La deposición en vacío es un proceso versátil y muy utilizado en diversos sectores gracias a su capacidad para crear revestimientos finos, uniformes y de alto rendimiento sobre distintos sustratos.Se emplea en aplicaciones que van desde la mejora de la funcionalidad de los dispositivos electrónicos hasta la mejora de la durabilidad y la estética de los productos de consumo.Entre las industrias clave que utilizan la deposición en vacío se encuentran la fabricación de semiconductores, la energía solar, los dispositivos médicos, la industria aeroespacial, la automoción y el envasado.El proceso es esencial para crear revestimientos como capas ópticas, espejos, decorativas, resistentes al desgaste y protectoras contra la corrosión, así como para producir películas funcionales como capas conductoras y barreras de permeabilidad.Sus aplicaciones son cruciales para el avance de tecnologías como las células solares de película fina, las pantallas flexibles y los dispositivos energéticamente eficientes.
Explicación de los puntos clave:
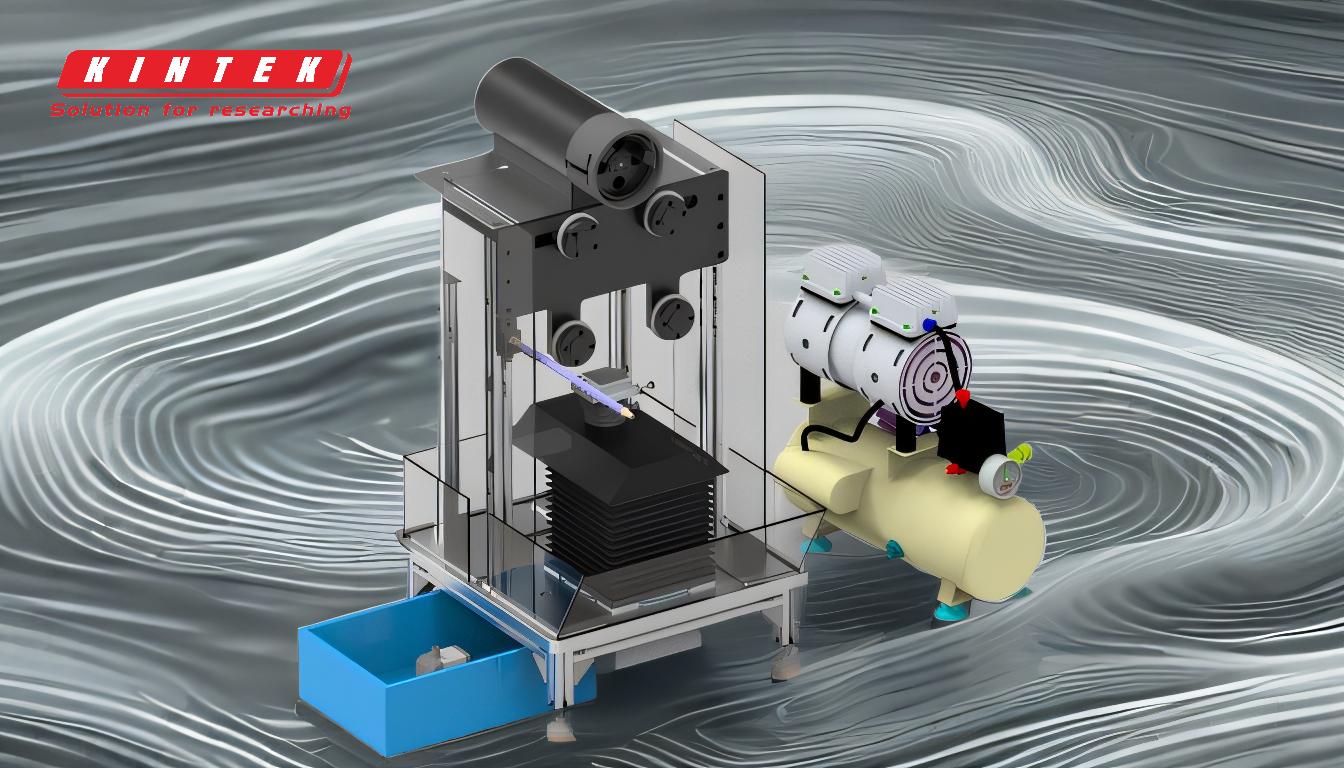
-
Fabricación de semiconductores y electrónica:
- La deposición en vacío es crucial en la producción de microchips, LED y transistores de película fina.Se utiliza para depositar patrones metálicos conductores y capas aislantes, esenciales para la funcionalidad de los dispositivos electrónicos.
