La porosidad en pulvimetalurgia es un factor crítico que afecta a las propiedades mecánicas y al rendimiento del producto final.Se puede reducir la porosidad optimizando varios parámetros clave durante el proceso de fabricación.Entre ellos se incluyen el aumento de la presión de compactación, la temperatura de sinterización y el tiempo de sinterización, que en conjunto ayudan a reducir la porosidad aparente y a aumentar la densidad aparente.Además, el control del tamaño de las partículas es crucial, ya que las partículas más grandes tienden a aumentar la porosidad.Controlando cuidadosamente estos factores, los fabricantes pueden producir componentes de alta densidad y baja porosidad con mejores propiedades mecánicas.
Explicación de los puntos clave:
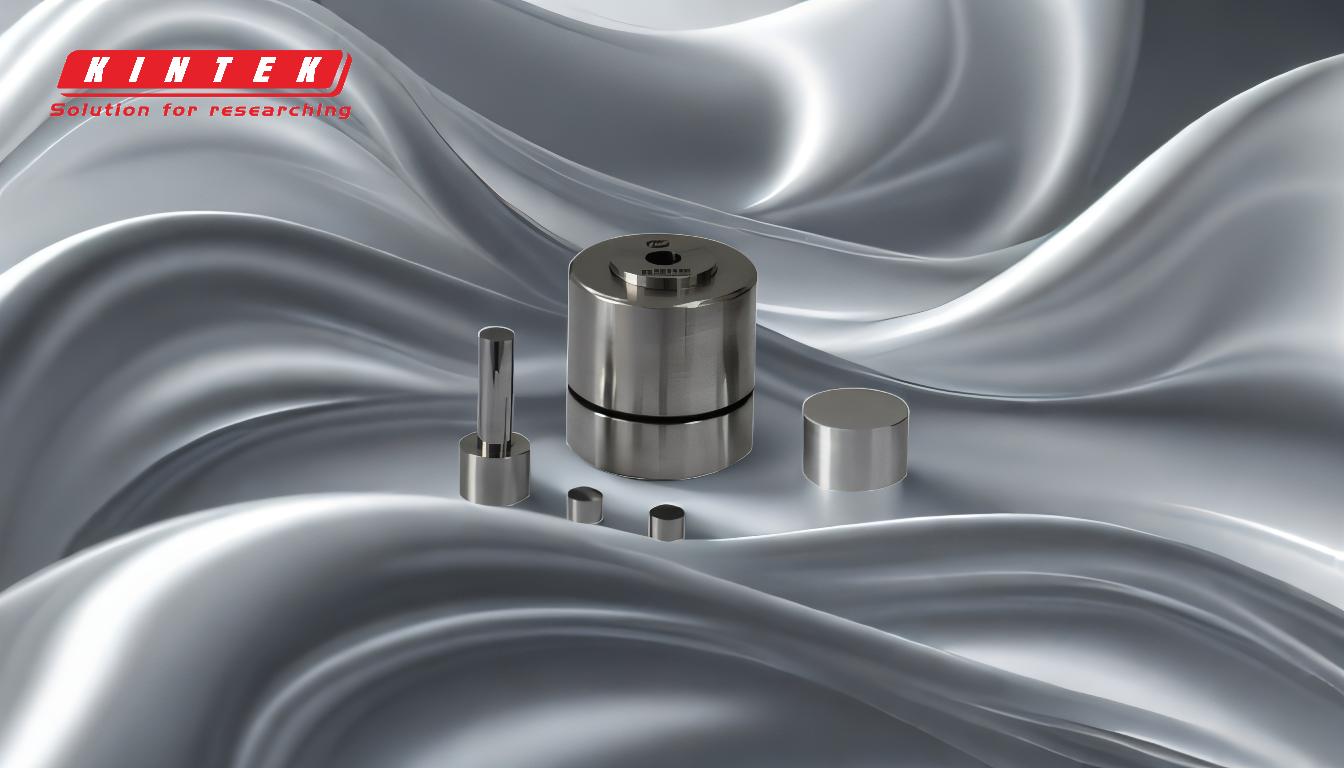
-
Aumento de la presión de compactación:
- Impacto:Una mayor presión de compactación reduce los espacios entre las partículas de polvo, dando lugar a un compacto más denso y con menor porosidad.
- Mecanismo:Cuando se aplica presión durante la etapa de compactación, las partículas son forzadas a juntarse más, minimizando los huecos y aumentando la densidad aparente del compacto verde.
