosidad y microfisuras.
- El proceso utiliza un gas, como el argón, como medio de presión para garantizar una aplicación de presión uniforme desde todas las direcciones.
- Se aplica comúnmente a piezas de fundición, componentes de pulvimetalurgia y piezas de fabricación aditiva para mejorar su integridad estructural y su rendimiento.
-
¿Cómo funciona HIP?
- El material o componente se coloca en un recipiente sellado o molde flexible, que luego se somete a alta temperatura y presión en un prensa isostática caliente .
- La presión se transmite uniformemente a través del medio gaseoso, asegurando una compactación igual en todas las direcciones.
- Este proceso permite el cierre de huecos internos y la formación de enlaces metalúrgicos, dando como resultado un material más denso y homogéneo.
-
Beneficios de HIP para piezas fundidas
- Eliminación de Porosidad: HIP elimina eficazmente la porosidad interna y las microfisuras, que son defectos comunes en las piezas fundidas. Esto conduce a propiedades mecánicas mejoradas como resistencia, resistencia a la fatiga y ductilidad.
- Densidad mejorada: El proceso aumenta la densidad del material, haciéndolo más adecuado para aplicaciones de alto estrés.
- Propiedades mecánicas mejoradas: HIP mejora la tenacidad, la resistencia al desgaste y la estabilidad térmica, extendiendo la vida útil de los componentes.
- Diseños livianos: Al mejorar las propiedades del material, HIP permite el diseño de componentes más ligeros sin comprometer el rendimiento.
- Reducción de desperdicios y pérdidas: La capacidad de reparar defectos en las piezas fundidas reduce el desperdicio y mejora la eficiencia de la producción.
-
Aplicaciones de HIP en la industria
- Aeroespacial: HIP se utiliza para producir componentes de alto rendimiento como álabes de turbinas, piezas de motores y componentes estructurales que requieren resistencia y confiabilidad excepcionales.
- Dispositivos Médicos: El proceso se emplea para fabricar implantes y prótesis con biocompatibilidad y propiedades mecánicas superiores.
- Automotor: HIP se utiliza para componentes críticos como piezas de motor, sistemas de transmisión y elementos estructurales livianos.
- Energía: La tecnología se aplica en la producción de componentes para reactores nucleares, turbinas de gas y sistemas de energía renovable.
-
Comparación con otros procesos
- A diferencia del prensado unidireccional o la sinterización, HIP garantiza una compactación uniforme en todas las direcciones, lo que da como resultado un material más homogéneo.
- HIP elimina la necesidad de lubricantes y reduce las limitaciones geométricas, lo que lo hace ideal para formas complejas y materiales difíciles de compactar.
- El proceso es particularmente ventajoso para materiales costosos como superaleaciones, titanio y acero inoxidable, donde la utilización y el rendimiento del material son críticos.
-
Ventajas sobre los métodos tradicionales
- Aplicación de presión uniforme: HIP aplica presión uniformemente en todas las direcciones, asegurando propiedades consistentes del material en todo el componente.
- No se requieren lubricantes: El proceso elimina la necesidad de lubricantes, lo que reduce la contaminación y simplifica el posprocesamiento.
- Densidad alta y uniforme: HIP logra una densidad alta y uniforme, que es difícil de lograr con los métodos de prensado tradicionales.
- Reparación de Defectos: El proceso puede reparar defectos internos en las piezas fundidas, reducir las tasas de desperdicio y mejorar la eficiencia de la producción.
-
Desafíos y consideraciones
- Costo: El equipo y el procesamiento HIP pueden ser costosos, lo que los hace más adecuados para aplicaciones de alto valor.
- Tiempo de ciclo: El proceso requiere un tiempo considerable para calentar, presurizar y enfriar, lo que puede afectar los programas de producción.
- Compatibilidad de materiales: No todos los materiales son adecuados para HIP y se requiere una selección cuidadosa para evitar efectos adversos.
En conclusión, el prensado isostático en caliente es una tecnología transformadora para mejorar la calidad y el rendimiento de las piezas fundidas. Al eliminar defectos internos, mejorar la densidad y mejorar las propiedades mecánicas, HIP permite la producción de componentes de alto rendimiento para aplicaciones exigentes. A pesar de sus desafíos, los beneficios de HIP lo convierten en un proceso indispensable en industrias donde la integridad y confiabilidad del material son críticas.
Tabla resumen:
Aspecto | Detalles |
---|---|
Proceso | Combina alta temperatura (900–2000°C) y presión hidrostática uniforme (100–200 MPa). |
Beneficios clave | Elimina la porosidad, potencia la densidad, mejora las propiedades mecánicas. |
Aplicaciones | Aeroespacial, dispositivos médicos, automoción, energía. |
Ventajas sobre los métodos tradicionales | Presión uniforme, sin lubricantes, alta densidad, reparación de defectos. |
Desafíos | Alto costo, largo tiempo de ciclo, compatibilidad de materiales. |
Descubra cómo HIP puede optimizar su proceso de fabricación: póngase en contacto con nuestros expertos hoy !