El recocido es un proceso de tratamiento térmico utilizado para alterar las propiedades físicas y a veces químicas de un material, normalmente metales, para aumentar la ductilidad y reducir la dureza. La temperatura a la que tiene lugar el recocido varía en función del tipo de metal y del proceso de recocido específico que se utilice. En general, el recocido consiste en calentar el metal a una temperatura superior a su punto de recristalización pero inferior a su punto de fusión, lo que permite que la estructura cristalina se vuelva fluida sin dejar de ser sólida. Esta temperatura se mantiene durante un tiempo suficiente para permitir que los defectos del material se reparen por sí mismos, seguido de un enfriamiento lento hasta la temperatura ambiente para producir una estructura más dúctil y menos quebradiza.
Explicación de los puntos clave:
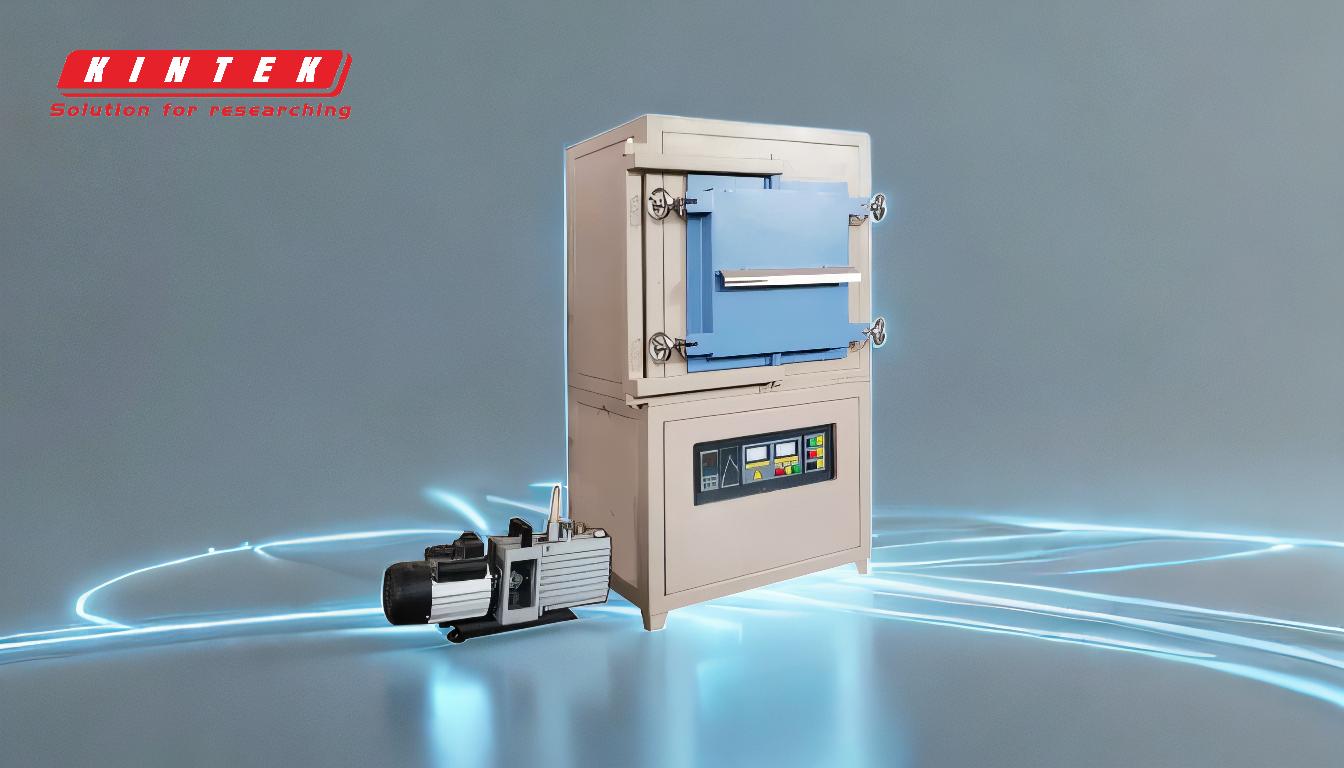
-
Definición de recocido:
- El recocido es un proceso de tratamiento térmico que consiste en calentar un material, normalmente un metal, a una temperatura específica, mantenerlo a esa temperatura y, a continuación, enfriarlo lentamente. Este proceso se utiliza para reducir la dureza, aumentar la ductilidad y eliminar tensiones internas.
