El proceso de sinterización es una técnica de fabricación fundamental que se utiliza para transformar materiales en polvo en cuerpos densos y sólidos aplicando calor y presión por debajo del punto de fusión del material. Comprende varias etapas, como la preparación de una mezcla de polvo con un agente aglutinante, el moldeado del material para darle la forma deseada, el calentamiento para eliminar el agente aglutinante y la fusión de las partículas primarias para crear una masa unificada de baja porosidad. Este proceso se utiliza ampliamente en industrias como la pulvimetalurgia y la cerámica para producir componentes duraderos y de alta resistencia. Los pasos clave incluyen la composición, la compresión, el calentamiento, la fusión de partículas y la solidificación, cada uno de los cuales contribuye a las propiedades finales del material.
Explicación de los puntos clave:
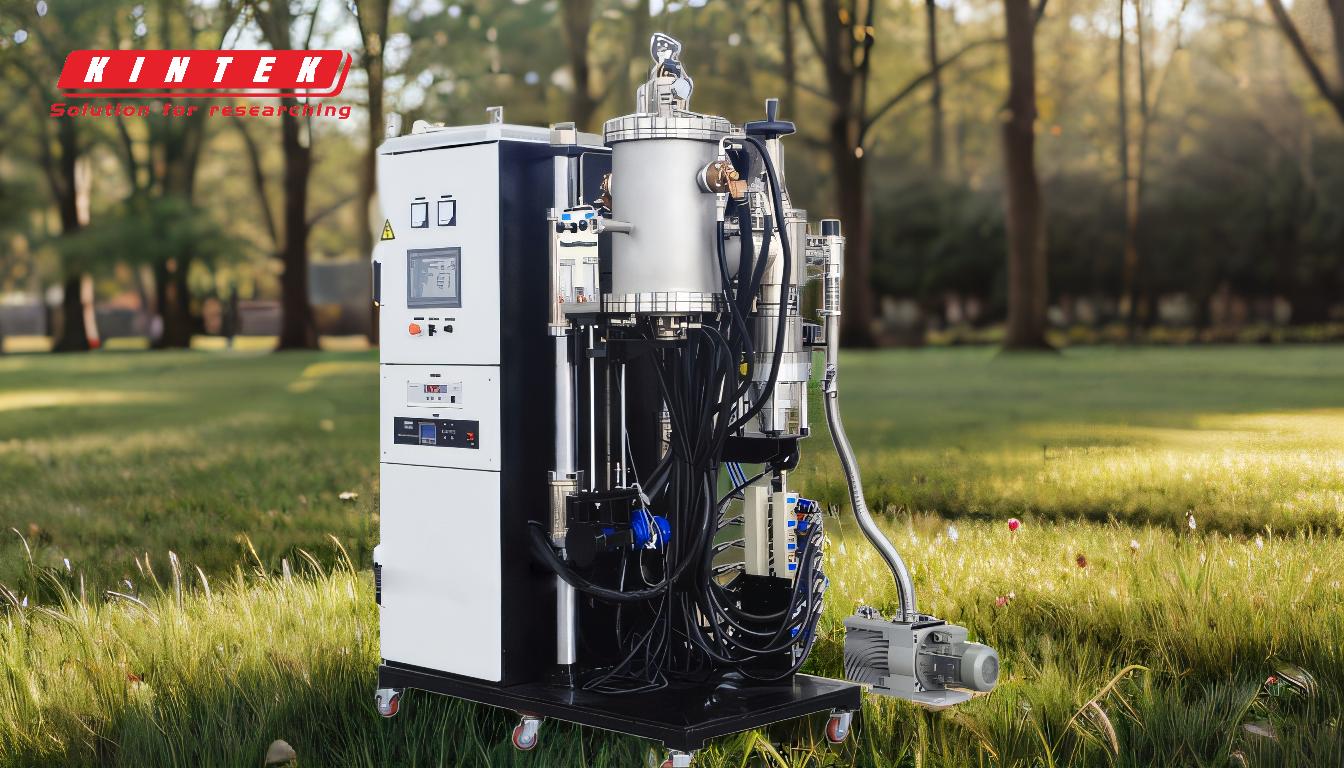
-
Preparación de la mezcla de polvos:
- Composición: El proceso comienza mezclando materiales primarios (como polvos metálicos o cerámicos) con un agente aglutinante (por ejemplo, cera o polímero). El agente aglutinante ayuda a que las partículas de polvo se adhieran entre sí, formando una mezcla cohesiva.
