El sputtering de corriente continua y el sputtering de magnetrón de corriente continua son técnicas de deposición física de vapor (PVD) utilizadas para crear películas finas, pero difieren significativamente en sus mecanismos, eficacia y aplicaciones.El sputtering de corriente continua utiliza una fuente de corriente continua para ionizar moléculas de gas que bombardean un material conductor, provocando la expulsión de átomos que se depositan sobre un sustrato.Por otro lado, el pulverizado con magnetrón de corriente continua incorpora un campo magnético cerca del objetivo, que atrapa electrones y aumenta la densidad del plasma, lo que permite mayores velocidades de deposición y un mejor control de las propiedades de la película.Mientras que el sputtering DC es rentable y adecuado para materiales conductores, el sputtering magnetrón DC es más eficaz, funciona a presiones más bajas y es ideal para sustratos más grandes.Además, el sputtering magnetrónico de corriente continua minimiza el daño al sustrato debido al confinamiento del plasma, lo que lo convierte en la opción preferida para aplicaciones de películas finas de alta calidad.
Explicación de los puntos clave:
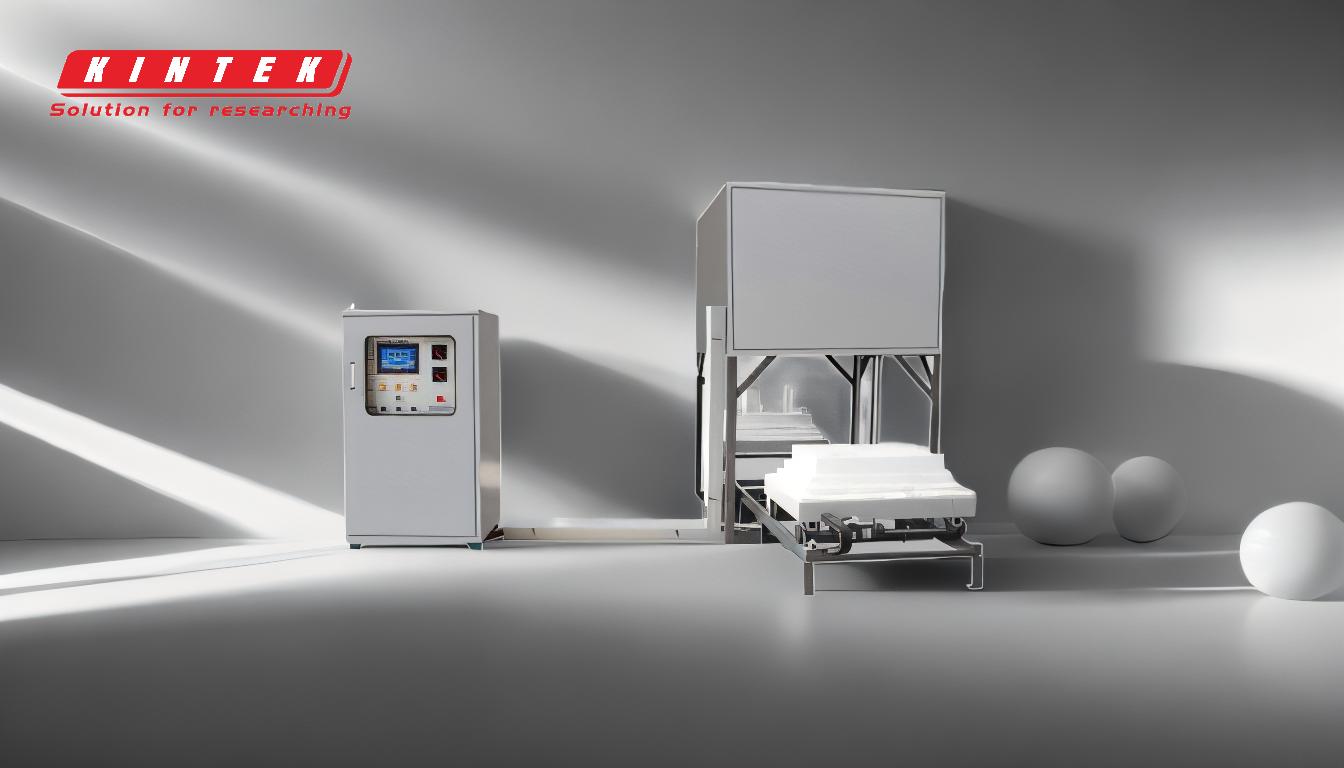
-
Fuente de alimentación y compatibilidad de materiales:
- Pulverización catódica DC:Utiliza una fuente de alimentación de corriente continua y se adapta principalmente a materiales conductores como los metales.Es rentable y eficaz para aplicaciones a gran escala.
