La duración del proceso de sinterización varía considerablemente en función de los materiales, las técnicas y los requisitos específicos del producto final.En general, la sinterización puede durar desde unos pocos milisegundos hasta más de 24 horas.El proceso en sí puede durar sólo unos segundos, pero los pasos posteriores a la sinterización de la forma pueden alargar el tiempo total hasta varias horas.Factores como la temperatura, la velocidad de calentamiento, la presión, el tamaño de las partículas, la composición y la atmósfera de sinterización (por ejemplo, aire, vacío o gases inertes) desempeñan un papel crucial a la hora de determinar el tiempo de sinterización.La sinterización a alta temperatura puede mejorar las propiedades del material, como la resistencia a la tracción y la energía de impacto, pero también requiere un control preciso del entorno de sinterización.Para muchas aplicaciones, el proceso de sinterización suele durar entre 15 y 20 horas, dependiendo del material y de la densidad deseada de la pieza final.
Explicación de los puntos clave:
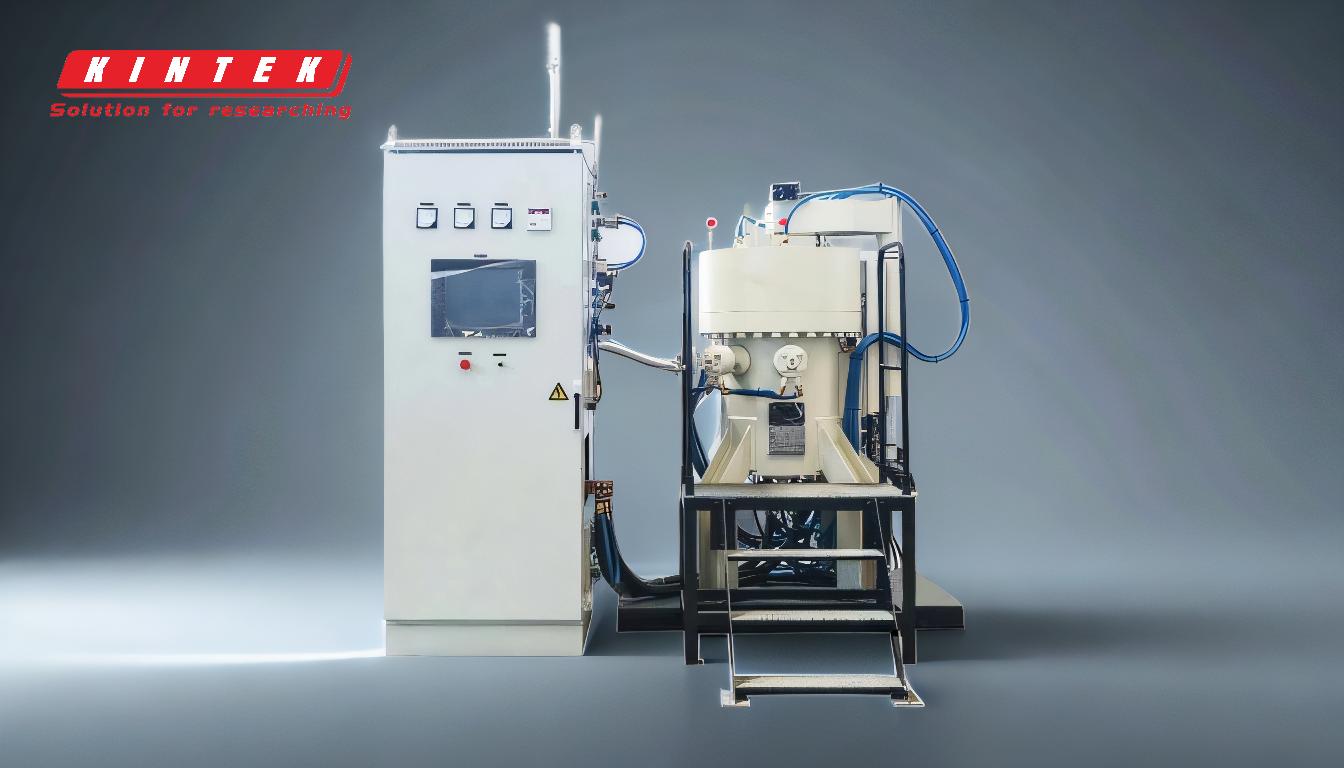
-
Gama de tiempos de sinterización:
- La sinterización puede durar desde unos pocos milisegundos hasta más de 24 horas.
