Introducción
Tabla de contenido
Cuando se trata de producir componentes cerámicos de alta calidad, uno de los procesos más cruciales es el prensado isostático. Esta técnica asegura la uniformidad y precisión requeridas para la fabricación de cerámicas utilizadas en diversas industrias. El prensado isostático implica seleccionar cuidadosamente los polvos de prensado y controlar las herramientas para lograr la uniformidad deseada. Otro factor clave en este proceso es la optimización del proceso de sinterización, que influye en gran medida en las propiedades físicas de la cerámica. Al comprender el proceso de prensado isostático, los fabricantes pueden garantizar la producción de cerámicas que cumplan con los estrictos estándares de precisión dimensional y rendimiento.
El proceso de prensado semiisostático
Importancia de la uniformidad del prensado
En el proceso de prensado semiisostático , los productos se colocan en un recipiente cerrado lleno de líquido y se someten a la misma presión en todas las superficies. Este entorno de alta presión aumenta la densidad de los productos y les da las formas requeridas. Las prensas semiisostáticas se utilizan ampliamente en la formación de refractarios de alta temperatura, cerámicas, carburo cementado, imanes permanentes de lantano, materiales de carbono y polvos de metales raros.
Papel de la cuidadosa selección de polvos de prensado y controles de herramientas
El prensado semiisostático se basa en una cuidadosa selección de polvos de prensado y controles de herramientas para garantizar el resultado deseado. A diferencia de otros procesos de pulvimetalurgia, el prensado semiisostático ofrece varios beneficios, incluida una compactación igual en todas las direcciones y una densidad final más uniforme del componente. Sin embargo, los fabricantes deben caracterizar cuidadosamente las propiedades del polvo metálico utilizado en el proceso para lograr propiedades finales óptimas del componente. La caracterización del material es crucial para garantizar la calidad y el rendimiento deseados del producto final.
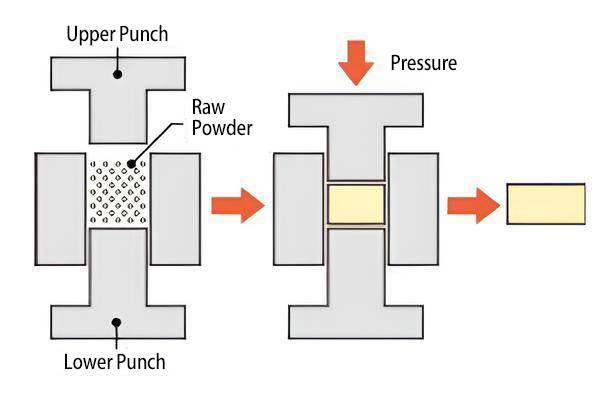
Influencia del proceso de sinterización optimizado en las propiedades físicas
El proceso de sinterización optimizado juega un papel importante en la determinación de las propiedades físicas de los componentes prensados semiisostáticamente. El prensado isostático permite la producción de varios tipos de materiales a partir de compactos en polvo al reducir la porosidad de la mezcla de polvo. La mezcla de polvo se compacta y encapsula mediante presión isostática, que aplica presión por igual desde todas las direcciones. Este confinamiento del polvo metálico dentro de una membrana flexible o recipiente hermético asegura una compactación y densidad uniformes dentro de la parte compactada.
El proceso de prensado isostático ha evolucionado a lo largo de los años y ahora se utiliza ampliamente en diversas industrias, incluidas la cerámica, los metales, los compuestos, los plásticos y el carbono. Ofrece beneficios únicos para aplicaciones cerámicas y refractarias, lo que permite dar forma precisa a los productos y reducir la necesidad de un mecanizado costoso. La presión general ejercida durante el prensado isostático garantiza una compactación y una densidad uniformes, lo que aborda las preocupaciones sobre la variación de la densidad en los métodos de procesamiento convencionales. El prensado isostático es particularmente adecuado para producir piezas más grandes, piezas con altas relaciones de espesor a diámetro y piezas que requieren propiedades de material superiores.
