La pulvimetalurgia es un proceso de fabricación versátil que ofrece numerosas ventajas, como eficiencia energética, rentabilidad y la capacidad de producir piezas complejas y de alta precisión con un mínimo de desperdicio. Es particularmente beneficioso para industrias como la automotriz y la aeroespacial debido a su capacidad para crear piezas homogéneas y uniformes con tolerancias excepcionales. Sin embargo, también tiene limitaciones, incluidas restricciones de tamaño, desafíos para producir formas altamente complejas y menor resistencia y ductilidad en comparación con los métodos tradicionales de fundición o forja. A pesar de estos inconvenientes, la pulvimetalurgia sigue siendo una tecnología vital y ecológica en la fabricación moderna.
Puntos clave explicados:
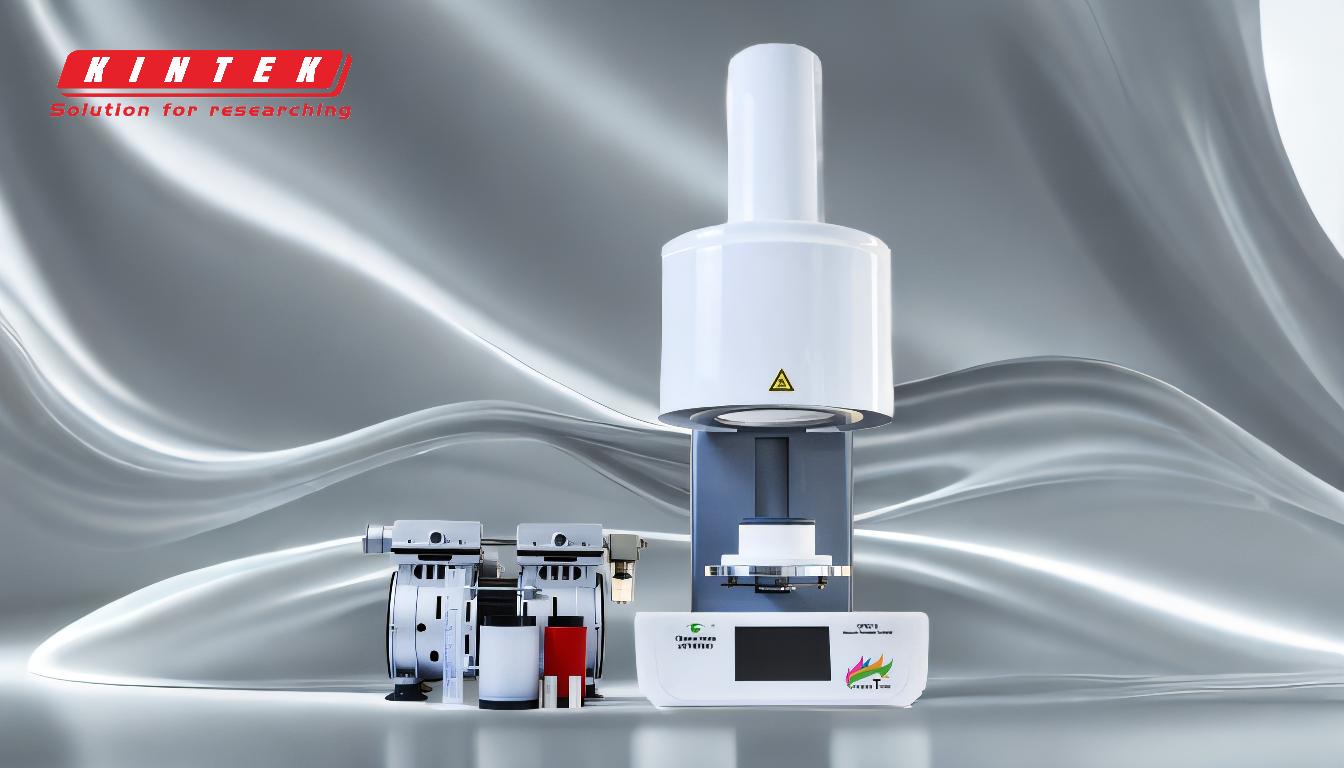
-
Ventajas de la metalurgia de polvos:
- Eficiencia energética y rentabilidad: La pulvimetalurgia es un proceso corto y eficiente que reduce el consumo de energía y el desperdicio de material. Aproximadamente el 97% del material utilizado pasa a formar parte del producto final, minimizando los desechos y reduciendo los costes.
