Los materiales utilizados en un horno de inducción se seleccionan cuidadosamente para garantizar que puedan soportar altas temperaturas y proporcionar una conservación eficaz del calor. Los materiales primarios incluyen materiales refractarios como magnesia, dolomita y alúmina para el revestimiento del horno, que ofrecen altos puntos de fusión y durabilidad. El cuerpo del horno se construye a menudo con materiales de fibra de alúmina de gran pureza formados al vacío, conocidos por su excelente conservación del calor y su resistencia a las altas temperaturas. Los elementos calefactores suelen estar fabricados con aleaciones de hierro-cromo-aluminio o níquel-cromo, y a veces con tiras de grafito o molibdeno. Además, el horno está diseñado para fundir una gran variedad de metales y aleaciones, como acero inoxidable, aluminio y metales preciosos, así como aleaciones especializadas como níquel, cobalto y superaleaciones basadas en hierro.
Explicación de los puntos clave:
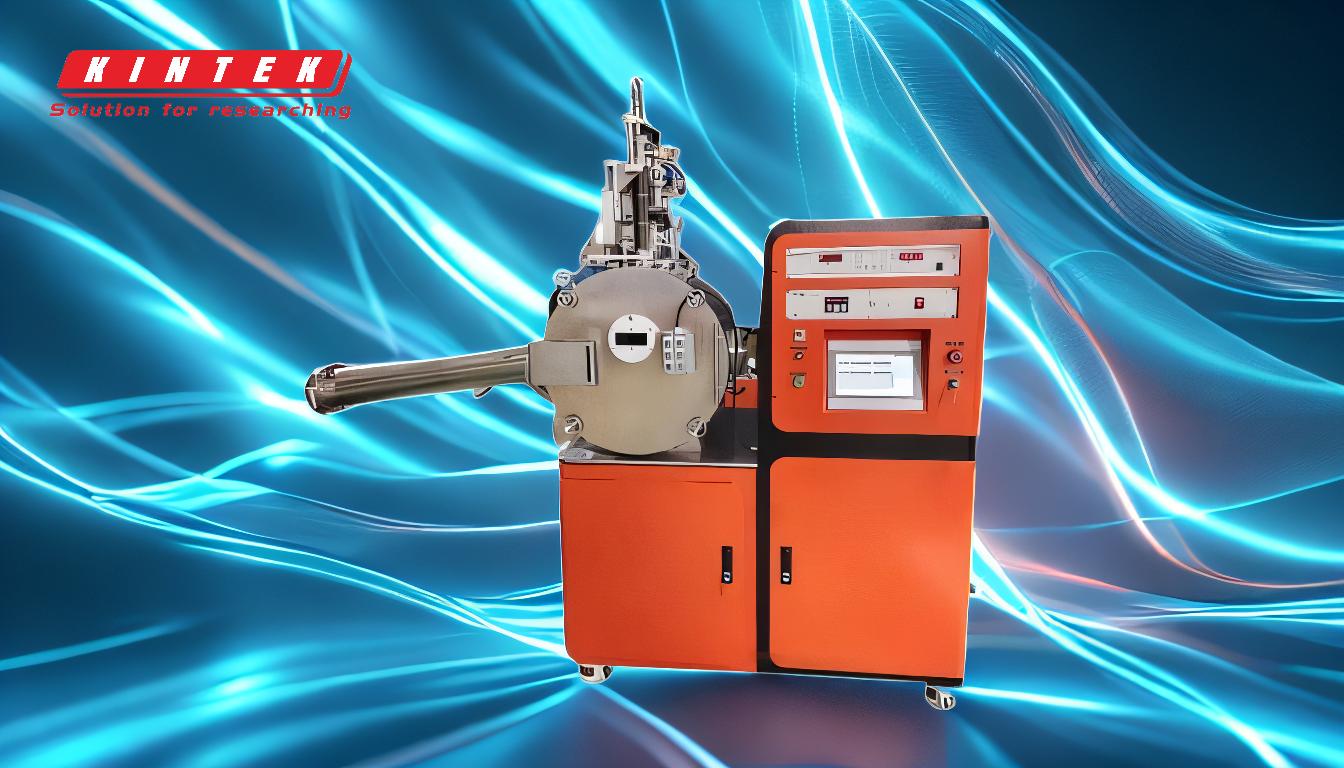
-
Materiales refractarios para revestimiento de hornos:
- Magnesia, dolomita y alúmina: Estos materiales se utilizan para el revestimiento del horno debido a sus altos puntos de fusión y a su capacidad para soportar temperaturas extremas. Garantizan el funcionamiento eficaz del horno sin degradarse con el paso del tiempo.
