Introducción al sputtering de magnetrón
Descripción general del proceso de sputtering por magnetrón
El sputtering por magnetrón es una sofisticada tecnología de deposición física en fase vapor (PVD) que consiste en la deposición de una fina película sobre un sustrato. Este proceso se lleva a cabo dentro de una cámara de vacío, donde un material objetivo se somete a un plasma de alta energía. El plasma, generado por la combinación de un gas de pulverización catódica y un campo magnético intenso cerca del objetivo, hace que los átomos o moléculas del material objetivo sean expulsados y posteriormente depositados sobre el sustrato.
El campo magnético desempeña un papel crucial en el sputtering por magnetrón, ya que confina el plasma en una región próxima al blanco. Este confinamiento garantiza que los iones energéticos dentro del plasma interactúen principalmente con el material objetivo, minimizando los daños a la fina película en crecimiento sobre el sustrato. El proceso comienza con la evacuación de la cámara para alcanzar condiciones de alto vacío, lo que reduce las presiones de gas de fondo y los posibles contaminantes. A continuación, se introduce el gas de pulverización catódica en la cámara y se regula la presión al rango de miliTorr mediante un sistema de control de precisión.
En esencia, el sputtering por magnetrón es un proceso de deposición basado en plasma en el que los iones golpean el objetivo, provocando la expulsión de átomos. Estos átomos se desplazan por el vacío y se incorporan a la película que crece sobre el sustrato. La compleja interacción entre el campo magnético, el plasma y las condiciones de vacío garantiza la formación precisa y eficaz de películas finas, lo que convierte al sputtering por magnetrón en una técnica versátil y muy utilizada en diversas aplicaciones industriales.
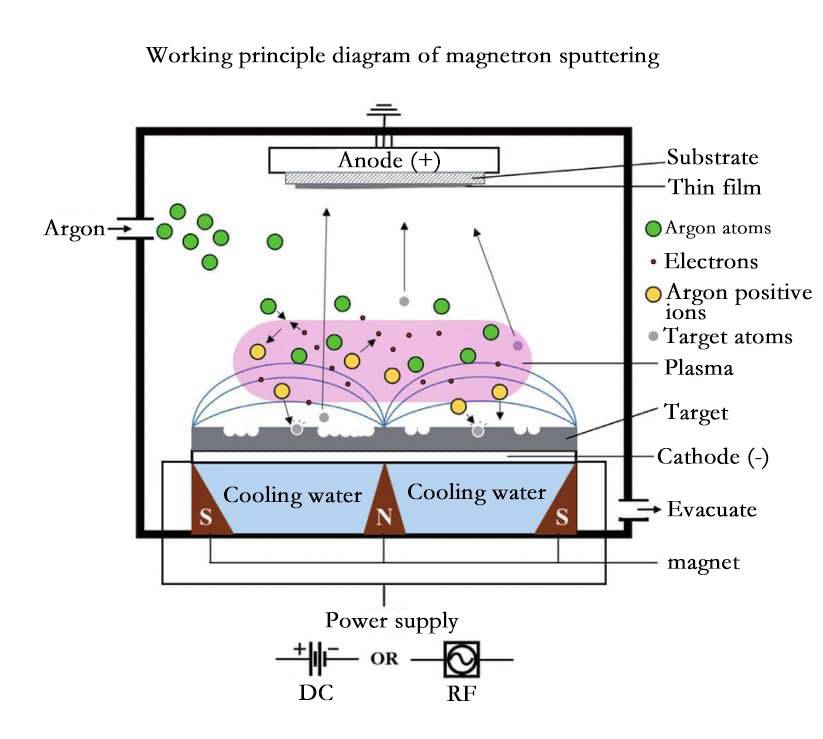
Causas de la formación de chispas en el material objetivo
Oxidación de la superficie del material objetivo
La interacción entre el material objetivo y las moléculas de oxígeno dentro de la cámara de vacío es un factor crítico en el proceso de sputtering. Cuando el material objetivo se expone al oxígeno, puede sufrir una reacción química que da lugar a la formación de óxidos en su superficie. Estos óxidos, aunque inicialmente estables, pueden descomponerse posteriormente en las condiciones de alta energía del proceso de sputtering.
La descomposición de estos óxidos libera gases, que pueden acumularse dentro de la cámara de vacío. Esta acumulación puede provocar cambios de presión localizados y, en casos extremos, causar chispas. Las chispas son el resultado de la liberación repentina de energía del proceso de descomposición, que puede alterar el entorno de sputtering y dañar potencialmente el equipo.
Para mitigar este problema, es esencial controlar la atmósfera dentro de la cámara de vacío. Esto implica mantener una baja concentración de gases reactivos como el oxígeno, garantizando que el entorno permanezca estable y propicio para el proceso de sputtering. Además, la limpieza periódica de la superficie del material objetivo puede evitar la acumulación de óxidos, reduciendo así el riesgo de formación de chispas.
