Un horno de inducción es un crisol refractario cilíndrico, abierto e inclinable con una bobina de inducción refrigerada por agua instalada alrededor de su pared lateral.Se utiliza principalmente para fundir metales y crear aleaciones con composiciones precisas.El horno funciona generando un campo electromagnético a través de una bobina de cobre hueca, que induce corrientes de Foucault en la carga metálica, produciendo calor directamente dentro del metal.Los principales componentes son una fuente de alimentación, una bobina de inducción, un crisol y diversos sistemas de apoyo, como sistemas de refrigeración, hidráulicos y de control eléctrico.Estos componentes trabajan conjuntamente para garantizar una fusión eficaz y controlada de los metales.
Explicación de los puntos clave:
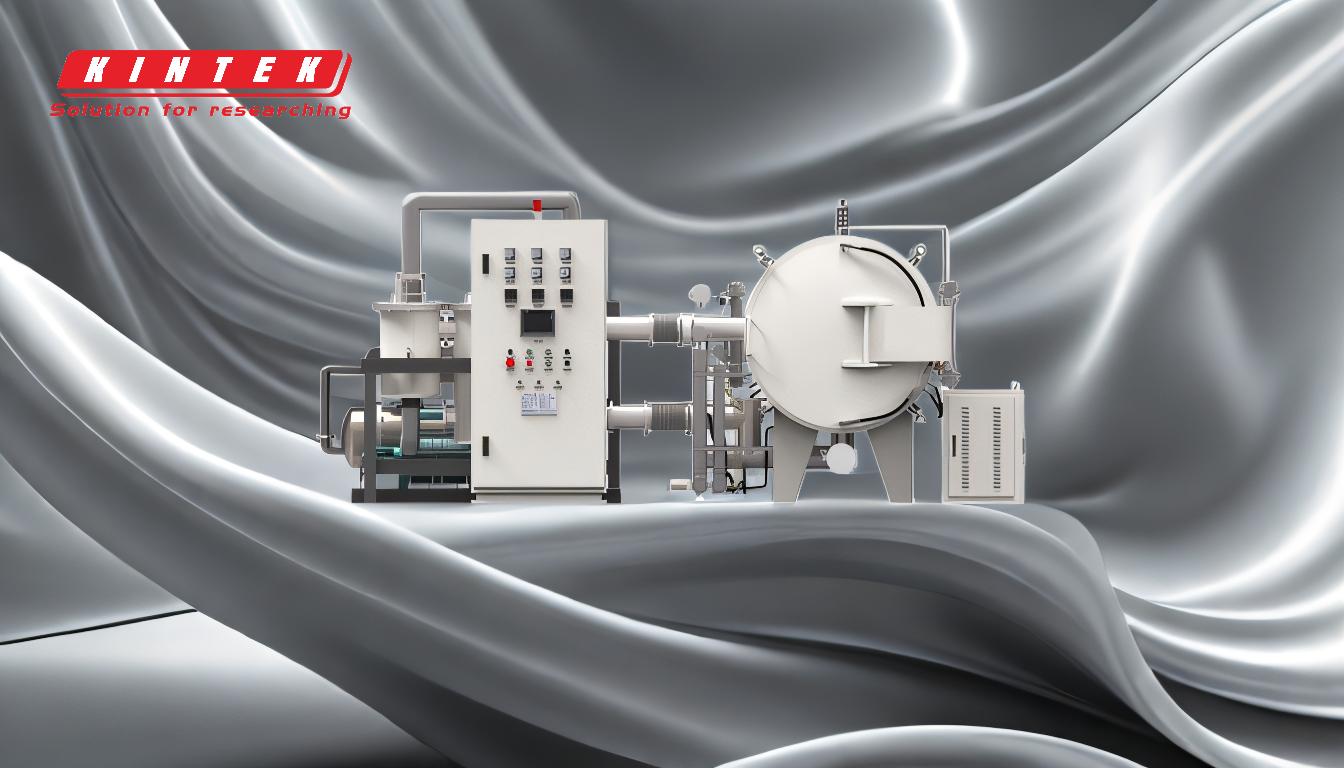
-
Diseño cilíndrico, abierto y basculante:
- Los hornos de inducción suelen tener forma cilíndrica, lo que permite contener y fundir eficazmente las cargas metálicas.
- El diseño de tapa abierta facilita la carga de materiales y la observación del proceso de fusión.
