La sinterización en cerámica es un proceso crítico que transforma materiales en polvo en una estructura sólida y cohesiva mediante la aplicación de calor, normalmente por debajo del punto de fusión del material primario.Este proceso consta de varias etapas, que incluyen la preparación del polvo, la conformación y el calentamiento controlado en un horno de sinterización que facilita la unión y densificación de las partículas.El resultado es un producto cerámico duradero, de baja porosidad y con mejores propiedades mecánicas y térmicas.Comprender el proceso de sinterización es esencial para optimizar la producción de cerámica y conseguir las características deseadas del material.
Explicación de los puntos clave:
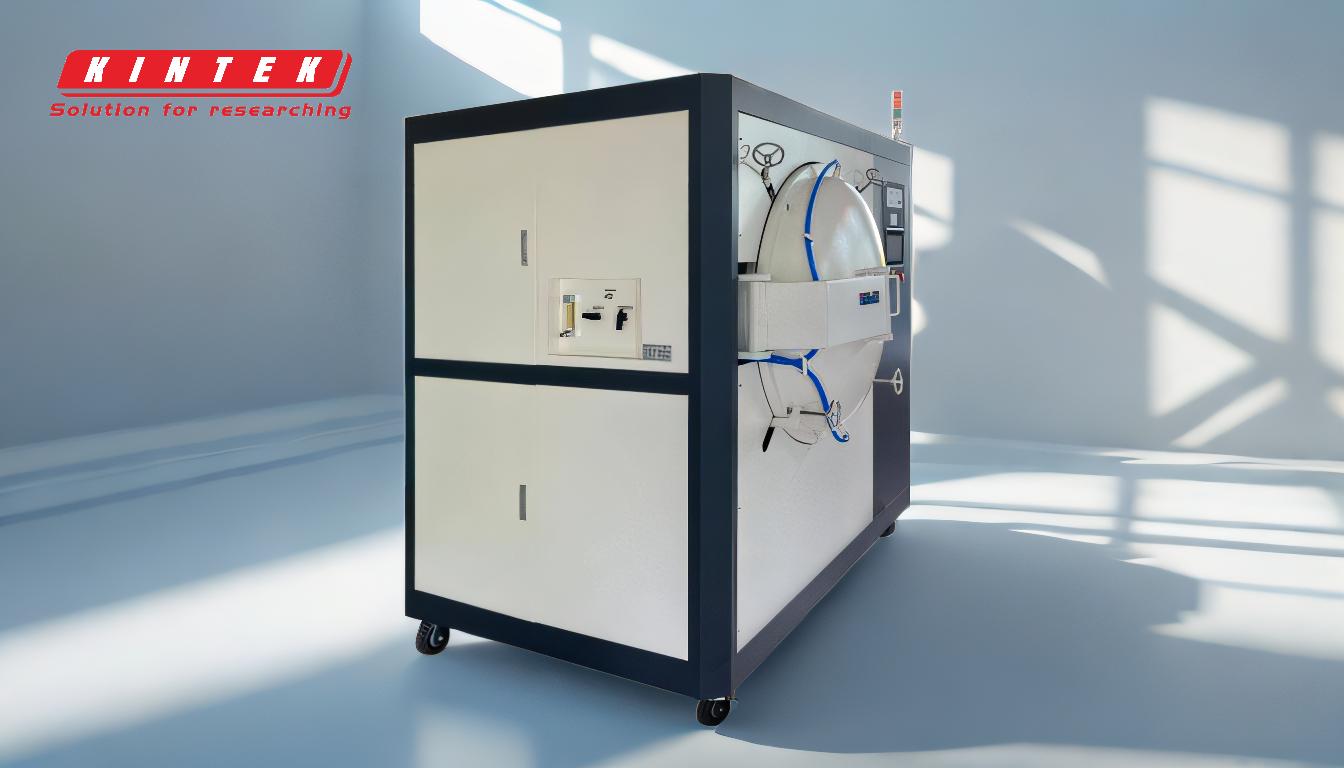
-
Definición y finalidad de la sinterización en cerámica:
- La sinterización es un proceso de tratamiento térmico utilizado para unir partículas cerámicas en una estructura sólida sin fundir el material primario.
- El objetivo principal es reducir la porosidad, aumentar la densidad y mejorar la resistencia mecánica y la estabilidad térmica del producto cerámico.
