El tratamiento térmico de metales es un proceso controlado que se utiliza para alterar las propiedades físicas y mecánicas de los metales, como la dureza, la ductilidad, la tenacidad y la resistencia. Esto se consigue mediante una serie de pasos que implican calentar, mantener a una temperatura específica y enfriar el metal de forma controlada. El proceso puede incluir métodos como el recocido, el temple, el revenido, la cementación en caja, etc., cada uno de ellos adaptado para conseguir características específicas del material. El tratamiento térmico se utiliza ampliamente en la fabricación para mejorar la durabilidad, versatilidad y rendimiento de los metales para diversas aplicaciones.
Explicación de los puntos clave:
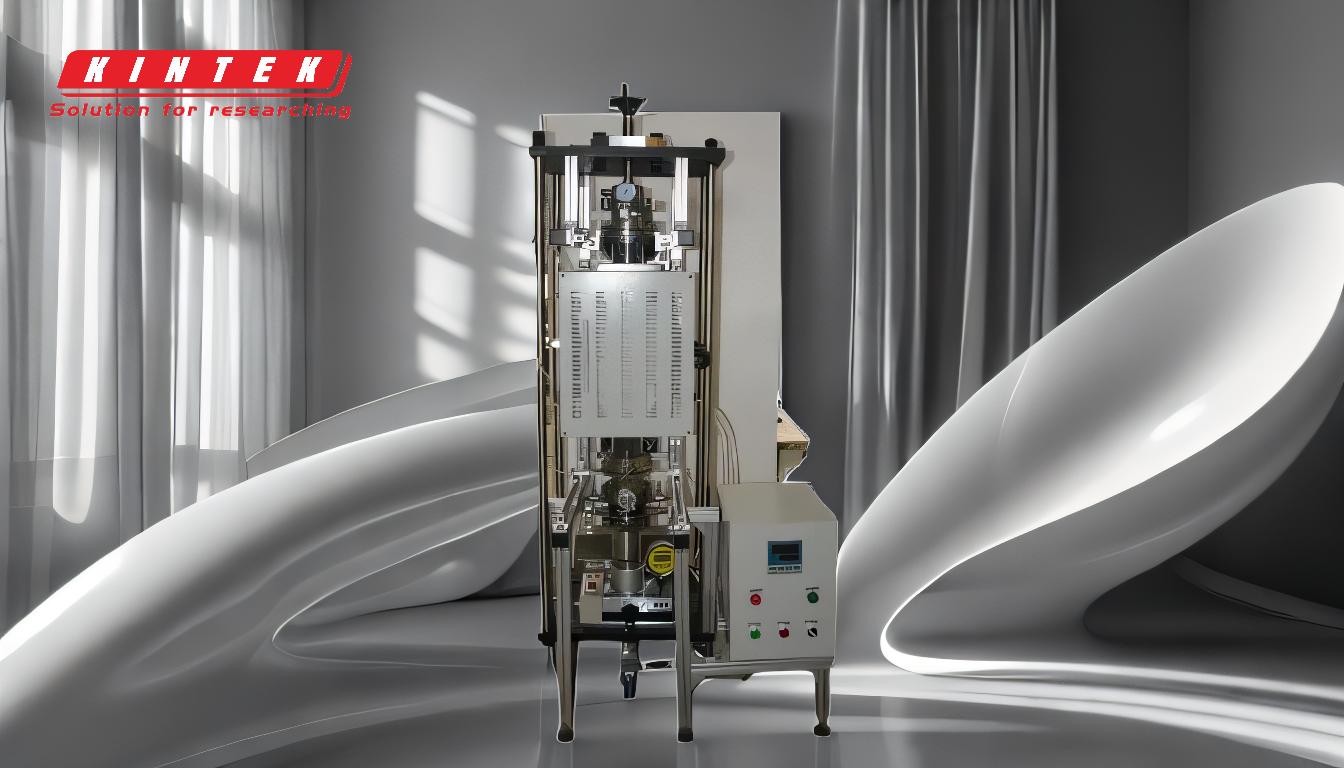
-
Definición de tratamiento térmico:
- El tratamiento térmico es un proceso que consiste en calentar metales a una temperatura específica, mantenerlos a esa temperatura durante un periodo determinado y, a continuación, enfriarlos de forma controlada. Este proceso modifica la microestructura del metal, lo que provoca cambios en sus propiedades físicas y mecánicas.
-
Finalidad del tratamiento térmico:
-
El objetivo principal del tratamiento térmico es mejorar las propiedades de los metales, como:
- Dureza: Aumento de la resistencia a la deformación.
- Ductilidad: Aumento de la capacidad de deformarse sin romperse.
- Dureza: Mejora de la resistencia a la fractura bajo tensión.
- Fuerza: Aumento de la capacidad de carga.
- Dureza de la superficie: Aumento de la resistencia al desgaste de la superficie.
-
El objetivo principal del tratamiento térmico es mejorar las propiedades de los metales, como:
-
Pasos básicos del tratamiento térmico:
- Calefacción: El metal se calienta a una temperatura específica, que puede alcanzar los 2.400 °F en función del material y del resultado deseado.