- El proceso en sí puede durar sólo unos segundos, pero los pasos posteriores a la sinterización pueden alargar el tiempo total hasta varias horas.
-
Factores que influyen en el tiempo de sinterización:
- Temperatura:Determina la cinética de sinterización y las propiedades del material.Las temperaturas más altas pueden acelerar el proceso, pero deben controlarse cuidadosamente para evitar la degradación del material.
- Velocidad de calentamiento:Afecta a la densificación.Una velocidad de calentamiento más rápida puede reducir el tiempo de sinterización, pero puede provocar una densificación desigual.
- Presión:Mejora la reorganización de las partículas y elimina la porosidad, lo que puede acortar el tiempo de sinterización.
- Tamaño y composición de las partículas:Las partículas más pequeñas y las composiciones homogéneas favorecen una mejor densificación, reduciendo potencialmente el tiempo de sinterización.
-
Atmósfera de sinterización:
- La atmósfera (por ejemplo, aire, vacío o argón/nitrógeno) puede influir significativamente en el proceso de sinterización.A menudo se utilizan atmósferas inertes para evitar la oxidación y otras reacciones no deseadas, que pueden afectar al tiempo de sinterización y a las propiedades finales del material.
-
Requisitos de material y densidad:
- La temperatura y el tiempo del horno de sinterización dependen del material utilizado y de la densidad requerida de la pieza final.Los distintos materiales tienen diferentes requisitos de sinterización, y para lograr densidades más altas pueden ser necesarios tiempos de sinterización más largos.
-
Duraciones típicas de sinterización:
- Para muchas aplicaciones industriales, el proceso de sinterización suele durar entre 15 y 20 horas.Esta duración puede variar en función del material específico, las propiedades deseadas y el tipo de horno de sinterización utilizado (por ejemplo, horno de cinta transportadora, de empuje o discontinuo).
-
Sinterización posterior:
- Aunque el proceso de sinterización inicial puede ser rápido, los pasos de sinterización posteriores a la forma pueden durar varias horas.Estos pasos son cruciales para conseguir las propiedades y dimensiones finales deseadas de la pieza sinterizada.
-
Impacto en las propiedades del material:
- La sinterización a alta temperatura puede aumentar la resistencia a la tracción, la resistencia a la fatiga por flexión y la energía de impacto.Sin embargo, para conseguir estas propiedades suele ser necesario un control preciso del entorno de sinterización y puede prolongarse el tiempo total de sinterización.
En resumen, el tiempo de sinterización es muy variable y depende de multitud de factores, como las propiedades del material, los resultados deseados y las condiciones del proceso.Comprender estos factores es crucial para optimizar el proceso de sinterización y conseguir las propiedades deseadas del material de forma eficiente.
Tabla resumen:
Factor | Impacto en el tiempo de sinterización |
---|---|
Temperatura | Las temperaturas más altas aceleran la sinterización, pero requieren un control preciso para evitar la degradación del material. |
Velocidad de calentamiento | Un calentamiento más rápido reduce el tiempo pero puede causar una densificación desigual. |
Presión | Mejora la reorganización de las partículas, acortando el tiempo de sinterización. |
Tamaño de las partículas | Las partículas más pequeñas favorecen una densificación más rápida. |
Atmósfera de sinterización | Los gases inertes evitan la oxidación, lo que afecta al tiempo y a las propiedades finales. |
Material/Densidad | Los materiales más densos o los requisitos de mayor densidad aumentan el tiempo de sinterización. |
Duración típica | 15-20 horas para muchas aplicaciones industriales, dependiendo del material y del tipo de horno. |
¿Necesita ayuda para optimizar su proceso de sinterización? Póngase en contacto con nuestros expertos para obtener soluciones a medida.