El fallo de los revestimientos de hornos se debe principalmente a la expansión térmica y al desconchamiento, que se producen debido a las tasas diferenciales de expansión y contracción de los materiales refractarios en condiciones térmicas variables.Este fenómeno provoca grietas y desconchados que, si no se tratan, pueden provocar el fallo estructural del revestimiento del horno.Comprender los mecanismos de estos fallos es crucial para seleccionar los materiales adecuados y aplicar estrategias de mantenimiento que prolonguen la vida útil de los revestimientos de hornos.
Explicación de los puntos clave:
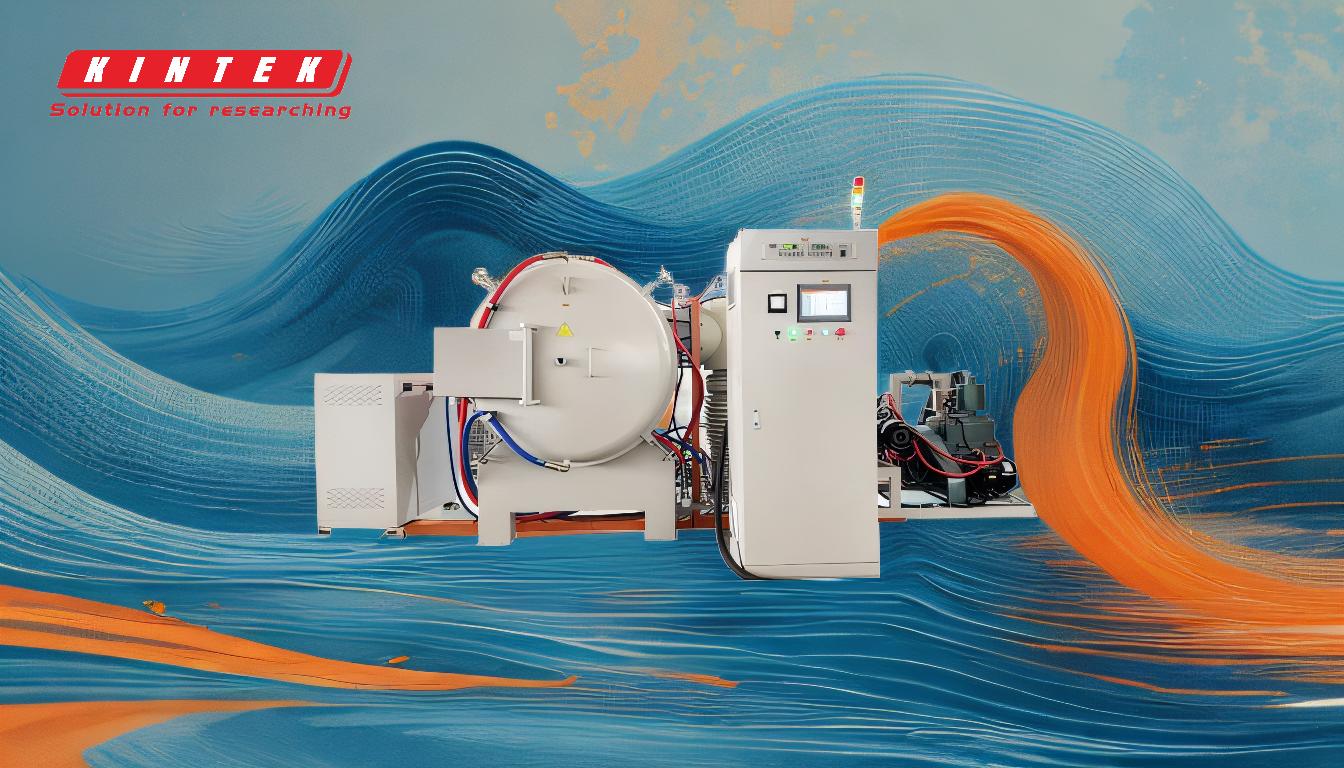
-
Expansión y contracción térmicas:
- Mecanismo: Los materiales refractarios se dilatan cuando se calientan y se contraen cuando se enfrían.Los coeficientes de dilatación térmica de los distintos materiales varían, lo que significa que se dilatan y contraen a ritmos diferentes.
