Los recubrimientos de carbono tipo diamante (DLC) son conocidos por sus excepcionales propiedades, como su gran dureza, baja fricción y resistencia química.Sin embargo, su rendimiento a altas temperaturas es una consideración crítica para las aplicaciones que implican estrés térmico.La estabilidad a altas temperaturas de los recubrimientos de DLC depende de factores como la estructura de enlace (sp3 frente a sp2), el contenido de hidrógeno y el método de deposición.Por lo general, los revestimientos de DLC pueden soportar temperaturas de hasta 300-400°C antes de sufrir una degradación significativa, como la grafitización o la pérdida de hidrógeno.Para aplicaciones a temperaturas más elevadas, pueden ser necesarias variantes especializadas de DLC o revestimientos alternativos.
Explicación de los puntos clave:
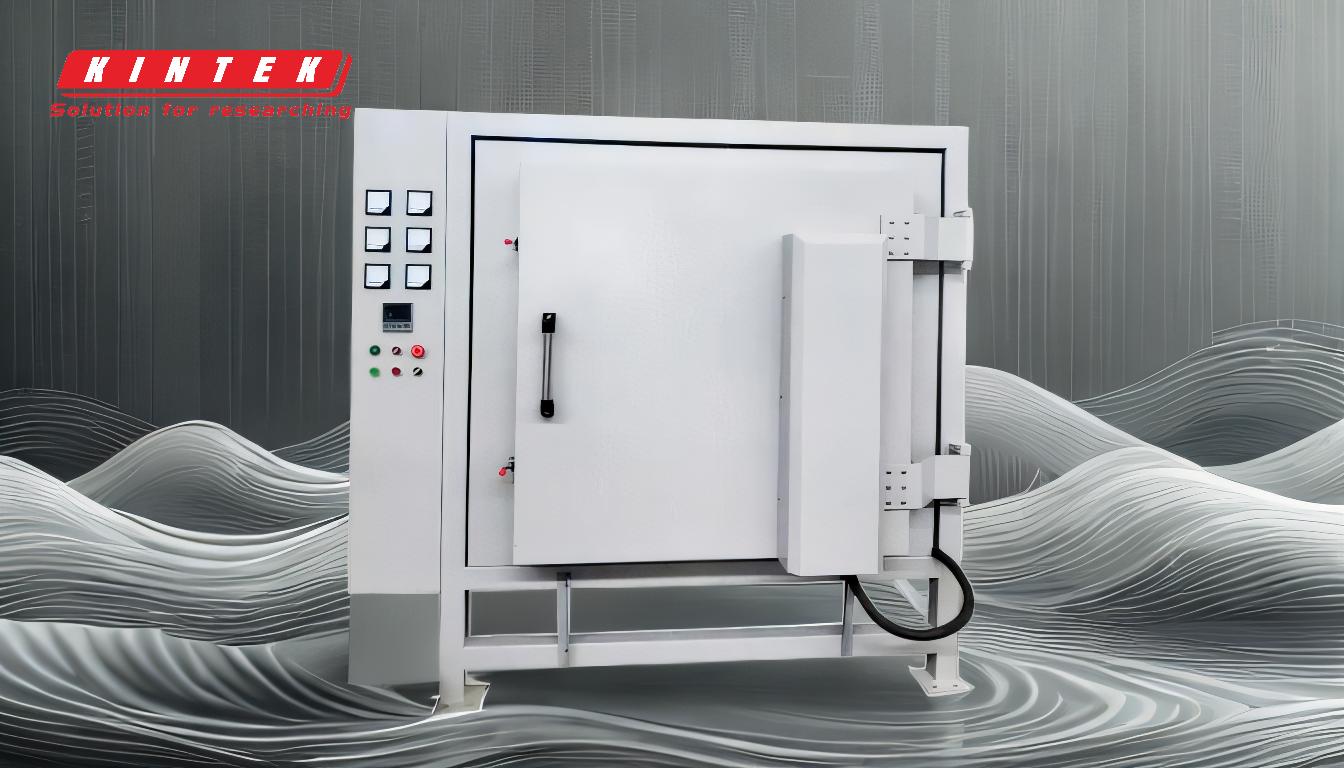
-
Composición y estructura de unión del revestimiento DLC:
- Los recubrimientos DLC están formados por una mezcla de enlaces de carbono sp3 (tipo diamante) y sp2 (tipo grafito).
