Los hornos de inducción sin núcleo, aunque ofrecen ventajas como el control preciso de la temperatura, la distribución uniforme del calor y la flexibilidad en los cambios de aleación, tienen desventajas notables.Los principales inconvenientes son la menor eficiencia energética (aproximadamente un 75%) en comparación con los hornos con núcleo, que pueden alcanzar hasta un 98% de eficiencia.Además, los frecuentes cambios de aleación pueden acelerar el desgaste del revestimiento refractario y reducir su vida útil.La ausencia de un núcleo concentrador de flujo en los hornos sin núcleo contribuye aún más a su menor eficiencia.Estos factores hacen que los hornos de inducción sin núcleo sean menos adecuados para operaciones de alto rendimiento o entornos que requieren una producción continua con un tiempo de inactividad mínimo.
Explicación de los puntos clave:
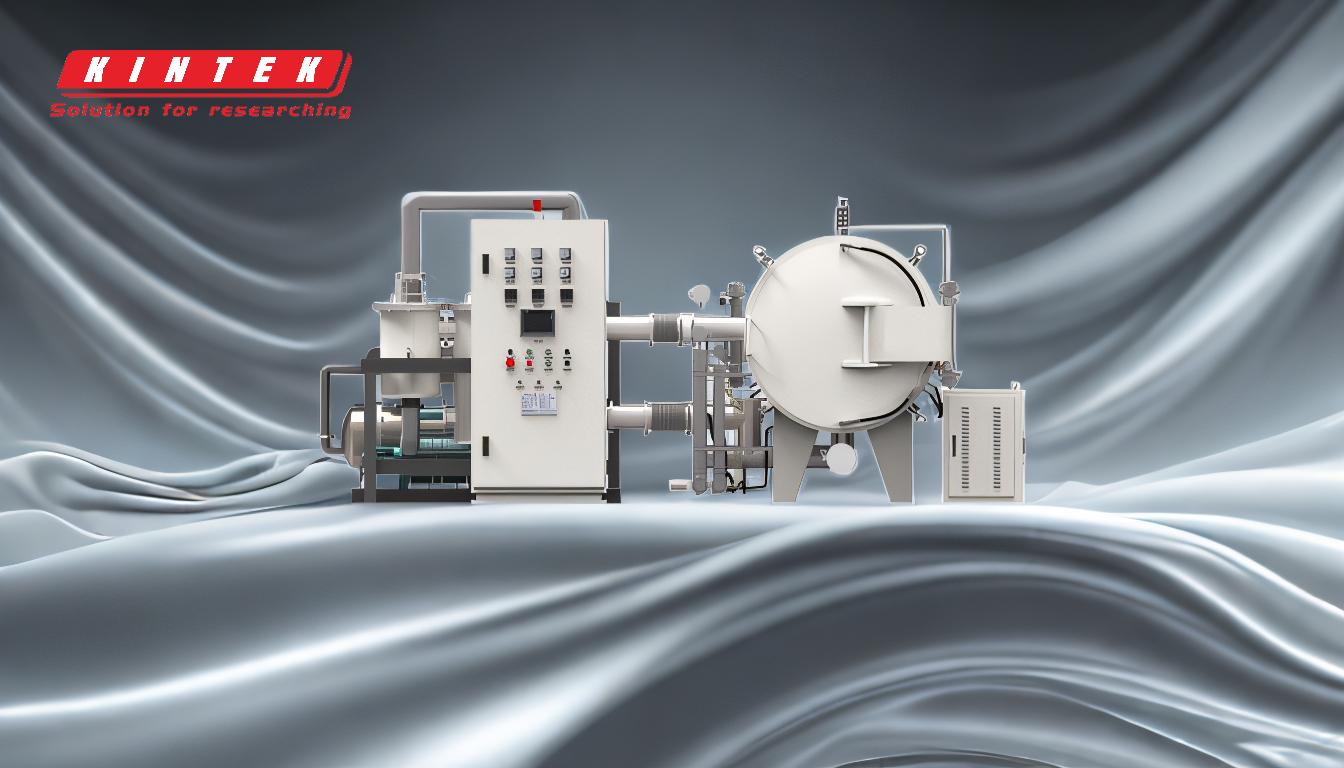
-
Eficiencia energética reducida
- Los hornos de inducción sin núcleo funcionan con una eficiencia energética aproximada del 75%, significativamente inferior a la de los hornos con núcleo, que pueden alcanzar una eficiencia de hasta el 98%.