- Sujeción: El metal se mantiene a la temperatura especificada durante un periodo determinado, que puede variar de unos segundos a varias horas.
- Refrigeración: El metal se enfría según los métodos prescritos, que pueden incluir el enfriamiento por aire, el temple en aceite o el temple en agua. La velocidad de enfriamiento es fundamental para determinar las propiedades finales del metal.
-
Procesos habituales de tratamiento térmico:
- Recocido: Este proceso consiste en calentar el metal a una temperatura específica y luego enfriarlo lentamente para ablandar el material, mejorar la ductilidad y aliviar las tensiones internas.
- Enfriamiento: El metal se enfría rápidamente (a menudo en agua, aceite o aire) para aumentar su dureza y resistencia. Sin embargo, esto puede hacer que el metal se vuelva quebradizo, por lo que suele ir seguido de un revenido.
- Templado: Tras el temple, el metal se recalienta a una temperatura inferior y luego se enfría para reducir la fragilidad y mejorar la tenacidad.
- Cementación: Este proceso endurece la superficie del metal manteniendo el núcleo blando y dúctil. Las técnicas incluyen el carburizado, la nitruración y el endurecimiento por inducción.
- Endurecimiento por precipitación: Consiste en calentar el metal a una temperatura determinada para formar precipitados que aumentan la resistencia y la dureza.
- Normalización: Similar al recocido, pero el metal se enfría en aire para refinar la estructura del grano y mejorar las propiedades mecánicas.
-
Aplicaciones del tratamiento térmico:
-
El tratamiento térmico se utiliza ampliamente en diversas industrias para mejorar el rendimiento y la longevidad de los componentes metálicos. Por ejemplo:
- Industria del automóvil: Para aumentar la solidez y la resistencia al desgaste de las piezas del motor, los engranajes y los ejes.
- Industria aeroespacial: Para mejorar la tenacidad y la resistencia a la fatiga de los componentes aeronáuticos.
- Fabricación de herramientas: Para aumentar la dureza y la durabilidad de las herramientas de corte y las matrices.
- Construcción: Para reforzar los componentes estructurales de acero.
-
El tratamiento térmico se utiliza ampliamente en diversas industrias para mejorar el rendimiento y la longevidad de los componentes metálicos. Por ejemplo:
-
Factores que influyen en el tratamiento térmico:
- Temperatura: La temperatura a la que se calienta el metal es crítica y varía en función del tipo de metal y de las propiedades deseadas.
- Tiempo: La duración del mantenimiento del metal a la temperatura especificada afecta a la magnitud de los cambios microestructurales.
- Tasa de enfriamiento: La velocidad de enfriamiento del metal determina sus propiedades finales. El enfriamiento rápido (temple) aumenta la dureza, mientras que el enfriamiento lento (recocido) aumenta la ductilidad.
-
Ventajas del tratamiento térmico:
- Propiedades mejoradas de los materiales: El tratamiento térmico puede mejorar significativamente las propiedades mecánicas de los metales, haciéndolos más adecuados para aplicaciones específicas.
- Versatilidad: Pueden aplicarse diferentes procesos de tratamiento térmico para conseguir una amplia gama de propiedades, desde blandas y dúctiles hasta duras y resistentes al desgaste.
- Relación coste-eficacia: Al mejorar las propiedades de los metales existentes, el tratamiento térmico puede reducir la necesidad de utilizar materiales más caros o procesos de fabricación complejos.
-
Retos y consideraciones:
- Precisión: El tratamiento térmico requiere un control preciso de la temperatura, el tiempo y la velocidad de enfriamiento para conseguir las propiedades deseadas.
- Distorsión: El enfriamiento rápido puede provocar alabeos o deformaciones en el metal, que pueden requerir mecanizados adicionales o procesos correctivos.
- Selección de materiales: No todos los metales responden de la misma manera al tratamiento térmico. La composición y la microestructura inicial del metal desempeñan un papel importante a la hora de determinar la eficacia del proceso.
En resumen, el tratamiento térmico es un proceso fundamental de la metalurgia que permite personalizar las propiedades de los metales para satisfacer requisitos de aplicación específicos. Controlando cuidadosamente los procesos de calentamiento, mantenimiento y enfriamiento, los fabricantes pueden producir metales con mayor resistencia, durabilidad y rendimiento, lo que convierte al tratamiento térmico en una parte indispensable de la fabricación moderna.
Cuadro recapitulativo:
Aspecto | Detalles |
---|---|
Propósito | Mejorar la dureza, la ductilidad, la tenacidad, la resistencia y la dureza superficial. |
Procesos clave | Recocido, temple, revenido, cementación, endurecimiento por precipitación. |
Aplicaciones | Industria automovilística, aeroespacial, fabricación de herramientas y construcción. |
Beneficios | Propiedades del material, versatilidad y rentabilidad mejoradas. |
Desafíos | Control de precisión, distorsión y respuestas específicas del material. |
Descubra cómo el tratamiento térmico puede optimizar sus componentes metálicos- contacte hoy mismo con nuestros expertos ¡!