- El proceso permite crear revestimientos de alta precisión necesarios para los dispositivos semiconductores, garantizando un rendimiento y una miniaturización óptimos.
-
Aplicaciones de energía solar:
- En la fabricación de células solares de película fina, la deposición al vacío se utiliza para mejorar la conductividad y las propiedades de absorción de la luz.Esto mejora la eficiencia y la durabilidad de las células solares.
- El proceso permite la deposición de múltiples capas con espesores precisos, optimizando la capacidad de conversión de energía de los paneles solares.
-
Recubrimientos ópticos y decorativos:
- La deposición en vacío se utiliza ampliamente para crear revestimientos ópticos, como revestimientos antirreflectantes, de espejo y de interferencia, que son esenciales para lentes, espejos y pantallas.
- Los revestimientos decorativos se aplican a productos como piezas de automóviles, joyas y productos electrónicos de consumo para mejorar su aspecto y durabilidad.
-
Recubrimientos resistentes al desgaste y protectores contra la corrosión:
- El proceso se emplea para depositar revestimientos resistentes al desgaste en herramientas, maquinaria y componentes de automoción, prolongando su vida útil y su rendimiento.
- Los revestimientos protectores contra la corrosión se aplican a metales y otros materiales utilizados en entornos difíciles, como aplicaciones aeroespaciales y marinas, para evitar su degradación.
-
Envases flexibles y barreras de permeación:
- La deposición al vacío se utiliza para crear películas finas y flexibles que actúan como barreras de permeabilidad en los materiales de envasado.Estas películas protegen los productos de la humedad, el oxígeno y otros contaminantes, prolongando su vida útil.
- Esta aplicación es especialmente importante en las industrias alimentaria y farmacéutica.
-
Dispositivos médicos y productos sanitarios a domicilio:
- El proceso se utiliza para revestir herramientas y dispositivos médicos, mejorando su funcionalidad, biocompatibilidad y resistencia al desgaste y la corrosión.
- Los dispositivos médicos de uso doméstico, como sensores y herramientas de diagnóstico, se benefician de revestimientos depositados al vacío que mejoran su precisión y durabilidad.
-
Industria aeroespacial y del automóvil:
- La deposición en vacío se utiliza para aplicar revestimientos que mejoran el rendimiento y la longevidad de componentes aeroespaciales, como álabes de turbina y sensores.
- En la industria del automóvil, se utiliza para acabados decorativos, protección contra la corrosión y revestimientos funcionales en piezas como espejos y sensores.
-
Conservación y generación de energía:
- El proceso se emplea en la producción de revestimientos energéticamente eficientes para ventanas y otras superficies, que reducen la pérdida de calor y mejoran el aislamiento.
- También se emplea en la fabricación de películas magnéticas y barreras de difusión, fundamentales para las tecnologías de almacenamiento y conversión de energía.
-
Pantallas y sensores flexibles:
- La deposición en vacío es esencial para producir transistores de película fina utilizados en pantallas y sensores flexibles, lo que permite desarrollar dispositivos electrónicos plegables y ligeros.
- Esta tecnología está impulsando la innovación en la electrónica vestible, los smartphones plegables y otros productos de consumo avanzados.
Al aprovechar la precisión y versatilidad de la deposición al vacío, las industrias pueden lograr un mayor rendimiento, durabilidad y funcionalidad en sus productos, lo que la convierte en una piedra angular de la fabricación moderna y el desarrollo tecnológico.
Tabla resumen:
Industria | Aplicaciones |
---|---|
Fabricación de semiconductores | Microchips, LED, transistores de película fina, patrones conductores, capas aislantes |
Energía solar | Células solares de capa fina, absorción de luz, optimización de la conversión energética |
Revestimientos ópticos | Revestimientos antirreflejos, de espejo y de interferencia para lentes y pantallas |
Revestimientos resistentes al desgaste | Herramientas, maquinaria, componentes de automoción para prolongar la vida útil |
Envases flexibles | Barreras de permeación para envases alimentarios y farmacéuticos |
Dispositivos médicos | Recubrimientos biocompatibles para herramientas, sensores y dispositivos de diagnóstico |
Aeroespacial y automoción | Protección contra la corrosión, acabados decorativos, revestimientos funcionales |
Conservación de la energía | Revestimientos energéticamente eficientes para ventanas, películas magnéticas, barreras de difusión |
Pantallas flexibles | Transistores de película fina para electrónica portátil y teléfonos inteligentes plegables |
¿Le interesa saber cómo la deposición al vacío puede mejorar su sector? Póngase en contacto con nosotros para obtener más información.