El sinterizado por plasma de chispa (SPS) es una técnica moderna de sinterización que reduce significativamente el tiempo necesario para la sinterización en comparación con los métodos convencionales.El proceso consiste normalmente en mantener el material a la temperatura de sinterización durante sólo 5 o 10 minutos, mientras que la sinterización convencional puede durar horas.Esta eficacia se consigue mediante el uso de corriente continua pulsada (CC) que genera altas temperaturas y plasma entre las partículas, lo que facilita una rápida densificación.El proceso también permite temperaturas de sinterización más bajas y da lugar a materiales con una alta densidad, a menudo superior al 99%.El SPS es versátil, capaz de sinterizar una amplia gama de materiales, incluidos metales, cerámica y materiales compuestos, y es conocido por su eficiencia energética y sus beneficios medioambientales.
Explicación de los puntos clave:
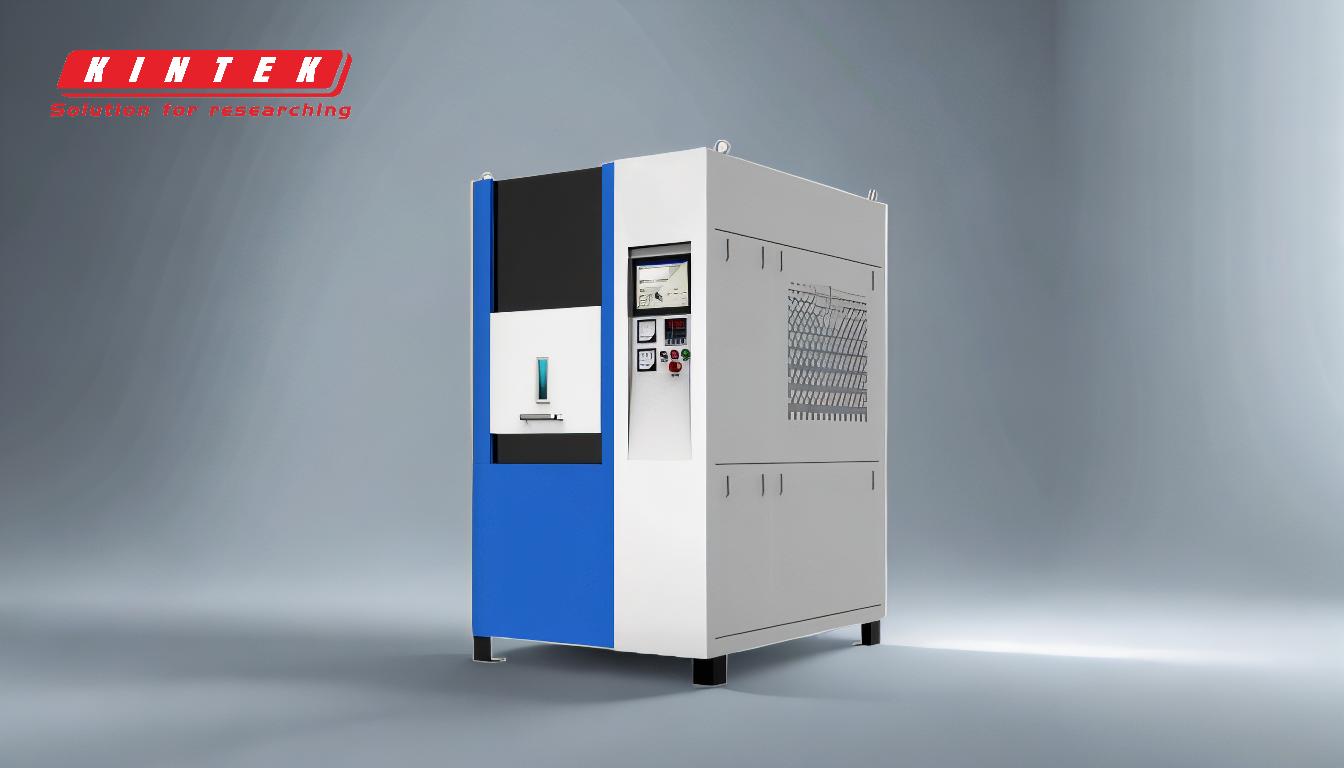
-
Reducción del tiempo de sinterización:
- Explicación: El SPS reduce drásticamente el tiempo de sinterización a sólo 5 a 10 minutos a la temperatura de sinterización, en comparación con varias horas en los métodos de sinterización convencionales.Esto se debe principalmente a las rápidas velocidades de calentamiento y enfriamiento facilitadas por la corriente continua pulsada.