- Los enlaces sp3 contribuyen a una gran dureza y resistencia al desgaste, mientras que los enlaces sp2 influyen en la fricción y la estabilidad térmica.
- El DLC hidrogenado (a-C:H) contiene hidrógeno, lo que afecta a sus propiedades térmicas.
-
Límites de temperatura de los revestimientos de DLC:
- Los recubrimientos DLC estándar suelen degradarse a temperaturas entre 300°C y 400°C .
- A temperaturas más elevadas, los enlaces sp3 se convierten en enlaces sp2 (grafitización), lo que reduce la dureza y la resistencia al desgaste.
- Los recubrimientos de DLC hidrogenados pueden perder hidrógeno a temperaturas elevadas, lo que compromete aún más sus propiedades.
-
Factores que influyen en el rendimiento a altas temperaturas:
- Contenido de hidrógeno:El DLC hidrogenado (a-C:H) es menos estable térmicamente que el DLC sin hidrógeno (ta-C).
- Método de deposición:Técnicas como la PACVD (deposición química de vapor asistida por plasma) pueden influir en la estabilidad térmica del revestimiento.
- Material del sustrato:El desajuste de dilatación térmica entre el revestimiento y el sustrato puede afectar al rendimiento a altas temperaturas.
-
Aplicaciones y limitaciones:
- Los recubrimientos de DLC son ideales para aplicaciones por debajo de 300 °C, como componentes de automoción, herramientas de corte y dispositivos biomédicos.
- Para entornos de alta temperatura (por ejemplo, maquinaria aeroespacial o industrial), pueden ser más adecuados recubrimientos alternativos como el diamante, el carburo de silicio o los recubrimientos cerámicos.
-
Mejora de la estabilidad a altas temperaturas:
- Dopaje:La adición de elementos como el silicio o el wolframio puede mejorar la estabilidad térmica.
- Estructuras multicapa:La combinación de DLC con otros materiales puede mejorar el rendimiento bajo estrés térmico.
- Tratamiento posterior:El recocido o el tratamiento con láser pueden modificar la estructura del revestimiento para mejorar su resistencia a las altas temperaturas.
-
Consideraciones prácticas para los compradores de equipos y consumibles:
- Evalúe el intervalo de temperaturas de funcionamiento de la aplicación antes de seleccionar un revestimiento de DLC.
- Tenga en cuenta las compensaciones entre coste, rendimiento y estabilidad térmica.
- Consulte a los proveedores de revestimientos para identificar la mejor variante o alternativa de DLC para su uso a altas temperaturas.
En resumen, aunque los revestimientos de DLC ofrecen excelentes propiedades para muchas aplicaciones, su rendimiento a altas temperaturas está limitado a unos 300-400°C.Para entornos con temperaturas más elevadas, deben considerarse soluciones alternativas o variantes especializadas de DLC.
Cuadro sinóptico:
Aspecto | Detalles |
---|---|
Temperatura límite | 300-400°C antes de la degradación (grafitización o pérdida de hidrógeno) |
Factores clave | Estructura de enlace (sp3 vs. sp2), contenido de hidrógeno, método de deposición |
Aplicaciones | Automoción, herramientas de corte, dispositivos biomédicos (por debajo de 300°C) |
Soluciones para altas temperaturas | Dopado, estructuras multicapa, postratamiento o revestimientos alternativos |
¿Necesita una solución de revestimiento para aplicaciones de alta temperatura? Póngase en contacto hoy mismo con nuestros expertos para encontrar el que mejor se adapte a sus necesidades.