El recocido en semiconductores es un proceso térmico crítico que se utiliza para modificar las propiedades del material, como reducir defectos, mejorar las características eléctricas y mejorar la integridad estructural. A diferencia del recocido de metales, que se centra principalmente en el alivio de tensiones y la ductilidad, el recocido de semiconductores está diseñado para abordar los requisitos únicos de los materiales semiconductores, como las obleas de silicio. El proceso implica calentar el material a una temperatura específica y luego enfriarlo en condiciones controladas. Este tratamiento térmico se puede clasificar en varios tipos, cada uno de los cuales tiene distintos propósitos en la fabricación de semiconductores.
Puntos clave explicados:
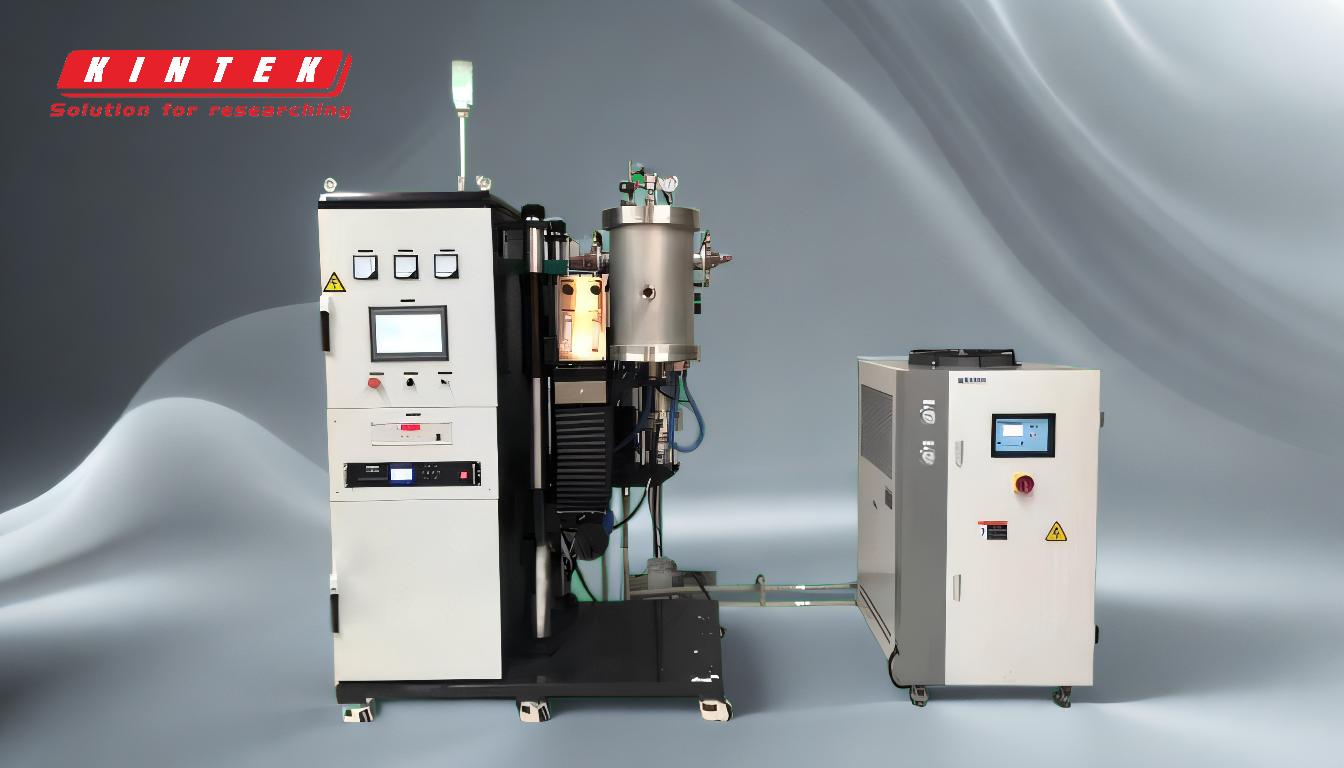
-
Propósito del recocido en semiconductores:
- Reducción de defectos: El recocido ayuda a reducir los defectos en la red cristalina, como vacantes y dislocaciones, que pueden afectar negativamente el rendimiento de los dispositivos semiconductores.
- Activación dopante: En la fabricación de semiconductores, se introducen dopantes para modificar las propiedades eléctricas. El recocido activa estos dopantes incorporándolos a la red cristalina.
- Alivio del estrés: De manera similar al recocido de metales, el recocido de semiconductores puede aliviar las tensiones internas que surgen durante los procesos de fabricación como la deposición o el grabado.
- Recristalización: El recocido puede promover la recristalización, lo que mejora la integridad estructural y las propiedades eléctricas del material.
-
Tipos de recocido en semiconductores:
-
Recocido en horno:
- Proceso: La oblea semiconductora se calienta en un horno a temperaturas que normalmente oscilan entre 600 °C y 1200 °C durante varios minutos u horas.
- Aplicaciones: Se utiliza para procesamiento a granel, como activación de dopantes y recocido de defectos. Es adecuado para la producción a gran escala debido a su capacidad para manejar múltiples obleas simultáneamente.
- Ventajas: El calentamiento uniforme y los tiempos de procesamiento prolongados permiten una reducción exhaustiva de los defectos y la activación de dopantes.
- Limitaciones: Tiempos de procesamiento más prolongados pueden provocar una difusión no deseada de dopantes, lo que afectará el rendimiento del dispositivo.