-
Etapas del proceso de sinterización:
- Preparación del polvo:Las materias primas cerámicas se muelen hasta obtener polvos finos y se mezclan con aditivos como aglutinantes o agentes de acoplamiento para mejorar la manipulación y la conformación.
- Conformación:El polvo se compacta en la forma deseada mediante técnicas como el prensado o el moldeado, formando un \"cuerpo verde".
- Eliminación del aglutinante:El cuerpo verde se calienta a baja temperatura para quemar o evaporar el aglutinante, dejando tras de sí una estructura porosa.
- Sinterización a alta temperatura:El material se calienta en un horno de sinterización a una temperatura inferior a su punto de fusión, lo que permite que las partículas se adhieran mediante difusión y formación de cuellos.
- Enfriamiento:El producto sinterizado se enfría gradualmente para solidificarse en una estructura rígida y cohesiva.
-
Función del horno de sinterización:
- A horno de sinterización proporciona entornos controlados de calentamiento y enfriamiento esenciales para el proceso de sinterización.
- Garantiza una distribución uniforme de la temperatura, evitando defectos como alabeos o grietas.
- Los hornos avanzados permiten un control preciso de las velocidades de calentamiento, los tiempos de permanencia y las velocidades de enfriamiento, que son fundamentales para conseguir unas propiedades óptimas de los materiales.
-
Mecanismos de sinterización:
- Difusión:Los átomos se mueven a través de las superficies de las partículas, dando lugar a la formación de cuellos y a la unión de las partículas.
- Crecimiento del grano:Las partículas se fusionan, reduciendo la porosidad y aumentando la densidad.
- Sinterización en fase líquida:En algunos casos, se forma una pequeña cantidad de fase líquida que contribuye a la reorganización y la unión de las partículas.
-
Factores que influyen en la sinterización:
- Temperatura:Las temperaturas más altas aceleran la difusión y la unión, pero deben controlarse para evitar la fusión.
- Tiempo:Los tiempos de sinterización más largos permiten una densificación más completa, pero pueden provocar un crecimiento excesivo del grano.
- Atmósfera:El entorno de sinterización (por ejemplo, aire, vacío o gas inerte) puede afectar a la oxidación, reducción o contaminación.
- Tamaño y forma de las partículas:Las partículas más pequeñas y uniformes sinterizan con mayor eficacia debido al aumento de la superficie y los puntos de contacto.
-
Aplicaciones de la cerámica sinterizada:
- La cerámica sinterizada se utiliza en industrias como la electrónica (aislantes, sustratos), aeroespacial (barreras térmicas), automovilística (discos de freno) y médica (implantes, prótesis).
- El proceso permite producir formas complejas con gran precisión y consistencia.
-
Ventajas de la sinterización:
- Produce materiales de gran solidez, resistencia al desgaste y estabilidad térmica.
- Permite la creación de geometrías intrincadas y componentes de forma casi neta.
- Reduce el desperdicio de material en comparación con los procesos de mecanizado tradicionales.
-
Retos y consideraciones:
- Controlar la contracción y los cambios dimensionales durante la sinterización.
- Evitar defectos como grietas, huecos o alabeos.
- Equilibrar los parámetros de sinterización para conseguir las propiedades deseadas sin un consumo excesivo de energía.
Al comprender el proceso de sinterización y sus etapas clave, los fabricantes pueden optimizar la producción de cerámica, garantizando productos duraderos y de alta calidad adaptados a aplicaciones específicas.El horno de sinterización horno de sinterización desempeña un papel fundamental en este proceso, ya que proporciona el entorno controlado necesario para el éxito de la sinterización.
Cuadro sinóptico:
Aspecto clave | Detalles |
---|---|
Finalidad | Adhiere partículas cerámicas, reduce la porosidad y aumenta la resistencia. |
Etapas | Preparación del polvo, conformación, eliminación del aglutinante, sinterización a alta temperatura, enfriamiento. |
Función del horno de sinterización | Proporciona un calentamiento/enfriamiento controlado para una distribución uniforme de la temperatura. |
Mecanismos | Difusión, crecimiento de grano y sinterización en fase líquida. |
Aplicaciones | Industria electrónica, aeroespacial, automovilística y médica. |
Ventajas | Alta resistencia, resistencia al desgaste y estabilidad térmica. |
Optimice su producción cerámica con el asesoramiento de expertos póngase en contacto con nosotros ¡!