La atmósfera de un horno de sinterización desempeña un papel fundamental en la determinación de la calidad y las propiedades de los productos sinterizados. Se controla cuidadosamente para evitar la oxidación, la descarburación y otras reacciones indeseables, al tiempo que se garantizan unas condiciones de sinterización adecuadas. Las atmósferas más comunes incluyen mezclas de nitrógeno e hidrógeno, hidrógeno puro, vacío, amoníaco disociado, gas endotérmico y gases inertes como el argón o el nitrógeno. La elección de la atmósfera depende del material sinterizado y de los resultados deseados, como mantener un entorno neutro, reductor o protector. Estas atmósferas se regulan en distintas zonas del horno para lograr vectores de sinterización específicos y garantizar resultados óptimos.
Explicación de los puntos clave:
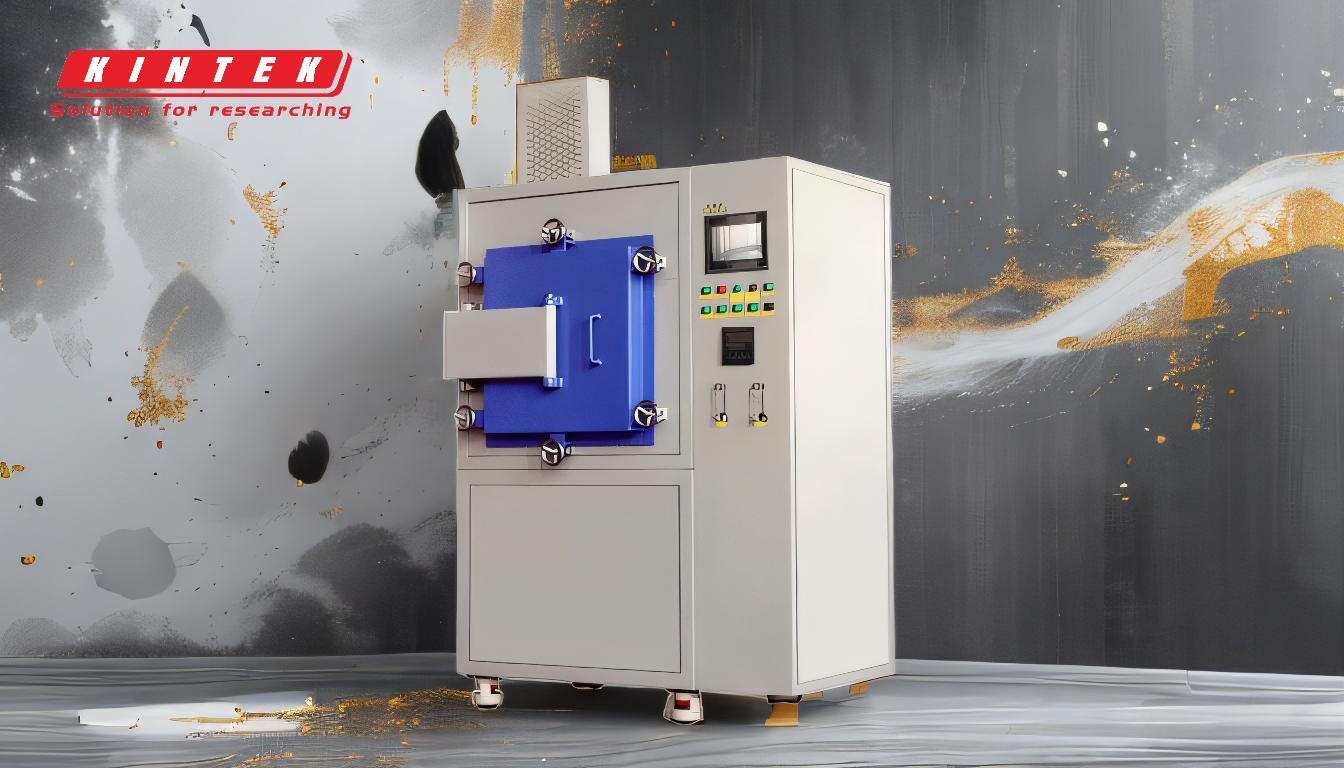
-
Finalidad de las atmósferas controladas en los hornos de sinterización:
- La atmósfera de un horno de sinterización es crucial para evitar la oxidación, la descarburación y otras reacciones químicas que podrían degradar la calidad del producto sinterizado.
- Garantiza la sinterización adecuada de metales en polvo u otros materiales manteniendo las condiciones térmicas y químicas requeridas.