- Precisión y uniformidad: El proceso permite la creación de piezas homogéneas y uniformes con tolerancias excepcionales, lo que lo hace ideal para aplicaciones de alta precisión.
- Flexibilidad de materiales: La pulvimetalurgia permite el ensamblaje de estructuras de materiales para controlar con precisión las propiedades, lo que la hace adecuada para producir materiales de alto valor agregado, especialmente aleaciones con altos puntos de fusión o baja moldeabilidad.
- Fabricación ecológica: Con un desperdicio mínimo y sin desechos, la pulvimetalurgia se considera una tecnología de fabricación ecológica, alineada con prácticas de producción sostenibles.
-
Aplicaciones en industrias clave:
- Automotriz y aeroespacial: La capacidad de producir componentes livianos, duraderos y de alta precisión hace que la pulvimetalurgia sea un proceso vital para estas industrias.
- Herramientas manuales: Las herramientas fabricadas con pulvimetalurgia exhiben una resistencia al desgaste, tenacidad y retención de dureza superiores, y duran hasta cinco veces más que las fabricadas con otros métodos.
-
Desventajas de la metalurgia de polvos:
- Limitaciones de tamaño: Las prensas más grandes de la industria pesan alrededor de 1.500 toneladas, lo que limita el tamaño práctico de las piezas a aproximadamente 40 a 50 pulgadas cuadradas de área plana.
- Formas complejas: Si bien los fabricantes cualificados pueden superar algunos desafíos, producir piezas con formas muy complejas todavía puede resultar difícil.
- Resistencia y Ductilidad: Las piezas de pulvimetalurgia generalmente no son tan fuertes ni tan dúctiles como las producidas por fundición o forja, lo que puede limitar su uso en aplicaciones que requieren un alto rendimiento mecánico.
-
Perspectivas futuras:
- La precisión y eficiencia de la pulvimetalurgia la convierten en una tecnología prometedora para la fabricación futura, especialmente a medida que las industrias continúan priorizando la sostenibilidad y los materiales de alto rendimiento. Es probable que más industrias, incluida la fabricación de herramientas manuales, adopten este método en un futuro próximo.
En resumen, la pulvimetalurgia ofrece ventajas significativas en términos de eficiencia, precisión y sostenibilidad, pero también tiene limitaciones en términos de tamaño de pieza, complejidad y propiedades mecánicas. Comprender estas compensaciones es crucial para los fabricantes y compradores al considerar esta tecnología para aplicaciones específicas.
Tabla resumen:
Aspecto | Ventajas | Desventajas |
---|---|---|
Eficiencia Energética | Reduce el consumo de energía y el desperdicio de material (97% de utilización de material). | Limitado por el tamaño de la prensa (hasta 1.500 toneladas). |
Precisión y uniformidad | Produce piezas homogéneas y de alta precisión con tolerancias excepcionales. | Desafíos en la producción de formas altamente complejas. |
Flexibilidad de materiales | Permite controlar las propiedades del material, ideal para aleaciones de alto valor añadido. | Menor resistencia y ductilidad en comparación con la fundición o la forja. |
Ecológico | Mínimo desperdicio y sin desperdicios, alineándose con prácticas sustentables. | Tamaño de pieza limitado a ~40-50 pulgadas cuadradas. |
Descubra cómo la pulvimetalurgia puede beneficiar su proceso de fabricación. póngase en contacto con nuestros expertos hoy !