Hay dos categorías principales de prensado isostático: prensado isostático en frío (CIP) y prensado isostático en caliente (HIP). CIP implica aplicar presión isostática al polvo suelto a temperatura ambiente, mientras que HIP aplica presión isostática al polvo cuando se calienta en un paquete. HIP utiliza un gas inerte como medio de transferencia de presión. El proceso de prensado isostático en caliente implica colocar el polvo en un recipiente de alta presión, someterlo a alta temperatura y presión equilibrada, y sinterizarlo en partes compactas. En comparación con otros métodos como el prensado en caliente, el prensado isostático en caliente ofrece temperaturas de sinterización más bajas y una mayor densidad del producto.
En conclusión, el proceso de prensado semiisostático ofrece ventajas únicas en términos de uniformidad del prensado y densidad del componente final. La cuidadosa selección de los polvos de prensado y los controles de las herramientas, así como la optimización del proceso de sinterización, son cruciales para lograr las propiedades físicas deseadas. El proceso de prensado isostático se ha convertido en una herramienta valiosa en diversas industrias, permitiendo la producción de componentes de alta calidad con formas precisas y propiedades materiales superiores.
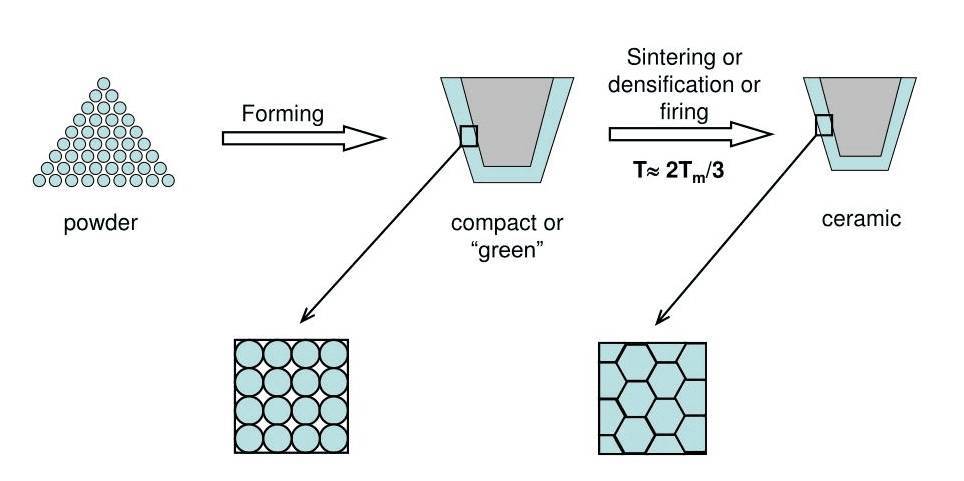
Papel de las técnicas de sinterización personalizadas
Lograr linealidad y concentricidad
La sinterización es un proceso crucial en la fabricación de componentes cerámicos. Las técnicas de sinterización personalizadas desempeñan un papel fundamental a la hora de lograr linealidad y concentricidad en estos componentes.
Una ventaja de la sinterización a temperatura ambiente es que permite la producción de objetivos de gran tamaño sin estar limitado por el tamaño del equipo. Este método también ofrece una baja inversión en equipos, un bajo costo de producción, una alta eficiencia de producción, un excelente rendimiento objetivo y una producción industrial sencilla. Es particularmente adecuado para los requisitos de rendimiento de objetivos recubiertos para pantallas de alta gama.
Sin embargo, la sinterización a temperatura ambiente tiene sus puntos débiles. Se considera el método de sinterización más difícil en comparación con otros. Para conseguir un cuerpo sinterizado denso, a menudo se añade un auxiliar de sinterización. Pero retirar el auxiliar de sinterización del cuerpo sinterizado puede resultar complicado, lo que da como resultado una menor pureza del producto. Además, se deben cumplir requisitos estrictos en cuanto a la forma, el tamaño de las partículas y la distribución del tamaño de las partículas del polvo. Para cumplir con estos requisitos se utilizan comúnmente técnicas de procesamiento de polvo, como molienda de bolas, molienda por chorro y clasificación por sedimentación. Finalmente, los objetivos producidos mediante sinterización a temperatura ambiente son generalmente delgados.
