El proceso de sinterización es un método fundamental en la ciencia de los materiales y la fabricación, utilizado para crear productos sólidos y duraderos a partir de materiales en polvo mediante calentamiento y enfriamiento controlados.Comprende varias etapas, como la preparación de las materias primas, la compactación, el calentamiento para facilitar la unión de las partículas y el enfriamiento para solidificar el producto final.Este proceso garantiza la formación de una estructura cohesiva de baja porosidad con propiedades mecánicas mejoradas.A continuación se explican en detalle los pasos y fases clave de la sinterización, centrándose en las reacciones químicas y transformaciones físicas que se producen durante cada etapa.
Explicación de los puntos clave:
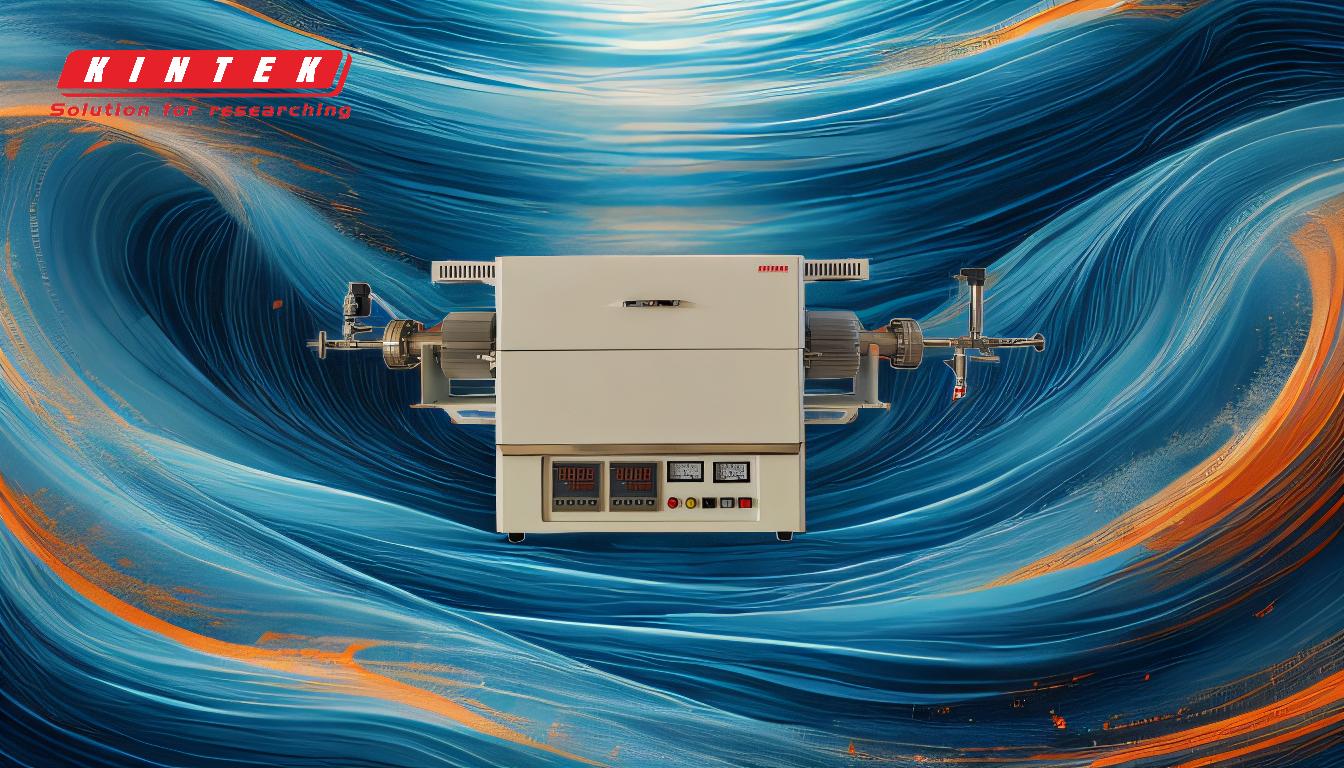
-
Preparación de las materias primas
- El proceso de sinterización comienza con la preparación de las materias primas, normalmente en forma de polvo.
- Estos polvos se mezclan con aditivos como agentes de acoplamiento, aglutinantes o defloculantes para mejorar la uniformidad y facilitar la unión.
- A menudo, la mezcla se seca por pulverización para crear una lechada, a la que luego se da la forma deseada.
