El método de deposición física en fase vapor (PVD) por evaporación en vacío es una técnica muy utilizada para depositar películas finas sobre sustratos.Consiste en la transformación de un material sólido en vapor mediante calentamiento en un entorno de alto vacío, seguida de la condensación del vapor sobre un sustrato para formar una película fina.Este método es sencillo, rentable y se utiliza desde hace décadas en diversas aplicaciones, como revestimientos ópticos, productos electrónicos y acabados decorativos.El proceso se basa en el calentamiento resistivo para evaporar el material de partida, lo que garantiza una gran pureza y uniformidad de las películas depositadas.
Explicación de los puntos clave:
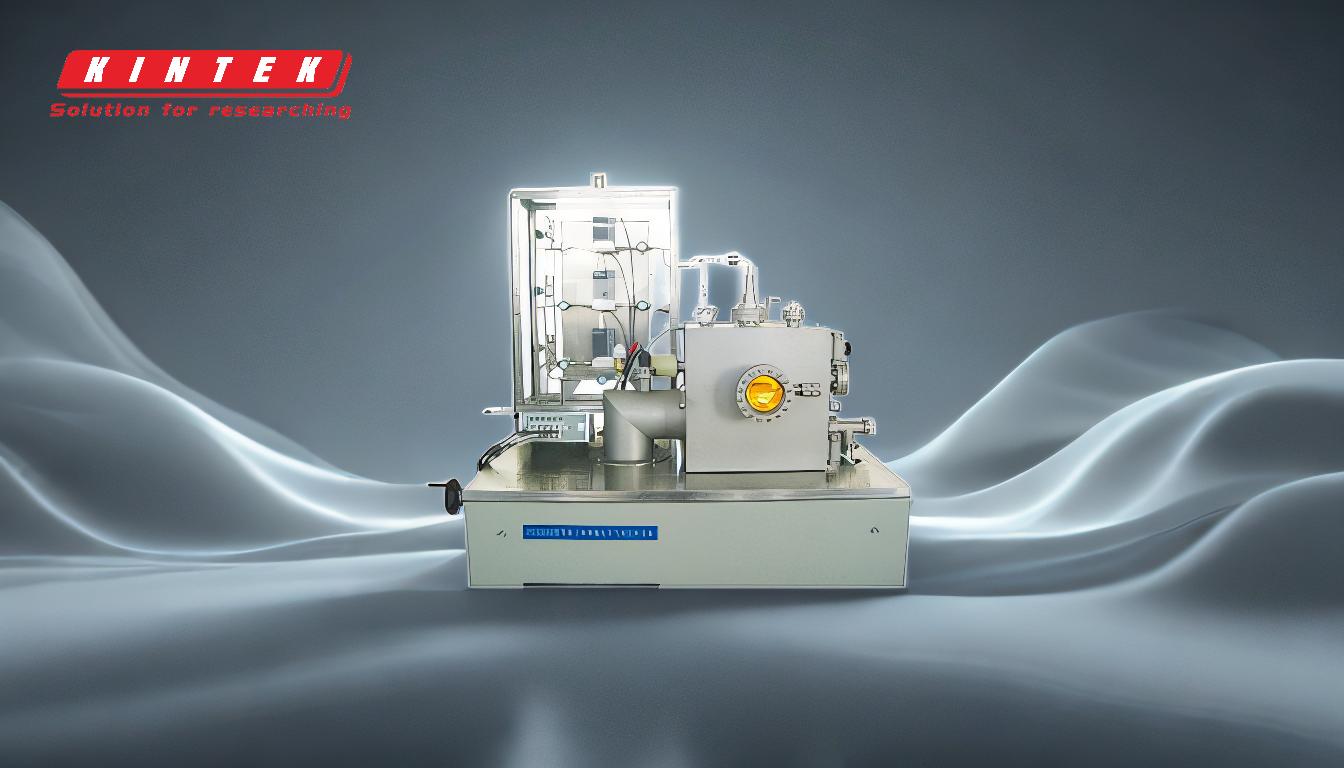
-
Definición y Proceso de Evaporación al Vacío PVD:
- La evaporación en vacío es una técnica de deposición física de vapor (PVD) en la que un material sólido se calienta en una cámara de alto vacío hasta que se evapora.A continuación, el vapor atraviesa el vacío y se condensa en un sustrato, formando una fina película.
