El sinterizado selectivo por láser (SLS) y la fusión por haz de electrones (EBM) son tecnologías de fabricación aditiva (impresión 3D), pero difieren significativamente en sus procesos, materiales y aplicaciones.El SLS utiliza un láser de alta potencia para sinterizar material en polvo, normalmente polímeros o metales, capa por capa para crear un objeto 3D.La EBM, por su parte, utiliza un haz de electrones para fundir polvo metálico en un entorno de vacío, lo que la hace adecuada para aplicaciones de alta resistencia y alta temperatura.Mientras que el SLS es versátil y funciona con diversos materiales, el EBM está más especializado en piezas metálicas, sobre todo en las industrias aeroespacial y médica.Ambas tecnologías eliminan la necesidad de moldes, pero la EBM ofrece mayor precisión y mejores propiedades mecánicas para los componentes metálicos.
Explicación de los puntos clave:
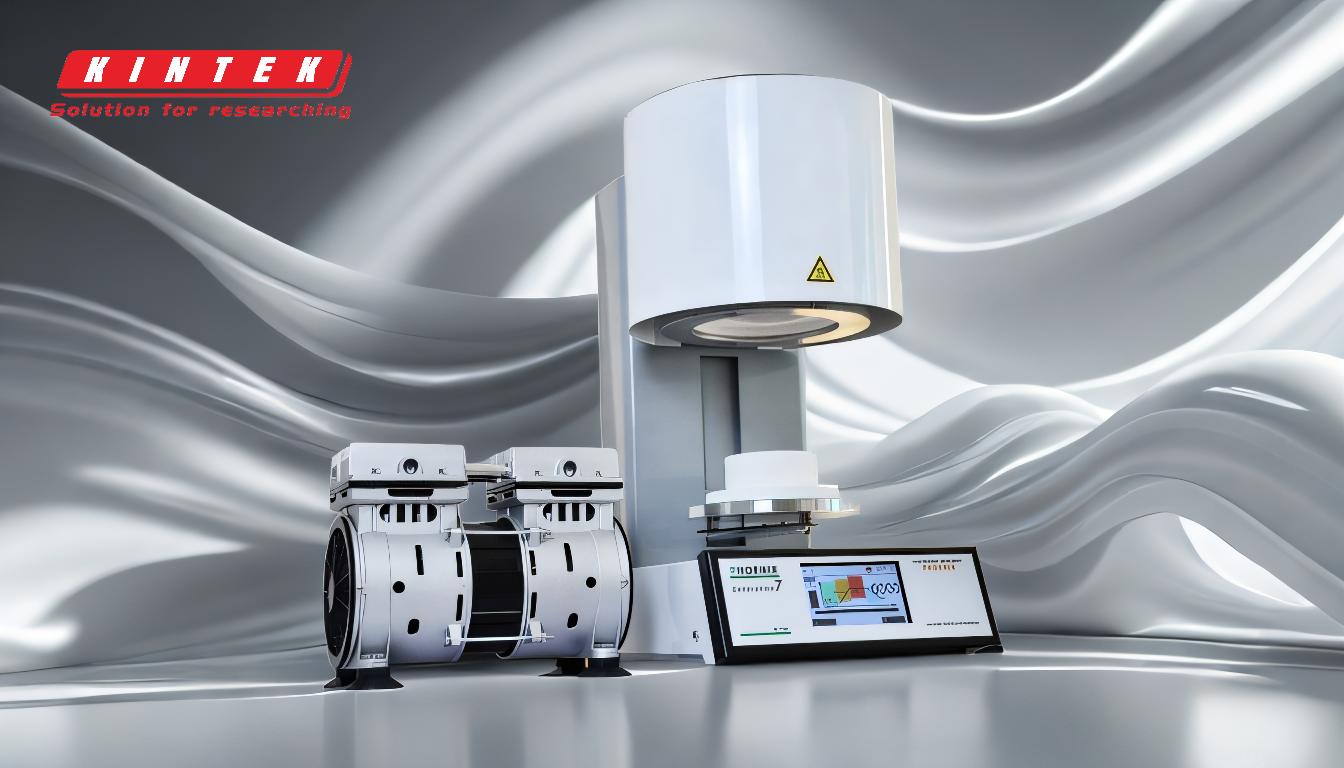
-
Mecanismo del proceso:
- Sinterización selectiva por láser (SLS):Utiliza un láser de alta potencia para sinterizar (fusionar) selectivamente material en polvo, capa por capa, para construir un objeto 3D.El láser calienta el polvo lo suficiente para unir las partículas sin fundirlas del todo.