- Reacciones químicas:Durante esta etapa, no se producen reacciones químicas significativas, pero la uniformidad de la mezcla es fundamental para garantizar una sinterización consistente posteriormente.
-
Compactación (compactación del polvo)
- El polvo mezclado se compacta mediante presión mecánica, como el prensado en molde frío o caliente, para formar una "pieza verde".
- La compactación elimina los huecos y garantiza que el material tenga una densidad uniforme, lo que es esencial para conseguir un producto final resistente.
- Reacciones químicas:En esta fase, las partículas pueden formar soldaduras en frío, pero no se producen cambios químicos importantes.
-
Calentamiento (sinterización o cocción)
- La pieza verde se calienta en un entorno controlado, normalmente en un horno de sinterización o un horno, a una temperatura justo por debajo del punto de fusión del material.
-
Durante el calentamiento, las partículas experimentan una difusión que conduce a la formación de cuellos y a la densificación.Aquí es donde se producen las principales reacciones químicas y transformaciones físicas.
- Formación del cuello:Las partículas se unen en sus puntos de contacto, formando cuellos que crecen a medida que los átomos se difunden a través de las superficies de las partículas.
- Densificación:Los huecos entre las partículas se reducen y el material se vuelve más denso y resistente.
- Sinterización en fase líquida (LPS):En algunos casos, puede formarse una fase líquida para acelerar la fusión y densificación de las partículas.
- Reacciones químicas:Dependiendo del material, pueden producirse oxidaciones, reducciones o transformaciones de fase.Por ejemplo, en la sinterización de cerámica, el aglutinante puede descomponerse y las partículas cerámicas pueden fundirse.
-
Enfriamiento y solidificación
- Tras la sinterización, el material se enfría gradualmente para permitir que se solidifique en una estructura rígida y cohesiva.
- El enfriamiento controlado evita tensiones térmicas y garantiza que el material conserve las propiedades deseadas.
- Reacciones químicas:Durante el enfriamiento no se producen reacciones químicas significativas, pero la microestructura del material se estabiliza.
-
Tratamiento posterior al sinterizado
- En algunos casos, pueden aplicarse tratamientos adicionales como mecanizado, pulido o revestimiento para conseguir las especificaciones finales del producto.
- Reacciones químicas:Los tratamientos posteriores al sinterizado son principalmente mecánicos o superficiales y no implican cambios químicos significativos.
Importancia de los parámetros controlados:
- Temperatura:El control preciso de la temperatura es crucial para garantizar una unión adecuada de las partículas sin provocar una fusión completa.
- Atmósfera:El entorno de sinterización (por ejemplo, vacío, gas inerte o atmósfera reductora) puede influir en las reacciones químicas y las propiedades finales del material.
- Tiempo:La duración del calentamiento y del enfriamiento afecta al grado de densificación y al desarrollo de la microestructura.
Aplicaciones de la sinterización:
- Metales:Se utiliza para fabricar componentes de gran solidez y resistencia al desgaste, como engranajes y cojinetes.
- Cerámica:Se utiliza para crear productos duraderos y resistentes al calor, como baldosas y aislantes.
- Materiales compuestos:La sinterización se emplea para combinar distintos materiales, como metales y cerámicas, para conseguir propiedades únicas.
Al comprender el proceso de sinterización y sus etapas, los fabricantes pueden optimizar la producción de materiales de alta calidad con propiedades adaptadas a aplicaciones específicas.
Tabla resumen:
Etapa | Acciones clave | Reacciones químicas |
---|---|---|
Preparación de materias primas | Mezcla de polvos con aditivos, secado por pulverización para formar lechada, moldeado. | Sin reacciones significativas; la uniformidad es fundamental. |
Compactación | Prensado en molde frío o caliente para formar una "pieza verde". | Pueden formarse soldaduras en frío; sin cambios químicos importantes. |
Calentamiento (Sinterización) | Calentamiento hasta justo por debajo del punto de fusión; formación de cuellos, densificación, LPS. | Oxidación, reducción o transformaciones de fase (por ejemplo, descomposición del ligante, fusión de partículas). |
Enfriamiento | Enfriamiento gradual para solidificar el material. | No se producen reacciones significativas; la microestructura se estabiliza. |
Tratamiento posterior a la sinterización | Mecanizado, pulido o revestimiento para obtener las especificaciones finales. | Principalmente a nivel mecánico o superficial; sin cambios químicos significativos. |
Optimice su proceso de sinterización para obtener materiales de alta calidad. contacte hoy mismo con nuestros expertos ¡!