- Implicaciones: Esta reducción de tiempo no sólo acelera el proceso de producción, sino que también minimiza el riesgo de degradación del material que puede producirse durante la exposición prolongada a altas temperaturas.
-
Mecanismo de acción:
- Explicación: El proceso SPS utiliza una corriente continua pulsada que crea un plasma de chispas entre las partículas, alcanzando temperaturas de hasta 10.000°C. Esta alta temperatura hace que la superficie de las partículas se funda y se fusione, formando estructuras densas conocidas como "cuellos".Esta alta temperatura hace que la superficie de las partículas se funda y se fusione, formando estructuras densas conocidas como "cuellos".
- Implicaciones: La formación de estos cuellos es crucial para conseguir materiales de alta densidad, que a menudo superan el 99% de densidad, lo que es esencial para aplicaciones que requieren materiales resistentes y duraderos.
-
Temperaturas de sinterización más bajas:
- Explicación: El SPS permite sinterizar a temperaturas varios cientos de grados inferiores a las requeridas en los métodos convencionales.Esto se consigue gracias a los efectos combinados del campo eléctrico y el prensado en caliente.
- Implicaciones: Las temperaturas de sinterización más bajas reducen el consumo de energía y minimizan el estrés térmico en los materiales, lo que conduce a productos de mejor calidad y más consistentes.
-
Versatilidad en el procesamiento de materiales:
- Explicación: El SPS puede utilizarse para sinterizar una amplia variedad de materiales, incluidos metales, cerámicas, materiales compuestos, nanomateriales a granel, materiales amorfos a granel y materiales gradientes.
- Implicaciones: Esta versatilidad hace del SPS una técnica valiosa en diversas industrias, desde la aeroespacial a la ingeniería biomédica, donde se requieren diferentes propiedades de los materiales.
-
Eficiencia energética y beneficios medioambientales:
- Explicación: Las rápidas velocidades de calentamiento y enfriamiento, junto con las bajas temperaturas de sinterización, contribuyen a la eficiencia energética del proceso SPS.Además, el proceso es respetuoso con el medio ambiente, ya que reduce el consumo total de energía y minimiza los residuos.
- Implicaciones: Estas ventajas hacen del SPS una opción atractiva para las industrias que buscan reducir su huella medioambiental al tiempo que mantienen altos estándares de producción.
-
Microestructura controlada:
- Explicación: El SPS permite controlar con precisión la microestructura del material sinterizado, lo que es crucial para conseguir las propiedades mecánicas y físicas deseadas.
- Implicaciones: Este control es especialmente importante en aplicaciones avanzadas en las que se requieren características específicas del material, como en el desarrollo de cerámicas de alto rendimiento o materiales compuestos avanzados.
En resumen, el sinterizado por plasma de chispa ofrece un método rápido, eficaz y versátil para sinterizar una amplia gama de materiales.Su capacidad para conseguir materiales de alta densidad con microestructuras controladas, a la vez que funciona a temperaturas más bajas y con un consumo energético reducido, lo convierte en una técnica muy ventajosa en la ciencia y la ingeniería de materiales modernas.
Cuadro sinóptico:
Característica clave | Descripción | Implicaciones |
---|---|---|
Reducción del tiempo de sinterización | Sinterización en 5-10 minutos frente a las horas de los métodos convencionales. | Producción más rápida, menor degradación del material. |
Mecanismo de acción | La corriente continua pulsada crea plasma, fundiendo las superficies de las partículas para formar cuellos densos. | Alcanza una densidad >99% para obtener materiales resistentes y duraderos. |
Temperaturas de sinterización más bajas | Funciona a temperaturas cientos de grados más bajas que los métodos convencionales. | Reduce el consumo de energía, minimiza el estrés térmico y mejora la consistencia del producto. |
Versatilidad | Sinteriza metales, cerámicas, materiales compuestos y mucho más. | Ideal para aplicaciones aeroespaciales, biomédicas y de materiales avanzados. |
Eficiencia energética | El calentamiento/enfriamiento rápido y las temperaturas más bajas reducen el consumo de energía. | Respetuoso con el medio ambiente y con un mínimo de residuos. |
Microestructura controlada | Control preciso de la microestructura del material. | Permite adaptar las propiedades mecánicas y físicas para aplicaciones avanzadas. |
¿Está listo para transformar el procesamiento de sus materiales? Póngase en contacto con nosotros para saber cómo SPS puede beneficiar a sus proyectos.