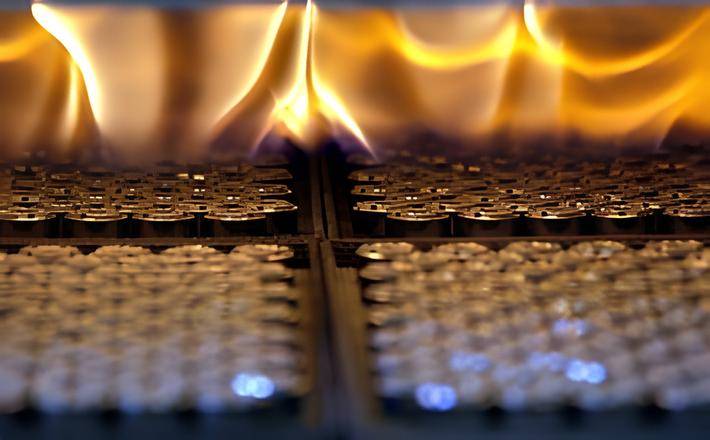
Idoneidad para la fabricación de diversos componentes cerámicos.
La sinterización es un proceso versátil que ofrece varias ventajas en la fabricación de componentes cerámicos. Éstos son algunos de los beneficios clave:
Formas complejas : la sinterización de metales permite la creación de formas complejas que serían difíciles o imposibles de producir con otros métodos. Esta capacidad abre posibilidades para diseños innovadores y componentes funcionales.
Alta precisión dimensional : la sinterización ofrece una alta precisión dimensional, lo que garantiza que el producto terminado se ajuste fielmente a la forma deseada. Esta precisión es crucial en aplicaciones donde se requieren tolerancias estrictas.
Fiabilidad y repetibilidad de la producción a gran escala : la sinterización es un proceso fiable que produce productos acabados consistentes. Esto lo hace ideal para tiradas de producción a gran escala, donde la consistencia y la uniformidad son esenciales.
Autolubricación : la sinterización puede crear piezas con propiedades autolubricantes. El polvo compactado forma una unión densa entre las partículas, lo que reduce la fricción y el desgaste. Esta propiedad es valiosa en aplicaciones donde la lubricación es desafiante o indeseable.
Materiales únicos e isotrópicos : la sinterización se utiliza para crear materiales isotrópicos únicos, es decir, que poseen las mismas propiedades en todas las direcciones. Estos materiales son muy duraderos y exhiben una excelente resistencia, lo que los hace adecuados para aplicaciones que requieren robustez.
Tecnología verde : la sinterización se considera una tecnología verde ya que no produce emisiones nocivas. Esto lo convierte en una opción respetuosa con el medio ambiente para las empresas que buscan reducir su impacto ambiental.
Amortiguación de vibraciones : la sinterización puede producir piezas con propiedades de amortiguación de vibraciones. El polvo compactado forma una unión densa que reduce las vibraciones y el ruido. Este atributo es beneficioso en aplicaciones donde el control de la vibración es crucial.
Varias piezas de cerámica.
La sinterización de metales encuentra aplicación en diversas industrias, incluidos componentes eléctricos, semiconductores y fibras ópticas. Mejora la resistencia, conductividad y translucidez de los metales, haciéndolos adecuados para estas industrias.
En la sinterización cerámica, el proceso se utiliza para fabricar objetos cerámicos, incluida la alfarería. Implica la consolidación del material, reduciendo la porosidad y aumentando la densidad. Las materias primas cerámicas suelen requerir aditivos orgánicos antes de la sinterización para mejorar la plasticidad. Las altas temperaturas, la presión o las corrientes eléctricas impulsan el proceso de sinterización.
Se han desarrollado métodos modernos de formación de formas en polvo, como el prensado isostático, la fundición deslizante, la extrusión, la fundición en cinta y la impresión 3D, para fabricar cuerpos verdes de cerámica y metales. Luego, el cuerpo verde se calienta mediante un proceso de sinterización, lo que reduce la porosidad y aumenta la densidad.
Los procesos de sinterización están controlados por mecanismos de difusión de estado sólido activados térmicamente. Estos mecanismos pueden cuantificarse desarrollando modelos de sinterización utilizando instrumentos como dilatómetros de varilla de empuje.
El equipo de sinterización por microondas se usa ampliamente en aplicaciones industriales para sinterizar diversas cerámicas de alta calidad, incluido óxido de cobalto y litio, nitruro de silicio, carburo de silicio, óxido de aluminio, nitruro de aluminio, óxido de circonio, hidróxido de magnesio, aluminio, zinc, caolín, sulfato de cobalto, cobalto. oxalato y óxido de vanadio. También se utiliza en la sinterización de dispositivos cerámicos electrónicos como varistores y cerámicas piezoeléctricas PZT.
