La forja es un proceso de fabricación que implica dar forma al metal utilizando fuerzas de compresión localizadas. Normalmente se realiza a altas temperaturas para hacer que el metal sea más maleable, aunque también es posible la forja en frío. El proceso comienza calentando el metal a una temperatura específica, seguido de darle forma utilizando troqueles o martillos. La forja mejora las propiedades mecánicas del metal, como la resistencia y la durabilidad, al alinear la estructura del grano. El paso final a menudo implica procesos de acabado como mecanizado o tratamiento térmico para lograr las dimensiones y propiedades deseadas. La forja se utiliza ampliamente en industrias como la automotriz, la aeroespacial y la construcción para producir componentes de alta resistencia.
Puntos clave explicados:
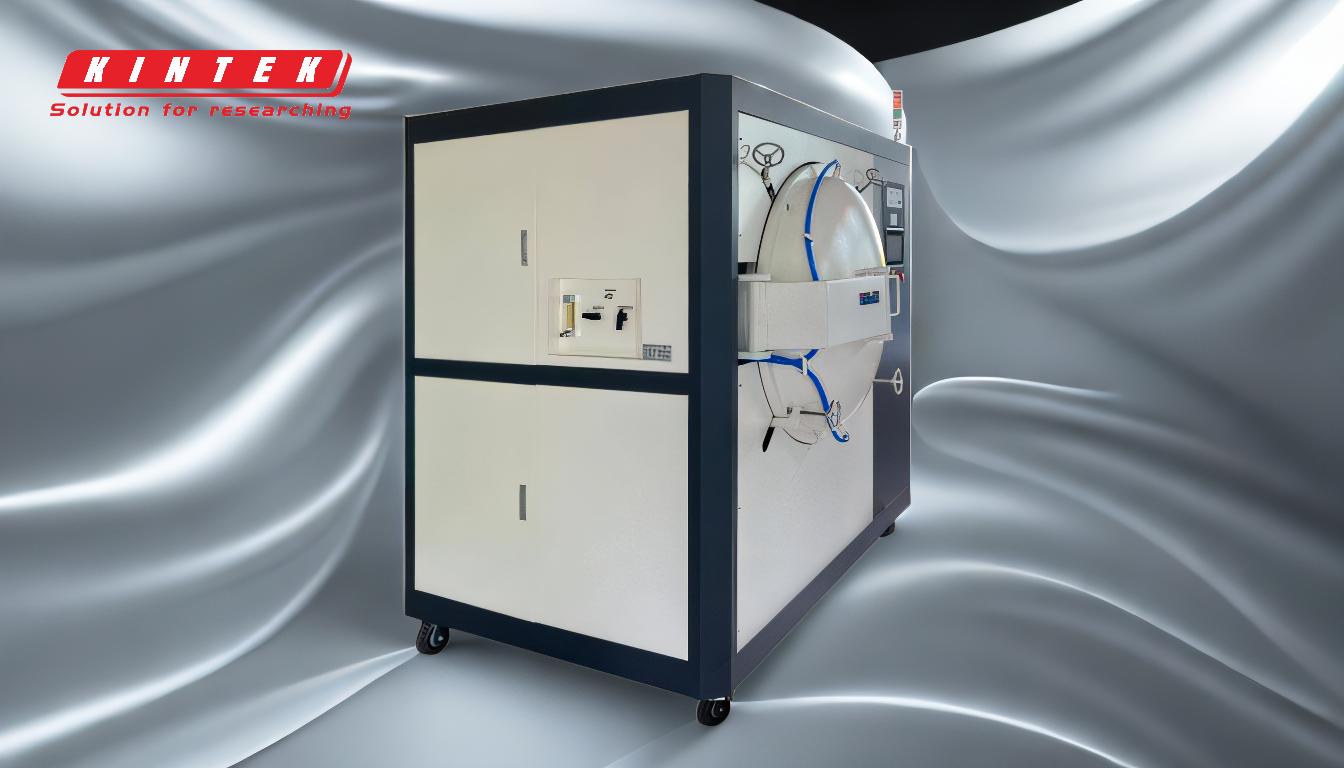
-
Calentar el metal:
- El primer paso en la forja es calentar el metal a una temperatura específica, lo que lo hace más maleable y más fácil de moldear. La temperatura varía según el tipo de metal que se forja. Por ejemplo, el acero normalmente se calienta a alrededor de 2100 °F (1150 °C).