- Pulverización catódica con magnetrón de corriente continua:También utiliza una fuente de corriente continua, pero incorpora un campo magnético, lo que la hace más versátil.Puede tratar tanto materiales conductores como no conductores, aunque los materiales no conductores son más adecuados para el sputtering por magnetrón de RF.
-
Mecanismo de pulverización catódica:
- Pulverización catódica DC:Los iones de gas cargados positivamente se aceleran hacia el material objetivo, provocando la pulverización de los átomos y su depósito en el sustrato.
- Pulverización catódica con magnetrón de corriente continua:Se introduce un campo magnético cerca del blanco, que atrapa los electrones y aumenta la densidad del plasma.Este plasma confinado mejora el proceso de sputtering, dando lugar a mayores velocidades de deposición y a una mejor calidad de la película.
-
Velocidad de deposición y eficiencia:
- Pulverización catódica DC:Ofrece altas velocidades de deposición, pero es menos eficaz que el sputtering por magnetrón.Es adecuado para sustratos grandes, pero puede requerir presiones de cámara más elevadas.
- Pulverización catódica con magnetrón de corriente continua:Proporciona tasas de deposición significativamente más altas debido a la capacidad del campo magnético para confinar electrones y aumentar la ionización.Funciona a presiones más bajas, por lo que es más eficaz y adecuado para sustratos más grandes.
-
Confinamiento del plasma y daños en el sustrato:
- Pulverización catódica DC:El plasma está menos confinado, lo que puede provocar daños en el sustrato debido al bombardeo de electrones.Esto limita su uso en aplicaciones que requieren películas finas de alta calidad.
- Pulverización catódica con magnetrón de corriente continua:El campo magnético confina el plasma cerca del objetivo, evitando que los electrones bombardeen el sustrato.El resultado es un menor daño del sustrato y películas de mayor calidad.
-
Aplicaciones e idoneidad:
- Pulverización catódica DC:El más adecuado para aplicaciones con materiales conductores y producción a gran escala en las que la rentabilidad es una prioridad.
- Pulverización catódica con magnetrón de corriente continua:Ideal para aplicaciones que requieren películas finas de alta calidad, como en las industrias óptica y de semiconductores.También es más eficiente para sustratos más grandes y puede funcionar a presiones más bajas, reduciendo los riesgos de contaminación.
-
Requisitos de presión:
- Pulverización catódica DC:A menudo requiere presiones de cámara más altas, que pueden ser más difíciles de mantener y pueden provocar impurezas en la película.
- Pulverización catódica con magnetrón de corriente continua:Funciona a presiones más bajas debido a la alta eficacia de ionización del plasma confinado, lo que da lugar a procesos de deposición más limpios y controlados.
-
Coste y complejidad:
- Pulverización catódica DC:Más sencillo y rentable, lo que lo convierte en una opción popular para aplicaciones industriales.
- Sputtering por magnetrón DC:Más complejo debido a la adición de campos magnéticos, pero el aumento de la eficacia y la calidad de la película suelen justificar el mayor coste.
En resumen, aunque tanto el sputtering DC como el sputtering magnetrón DC son técnicas de PVD eficaces, la adición de un campo magnético en el sputtering magnetrón DC mejora significativamente las velocidades de deposición, la calidad de la película y la eficiencia, convirtiéndola en la opción preferida para aplicaciones de alto rendimiento.
Tabla resumen:
Aspecto | Sputtering DC | Sputtering de magnetrón de CC |
---|---|---|
Fuente de energía | Fuente de corriente continua | Fuente de corriente continua con campo magnético |
Compatibilidad de materiales | Materiales principalmente conductores (por ejemplo, metales) | Materiales conductores y no conductores (los no conductores mejor con magnetrón de RF) |
Mecanismo | Los iones de gas bombardean el objetivo, expulsando átomos para su deposición | El campo magnético atrapa los electrones, aumentando la densidad del plasma y la eficacia del sputtering. |
Tasas de deposición | Altas pero menos eficientes | Significativamente mayor debido al plasma confinado |
Requisitos de presión | Presiones de cámara más altas | Funciona a presiones más bajas |
Daños al sustrato | Mayor riesgo debido a un plasma menos confinado | Mínimo debido al plasma confinado |
Aplicaciones | Producción a gran escala, rentable para materiales conductores | Películas finas de alta calidad, semiconductores, óptica y sustratos de mayor tamaño |
Coste y complejidad | Más sencillo y rentable | Más complejo pero justifica el coste con una mayor eficacia y calidad de la película |
¿Necesita ayuda para elegir el método de sputtering adecuado para su aplicación? Póngase en contacto con nuestros expertos hoy mismo ¡!