-
Recocido térmico rápido (RTA):
- Proceso: La oblea se calienta a altas temperaturas (hasta 1200 °C) durante un período muy corto, normalmente unos pocos segundos, utilizando fuentes de luz intensa como lámparas halógenas.
- Aplicaciones: Ideal para procesos que requieren un control preciso de la temperatura y el tiempo, como la formación de uniones poco profundas en dispositivos semiconductores avanzados.
- Ventajas: Minimiza la difusión de dopantes, lo que lo hace adecuado para dispositivos modernos con características más pequeñas.
- Limitaciones: Requiere equipos sofisticados y un control preciso para evitar estrés térmico y daños a la oblea.
-
Recocido por láser:
- Proceso: Se utiliza un rayo láser de alta energía para calentar la superficie de la oblea a temperaturas extremadamente altas durante un tiempo muy corto (de nanosegundos a milisegundos).
- Aplicaciones: Se utiliza para recocido localizado, como reparar defectos en áreas específicas o activar dopantes en regiones pequeñas.
- Ventajas: Calentamiento altamente preciso y localizado, minimizando el impacto térmico en las zonas circundantes.
- Limitaciones: Limitado a tratamientos de superficie y requiere sistemas láser avanzados.
-
Recocido de lámpara de flash:
- Proceso: Se utiliza luz intensa de una lámpara de flash para calentar la superficie de la oblea rápidamente, similar al RTA pero con duraciones aún más cortas (milisegundos).
- Aplicaciones: Adecuado para la formación de uniones ultra superficiales y reparación de defectos superficiales.
- Ventajas: Procesamiento extremadamente rápido, lo que reduce el riesgo de difusión de dopantes.
- Limitaciones: Limitado a tratamientos de superficie y requiere equipo especializado.
-
-
Comparación de técnicas de recocido:
- Temperatura y tiempo: El recocido en horno funciona a temperaturas más bajas durante períodos más prolongados, mientras que el RTA, el recocido por láser y el recocido con lámpara de destello implican temperaturas más altas durante tiempos más cortos.
- Precisión y localización: El recocido con láser y lámpara de flash ofrece mayor precisión y localización en comparación con el recocido en horno y RTA.
- Complejidad del equipo: El recocido en horno es relativamente simple, mientras que RTA, el recocido por láser y el recocido con lámpara de flash requieren equipos más avanzados y costosos.
-
Aplicaciones en la fabricación de semiconductores:
- Activación dopante: Se utilizan todas las técnicas de recocido para activar dopantes, pero la elección depende de los requisitos del dispositivo y el tamaño de la característica.
- Reparación de defectos: El recocido con láser y lámpara de flash es particularmente útil para reparar defectos en áreas específicas sin afectar toda la oblea.
- Alivio del estrés: El recocido en horno se usa comúnmente para aliviar tensiones en el procesamiento a granel, mientras que se prefiere RTA para aliviar tensiones en dispositivos avanzados.
-
Tendencias futuras en el recocido de semiconductores:
- Materiales avanzados: A medida que los materiales semiconductores evolucionen, las técnicas de recocido deberán adaptarse para manejar nuevos materiales como el nitruro de galio (GaN) y el carburo de silicio (SiC).
- Dispositivos 3D: Con el auge de los dispositivos semiconductores 3D, las técnicas de recocido deberán abordar los desafíos relacionados con la distribución del calor y el manejo de la tensión en estructuras complejas.
- Eficiencia Energética: Los futuros procesos de recocido pueden centrarse en reducir el consumo de energía manteniendo o mejorando el rendimiento.
En resumen, el recocido en semiconductores es un proceso versátil y esencial que desempeña un papel crucial en el rendimiento y la confiabilidad del dispositivo. La elección de la técnica de recocido depende de los requisitos específicos del dispositivo semiconductor, como el tamaño de la característica, las propiedades del material y las características eléctricas deseadas. A medida que la tecnología de semiconductores siga avanzando, los procesos de recocido evolucionarán para satisfacer las demandas de los dispositivos de próxima generación.
Tabla resumen:
Tipo | Proceso | Aplicaciones | Ventajas | Limitaciones |
---|---|---|---|---|
Recocido en horno | Calentado a 600°C–1200°C durante minutos u horas | Procesamiento a granel, activación de dopantes, recocido de defectos. | Calentamiento uniforme, reducción exhaustiva de defectos. | Tiempos de procesamiento más prolongados pueden causar difusión dopante |
Térmico rápido (RTA) | Calentado a 1200°C durante segundos usando lámparas halógenas. | Formación de uniones poco profundas, dispositivos avanzados. | Minimiza la difusión de dopantes, control preciso. | Requiere equipos sofisticados, riesgo de estrés térmico. |
Recocido por láser | Un láser de alta energía calienta la superficie durante nanosegundos a milisegundos | Reparación de defectos localizados, activación dopante. | Alta precisión, mínimo impacto térmico en las áreas circundantes. | Limitado a tratamientos de superficie, requiere sistemas láser avanzados. |
Recocido de lámpara de flash | La luz intensa calienta la superficie rápidamente (milisegundos) | Formación de uniones ultrasuperficiales, reparación de defectos superficiales. | Procesamiento extremadamente rápido, reduce la difusión de dopantes. | Limitado a tratamientos de superficie, requiere equipo especializado. |
Descubra la mejor técnica de recocido para sus necesidades de semiconductores: contacte a nuestros expertos hoy !