-
Dar forma al metal:
- Una vez que el metal se calienta, se coloca sobre un troquel o yunque y se le da forma mediante fuerzas de compresión. Esto se puede hacer mediante varios métodos, como martillar, presionar o rodar. El proceso de conformado se puede realizar manualmente o con la ayuda de máquinas, dependiendo de la complejidad y el tamaño de la pieza a forjar.
-
Tipos de forja:
- Forja con matriz abierta: Este método implica dar forma al metal entre matrices planas, lo que permite una mayor flexibilidad en la forma y el tamaño del producto final. A menudo se utiliza para piezas grandes o personalizadas.
- Forja en matriz cerrada: En este método, el metal se coloca en un troquel que contiene una cavidad preformada. Luego, el metal se introduce en la cavidad para que tome su forma. Este método es más preciso y se utiliza para producir piezas complejas con tolerancias estrictas.
- Forja en rollo: Este proceso consiste en pasar el metal por un juego de rodillos para reducir su espesor y aumentar su longitud. Se utiliza comúnmente para producir componentes largos y delgados como ejes o barras.
-
Mejora de las propiedades mecánicas:
- La forja mejora las propiedades mecánicas del metal alineando la estructura del grano a lo largo de los contornos de la pieza final. Esto da como resultado una mayor resistencia, durabilidad y resistencia a la fatiga y al impacto. El proceso también elimina huecos y defectos internos, lo que da como resultado un material más uniforme y confiable.
-
Procesos de acabado:
- Después del proceso de forjado, la pieza suele pasar por procesos de acabado adicionales para lograr las dimensiones y la calidad superficial deseadas. Estos procesos pueden incluir mecanizado, tratamiento térmico o técnicas de acabado de superficies como esmerilado o pulido. El tratamiento térmico, en particular, se utiliza para mejorar la dureza y resistencia de la pieza forjada.
-
Aplicaciones de la forja:
- La forja se utiliza en una amplia gama de industrias para producir componentes de alta resistencia. En la industria automotriz, las piezas forjadas incluyen cigüeñales, bielas y engranajes. En el sector aeroespacial, los componentes forjados se utilizan en motores, trenes de aterrizaje y piezas estructurales. La industria de la construcción también depende de la forja para producir componentes de alta resistencia como pernos, anclajes y vigas estructurales.
-
Ventajas de la forja:
- Resistencia y durabilidad: Las piezas forjadas son más resistentes y duraderas que las producidas por fundición o mecanizado.
- Eficiencia de materiales: La forja minimiza el desperdicio de material, ya que el proceso implica dar forma al metal en lugar de eliminar material.
- Versatilidad: La forja se puede utilizar para producir una amplia gama de formas y tamaños, desde pequeñas piezas intrincadas hasta grandes componentes estructurales.
-
Desafíos en la forja:
- Costo: Los costos de configuración inicial para la forja pueden ser altos, especialmente para troqueles y herramientas personalizados.
- Complejidad: Producir formas complejas con tolerancias estrictas puede ser un desafío y puede requerir equipos y experiencia especializados.
- Limitaciones de materiales: No todos los metales son aptos para la forja y algunos pueden requerir condiciones o tratamientos específicos para lograr las propiedades deseadas.
En resumen, la forja es un proceso de fabricación versátil y eficaz que mejora las propiedades mecánicas de los componentes metálicos. Implica calentar, dar forma y terminar el metal para producir piezas resistentes y duraderas que se utilizan en diversas industrias. A pesar de algunos desafíos, los beneficios de la forja la convierten en el método preferido para producir componentes de alto rendimiento.
Tabla resumen:
Paso | Descripción |
---|---|
Calentar el metal | El metal se calienta a una temperatura específica para hacerlo maleable. |
Dar forma al metal | Las fuerzas de compresión dan forma al metal mediante matrices, martillos o rodillos. |
Tipos de forja | Forjado con troquel abierto, con troquel cerrado y por rodillos para diferentes formas y precisión. |
Mejora de propiedades | Alinea la estructura del grano para mayor resistencia, durabilidad y confiabilidad. |
Procesos de acabado | Mecanizado, tratamiento térmico o acabado superficial para lograr las propiedades deseadas. |
Aplicaciones | Se utiliza en automoción, aeroespacial y construcción para componentes de alta resistencia. |
Descubra cómo la forja puede mejorar su proceso de fabricación. contáctanos hoy ¡Para orientación experta!