- Repercusiones: Cuando el horno se somete a ciclos térmicos (calentamiento y enfriamiento), las tasas diferenciales de expansión y contracción pueden provocar tensiones en el revestimiento.Con el tiempo, esta tensión puede provocar la formación de grietas.
-
Desconchamiento:
- Definición: El desconchado se refiere al desprendimiento de fragmentos o capas de la superficie del revestimiento refractario.
- Causas: El desconchamiento suele ser consecuencia directa de las tensiones causadas por la dilatación y contracción térmicas.También puede verse agravado por el desgaste mecánico, el ataque químico o la instalación incorrecta de los materiales refractarios.
- Consecuencias: El desconchamiento expone las capas subyacentes del revestimiento refractario a temperaturas más elevadas y a condiciones térmicas y químicas más severas, acelerando una mayor degradación y pudiendo provocar un fallo catastrófico.
-
Agrietamiento:
- Formación: Pueden formarse grietas debido a los repetidos ciclos térmicos del horno.Estas grietas pueden empezar como microfisuras y agrandarse con el tiempo.
- Consecuencias: Las grietas proporcionan vías para que el calor y los gases corrosivos penetren más profundamente en el revestimiento refractario, provocando un mayor deterioro.También debilitan la integridad estructural del revestimiento, haciéndolo más susceptible a fallos mecánicos.
-
Medidas preventivas:
- Selección de materiales: La elección de materiales refractarios con coeficientes de dilatación térmica compatibles puede minimizar la tensión causada por los ciclos térmicos.
- Consideraciones de diseño: El diseño adecuado del revestimiento del horno, incluyendo el uso de juntas de dilatación y espesores adecuados, puede ayudar a acomodar la expansión y contracción térmica.
- Mantenimiento: La inspección periódica y la reparación oportuna de grietas y zonas agrietadas pueden evitar que problemas menores se conviertan en averías importantes.
-
Reparación y mantenimiento:
- Importancia: La detección y reparación precoz de grietas y zonas desconchadas son cruciales para mantener la integridad del revestimiento del horno.
- Técnicas: Para reparar las zonas dañadas y prolongar la vida útil del revestimiento pueden utilizarse técnicas como el parcheado, el gunitado y la aplicación de revestimientos protectores.
En resumen, el fallo de los revestimientos de hornos se debe principalmente a la dilatación térmica y el desconchado, que provocan grietas y degradación estructural.Para garantizar la longevidad y fiabilidad de los revestimientos de hornos, es esencial comprender estos mecanismos y aplicar las medidas preventivas y de mantenimiento adecuadas.
Cuadro sinóptico:
Factor clave | Descripción | Impacto |
---|---|---|
Expansión térmica | Los materiales refractarios se dilatan y contraen a diferentes velocidades bajo los ciclos térmicos. | Provoca tensiones que provocan grietas y debilitan la estructura del revestimiento. |
Desconchamiento | Los fragmentos se desprenden debido a la tensión, el desgaste o el ataque químico. | Expone las capas subyacentes, acelerando la degradación y arriesgando un fallo catastrófico. |
Agrietamiento | Los ciclos térmicos repetidos hacen que las microfisuras aumenten de tamaño. | Permite que penetren el calor y los gases corrosivos, deteriorando aún más el revestimiento. |
Medidas preventivas | Selección de materiales, diseño y estrategias de mantenimiento adecuados. | Minimiza la tensión, se adapta a los cambios térmicos y evita que los problemas menores se agraven. |
Técnicas de reparación | Parcheado, gunitado y revestimientos protectores. | Prolonga la vida útil del revestimiento reparando las zonas dañadas. |
Protege el revestimiento de su horno contra fallos-. contacte con nuestros expertos para soluciones a medida y estrategias de mantenimiento.