El pulverizado de magnetrón por impulsos de corriente continua (pulverizado por impulsos de corriente continua) es una variante avanzada del pulverizado de magnetrón, una técnica de deposición física de vapor (PVD) utilizada para crear películas finas sobre sustratos.A diferencia del sputtering de magnetrón de CC tradicional, que utiliza una corriente continua, el sputtering de pulsos de CC aplica una fuente de alimentación de CC pulsada al material objetivo.Este método combina las ventajas de altas velocidades de deposición y un control preciso de las propiedades de la película, lo que lo hace especialmente eficaz para depositar películas finas de alta calidad, sobre todo en materiales difíciles de bombardear, como dieléctricos o aislantes.La potencia pulsada ayuda a reducir la formación de arcos y el sobrecalentamiento, problemas habituales en el sputtering de CC tradicional, mejorando así la calidad de la película y la estabilidad del proceso.
Explicación de los puntos clave:
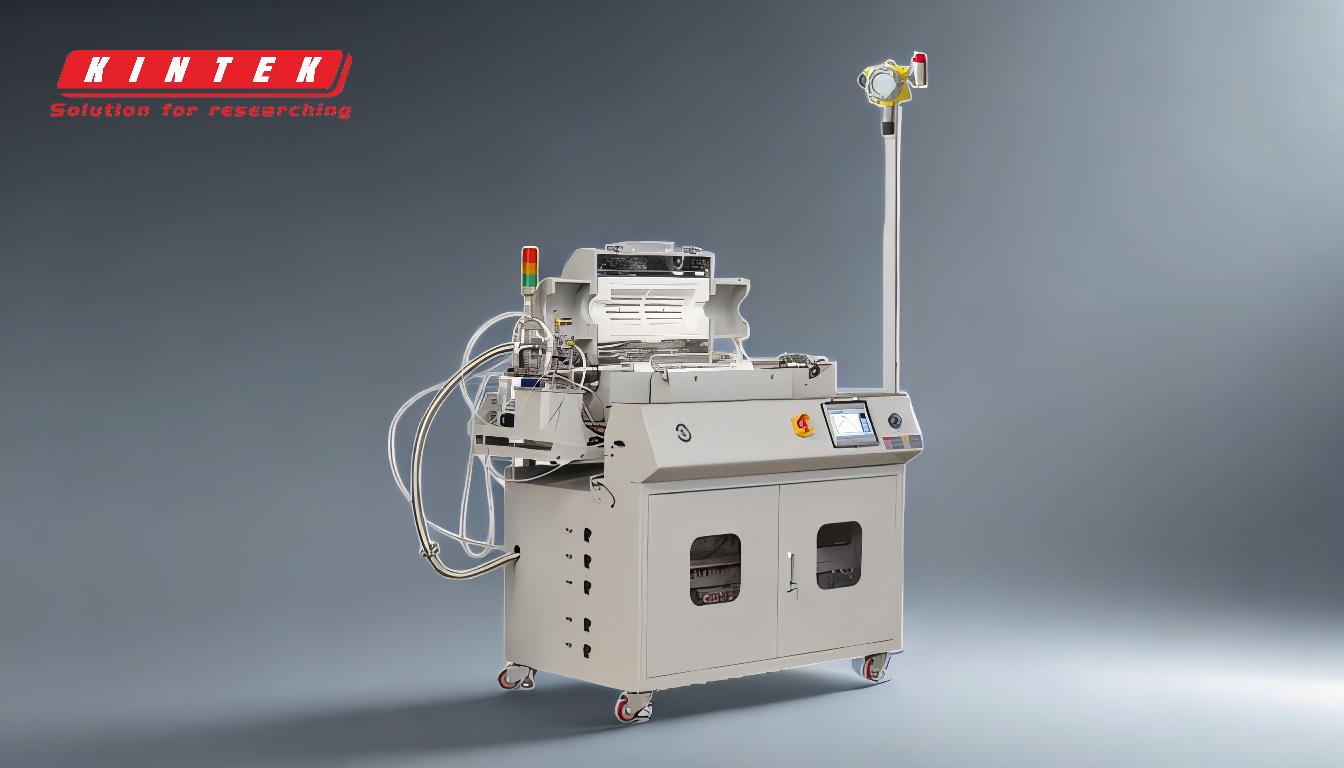
-
Principio básico del sputtering por magnetrón:
- El pulverizado con magnetrón es un método de PVD basado en plasma en el que un material objetivo es bombardeado con iones en una cámara de vacío, lo que provoca la expulsión de átomos que se depositan sobre un sustrato.
- El proceso implica el uso de un campo magnético para confinar los electrones cerca del objetivo, aumentando la ionización del gas de pulverización catódica (normalmente argón) y mejorando la eficacia del proceso de pulverización catódica.
