El enfriamiento rápido del aluminio es un proceso crítico en metalurgia cuyo objetivo es enfriar rápidamente el metal para conseguir propiedades mecánicas y estructurales específicas.Este proceso es esencial para mejorar la dureza, resistencia y durabilidad de las aleaciones de aluminio, haciéndolas adecuadas para diversas aplicaciones industriales.Al controlar la velocidad de enfriamiento, el temple ayuda a fijar la microestructura deseada, evitando la formación de fases no deseadas que podrían debilitar el material.Este resumen proporciona una comprensión básica de por qué el enfriamiento rápido es indispensable en el procesamiento del aluminio.
Explicación de los puntos clave:
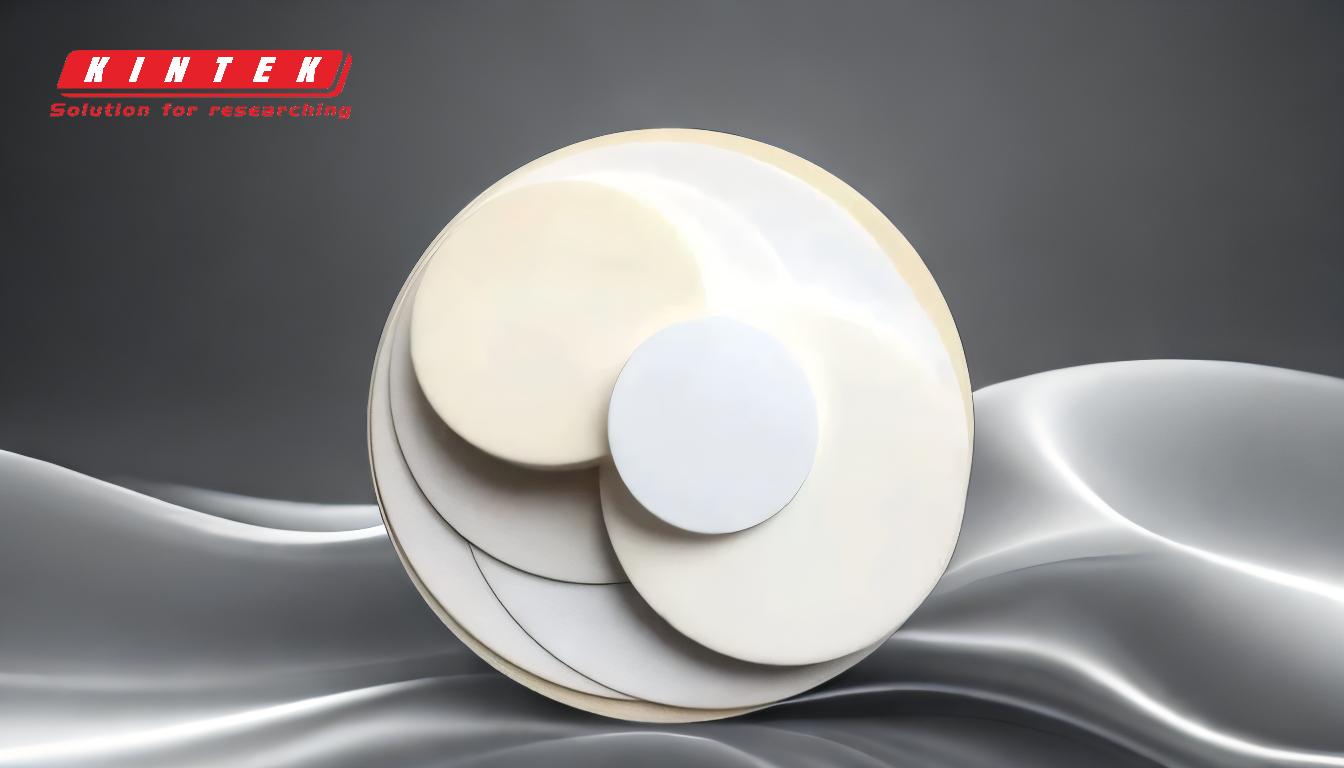
-
Mejora de las propiedades mecánicas:
- El enfriamiento rápido del aluminio mejora significativamente sus propiedades mecánicas, como la dureza y la resistencia.Cuando el aluminio se calienta a alta temperatura, su microestructura se vuelve más maleable.El enfriamiento rápido mediante temple mantiene esta estructura en su lugar, impidiendo la formación de fases más blandas que, de otro modo, reducirían la resistencia del material.