Defectos superficiales en el material objetivo
Los defectos superficiales en el material del cátodo, como pequeñas grietas o agujeros, pueden afectar significativamente al proceso de sputtering. Estas imperfecciones actúan como puntos débiles localizados, donde se concentra la descarga eléctrica durante el sputtering. Esta concentración de descarga puede provocar la formación de fuertes arcos locales, que son descargas eléctricas intensas que pueden inflamar el material objetivo.
La presencia de tales defectos es especialmente problemática porque perturban la distribución uniforme del proceso de sputtering. En lugar de un recubrimiento liso y uniforme, los defectos hacen que la energía se concentre en zonas específicas, lo que provoca un sobrecalentamiento localizado y una posible ignición. Esto no sólo compromete la calidad del revestimiento, sino que también supone un riesgo para la seguridad del equipo y los operarios.
Para mitigar el riesgo de chispas debidas a defectos superficiales, es fundamental inspeccionar y preparar minuciosamente el material objetivo antes de iniciar el proceso de sputtering. Esto incluye identificar y tratar cualquier imperfección de la superficie, asegurando que el material está en condiciones óptimas para la aplicación del revestimiento.
Condiciones de sputtering inadecuadas
Unas condiciones de sputtering inadecuadas pueden contribuir significativamente a la ignición del cátodo durante el proceso de sputtering por magnetrón. Estas condiciones surgen a menudo de una combinación de ajustes de potencia altos o bajos durante el calentamiento del cátodo y campos magnéticos desiguales. Los ajustes de alta potencia pueden causar un calentamiento excesivo, lo que conduce a una rápida vaporización y posterior ignición del material objetivo. Por el contrario, los ajustes de baja potencia pueden provocar un calentamiento insuficiente, causando un sobrecalentamiento localizado y chispas debido a la distribución desigual de la energía.
Además, un campo magnético irregular puede alterar la distribución uniforme del plasma dentro de la cámara de vacío, provocando descargas concentradas en puntos específicos de la superficie del objetivo. Esta concentración de energía puede crear fuertes arcos locales, que son propensos a la ignición. La tabla siguiente resume los efectos de estas condiciones inadecuadas:
Condición | Efecto |
---|---|
Ajuste de alta potencia | Calentamiento excesivo, vaporización rápida e ignición del objetivo |
Baja potencia | Calentamiento insuficiente, sobrecalentamiento localizado y chispas |
Campo magnético irregular | Distribución alterada del plasma, descargas concentradas e ignición |
Para hacer frente a estos problemas es necesario un enfoque meticuloso a la hora de establecer y mantener los parámetros de sputtering, garantizando que la potencia y el campo magnético sean estables y se distribuyan uniformemente.
Soluciones para evitar la ignición del blanco
Garantizar la limpieza de la superficie del blanco
La limpieza de la superficie del cátodo antes del proceso de sputtering es un paso fundamental para evitar la aparición de chispas. Este procedimiento consiste en eliminar meticulosamente la suciedad, los contaminantes y, en particular, los óxidos que puedan haberse formado en la superficie del material del cátodo. Los óxidos son especialmente problemáticos, ya que pueden descomponerse en las condiciones de alta energía del sputtering, liberando gases que pueden provocar arcos localizados e ignición.
Para garantizar una limpieza a fondo, pueden emplearse varios métodos:
- Limpieza mecánica: Utilización de cepillos o materiales abrasivos para eliminar físicamente los contaminantes de la superficie.
- Limpieza química: Sumergir el objetivo en disolventes o ácidos específicos que pueden disolver óxidos y otras impurezas.
- Limpieza ultrasónica: Utilización de ondas ultrasónicas para desalojar y eliminar partículas incrustadas en la superficie.
- Limpieza por haz de iones: Bombardeo de la superficie objetivo con un haz de iones para eliminar los contaminantes a nivel atómico.
La elección del método de limpieza depende de la naturaleza de los contaminantes y de los requisitos específicos del proceso de sputtering. Independientemente del método utilizado, el objetivo es conseguir una superficie prístina libre de cualquier sustancia que pueda interferir en el proceso de sputtering o provocar chispas no deseadas. Esta meticulosa preparación garantiza que el material objetivo esté en condiciones óptimas para la deposición de una película fina de alta calidad.
Control de la atmósfera de la cámara de vacío
Mantener la atmósfera dentro de un rango controlable es crucial para evitar que la concentración de oxígeno y otros gases alcance un nivel inflamable. Para ello es necesario crear y mantener una atmósfera modificada dentro de la cámara de vacío, lo que puede reducir significativamente el riesgo de que se produzcan chispas en el material objetivo durante el sputtering por magnetrón.
Para lograrlo, es esencial contar con un recipiente sellado. Puede tratarse de un tubo de trabajo con juntas especiales diseñadas para su uso en hornos tubulares, o de una retorta utilizada habitualmente en hornos de cámara. Estos recipientes ayudan a aislar el ambiente interno de las influencias externas, lo que permite un control preciso de las condiciones atmosféricas.