-
Tipos de atmósferas:
- Atmósferas inertes/protectoras: Se trata de nitrógeno, argón o mezclas de nitrógeno e hidrógeno. Se utilizan para evitar reacciones con el material sinterizado, sobre todo en el caso de metales sensibles a la oxidación.
- Atmósfera de hidrógeno: El hidrógeno puro se utiliza a menudo por sus propiedades reductoras, que ayudan a eliminar los óxidos de la superficie del material.
- Vacío: Un entorno de vacío elimina la presencia de gases reactivos, por lo que es ideal para sinterizar materiales muy reactivos con oxígeno o nitrógeno.
- Amoníaco disociado: Esta atmósfera proporciona una mezcla de hidrógeno y nitrógeno que ofrece propiedades reductoras y protectoras.
- Gas endotérmico: Se trata de una mezcla de hidrógeno, monóxido de carbono y nitrógeno, utilizada habitualmente en los procesos de sinterización para evitar la oxidación y la descarburación.
-
Selección de la atmósfera en función de los requisitos del material y el proceso:
-
La elección de la atmósfera depende del material sinterizado. Por ejemplo:
- Atmósferas oxidantes: Se utiliza para materiales que requieren oxidación durante la sinterización.
- Atmósferas neutras: Adecuado para materiales que no deben reaccionar con la atmósfera.
- Atmósferas reductoras: Ideal para materiales que necesitan reducción de óxidos, como los metales.
- Atmósferas alcalinas o ácidas: Se utiliza para procesos de sinterización especializados en los que se requieren reacciones químicas específicas.
-
La elección de la atmósfera depende del material sinterizado. Por ejemplo:
-
Regulación de la atmósfera en distintas zonas:
-
Los hornos de sinterización suelen tener varias zonas, cada una de las cuales requiere una atmósfera específica para conseguir los vectores de sinterización deseados. Por ejemplo:
- Puede utilizarse una atmósfera reductora en la zona de calentamiento inicial para eliminar los óxidos.
- Puede mantenerse una atmósfera neutra o inerte en la zona de sinterización para evitar reacciones posteriores.
- Una zona de enfriamiento puede utilizar una atmósfera protectora para garantizar que el material no se oxida al enfriarse.
-
Los hornos de sinterización suelen tener varias zonas, cada una de las cuales requiere una atmósfera específica para conseguir los vectores de sinterización deseados. Por ejemplo:
-
Modos operativos:
-
Los hornos de sinterización pueden funcionar en varios modos, entre ellos:
- Aire: Se utiliza para materiales poco sensibles a la oxidación.
- Vacío: Se utiliza para materiales muy reactivos.
- Vacío parcial o presión positiva: Se utiliza para controlar el flujo de gases y mantener una atmósfera estable.
-
Los hornos de sinterización pueden funcionar en varios modos, entre ellos:
-
Gases protectores:
- Gases como el hidrógeno, el nitrógeno y el monóxido de carbono se utilizan habitualmente para mantener la presión atmosférica y garantizar unas condiciones de sinterización adecuadas. Estos gases ayudan a controlar el entorno térmico y químico dentro del horno.
-
Impacto en la calidad del producto sinterizado:
- La elección y el control de la atmósfera influyen directamente en la densidad, la resistencia y la microestructura del producto sinterizado. Un control adecuado de la atmósfera garantiza la uniformidad y consistencia del producto final.
Seleccionando y regulando cuidadosamente la atmósfera del horno, los fabricantes pueden conseguir las propiedades deseadas en sus productos sinterizados, lo que la convierte en un aspecto crítico del proceso de sinterización.
Cuadro recapitulativo:
Aspecto clave | Detalles |
---|---|
Finalidad de la atmósfera controlada | Previene la oxidación, la descarburación y garantiza unas condiciones de sinterización adecuadas. |
Tipos de atmósferas | Inerte (N₂, Ar), Hidrógeno, Vacío, Amoníaco disociado, Gas endotérmico. |
Selección del ambiente | En función del material (por ejemplo, oxidante, neutro, reductor o protector). |
Regulación por zonas | Diferentes zonas requieren atmósferas específicas para vectores de sinterización óptimos. |
Modos operativos | Aire, vacío, vacío parcial o presión positiva. |
Impacto en la calidad del producto | Controla la densidad, la resistencia y la microestructura de los productos sinterizados. |
¿Necesita ayuda para seleccionar la atmósfera de horno de sinterización adecuada? Contacte hoy mismo con nuestros expertos soluciones a medida