En general, las técnicas de sinterización personalizadas desempeñan un papel crucial a la hora de lograr linealidad y concentricidad en los componentes cerámicos. Ofrecen numerosas ventajas, incluida la capacidad de fabricar formas complejas, alta precisión dimensional, confiabilidad en la producción a gran escala, autolubricación, materiales isotrópicos únicos, tecnología ecológica y amortiguación de vibraciones. La sinterización de metales encuentra aplicaciones en diversas industrias, mientras que la sinterización de cerámica se utiliza en alfarería y otros procesos de fabricación de cerámica. Los equipos de sinterización por microondas se utilizan ampliamente en aplicaciones industriales para sinterizar diversas cerámicas y dispositivos cerámicos electrónicos.
Capacidades de dimensión y precisión
Gama estándar de capacidades de dimensión
Las capacidades dimensionales de un sistema de deposición desempeñan un papel crucial a la hora de determinar su idoneidad para diversas aplicaciones. En entornos de I+D, la flexibilidad es un factor clave. El sistema debe poder manejar diferentes materiales, tamaños de sustrato, rangos de temperatura, flujo de iones, tasas de deposición, frecuencias, puntos finales y regímenes operativos de presión. Esto permite la experimentación y la adaptación a las prioridades cambiantes. Además, también entran en juego consideraciones presupuestarias, ya que el coste de los sistemas puede variar significativamente según las opciones tecnológicas.
Precisión en condiciones de disparo
La precisión es un factor crítico cuando se trata de sistemas de deposición. Por ejemplo, en el caso de micromecanizado o aplicaciones de ultraprecisión, el diamante se suele utilizar como material de herramienta debido a su extrema dureza y estabilidad dimensional. Al considerar la precisión en la condición de cocción, es importante tener en cuenta que el diámetro interno puede tener una tolerancia de +/- 0,02 mm con una repetibilidad de menos de 10 µm dentro del mismo lote de producción.
Precisión después del pulido con diamante
El rectificado con diamante es un proceso que puede mejorar significativamente la precisión en aplicaciones de mecanizado. Después del rectificado con diamante, la longitud de la pieza de trabajo puede tener una tolerancia de +/- 0,03 mm, mientras que el diámetro exterior puede tener una tolerancia de +/- 0,01 mm. Además, el espesor de pared mínimo alcanzable es de 0,3 µm. Estos niveles de precisión garantizan resultados de piezas de trabajo de alta calidad.
Las herramientas de corte de diamante se pueden crear utilizando diamante macizo (monocristal, diamante CVD, PCD) o recubrimientos de diamante. Las herramientas abrasivas de diamante estándar se fabrican uniendo monocristales de diamante sobre un cuerpo base. Alternativamente, existe una nueva tecnología de capa de molienda que involucra capas de diamante microcristalino depositadas químicamente con vapor con puntas de cristalita afiladas. Estos bordes afilados contribuyen a la eficacia del proceso de rectificado.
