La sinterización en estado sólido y la sinterización en fase líquida son dos métodos distintos utilizados en la densificación de materiales en polvo, cada uno con mecanismos y aplicaciones únicos.La sinterización en estado sólido se basa en la difusión atómica para unir partículas sin fundirlas, lo que la hace adecuada para cerámicas como la circonia y la alúmina.Por otro lado, la sinterización en fase líquida implica la adición de un material de bajo punto de fusión que forma una fase líquida a temperaturas de sinterización, lo que facilita la reorganización y la unión de las partículas.Este método es especialmente útil para cerámicas difíciles de densificar, como el nitruro de silicio y el carburo de silicio.La elección entre estos métodos depende de las propiedades del material, las velocidades de densificación deseadas y las temperaturas de sinterización.
Explicación de los puntos clave:
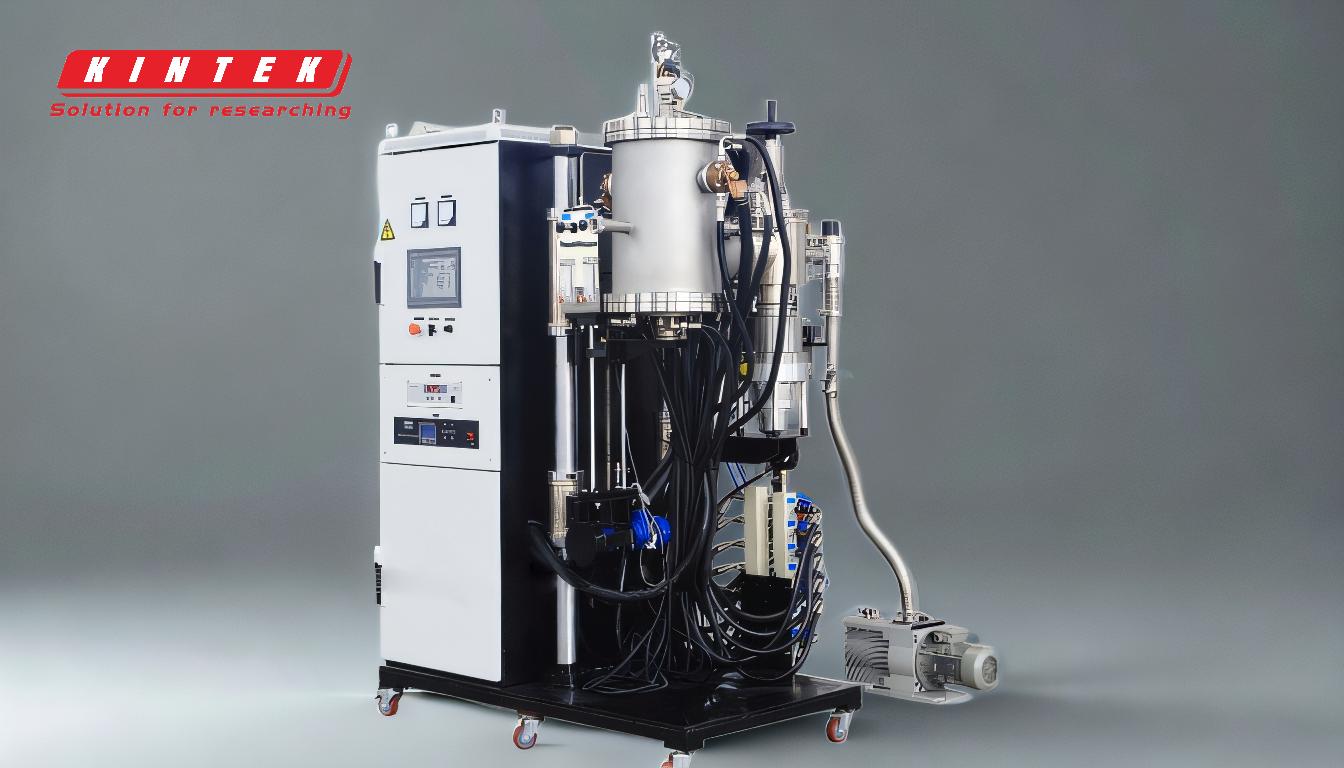
-
Mecanismo de enlace:
- Sinterización en estado sólido:En este proceso, los materiales en polvo se calientan a una temperatura justo por debajo de su punto de fusión.La unión se produce a través de la difusión atómica, en la que los átomos se mueven a través de los límites de las partículas, lo que conduce a la densificación y la resistencia.Este método no implica ninguna fase líquida.