- La característica basculante permite verter el metal fundido en moldes u otros recipientes una vez finalizado el proceso de fusión.
-
Crisol refractario:
- El crisol está hecho de materiales refractarios que pueden soportar temperaturas extremadamente altas sin degradarse.
- Contiene la carga metálica y actúa como el devanado secundario de un transformador, donde la propia carga metálica pasa a formar parte del circuito eléctrico.
-
Bobina de inducción refrigerada por agua:
- La bobina de inducción se instala alrededor de la pared lateral del crisol y suele ser de cobre hueco.
- La bobina se refrigera con agua para evitar el sobrecalentamiento debido a la corriente alterna de alta frecuencia que pasa a través de ella.
- Esta bobina genera el campo electromagnético necesario para inducir corrientes parásitas en la carga metálica.
-
Fuente de alimentación:
- La fuente de alimentación suministra la corriente alterna necesaria a la bobina de inducción.
- En los hornos de inducción de frecuencia media, la fuente de alimentación funciona a frecuencias como 2500 Hz, que son óptimas para calentar y fundir metales con eficacia.
-
Mecanismo de calentamiento por inducción:
- La corriente alterna en la bobina de inducción crea un campo electromagnético fluctuante.
- Este campo induce corrientes de Foucault dentro de la carga metálica conductora, provocando un calentamiento resistivo.
- El calor generado se localiza dentro de la carga metálica, lo que garantiza una fusión rápida y eficaz sin un calentamiento excesivo de la estructura del horno.
-
Sistemas de apoyo:
- Sistema hidráulico:Facilita el mecanismo de inclinación del horno para verter el metal fundido.
- Sistema de refrigeración por agua:Garantiza que la bobina de inducción y otros componentes se mantengan a temperaturas de funcionamiento seguras.
- Sistema de control eléctrico:Gestiona la fuente de alimentación y otros componentes eléctricos para mantener unas condiciones de fusión óptimas.
-
Componentes específicos de los hornos de inducción para fusión de aluminio:
- Fuente de alimentación de frecuencia intermedia:Funciona a 2500 Hz, adecuado para fundir aluminio.
- Condensador de compensación:Ayuda a mantener la eficiencia de la fuente de alimentación.
- Cable refrigerado por agua:Conecta la alimentación eléctrica a la bobina de inducción, garantizando una transmisión eficaz de la potencia.
- Reductor:Parte del sistema hidráulico, que ayuda a la inclinación controlada del horno.
-
Transformador Analogía:
- El horno de inducción funciona de forma similar a un transformador, en el que la bobina de inducción actúa como devanado primario y la carga metálica del crisol actúa como devanado secundario.
- Las corrientes inducidas en la carga metálica generan calor, que es el mecanismo principal para fundir el metal.
-
Generación y contención del calor:
- El calor se genera directamente dentro de la carga metálica, lo que hace que el proceso sea muy eficaz.
- El crisol refractario y el serpentín refrigerado por agua garantizan la contención y gestión eficaz del calor, evitando daños en la estructura del horno.
-
Aplicaciones:
- Los hornos de inducción se utilizan mucho en acerías y fundiciones especializadas.
- Son especialmente apreciados por su capacidad para producir aleaciones con composiciones exactas y por su eficacia para fundir metales como el aluminio.
En resumen, la estructura de un horno de inducción está diseñada para optimizar el proceso de fusión mediante una eficiente generación y contención del calor.Los componentes clave trabajan en armonía para garantizar un control preciso del proceso de fusión, lo que hace que los hornos de inducción sean indispensables en las aplicaciones metalúrgicas modernas.
Tabla resumen:
Componente | Función |
---|---|
Crisol cilíndrico | Contiene y funde eficazmente cargas metálicas; inclinable para verter. |
Crisol refractario | Soporta altas temperaturas; actúa como devanado secundario en el circuito. |
Bobina de inducción refrigerada por agua | Genera un campo electromagnético; induce corrientes de Foucault para el calentamiento. |
Fuente de alimentación | Proporciona corriente alterna para el calentamiento por inducción. |
Sistema hidráulico | Permite la inclinación para verter metal fundido. |
Sistema de refrigeración por agua | Evita el sobrecalentamiento de los componentes. |
Sistema de control eléctrico | Gestiona el suministro eléctrico y las condiciones de fusión. |
Descubra cómo un horno de inducción puede revolucionar su proceso de fusión de metales. contacte con nosotros para recibir asesoramiento experto.