El proceso de evacuación de un recipiente reduce el número de átomos y moléculas en su interior. Sin embargo, conseguir un vacío perfecto es prácticamente imposible; incluso en un vacío inferior a 10-7 mbar, sigue habiendo aproximadamente 109 partículas por centímetro cúbico. Esta presencia residual de gas debe gestionarse cuidadosamente para evitar cualquier acumulación de gases inflamables.
KINTEK ofrece una gama de paquetes de gas estándar y equipos asociados diseñados para ayudar a crear y mantener estas atmósferas modificadas. Estos productos no sólo son versátiles, sino también adaptables, lo que permite una mayor flexibilidad operativa. Por ejemplo, los equipos y accesorios opcionales para atmósferas modificadas permiten utilizar los mismos productos para múltiples aplicaciones con diferentes gases, niveles de vacío o incluso sin atmósfera modificada.
Al controlar meticulosamente la atmósfera de la cámara de vacío, se reduce significativamente la probabilidad de ignición del material objetivo durante el sputtering por magnetrón, lo que garantiza un proceso de recubrimiento más seguro y eficaz.
Establezca unas condiciones de sputtering razonables
El ajuste de las condiciones de sputtering es crucial para evitar la ignición y garantizar el rendimiento óptimo del proceso de sputtering por magnetrón. Los ajustes específicos deben adaptarse meticulosamente a las características del material objetivo y a las especificaciones del equipo. Esto implica ajustar parámetros como los niveles de potencia, las configuraciones del campo magnético y las presiones de la cámara de vacío.
Por ejemploniveles de potencia deben calibrarse cuidadosamente para que coincidan con las propiedades térmicas del material objetivo. Una potencia excesiva puede provocar un sobrecalentamiento que provoque arcos localizados e ignición, mientras que una potencia insuficiente puede no vaporizar eficazmente el material, con la consiguiente mala calidad del revestimiento. De forma similar,las configuraciones del campo magnético deben equilibrarse para crear una distribución uniforme del plasma, evitando descargas concentradas que puedan provocar chispas.
Además, mantener una presiónpresión de la cámara de vacío es esencial. Una presión demasiado alta puede permitir que los gases residuales interactúen con el material objetivo, provocando reacciones no deseadas y una posible ignición. Por el contrario, una presión demasiado baja puede provocar una formación de plasma ineficaz, afectando al proceso de sputtering.
Ajustando sistemáticamente estas condiciones, los operadores pueden reducir significativamente el riesgo de ignición del material objetivo, asegurando un proceso de sputtering estable y eficiente.
Inspección periódica del equipo
La inspección periódica del equipo es una práctica fundamental en el contexto del sputtering por magnetrón para garantizar la longevidad y eficacia del proceso. Este mantenimiento rutinario implica un examen exhaustivo de todos los componentes, desde la cámara de vacío hasta las fuentes de alimentación, para identificar cualquier signo de desgaste o mal funcionamiento. Siguiendo un estricto programa de inspecciones, los operarios pueden detectar y abordar posibles problemas antes de que se conviertan en problemas más importantes.
Uno de los objetivos principales de estas inspecciones es verificar que todas las piezas mecánicas funcionan correctamente. Esto incluye comprobar si hay conexiones sueltas, componentes desalineados o signos de daños físicos. Además, los sistemas eléctricos deben examinarse para garantizar que funcionan dentro de unos parámetros seguros, evitando posibles cortocircuitos o subidas de tensión que podrían provocar fallos en los equipos o, lo que es peor, riesgos para la seguridad.
Además, las inspecciones periódicas ayudan a mantener la integridad del entorno de vacío dentro de la cámara. Cualquier fuga o degradación en las juntas de vacío puede comprometer el proceso de sputtering, provocando una deposición subóptima de la película y posibles chispas en el material objetivo. Al identificar y rectificar estos problemas con prontitud, los operarios pueden mantener una atmósfera estable y controlada, necesaria para aplicaciones de revestimiento de alta calidad.
En resumen, la inspección periódica de los equipos no es una mera medida preventiva, sino un aspecto esencial para garantizar el funcionamiento continuo y seguro de los equipos de sputtering magnetrónico. Abarca una evaluación exhaustiva de los componentes mecánicos y eléctricos, garantizando que todo el sistema funcione según lo previsto, minimizando así el riesgo de que se produzcan chispas en el material objetivo y otros problemas relacionados.
CONTÁCTANOS PARA UNA CONSULTA GRATUITA
Los productos y servicios de KINTEK LAB SOLUTION han sido reconocidos por clientes de todo el mundo. Nuestro personal estará encantado de ayudarle con cualquier consulta que pueda tener. ¡Contáctenos para una consulta gratuita y hable con un especialista del producto para encontrar la solución más adecuada para sus necesidades de aplicación!