- Conformación: A continuación, se da a la mezcla de polvo la forma deseada mediante técnicas como el prensado en frío, la impresión 3D u otros métodos de conformado. Así se crea una "pieza verde", que es una estructura preliminar que mantiene su forma pero aún no es totalmente densa.
-
Compresión y conformado:
- Compresión: La pieza verde se comprime para conseguir la forma y densidad requeridas. Este paso garantiza que las partículas se empaqueten estrechamente, reduciendo la porosidad y preparando el material para la fase de calentamiento.
- Atmósfera controlada: En algunos casos, la compresión se produce en una atmósfera controlada para evitar la oxidación o la contaminación, que podrían afectar a las propiedades del material.
-
Calentamiento y eliminación del agente adhesivo:
- Calentamiento inicial: La pieza verde se calienta a una temperatura en la que el agente adhesivo se evapora o se quema. Este paso es crucial para eliminar cualquier material orgánico que pudiera interferir en el proceso de sinterización.
- Control de la temperatura: La temperatura se controla cuidadosamente para garantizar que el agente adhesivo se elimine por completo sin dañar el material primario.
-
Fusión de partículas:
-
Temperatura de sinterización: A continuación, la temperatura se eleva justo por debajo del punto de fusión del material. En esta fase, se produce uno de los dos procesos siguientes:
- Sinterización en estado sólido: Las partículas primarias comienzan a fundirse en sus superficies debido a la difusión atómica, creando una estructura más densa.
- Sinterización en fase líquida (LPS): Un agente de unión intermedio, como el bronce, se funde y fluye entre las partículas, uniéndolas mientras el material primario permanece sólido.
- Densificación: Las partículas se densifican y fusionan, reduciendo la porosidad y aumentando la resistencia y durabilidad del material.
-
Temperatura de sinterización: A continuación, la temperatura se eleva justo por debajo del punto de fusión del material. En esta fase, se produce uno de los dos procesos siguientes:
-
Solidificación y enfriamiento:
- Fase de enfriamiento: Una vez finalizado el proceso de sinterización, se deja enfriar el material y se solidifica en una masa unificada. Este paso garantiza que el material conserve su forma y sus propiedades.
- Propiedades finales: El producto final es un material denso y de baja porosidad con propiedades mecánicas mejoradas, como dureza, resistencia y durabilidad.
-
Aplicaciones y ventajas:
- Uso industrial: La sinterización se utiliza ampliamente en la pulvimetalurgia para producir componentes metálicos y en la fabricación de cerámica para crear productos cerámicos duraderos.
- Materiales de alto punto de fusión: Este proceso es especialmente útil para materiales con puntos de fusión extremadamente altos, como el tungsteno y el molibdeno, que son difíciles de procesar mediante técnicas de fusión tradicionales.
- Personalización: El sinterizado permite la producción de formas complejas y componentes personalizados, lo que lo convierte en un método de fabricación versátil.
Siguiendo estos pasos, el proceso de sinterización transforma polvos sueltos en materiales resistentes y densos adecuados para una amplia gama de aplicaciones industriales. El cuidadoso control de la temperatura, la presión y la atmósfera garantiza que el producto final cumpla las especificaciones y los requisitos de rendimiento deseados.
Tabla resumen:
Etapa | Detalles clave |
---|---|
Preparación | Mezclar las materias primas con un agente adhesivo y dar forma a una "pieza verde". |
Compresión | Comprimir la pieza verde para reducir la porosidad y alcanzar la densidad deseada. |
Calentamiento | Calentar para eliminar el agente adhesivo y preparar la fusión de partículas. |
Fusión de partículas | Aumentar la temperatura para fusionar las partículas mediante sinterización en estado sólido o en fase líquida. |
Solidificación | Enfriar y solidificar en un material denso y de baja porosidad con propiedades mejoradas. |
Aplicaciones | Se utiliza en pulvimetalurgia y cerámica para obtener componentes duraderos y de alta resistencia. |
Descubra cómo el sinterizado puede mejorar su proceso de fabricación. póngase en contacto con nosotros para obtener asesoramiento experto.