- La ausencia de un núcleo concentrador de flujo en los hornos sin núcleo provoca pérdidas de energía, ya que el campo magnético se concentra con menor eficacia en la carga metálica.
- Esta menor eficacia se traduce en un mayor consumo de energía y costes de funcionamiento, lo que hace que los hornos sin núcleo sean menos económicos para aplicaciones de alto rendimiento o de alto consumo energético.
-
Desgaste del revestimiento refractario
- Los cambios frecuentes de aleación, una práctica habitual en los hornos sin núcleo, pueden acelerar la degradación del revestimiento refractario.
- El revestimiento refractario está expuesto a ciclos térmicos y reacciones químicas con diferentes aleaciones, lo que provoca grietas, erosión y una reducción de la vida útil.
- La sustitución del revestimiento refractario es costosa y requiere mucho tiempo, lo que aumenta los gastos de mantenimiento y el tiempo de inactividad.
-
Idoneidad limitada para operaciones continuas
- Los hornos de inducción sin núcleo están diseñados para ser flexibles, lo que permite apagarlos y arrancarlos en frío, lo que resulta ventajoso para los cambios de aleación.
- Sin embargo, este diseño los hace menos adecuados para operaciones continuas de alta producción en las que es esencial mantener un baño constante de metal fundido.
- Los hornos con núcleo, por el contrario, son más adecuados para este tipo de aplicaciones debido a su mayor eficiencia y a su capacidad para funcionar de forma continua.
-
Mayor consumo de energía
- La menor eficiencia de los hornos sin núcleo significa que se necesita más energía para lograr los mismos resultados de fusión que los hornos con núcleo.
- Esta mayor demanda de energía puede suponer mayores costes operativos, sobre todo en regiones con electricidad cara.
- Para las empresas que desean minimizar los gastos energéticos, los hornos sin núcleo pueden no ser la opción más rentable.
-
Dependencia del sistema de refrigeración
- Los hornos de inducción sin núcleo dependen de bobinas de cobre refrigeradas por agua para evitar el sobrecalentamiento durante el funcionamiento.
- El sistema de refrigeración añade complejidad al diseño del horno y requiere un mantenimiento regular para garantizar su correcto funcionamiento.
- Cualquier fallo en el sistema de refrigeración puede provocar daños en la bobina o la parada del horno, interrumpiendo la producción.
-
Limitaciones operativas
- Aunque los hornos sin núcleo ofrecen flexibilidad en cuanto a cambios de aleación y gama de frecuencias (de 50 Hz a 10 kHz), son menos eficientes a frecuencias más bajas.
- Los hornos con núcleo, con su mayor eficiencia, son más adecuados para aplicaciones que requieren un rendimiento constante en una amplia gama de frecuencias.
En resumen, aunque los hornos de inducción sin núcleo ofrecen un excelente control de la temperatura y de la composición química del metal, su menor eficiencia energética, su susceptibilidad al desgaste del revestimiento refractario y su mayor consumo de energía los hacen menos idóneos para operaciones de alto rendimiento o continuas.Estas desventajas deben tenerse muy en cuenta a la hora de seleccionar un horno para aplicaciones industriales específicas.
Tabla resumen:
Desventaja | Descripción |
---|---|
Eficiencia energética reducida | Funciona con un rendimiento del ~75% frente al 98% de los hornos de núcleo, lo que conlleva un mayor consumo de energía. |
Desgaste del revestimiento refractario | Los cambios frecuentes de aleación aceleran la degradación del revestimiento, aumentando los costes de mantenimiento y el tiempo de inactividad. |
Limitado para uso continuo | Menos adecuado para operaciones de alto rendimiento o continuas debido a limitaciones de diseño. |
Mayor consumo de energía | Una menor eficiencia aumenta los costes operativos, especialmente en regiones con electricidad cara. |
Dependencia del sistema de refrigeración | Depende de serpentines refrigerados por agua, lo que añade complejidad y necesidades de mantenimiento. |
Limitaciones operativas | Menos eficientes a bajas frecuencias, por lo que los hornos de núcleo son mejores para un rendimiento constante. |
¿Necesita ayuda para elegir el horno adecuado a sus necesidades? Póngase en contacto con nuestros expertos hoy mismo ¡!