-
Prevención de la formación de fases no deseadas:
- Durante el proceso de enfriamiento, el aluminio puede formar diferentes fases en función de la velocidad de enfriamiento.Un enfriamiento lento puede dar lugar a la formación de fases más blandas y menos deseables.El enfriamiento rápido garantiza que el aluminio se enfríe lo suficientemente rápido como para evitar estas fases, manteniendo una microestructura más uniforme y deseable.
-
Mejora de la durabilidad y la resistencia al desgaste:
- El enfriamiento rápido que se consigue mediante el temple no sólo aumenta la dureza, sino que también mejora la durabilidad general y la resistencia al desgaste del aluminio.Esto hace que el aluminio templado sea ideal para aplicaciones en las que el material está sometido a una gran tensión y fricción, como en los componentes de automoción y aeroespaciales.
-
Obtención de la microestructura deseada:
- La microestructura del aluminio desempeña un papel crucial en la determinación de sus propiedades.El enfriamiento rápido permite un control preciso de esta microestructura, garantizando que el producto final tenga las características deseadas.Esto es especialmente importante en industrias en las que el rendimiento del material es crítico.
-
Aplicación en procesos de tratamiento térmico:
- El enfriamiento rápido suele ser un paso clave en el tratamiento térmico de las aleaciones de aluminio.Tras calentarlo a una temperatura específica, el aluminio se enfría rápidamente para conseguir las propiedades deseadas.Este proceso es esencial para crear materiales de alto rendimiento utilizados en diversas aplicaciones industriales.
-
Comparación con otros materiales:
- Aunque el temple suele asociarse al acero, es igualmente importante para el aluminio.A diferencia del acero, que suele enfriarse en agua o aceite, el aluminio suele enfriarse en agua o aire, dependiendo de la aleación específica y de las propiedades deseadas.
-
Relevancia industrial:
- La capacidad de enfriar eficazmente el aluminio es crucial para las industrias que dependen de materiales de alto rendimiento.Desde la automoción hasta la industria aeroespacial, las propiedades mejoradas que se consiguen mediante el temple hacen del aluminio un material versátil y fiable para una amplia gama de aplicaciones.
En conclusión, el temple del aluminio es un proceso vital que mejora sus propiedades mecánicas, evita la formación de fases no deseadas y mejora su durabilidad general y su resistencia al desgaste.Mediante el control de la velocidad de enfriamiento, el temple garantiza que las aleaciones de aluminio alcancen la microestructura deseada, haciéndolas adecuadas para diversas aplicaciones de alta resistencia.Este proceso forma parte integral del tratamiento térmico del aluminio, destacando su importancia en la metalurgia moderna y en las aplicaciones industriales.
Tabla resumen:
Beneficio clave | Descripción |
---|---|
Propiedades mecánicas mejoradas | Mejora la dureza y la resistencia al fijar una microestructura deseable. |
Evita fases no deseadas | El enfriamiento rápido evita las fases más blandas y menos deseables, garantizando una estructura uniforme. |
Aumenta la durabilidad | Aumenta la resistencia al desgaste, ideal para aplicaciones de alto esfuerzo. |
Controla la microestructura | Consigue propiedades precisas de los materiales para usos industriales críticos. |
Integrado en el tratamiento térmico | Un paso clave en la creación de aleaciones de aluminio de alto rendimiento. |
Descubra cómo el temple del aluminio puede optimizar el rendimiento de sus materiales. contacte hoy mismo con nuestros expertos ¡!