- Esta técnica es conocida por sus altas velocidades de deposición, la excelente calidad de la película y la capacidad de funcionar a bajas presiones (alrededor de 0,1 Pa).
-
Introducción al pulverizado con magnetrón de impulsos de corriente continua:
- La pulverización catódica por impulsos de CC es una modificación de la pulverización catódica por magnetrón de CC tradicional, en la que se utiliza una fuente de alimentación de CC por impulsos en lugar de una fuente de CC continua.
- La alimentación por impulsos alterna entre estados de alta y baja tensión, lo que ayuda a controlar la acumulación de calor y reduce la formación de arcos, un problema habitual en el sputtering de materiales aislantes o dieléctricos.
- Este método es especialmente útil para depositar películas finas de materiales propensos a la carga o la formación de arcos, como óxidos, nitruros y otros aislantes.
-
Ventajas del sputtering por impulsos de corriente continua:
- Arco reducido:La naturaleza pulsante de la fuente de alimentación minimiza el arco eléctrico, que puede dañar el objetivo y degradar la calidad de la película.
- Calidad de película mejorada:Mediante el control de los impulsos de potencia, el sputtering por impulsos de corriente continua produce películas más densas y uniformes con menos defectos.
- Versatilidad:Este método puede utilizarse para depositar una amplia gama de materiales, incluidas películas conductoras, aislantes y dieléctricas, lo que lo hace adecuado para aplicaciones en microelectrónica, óptica y semiconductores.
-
Mecanismo del proceso:
- En el pulverizado por impulsos de corriente continua, el blanco se conecta a una fuente de alimentación de corriente continua pulsada, que alterna entre estados de tensión positiva y negativa.
- Durante el pulso negativo, los iones del plasma se aceleran hacia el blanco, provocando la pulverización catódica de los átomos del blanco.
- Durante el pulso positivo, el blanco se descarga brevemente, evitando la acumulación de carga y reduciendo el riesgo de arco.
- Los átomos pulverizados viajan a través de la cámara de vacío y se depositan sobre el sustrato, formando una fina película.
-
Aplicaciones del pulverizado con magnetrón de impulsos de corriente continua:
- Microelectrónica:Se utiliza para depositar películas dieléctricas y de nitruro en la fabricación de semiconductores.
- Recubrimientos ópticos:Ideal para crear películas finas con propiedades ópticas específicas, como revestimientos antirreflectantes o reflectantes.
- Revestimientos decorativos y funcionales:Se aplica en industrias que requieren revestimientos duraderos y de alta calidad con un espesor y una uniformidad precisos.
-
Comparación con otras técnicas de sputtering:
- Sputtering por magnetrón DC:La alimentación continua de CC puede provocar arcos eléctricos y sobrecalentamiento, especialmente con materiales aislantes.
- Pulverización catódica por magnetrón de RF:Adecuado para materiales no conductores, pero normalmente tiene tasas de deposición inferiores en comparación con el sputtering por impulsos de corriente continua.
- Pulso DC:Combina las ventajas del sputtering DC y RF, ofreciendo altas velocidades de deposición, arco eléctrico reducido y compatibilidad con una amplia gama de materiales.
-
Desarrollos futuros:
- Las investigaciones en curso pretenden optimizar los parámetros del pulso (frecuencia, ciclo de trabajo y voltaje) para mejorar aún más la calidad de la película y la eficiencia de la deposición.
- Se espera que los avances en la tecnología de alimentación eléctrica y control de procesos amplíen las aplicaciones del pulverizado por impulsos de corriente continua en campos emergentes como la electrónica flexible y el almacenamiento de energía.
Al aprovechar las ventajas exclusivas del sputtering magnetrónico de impulsos de corriente continua, los fabricantes pueden lograr una deposición superior de películas finas con mayor precisión y fiabilidad, lo que la convierte en una técnica valiosa en la ciencia y la ingeniería de materiales modernas.
Tabla resumen:
Aspecto | Detalles |
---|---|
Principio básico | Método PVD basado en plasma que utiliza un campo magnético para mejorar la eficacia del sputtering. |
Ventaja clave | Reduce el arco eléctrico y el sobrecalentamiento, mejorando la calidad de la película y la estabilidad del proceso. |
Aplicaciones | Microelectrónica, revestimientos ópticos, revestimientos decorativos y funcionales. |
Comparación | Combina las ventajas del sputtering DC y RF, ofreciendo versatilidad y eficiencia. |
Desarrollos futuros | Optimización de los parámetros de pulso y expansión a la electrónica flexible. |
Libere el potencial del sputtering por magnetrón de impulsos de corriente continua para sus proyectos. póngase en contacto con nuestros expertos hoy mismo ¡!