- Sinterización en fase líquida:Aquí se introduce una pequeña cantidad de un aditivo de bajo punto de fusión.A temperaturas de sinterización, este aditivo forma una fase líquida.El líquido ayuda a la reorganización de las partículas debido a las fuerzas capilares, mejorando la densificación y la unión.
-
Requisitos de temperatura:
- Sinterización en estado sólido:Normalmente requiere temperaturas más elevadas, ya que depende únicamente de la difusión atómica.La ausencia de una fase líquida significa que el material debe calentarse cerca de su punto de fusión para lograr una movilidad atómica suficiente.
- Sinterización en fase líquida:Generalmente funciona a temperaturas más bajas que la sinterización en estado sólido.La presencia de una fase líquida reduce la energía necesaria para el reordenamiento y la unión de las partículas, lo que lo hace más eficiente desde el punto de vista energético.
-
Idoneidad de los materiales:
- Sinterización en estado sólido:El más adecuado para materiales que pueden densificarse únicamente por difusión, como la circonia y la alúmina.Estos materiales tienen puntos de fusión relativamente bajos y pueden densificarse eficazmente sin necesidad de fase líquida.
- Sinterización en fase líquida:Ideal para materiales más difíciles de densificar, como el nitruro de silicio y el carburo de silicio.Estos materiales tienen puntos de fusión elevados y requieren mecanismos adicionales, como la presencia de una fase líquida, para lograr una densificación eficaz.
-
Velocidad de densificación:
- Sinterización en estado sólido:La tasa de densificación es generalmente más lenta debido a la dependencia de la difusión atómica, que es un proceso más lento en comparación con los mecanismos en fase líquida.
- Sinterización en fase líquida:Ofrece una tasa de densificación más rápida debido a la mayor movilidad de las partículas en presencia de una fase líquida.Esto lo hace especialmente útil cuando se desea una densificación rápida.
-
Aplicaciones:
- Sinterización en estado sólido:Comúnmente utilizado en la producción de componentes cerámicos donde la alta pureza y la integridad estructural son críticas.Algunos ejemplos son los implantes médicos, las herramientas de corte y los sustratos electrónicos.
- Sinterización en fase líquida:A menudo se emplea en la fabricación de cerámicas y compuestos avanzados que requieren gran resistencia y tenacidad.Las aplicaciones incluyen componentes aeroespaciales, herramientas de corte y piezas resistentes al desgaste.
-
Ventajas y limitaciones:
-
Sinterización en estado sólido:
- Ventajas:Produce materiales de gran pureza con una contaminación mínima.Adecuado para materiales que no requieren una densificación rápida.
- Limitaciones:Proceso más lento y requiere temperaturas más elevadas, lo que puede suponer un gran consumo de energía.
-
Sinterización en fase líquida:
- Ventajas:Densificación más rápida, temperaturas de sinterización más bajas y eficaz para materiales con punto de fusión elevado.
- Limitaciones:Potencial de contaminación de la fase líquida y puede requerir tratamientos posteriores a la sinterización para eliminar el líquido residual.
-
Sinterización en estado sólido:
En resumen, la elección entre la sinterización en estado sólido y la sinterización en fase líquida depende de las propiedades específicas del material y de los resultados deseados del proceso de sinterización.El sinterizado en estado sólido es ideal para materiales que pueden densificarse únicamente mediante difusión, mientras que el sinterizado en fase líquida es más adecuado para materiales más difíciles de densificar que se benefician de la presencia de una fase líquida.Comprender estas diferencias es crucial para seleccionar el método de sinterización adecuado para una aplicación determinada.
Cuadro sinóptico:
Aspecto | Sinterización en estado sólido | Sinterización en fase líquida |
---|---|---|
Mecanismo | Difusión atómica sin fusión | La fase líquida favorece la reorganización y la unión de las partículas |
Temperatura | Temperaturas más altas (cerca del punto de fusión) | Temperaturas más bajas debido a la fase líquida |
Idoneidad del material | Circonio, alúmina (puntos de fusión bajos) | Nitruro de silicio, carburo de silicio (puntos de fusión altos) |
Velocidad de densificación | Más lenta (depende de la difusión atómica) | Más rápida (potenciada por la fase líquida) |
Aplicaciones | Implantes médicos, herramientas de corte, sustratos electrónicos | Componentes aeroespaciales, piezas resistentes al desgaste, herramientas de corte |
Ventajas | Alta pureza, contaminación mínima | Densificación más rápida, temperaturas más bajas, eficaz para materiales con alto punto de fusión |
Limitaciones | Proceso más lento, consume mucha energía | Posible contaminación, pueden ser necesarios tratamientos posteriores a la sinterización |
¿Necesita ayuda para elegir el método de sinterización adecuado para sus materiales? Póngase en contacto con nuestros expertos para obtener soluciones a medida.