-
Temperatura de recocido:
-
La temperatura a la que se produce el recocido depende del tipo de metal y del proceso de recocido específico. Por lo general, se sitúa por encima de la temperatura de recristalización del metal pero por debajo de su punto de fusión. Por ejemplo:
- Acero: Típicamente recocido a temperaturas entre 700°C y 900°C (1292°F a 1652°F).
- Aluminio: Recocido a unos 300°C a 400°C (572°F a 752°F).
- Cobre: Recocido a aproximadamente 400°C a 700°C (752°F a 1292°F).
-
La temperatura a la que se produce el recocido depende del tipo de metal y del proceso de recocido específico. Por lo general, se sitúa por encima de la temperatura de recristalización del metal pero por debajo de su punto de fusión. Por ejemplo:
-
Temperatura de recristalización:
- La recristalización es el proceso por el cual los granos deformados de un metal son sustituidos por nuevos granos sin deformación. La temperatura de recristalización suele ser entre un tercio y la mitad del punto de fusión del metal en grados Kelvin. Esta es la temperatura mínima a la que puede producirse efectivamente el recocido.
-
Tipos de procesos de recocido:
-
Existen varios tipos de procesos de recocido, cada uno con rangos de temperatura y aplicaciones específicas:
- Recocido completo: Consiste en calentar el metal a una temperatura superior a la temperatura crítica superior (para los aceros) y, a continuación, enfriarlo lentamente en el horno. Este proceso se utiliza para producir una estructura blanda y dúctil.
- Proceso de recocido: Se realiza a temperaturas más bajas (por debajo de la temperatura crítica inferior) para aliviar la tensión en metales trabajados en frío sin alterar significativamente la microestructura.
- Esferoidización: Un proceso de recocido especializado utilizado para aceros de alto contenido en carbono, en el que el metal se calienta justo por debajo de la temperatura crítica inferior para producir una estructura de carburo esferoidal, mejorando la maquinabilidad.
- Recocido isotérmico: El metal se calienta hasta una temperatura superior a la temperatura crítica superior y, a continuación, se enfría rápidamente hasta una temperatura inferior a la temperatura crítica inferior, donde se mantiene hasta que se completa la transformación.
-
Existen varios tipos de procesos de recocido, cada uno con rangos de temperatura y aplicaciones específicas:
-
Tasa de enfriamiento:
- La velocidad de enfriamiento tras el recocido es crucial. Un enfriamiento lento permite la formación de una estructura cristalina más dúctil, reduciendo las tensiones internas y mejorando la trabajabilidad del material. El enfriamiento rápido puede dar lugar a la formación de una estructura más dura y quebradiza, que no suele ser la deseada en el recocido.
-
Aplicaciones del recocido:
-
El recocido se utiliza en diversas industrias para mejorar las propiedades de los metales. Entre las aplicaciones más comunes se incluyen:
- Fabricación: Hacer que los metales sean más manejables para su conformación, mecanizado o soldadura.
- Electrónica: Para mejorar la conductividad eléctrica de metales como el cobre.
- Aeroespacial: Para mejorar las propiedades mecánicas de los componentes sometidos a grandes esfuerzos.
-
El recocido se utiliza en diversas industrias para mejorar las propiedades de los metales. Entre las aplicaciones más comunes se incluyen:
-
Importancia del control de la temperatura:
- El control preciso de la temperatura durante el recocido es esencial para conseguir las propiedades deseadas del material. El sobrecalentamiento puede provocar el crecimiento de grano, lo que puede debilitar el material, mientras que un calentamiento insuficiente puede no aliviar totalmente las tensiones internas ni lograr la microestructura deseada.
En resumen, la temperatura a la que tiene lugar el recocido es específica del tipo de metal y del proceso de recocido que se utilice. Por lo general, consiste en calentar el metal a una temperatura superior a su punto de recristalización pero inferior a su punto de fusión, seguido de un enfriamiento controlado para conseguir las propiedades deseadas del material.
Cuadro recapitulativo:
Metal | Temperatura de recocido (°C) | Aplicaciones clave |
---|---|---|
Acero | 700°C - 900°C | Fabricación, Aeroespacial |
Aluminio | 300°C - 400°C | Electrónica, Automoción |
Cobre | 400°C - 700°C | Componentes eléctricos |
Proceso | Temperatura | Propósito |
Recocido completo | Por encima de la temperatura crítica superior | Estructura blanda y dúctil |
Proceso de recocido | Por debajo de la temperatura crítica inferior | Alivio del estrés |
Esferoidización | Justo por debajo de la temperatura crítica inferior | Maquinabilidad mejorada |
¿Necesita asesoramiento experto sobre las temperaturas de recocido de sus materiales? Póngase en contacto con nosotros para optimizar su proceso de tratamiento térmico