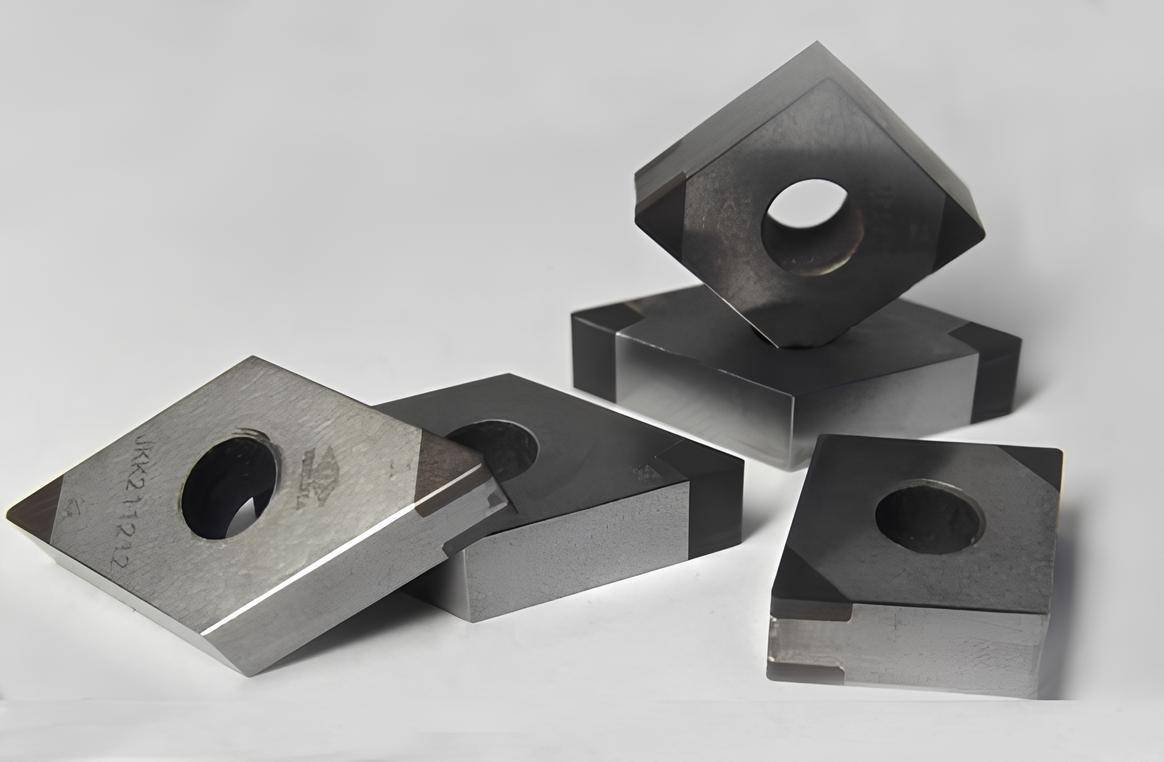
También se pueden producir microherramientas abrasivas, como lápices abrasivos y fresas, utilizando la misma tecnología de recubrimiento. Incluso se han probado con éxito herramientas muy pequeñas con un diámetro de 50 mm.
En conclusión, las capacidades dimensionales y la precisión de un sistema de deposición son factores cruciales a considerar en entornos de I+D. El sistema debería ofrecer flexibilidad, permitiendo la experimentación y la adaptación a las prioridades cambiantes. El rectificado con diamante puede mejorar enormemente la precisión en las aplicaciones de mecanizado, garantizando resultados de alta calidad. Ya sea que se trate de un rango estándar de capacidades dimensionales o de precisión después del rectificado con diamante, estos factores contribuyen a la efectividad y eficiencia general del sistema de deposición.
Conclusión
En conclusión, el prensado isostático es un proceso crucial en la fabricación cerámica que asegura la uniformidad y precisión de los componentes cerámicos. Seleccionando cuidadosamente los polvos de prensado y controlando las herramientas, los fabricantes pueden lograr la uniformidad deseada en la cerámica prensada. Además, la optimización del proceso de sinterización mejora aún más las propiedades físicas de la cerámica. Las técnicas de sinterización personalizadas desempeñan un papel fundamental a la hora de lograr linealidad y concentricidad en el producto final, haciéndolo adecuado para diversas aplicaciones. Además, las capacidades dimensionales y la precisión de la cerámica se pueden estandarizar y cualquier ajuste necesario se puede realizar mediante pulido con diamante. En general, el prensado isostático y las técnicas de sinterización personalizadas son esenciales para producir componentes cerámicos precisos y de alta calidad.
Si está interesado en nuestros productos, visite el sitio web de nuestra empresa: https://kindle-tech.com/product-categories/isostatic-press , donde la innovación siempre ha sido una prioridad. Nuestro equipo de I+D está formado por ingenieros y científicos experimentados que siguen de cerca las tendencias de la industria y están constantemente superando los límites de lo posible. Nuestro equipo de laboratorio incorpora la última tecnología para garantizar que pueda obtener resultados precisos y repetibles durante sus experimentos. Desde instrumentos de alta precisión hasta sistemas de control inteligentes, nuestros productos le brindarán posibilidades ilimitadas para su trabajo experimental.
CONTÁCTANOS PARA UNA CONSULTA GRATUITA
Los productos y servicios de KINTEK LAB SOLUTION han sido reconocidos por clientes de todo el mundo. Nuestro personal estará encantado de ayudarle con cualquier consulta que pueda tener. ¡Contáctenos para una consulta gratuita y hable con un especialista del producto para encontrar la solución más adecuada para sus necesidades de aplicación!