Los sistemas de calentamiento por inducción funcionan a distintas frecuencias en función de la aplicación, las propiedades del material y los resultados deseados.La frecuencia de un sistema de calentamiento por inducción suele oscilar entre frecuencias utilitarias (50 o 60 Hz) y frecuencias altas (hasta 500 kHz o más).Las frecuencias más bajas se utilizan para materiales más grandes y gruesos y aplicaciones que requieren una penetración más profunda del calor, mientras que las frecuencias más altas son adecuadas para materiales más pequeños y delgados y para el calentamiento de superficies.En la elección de la frecuencia influyen factores como el tipo de material, el tamaño, la resistividad y la profundidad de calentamiento deseada, que se rige por el efecto piel.Comprender estos principios ayuda a seleccionar la frecuencia adecuada para las necesidades específicas de calentamiento por inducción.
Explicación de los puntos clave:
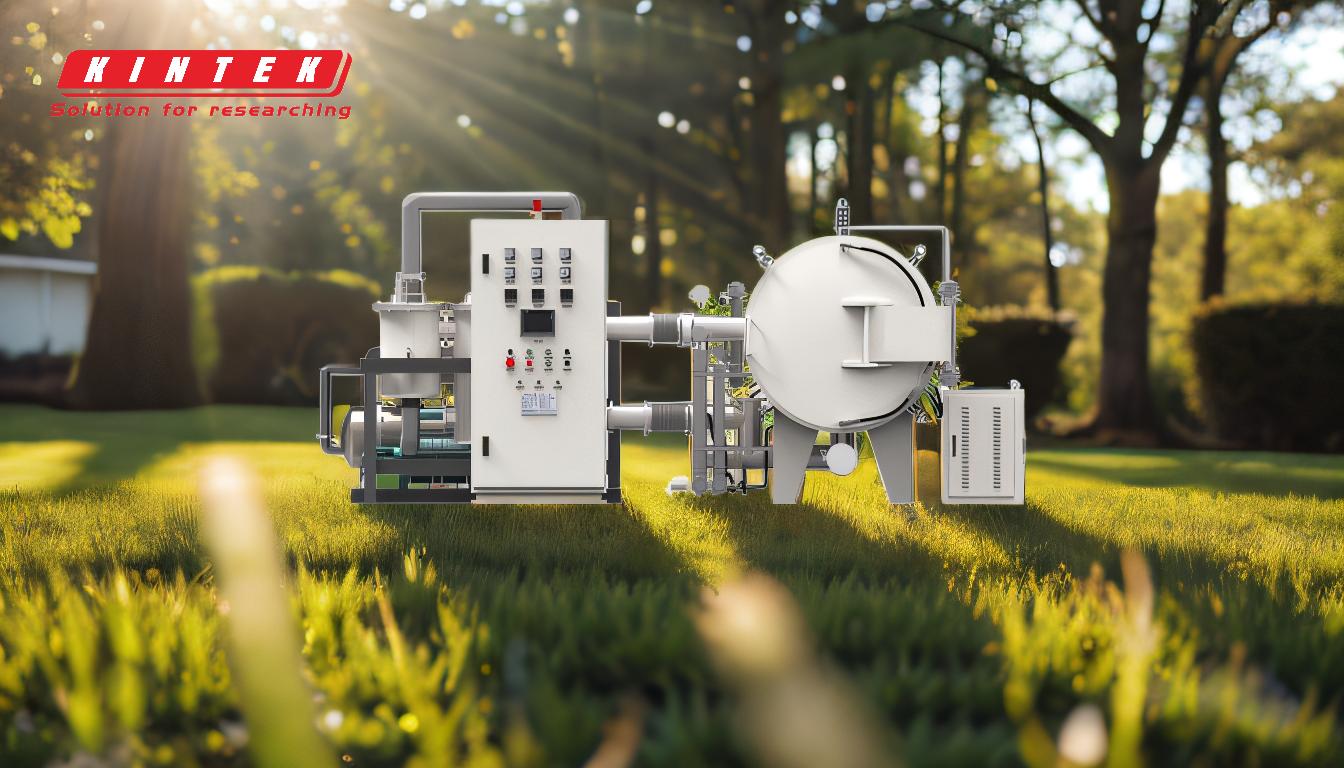
-
Gama de frecuencias de los sistemas de calentamiento por inducción:
- Los sistemas de calentamiento por inducción funcionan en un amplio espectro de frecuencias, desde las frecuencias de uso general (50 o 60 Hz) hasta las altas frecuencias (hasta 500 kHz o más).