-
El proceso consta de tres pasos principales:
- Evaporación:El material fuente se calienta hasta su punto de evaporación, normalmente mediante calentamiento resistivo, haces de electrones u otros métodos.
- Transporte:El material vaporizado viaja a través del entorno de vacío hasta el sustrato.
- Condensación:El vapor se condensa en el sustrato, formando una película fina y uniforme.
-
Aplicaciones del PVD por evaporación en vacío:
-
Este método es versátil y se utiliza en diversas industrias:
- Recubrimientos ópticos:Para espejos, lentes y revestimientos antirreflectantes.
- Electrónica:En la producción de semiconductores, células solares y transistores de película fina.
- Acabados decorativos:Para juguetes, cosméticos y tacones de zapatos.
- Recubrimientos funcionales:En dispositivos aeroespaciales, de automoción y médicos para la resistencia al desgaste y la protección contra la corrosión.
-
Este método es versátil y se utiliza en diversas industrias:
-
Ventajas del PVD por evaporación en vacío:
- Alta pureza:El entorno de vacío minimiza la contaminación, lo que da como resultado películas de gran pureza.
- Uniformidad:El proceso permite un control preciso del grosor y la uniformidad de la película.
- Rentabilidad:Es relativamente sencillo y rentable en comparación con otros métodos de PVD.
- Versatilidad:Adecuado para una amplia gama de materiales, incluidos metales, aleaciones y cerámicas.
-
Formas especializadas de PVD por evaporación:
- Proyección de plasma:Una variante del PVD por evaporación en la que se utiliza una llama de plasma para fundir o evaporar material de revestimiento en forma de polvo, creando películas gruesas sobre sustratos.
- Evaporación por haz de electrones:Utiliza un haz de electrones para calentar el material de partida, lo que permite mayores velocidades de evaporación y un mejor control de la deposición.
-
Contexto histórico:
- La evaporación al vacío se utiliza desde el siglo XIX, sobre todo para crear espejos depositando plata sobre vidrio.Esta aplicación histórica pone de manifiesto la fiabilidad y eficacia del método.
-
Retos y consideraciones:
- Requisitos de alto vacío:El proceso requiere un entorno de alto vacío, cuyo mantenimiento puede resultar costoso.
- Limitaciones del material:No todos los materiales pueden evaporarse fácilmente, y algunos pueden requerir equipos especializados.
- Compatibilidad del sustrato:El sustrato debe soportar las altas temperaturas y las condiciones de vacío del proceso.
En conclusión, el PVD por evaporación en vacío es un método fundacional y versátil para la deposición de películas finas, que ofrece una gran pureza, uniformidad y rentabilidad.Sus aplicaciones abarcan múltiples industrias y su uso histórico subraya su fiabilidad.Aunque existen retos, como los requisitos de alto vacío y las limitaciones de los materiales, el método sigue siendo una piedra angular de las modernas tecnologías de revestimiento.
Cuadro sinóptico:
Aspecto | Detalles |
---|---|
Proceso | Evaporación, transporte y condensación de materiales en alto vacío. |
Aplicaciones | Recubrimientos ópticos, electrónica, acabados decorativos, recubrimientos funcionales. |
Ventajas | Alta pureza, uniformidad, rentabilidad, versatilidad. |
Formas especializadas | Pulverización por plasma, evaporación por haz de electrones. |
Desafíos | Requisitos de alto vacío, limitaciones de materiales, compatibilidad de sustratos. |
Descubra cómo el PVD por evaporación en vacío puede mejorar sus proyectos. contacte hoy mismo con nuestros expertos ¡!