- Finalidad: El revestimiento protege la estructura del horno del intenso calor generado durante los procesos de fusión y evita la contaminación del metal fundido.
-
Materiales de construcción del horno:
- Fibra de alúmina de alta pureza moldeada al vacío: Este material se utiliza para construir el cuerpo del horno. Proporciona una excelente conservación del calor y puede soportar altas temperaturas, por lo que es ideal para mantener niveles de calor constantes durante la fusión.
- Ventajas: La fibra de alúmina de gran pureza es ligera, duradera y ofrece un aislamiento térmico superior, lo que mejora la eficiencia energética.
-
Elementos calefactores:
- Aleaciones de hierro-cromo-aluminio o níquel-cromo: Estos materiales se utilizan habitualmente como elementos calefactores por su gran resistencia al calor y al desgaste. Se les da forma cilíndrica, semicircular o plana para garantizar una distribución uniforme del calor.
- Tiras de grafito o molibdeno: En algunos diseños, los elementos calefactores se fabrican con tiras curvas ligeras de grafito o molibdeno, que son muy eficaces en entornos de alta temperatura.
-
Materiales fundidos en hornos de inducción:
- Metales: Los metales fundidos más comunes son el acero inoxidable, el aluminio y los metales preciosos como el oro y la plata. Estos metales se funden para hacerlos más maleables para su conformación, moldeo y reconfiguración.
- Aleaciones especializadas: Los hornos de inducción también se utilizan para fundir níquel, cobalto y superaleaciones basadas en hierro, así como otros materiales especializados como acero para herramientas, acero para rodamientos y aleaciones magnéticas.
-
Aplicaciones de los hornos de inducción:
- Producción de acero y aleaciones: Los hornos de inducción pueden producir acero y aleaciones a partir de residuos aleados, hierro puro y ferroaleaciones.
- Metales no ferrosos: También son capaces de fundir metales no férreos como el cobre y el aluminio, lo que los hace versátiles para diversas aplicaciones industriales.
-
Resistencia a altas temperaturas:
- Metales refractarios: Los hornos de alta temperatura suelen fabricarse con metales refractarios, que son densos, duros y muy resistentes al calor y al desgaste. Estas propiedades garantizan que el horno pueda funcionar a temperaturas extremas sin fallos estructurales.
Al comprender estos puntos clave, el comprador puede tomar decisiones informadas sobre los materiales y las características de diseño necesarias para sus requisitos específicos de hornos de inducción. La elección de los materiales influye directamente en el rendimiento, la durabilidad y la eficacia del horno, por lo que es crucial seleccionar los componentes adecuados para la aplicación prevista.
Tabla resumen:
Componente | Materiales utilizados | Principales ventajas |
---|---|---|
Revestimiento del horno | Magnesia, dolomita, alúmina | Altos puntos de fusión, durabilidad y protección contra la contaminación. |
Cuerpo del horno | Fibra de alúmina de gran pureza moldeada al vacío | Excelente conservación del calor, ligereza y aislamiento térmico superior. |
Elementos calefactores | Aluminio hierro-cromo, aleaciones de níquel-cromo | Alta resistencia al calor y al desgaste, distribución uniforme del calor. |
Calentamiento alternativo | Tiras de grafito o molibdeno | Ligeras y eficaces en entornos de alta temperatura. |
Metales fundidos | Acero inoxidable, aluminio, metales preciosos | Versátil para formar, moldear y reconfigurar diversos metales y aleaciones. |
Aleaciones especializadas | Níquel, cobalto, superaleaciones con base de hierro | Ideales para aplicaciones de alto rendimiento en entornos industriales. |
¿Está listo para mejorar el rendimiento de su horno de inducción? Póngase en contacto hoy mismo con nuestros expertos para soluciones a medida.