- Las frecuencias bajas (50-60 Hz) suelen utilizarse para aplicaciones industriales a gran escala, como la fusión de grandes volúmenes de metal en hornos de inducción.
- Las frecuencias medias (1-10 kHz) suelen utilizarse para aplicaciones que requieren profundidades de calentamiento moderadas, como la forja o el tratamiento térmico de componentes de tamaño medio.
- Las frecuencias altas (100-500 kHz) son ideales para materiales pequeños y finos o aplicaciones de calentamiento superficial, como el temple o la soldadura fuerte.
-
Factores que influyen en la selección de la frecuencia:
- Tipo y tamaño del material:Los materiales más pequeños y delgados requieren frecuencias más altas debido al efecto piel, que hace que las frecuencias más altas generen calor más cerca de la superficie.Los materiales más grandes y gruesos se benefician de frecuencias más bajas para una penetración más profunda del calor.
- Efecto de profundidad de la piel:La profundidad superficial es la distancia desde la superficie de un conductor en la que la densidad de corriente desciende hasta aproximadamente el 37% de su valor superficial.Las frecuencias más altas dan lugar a profundidades menores, lo que las hace adecuadas para el calentamiento superficial.
- Profundidad de calentamiento deseada:Las aplicaciones que requieren un calentamiento profundo, como la fusión de grandes volúmenes de metal, utilizan frecuencias más bajas.Por el contrario, los tratamientos superficiales como el endurecimiento o el recocido utilizan frecuencias más altas.
- Resistividad del material:Los materiales con mayor resistividad se calientan más eficazmente a frecuencias más altas, mientras que los materiales de menor resistividad pueden requerir frecuencias más bajas para un calentamiento eficaz.
-
Aplicaciones y correlación de frecuencias:
- Baja frecuencia (50-60 Hz):Se utilizan para la fusión a gran escala, como en los hornos de inducción para acero o hierro.Estas frecuencias también son adecuadas para aplicaciones que requieren una agitación o turbulencia importantes en la masa fundida.
- Frecuencia media (1-10 kHz):Ideal para el tratamiento térmico, la forja y la fusión de componentes de tamaño medio.Estas frecuencias equilibran la profundidad de calentamiento y la eficacia para una amplia gama de aplicaciones industriales.
- Alta frecuencia (100-500 kHz):Ideal para aplicaciones de calentamiento superficial, como endurecimiento, soldadura fuerte o recocido de materiales finos.Las altas frecuencias garantizan un calentamiento rápido y localizado.
-
Consideraciones sobre la fuente de alimentación y la eficiencia:
- La eficacia de un sistema de calentamiento por inducción depende de la capacidad de la fuente de alimentación, el diseño del inductor y el cambio de temperatura requerido.
- Las frecuencias más altas suelen requerir fuentes de alimentación más sofisticadas y caras, pero ofrecen velocidades de calentamiento más rápidas y un mejor control para piezas pequeñas o complejas.
- Las frecuencias más bajas son más eficientes energéticamente para aplicaciones a gran escala, pero pueden carecer de la precisión necesaria para componentes más pequeños.
-
Implicaciones prácticas para la selección de equipos:
- Al seleccionar un sistema de calentamiento por inducción, hay que tener en cuenta las propiedades del material (por ejemplo, resistividad, tamaño y forma) y el resultado deseado (por ejemplo, endurecimiento superficial frente a calentamiento profundo).
- El diseño de la bobina inductora y los condensadores de compensación pueden ajustarse para optimizar el rendimiento en frecuencias y aplicaciones específicas.
- Los niveles de ruido, la eficiencia de la fusión y los efectos de la agitación son factores adicionales que pueden influir en la selección de la frecuencia en las máquinas de fusión por inducción.
Al comprender estos puntos clave, los compradores de equipos y consumibles pueden tomar decisiones informadas sobre la frecuencia adecuada para sus necesidades específicas de calentamiento por inducción, garantizando un rendimiento y una eficacia óptimos.
Tabla resumen:
Gama de frecuencias | Aplicaciones | Características principales |
---|---|---|
Baja (50-60 Hz) | Fusión a gran escala, calentamiento profundo | Ideal para materiales gruesos, eficiente energéticamente para grandes volúmenes |
Medio (1-10 kHz) | Tratamiento térmico, forja, componentes de tamaño medio | Equilibra la profundidad de calentamiento y la eficacia |
Alta (100-500 kHz) | Calentamiento de superficies, endurecimiento, soldadura fuerte | Ideal para materiales finos, calentamiento rápido y localizado |
¿Necesita ayuda para elegir la frecuencia de calentamiento por inducción adecuada? Póngase en contacto con nuestros expertos para obtener soluciones a medida.