- Consideraciones prácticas:Aunque una mayor presión es beneficiosa, debe equilibrarse con el riesgo de dañar la matriz o provocar una distribución desigual de la densidad en la pieza.
-
Optimización de la temperatura y el tiempo de sinterización:
- Impacto:Las temperaturas de sinterización más altas y los tiempos de sinterización más largos favorecen una mejor unión y difusión de las partículas, reduciendo la porosidad y aumentando la densidad.
- Mecanismo:La sinterización consiste en calentar el polvo compactado por debajo de su punto de fusión, permitiendo que los átomos se difundan a través de los límites de las partículas, lo que cierra los poros y refuerza el material.
- Consideraciones prácticas:Una temperatura o un tiempo excesivos pueden provocar el crecimiento o la distorsión del grano, por lo que es necesaria una optimización cuidadosa.
-
Control del tamaño de las partículas:
- Impacto:Las partículas de menor tamaño suelen tener menor porosidad porque se compactan mejor y dejan menos huecos.
- Mecanismo:Las partículas finas tienen una mayor relación superficie/volumen, lo que favorece la sinterización y la adhesión.En cambio, las partículas más grandes crean más huecos y aumentan la porosidad.
- Consideraciones prácticas:Aunque las partículas más pequeñas son preferibles, también pueden aumentar el riesgo de aglomeración, que debe controlarse durante el procesado.
-
Métodos de producción de polvo:
- Impacto:El método utilizado para producir polvos metálicos influye en su tamaño, forma y distribución, lo que a su vez afecta a la porosidad.
- Mecanismo:Técnicas como la atomización producen polvos con rangos de tamaño controlados, que pueden adaptarse para minimizar la porosidad.La trituración y la molienda pueden producir partículas de forma irregular que se empaquetan con menos eficacia.
- Consideraciones prácticas:La selección del método de producción de polvo adecuado es esencial para conseguir las características deseadas de las partículas y minimizar la porosidad.
-
Selección del material:
- Impacto:La elección del material base (por ejemplo, base cobre o base hierro) puede influir en la porosidad debido a las diferencias en la forma, el tamaño y el comportamiento de sinterización de las partículas.
- Mecanismo:Algunos materiales sinterizan más fácilmente que otros, lo que da lugar a una mejor densificación y a una menor porosidad.
- Consideraciones prácticas:La selección del material debe ajustarse a la aplicación prevista y a las propiedades mecánicas deseadas.
Si se tienen en cuenta estos factores clave, los fabricantes pueden reducir eficazmente la porosidad en la pulvimetalurgia, lo que se traduce en componentes de mayor resistencia, durabilidad y rendimiento.
Tabla resumen:
Factor clave | Impacto | Mecanismo | Consideraciones prácticas |
---|---|---|---|
Aumento de la presión de compactación | Reduce los huecos entre las partículas, dando lugar a compactos más densos con menor porosidad. | La presión acerca las partículas, minimizando los huecos y aumentando la densidad aparente. | Equilibre la presión para evitar daños en la matriz o una distribución desigual de la densidad. |
Optimización de la temperatura y el tiempo de sinterización | Favorece la unión de las partículas, reduce la porosidad y aumenta la densidad. | El calentamiento por debajo del punto de fusión permite la difusión de átomos, cerrando los poros y reforzando el material. | Evite temperaturas o tiempos excesivos para prevenir el crecimiento de grano o la distorsión. |
Control del tamaño de las partículas | Las partículas más pequeñas se empaquetan eficazmente, reduciendo la porosidad. | Las partículas finas tienen una mayor relación superficie-volumen, lo que mejora la sinterización y la adhesión. | Gestione los riesgos de aglomeración con partículas más pequeñas. |
Métodos de producción de polvo | Influye en el tamaño, la forma y la distribución de las partículas, afectando a la porosidad. | La atomización produce rangos de tamaño controlados; la trituración puede crear partículas irregulares. | Seleccione el método adecuado para conseguir las características deseadas de las partículas. |
Selección del material | El material base afecta a la porosidad debido a diferencias en el comportamiento de sinterización. | Algunos materiales sinterizan más fácilmente, lo que da lugar a una mejor densificación y una menor porosidad. | Alinee la elección del material con la aplicación y las propiedades mecánicas deseadas. |
¿Está listo para optimizar su proceso pulvimetalúrgico? Póngase en contacto con nuestros expertos para obtener soluciones a medida.