El revestimiento de un horno de inducción es un componente crítico fabricado con materiales refractarios, diseñado para contener el metal fundido, aislarlo de la estructura exterior del horno y proteger el cuerpo del horno durante su funcionamiento.Es esencial para mantener la eficacia y longevidad del horno, especialmente cuando se funden metales como el aluminio, que requieren revestimientos especializados debido a su alta frecuencia, vibración y penetrabilidad.La calidad del revestimiento influye directamente en el rendimiento del horno, y su vida útil se mide por el número de ciclos térmicos que puede soportar antes de requerir reparación o sustitución.
Explicación de los puntos clave:
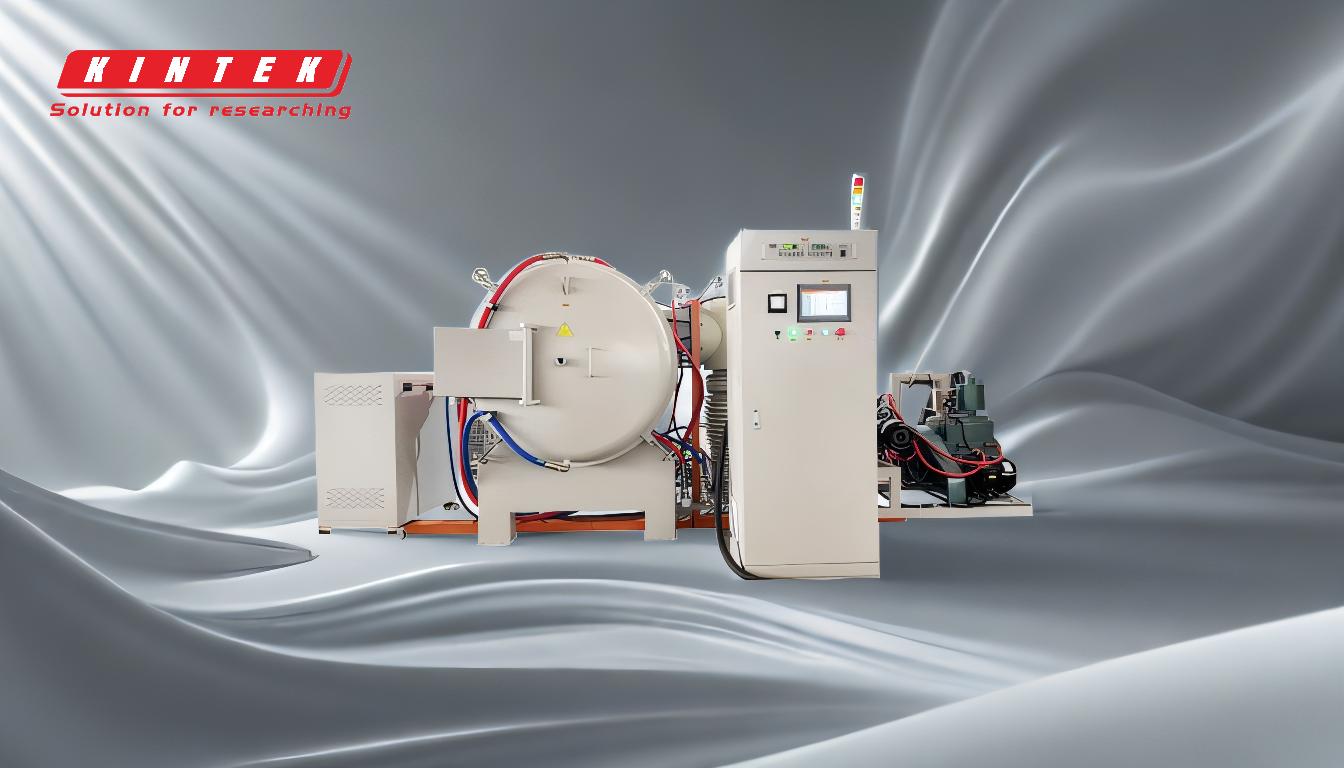
-
Finalidad del forro:
- Contención de metal fundido:La función principal del revestimiento es mantener el metal fundido firmemente dentro del crisol, evitando fugas y garantizando un funcionamiento seguro.
- Aislamiento de la estructura exterior:El revestimiento actúa como barrera, impidiendo el contacto directo entre el metal fundido y los componentes exteriores del horno, como la bobina de inducción, que de otro modo podrían resultar dañados.
- Protección del cuerpo del horno:Al aislar el cuerpo del horno de las temperaturas extremas y de las reacciones químicas, el revestimiento prolonga la vida útil del horno.
-
Composición y materiales:
- Materiales refractarios:El revestimiento suele estar fabricado con materiales refractarios de alta calidad capaces de soportar temperaturas extremas y la corrosión química.Estos materiales se eligen en función del tipo de metal que se funde.
- Revestimientos especializados para aluminio:Debido a las propiedades únicas del aluminio (alta frecuencia, vibración y penetrabilidad), se requieren revestimientos especiales para los hornos de fusión de aluminio.Estos revestimientos están diseñados para soportar más de 300 ciclos térmicos.
-
Importancia en los hornos de inducción:
- Componente crítico:El revestimiento se considera la parte más importante del horno de inducción, ya que su calidad afecta directamente a la eficiencia del horno y a la calidad del metal fundido.
- Vida útil:La vida útil del revestimiento, conocida como vida útil del revestimiento, es un parámetro de rendimiento clave.Indica el número de ciclos térmicos que puede soportar el revestimiento antes de degradarse y necesitar reparación o sustitución.
-
Degradación y mantenimiento:
- Degradación a lo largo del tiempo:Los revestimientos refractarios se degradan debido al estrés térmico, las reacciones químicas y el desgaste mecánico.La supervisión y el mantenimiento periódicos son esenciales para garantizar un rendimiento óptimo.
- Reparación y sustitución:Cuando el revestimiento llega al final de su vida útil, debe repararse o sustituirse para mantener la eficacia y la seguridad del horno.
-
Impacto en la eficiencia de la producción:
- Calidad del revestimiento:Un revestimiento de alta calidad garantiza un funcionamiento sin problemas, reduce el tiempo de inactividad y mejora la eficacia general del proceso de producción.
- Consideraciones económicas:Aunque los revestimientos de alta calidad pueden tener un coste inicial más elevado, ofrecen un mejor rendimiento y una vida útil más larga, lo que supone un ahorro de costes a largo plazo.
En resumen, el revestimiento de un horno de inducción es un componente vital que garantiza la fusión segura y eficaz de los metales.Su diseño, selección de materiales y mantenimiento son cruciales para lograr un rendimiento óptimo del horno y prolongar su vida útil.
Cuadro sinóptico:
Aspecto clave | Detalles |
---|---|
Finalidad | Contiene el metal fundido, lo aísla de la estructura exterior, protege el cuerpo del horno. |
Materiales | Materiales refractarios de alta calidad; revestimientos especializados para aluminio. |
Importancia | Crítico para la eficiencia del horno, la calidad del metal fundido y la vida útil del revestimiento. |
Degradación y mantenimiento | Se degrada por el estrés térmico y las reacciones químicas; requiere un mantenimiento regular. |
Impacto en la producción | Los revestimientos de alta calidad reducen el tiempo de inactividad, mejoran la eficiencia y ahorran costes. |
Optimice el rendimiento de su horno con el revestimiento adecuado. contacte con nuestros expertos hoy mismo ¡!