- Fusión por haz de electrones (EBM):Utiliza un haz de electrones de alta energía para fundir completamente el polvo metálico en una cámara de vacío.El haz de electrones explora el lecho de polvo, fundiendo el material capa por capa para crear una pieza densa y de alta resistencia.
-
Materiales utilizados:
- SLS:Trabaja principalmente con polímeros (por ejemplo, nailon, poliamida) y algunos polvos metálicos.Es versátil y puede trabajar con una amplia gama de materiales, incluidos los compuestos.
- EBM:Exclusivo para polvos metálicos, como titanio, cromo-cobalto y aleaciones a base de níquel.Es ideal para producir piezas de alta resistencia y resistentes a altas temperaturas.
-
Condiciones ambientales:
- SLS:Funciona en una atmósfera controlada, normalmente nitrógeno o argón, para evitar la oxidación del material.No requiere vacío.
- EBM:Requiere un entorno de alto vacío para evitar la contaminación y garantizar el funcionamiento eficaz del haz de electrones.Esto hace que el proceso sea más complejo y costoso.
-
Precisión y acabado superficial:
- SLS:Produce piezas con un buen acabado superficial y una precisión moderada.Sin embargo, la superficie puede requerir un tratamiento posterior (por ejemplo, lijado o revestimiento) para obtener acabados más lisos.
- EBM:Ofrece mayor precisión y mejores propiedades mecánicas gracias a la fusión completa del polvo metálico.Las piezas tienen un acabado superficial más rugoso en comparación con el SLS, pero son más resistentes y duraderas.
-
Aplicaciones:
- SLS:Adecuado para prototipos, piezas funcionales y producción de bajo volumen.Se utiliza habitualmente en las industrias de automoción, aeroespacial y de bienes de consumo.
- EBM:Ideal para aplicaciones de alto rendimiento, como componentes aeroespaciales, implantes médicos y álabes de turbina, donde la solidez y la resistencia térmica son fundamentales.
-
Coste y velocidad de producción:
- SLS:Generalmente más rápido y rentable para la creación de prototipos y la producción de lotes pequeños.No requiere moldes, lo que reduce los costes iniciales.
- EBM:Más caro debido al entorno de vacío y al equipo especializado.Es más lento pero produce piezas con propiedades mecánicas superiores, lo que justifica el mayor coste para aplicaciones críticas.
-
Requisitos de postprocesado:
- SLS:Las piezas pueden requerir un tratamiento posterior mínimo, como la eliminación de soportes o el acabado de la superficie.Sin embargo, el proceso es relativamente sencillo.
- EBM:Las piezas suelen requerir tratamiento térmico o mecanizado para conseguir las propiedades mecánicas y el acabado superficial deseados.El entorno de vacío también añade complejidad al postprocesado.
Al comprender estas diferencias clave, los compradores de equipos y consumibles pueden tomar decisiones informadas basadas en los requisitos específicos de sus proyectos, como las propiedades de los materiales, la precisión y las necesidades de la aplicación.
Cuadro sinóptico:
Aspecto | Sinterización selectiva por láser (SLS) | Fusión por haz de electrones (EBM) |
---|---|---|
Mecanismo de proceso | Utiliza un láser de alta potencia para sinterizar el material en polvo capa por capa. | Utiliza un haz de electrones para fundir completamente el polvo metálico en el vacío. |
Materiales utilizados | Polímeros (por ejemplo, nailon, poliamida) y algunos polvos metálicos. | Exclusivo para polvos metálicos (por ejemplo, titanio, cromo-cobalto, aleaciones a base de níquel). |
Condiciones ambientales | Funciona en atmósfera controlada (nitrógeno/argón). | Requiere un entorno de alto vacío. |
Precisión y acabado superficial | Buen acabado superficial, precisión moderada.Puede requerir tratamiento posterior. | Mayor precisión, piezas más resistentes.Acabado superficial más rugoso pero propiedades mecánicas superiores. |
Aplicaciones | Prototipos, piezas funcionales, producción de bajo volumen (automoción, aeroespacial, bienes de consumo). | Aplicaciones de alto rendimiento (aeroespacial, implantes médicos, álabes de turbina). |
Coste y velocidad de producción | Más rápido y rentable para la creación de prototipos y la producción de lotes pequeños. | Más caro y lento, pero ideal para aplicaciones críticas. |
Postprocesado | Mínimo (eliminación de soportes, acabado superficial). | A menudo requiere tratamiento térmico o mecanizado debido al entorno de vacío. |
¿Necesita ayuda para elegir la tecnología de impresión 3D adecuada para su proyecto? Póngase en contacto con nuestros expertos hoy mismo.